Tryckluft är livsmedels- och dryckesindustrins fjärde nödvändighet, efter vatten, elektricitet och naturgas. Tillförlitligheten hos denna hänger på ett förutsägbart lufttryck, vilket innebär att även små läckor kan leda till stora kostnader.
Här är en titt på luftläckage som ofta förekommer i livsmedels- och dryckesindustrin, tillsammans med bästa praxis och tekniker för att hantera dem.
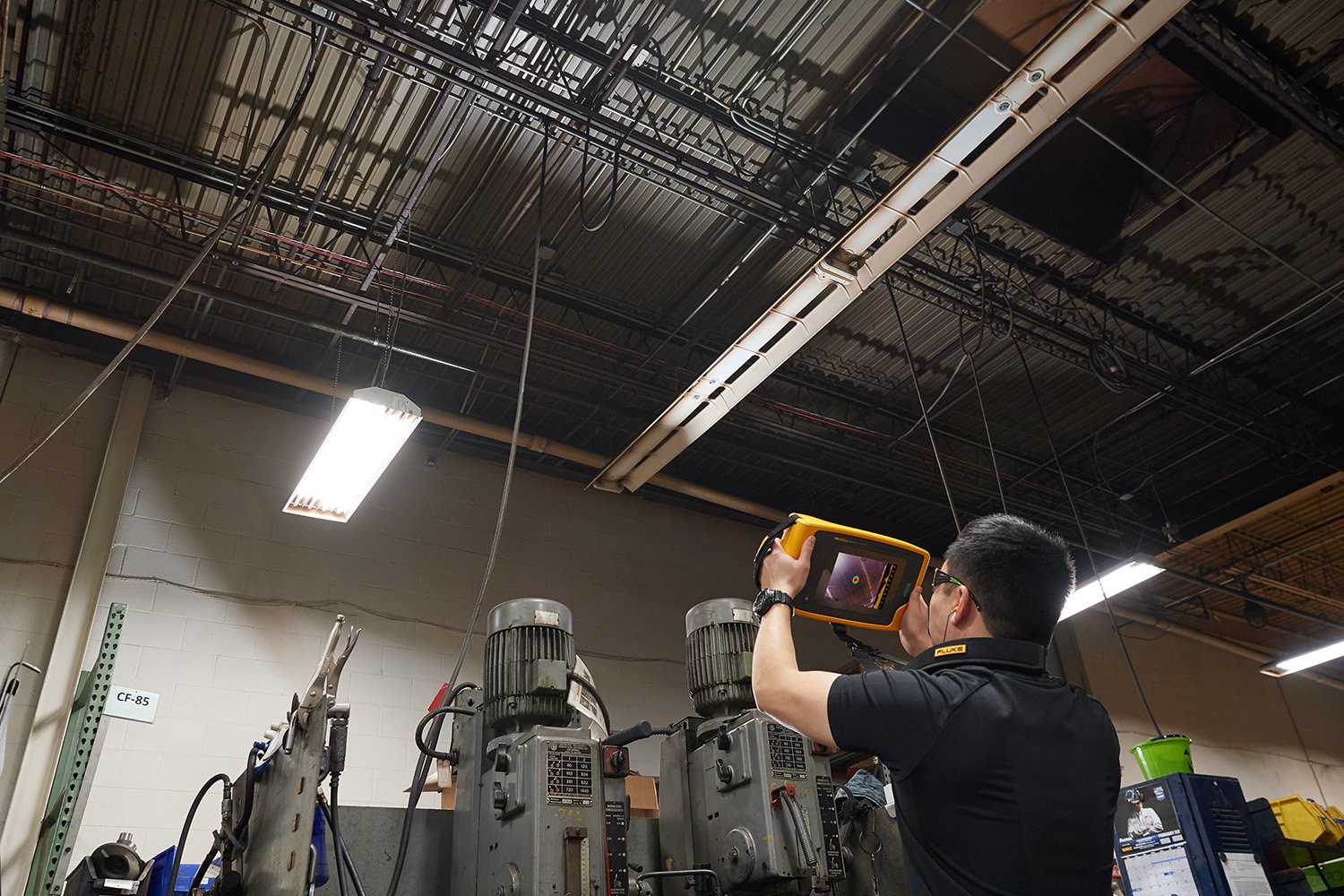
Livsmedels- och dryckestillverkare har unika överväganden när det gäller tryckluftsläckor eftersom enhetlig produktkvalitet är avgörande för varumärkets rykte och efterlevnad, särskilt eftersom produktionsanläggningar och deras utrustning är föremål för stränga kontroller och föreskrifter för att undvika kontaminering.
I livsmedels- och dryckesanläggningar ansluts flera luftkompressorer via rör för att leverera tryckluft som ska förflytta produkter, driva pneumatiska verktyg eller pumpa vätskor för en mängd olika ändamål inom produktionskedjor, förpackning och rengöring. Här är några exempel:
- Snacks och kvävedämpning: Kvävespolning används till att fylla snackspåsar så att ömtåliga snacks skyddas av en luftkudde. Syre kan inte användas eftersom det reagerar med livsmedelsprodukter, särskilt med sådana som framställs med oljor.
- Mat och renlighet: Tryckluft renas och filtreras för att säkerställa livsmedelssäkerhet och för att bibehålla rätt tryckdaggpunkt för att förhindra mikrobiell tillväxt.
- Skalning av frukt och grönsaker: Inför paketering används tryckluftstrålar för att effektivt ta bort skal från frukt och grönsaker. Högtrycksluft används också för att skära mat som ett renare alternativ till knivar eller klingor.
- Bryggerier, jäsning och tappning: Tryckluft ökar syrenivåerna för att slutföra processen med bakteriell jäsning. Luftkompressorer minskar mängden kvarvarande syre under flasktappning och flaskorna spolas med koldioxid och fylls med öl med hjälp av pneumatiskt drivna maskiner. Eftersom bryggerier arbetar i varma miljöer är systemen mer känsliga för läckor.
Luftläckage kan när som helst sakta ned produktionen, påverka produktkvaliteten, skapa säkerhets- eller kontamineringsproblem eller alla fyra – och därmed skada slutresultatet.
De dolda kostnaderna för tryckluftsläckor
Tryckluft och gaser måste finnas tillgängliga vid ett specifikt tryck för att uppnå produktions- och kvalitetsmål, men många anläggningar accepterar luftläckage som en kostnad för att göra affärer. Dessa kostnader kan vara höga i energiförluster, men ofta på andra dolda sätt som effektivitet, kvalitet och driftstopp.
Enligt Compressed Air & Gas Handbook Seventh Edition som publicerats av CAGI (Compressed Air & Gas Institute) kan ”en enda kvartstumsläcka i en tryckluftsledning kosta en anläggning från 2 500 till mer än 8 000 dollar per år. Att lokalisera och åtgärda läckor leder till betydande besparingar beroende på tryckbehov och energikostnader.”
Fördelar med testning av tryckluftssystem
- Öka effektiviteten genom regelbundet underhåll: Tryckluftssystem som inte regelbundet underhålls efter installation kan förlora 20 till 30 procent av tryckluften enbart genom läckage.
- Minska kostnader: Tryckfall feldiagnostiseras ofta som utrustningsfel, vilket resulterar i ytterligare kapitalinvesteringar i nya luftkompressorer.
- Minska driftstoppen: Förlorad produktionstid till följd av tryckfall eller installation av ny utrustning kräver driftstopp för utrustningen och har en negativ inverkan på planeringsscheman. Oplanerade driftstopp kostar i genomsnitt 200 dollar i minuten, vilket gör det viktigt att undvika dem.
- Förbättra produktkvaliteten: Otillräckligt tryck resulterar i dålig försegling av förpackningar eller att den ätbara produkten inte uppfyller kraven på enhetlig konsistens och smak.
- Förbättra produktsäkerheten: Läckor som orsakar kontaminering leder till höga kostnader för slöseri, straffavgifter för bristande regelefterlevnad och försämrat rykte.
- Minska koldioxidutsläppen: System med luft- och gasläckor blir ineffektiva, vilket påverkar företagets koldioxidutsläpp och förhindrar att det uppfyller sina hållbarhetsmål eller miljömål.
Formeln som används för att fastställa omfattningen av tryckluftsläckage vid en anläggning är: Läckage (%) = (T x 100) ÷ (T + t) T = pålastningstid (minuter), t = avlastningstid (minuter).
Om tryckluftssystemet är konfigurerat med start/stopp-reglage startar du luftkompressorn när det inte finns något luftbehov i systemet – efter arbetstid eller mellan skift. Gör sedan flera avläsningar av kompressorcykler för att fastställa den genomsnittliga tiden för avlastning av systemet.
Metoder för identifiering och korrigering av luftläckage
Det första steget i att styra processer och kostnader är att hitta luftläckor där de uppstår. Här är en lista över vanliga läckageställen:
- Kondensatfällor
- Kopplingar
- Maskindelar
- Flänsar
- Filter-, regulatorer-, och smörjningskombinationer (FRL:er)
- Slangar
- Inpackningar
- Pneumatiska förvaringstankar
- Snabbkopplingar
- Gängade röranslutningar
- Rör
- Ventiler
Luftläckor är ett stort problem eftersom de är många och svåra att hitta. När de har hittats och åtgärdats brukar fler läckor dyka upp på grund av normalt slitage på systemet.
Även om det kanske inte är möjligt att eliminera varje enskild läcka är det möjligt att minska det totala antalet med fokuserad inspektion med traditionella identifieringsmetoder. Med de här metoderna används en pappersetikett för att markera punkten där en läcka har hittats. Fyra traditionella identifieringsmetoder inkluderar:
- Ljud: Väsande indikerar läckage, vilket innebär att läckan är stor, eftersom bara en ljudnivå som är högre än 60 dBA kan höras utan särskild utrustning för upptäckt av läckage. Eftersom de flesta anläggningar är bullriga och ofta kräver att arbetarna bär hörselskydd måste man lyssna efter läckor under driftstopp – mellan skift, på helger eller vid schemalagt underhåll.
- Vatten och tvål: Tekniker sprutar tvålvatten på områden med hörbart läckage och där det dyker upp bubblor är läckagestället. Metoden är utdragen, långt ifrån exakt, och kräver rengöring eftersom tvålvattensspill utgör en halkrisk. I vissa rena och kontaminationsskyddade processer är det inte tillåtet.
- Akustisk lokalisering med ultraljud: Under driftstopp kan tekniker med hörlurar avsöka potentiella läckageställen med ett parabol- eller konformat tillbehör. När ett ljud som indikerar läckage upptäcks byter teknikern till en stavformad enhet som måste hållas ett par tum från läckan för att fastställa exakt var den finns.
- Använda externa experter: Ingenjörer eller andra experter anlitas vanligtvis en gång om året för att spara pengar och störningar. De använder en av eller alla de traditionella teknikerna och de reparationer och kontroller som hanteras av interna tekniker.
Ingen av dessa metoder är idiotsäker och kräver oftast driftstopp, vilket leder till förluster i tid och pengar.
Läckagetestning av tryckluftssystem hjälper kafferosteri att enkelt identifiera energibesparingar på 10 %
Projektingenjörer på ett kafferosteri deltog i en pilotstudie där man använde teknik för industriell akustisk avbildning i en anläggning där förhållandena tenderar att generera många läckor. Testet identifierade att företaget kunde spara mer än 10 % om året i energiförbrukning med den nya läckageavkänningsenheten.
På den 28.000 kvadratmeter stora anläggningen finns ett område för kafferostning och paketering, ett område för våtbehandling av kaffe samt ett område för blandning och förpackning av te. All verksamhet kräver rätt lufttryck för att effektivt slutföra processer och traditionella metoder för läckagedetektering hinner inte med.
Under en genomsnittlig dag använder anläggningen mellan 28 och 45 kubikmeter per minut (cu. m/min) av tryckluft. Företagets tryckluftssystem, som består av fem luftkompressorer på totalt 585 hästkrafter, driver automation och slangar som används för att mata verksamhetens kvävegenereringssystem. Kväve används för att förbättra kaffets kvalitet. Dessutom används den inerta gasen för att blanda te.
Med Fluke ii900-kameran för akustisk avbildning identifierade teamet potentiella energibesparingar på 10 %, vilket är i linje med målet att förbättra hållbarheten. Den nya metoden visade också hur teamet kunde förenkla identifieringen av luftläckage, så att projektingenjörerna kan låta personalen fortsätta arbeta med produkter i stället för att stoppa driften under långa perioder för att upptäcka och åtgärda luftläckage.
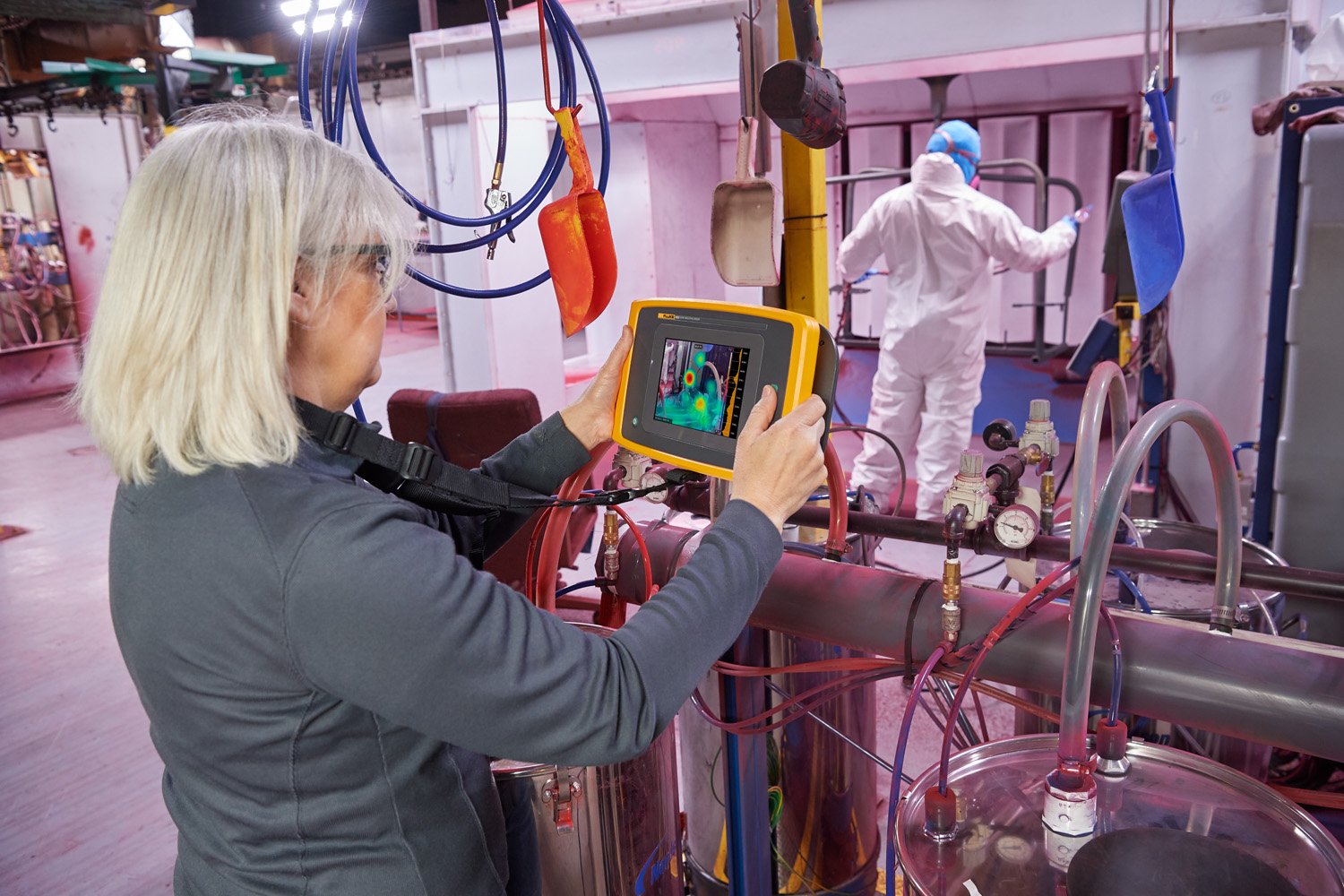
Se luftläckor för första gången med en kamera för akustisk avbildning
Ett framsteg inom tekniken för läckagedetektering i form av en bärbar industriell akustisk avbildare gör det lättare att upptäcka läckor och undvika förlorad vinst.
Med luftläckagedetektorn Fluke ii900 kan användare hitta och se luftläckor på en LED-skärm i realtid med en sikta-och-tryck-process som inte kräver någon specialiserad tekniker. De flesta användare kan komma igång på ungefär 10 minuter. Tekniker kan också arbeta snabbt på säkert avstånd medan utrustningen är igång. Dessutom gör enheten det enklare att hitta läckor på svåråtkomliga ställen eller att skilja mellan flera läckor inom samma område.
Den handhållna avbildaren innehåller en mängd ultrakänsliga mikrofoner som känner av ljud både inom det mänskligt hörbara området och i ultraljudsområdet och visar dem sedan visuellt. Enheten tillämpar sedan egenutvecklade algoritmer på resultaten och skapar omedelbart en visuell karta över läckan på skärmen. Bilden av läckan är överlagrad på en synligt ljus-bild av området så att operatören snabbt kan lokalisera läckan.
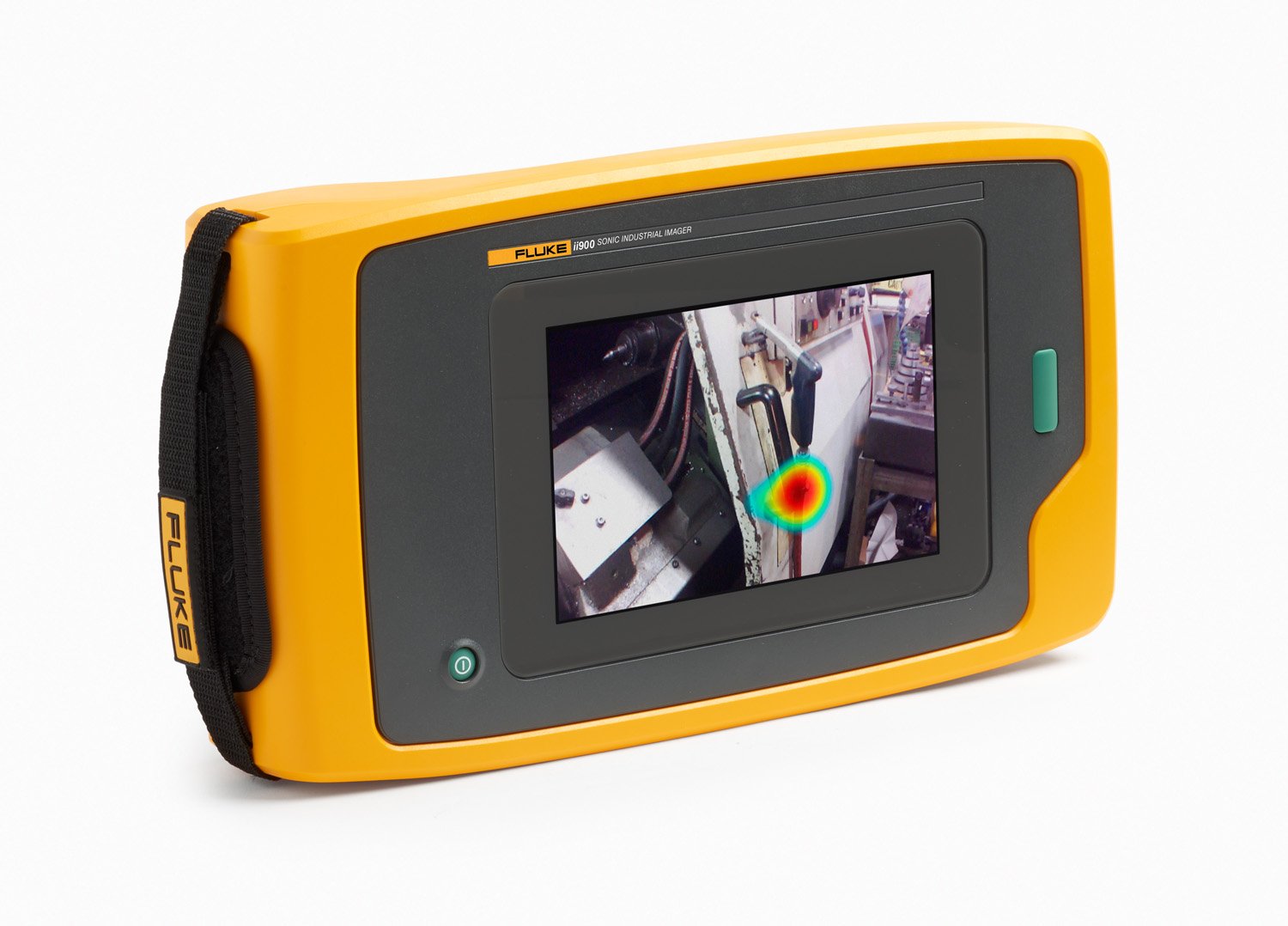
Fluke ii900 kan även användas för att verifiera att reparationer har utförts korrekt. Om frågor uppstår kan du dela och diskutera avsökningar som registrerats som stillbilder eller videor med kollegor. De tagna bilderna gör att du inte behöver klättra på stegar eller markera läckan med den vanliga ömtåliga fysiska etiketten.
Hur du minskar kostnaderna för dolda luftläckor
Vare sig du använder vanliga eller nya detektionsmetoder är nu den bästa tiden att avlägsna de dolda kostnaderna och det onödiga slöseriet som luftläckage innebär. Här är något av bästa praxis att följa:
- Närma dig problemet på systemnivå: När en läcka tätas ökar ofta trycket i systemet och gör små läckor större, vilket påverkar hela systemet. Kombinera förändringar med övergripande strategier för förbättrad energianvändning och mer robusta styrsystem. Även om de kan vara svåra att göra ger kapitalinköp ofta energibesparingar som avsevärt minskar återbetalningstiden.
- Granska ofta: Regelbunden granskning – oftare än de vanliga läckageinspektionerna varje år eller en gång i kvartalet – sparar tid, pengar och resurser i längden, även om du behöver stänga av utrustningen. Ny avbildningsteknik innebär att du kan fokusera på läckor och åtgärda dem kontinuerligt utan att förlora värdefull produktionstid.
- Bekräfta grundorsakerna till tryckfall: Tryckfall kan feldiagnostiseras som utrustningsfel. Innan du drar på dig kapitalutgifter kan läckagekontroller och åtgärder spara tusentals eller hundratusentals dollar och hjälpa dig att omedelbart återfå kapaciteten.
- Logga, spåra och verifiera över tid: Det är viktigt att notera exakt var läckor har inträffat och inspektera dessa områden regelbundet, eftersom de här svaga punkterna tenderar att vara där nya läckor uppstår. Genom att logga information online kan data enkelt delas och användas för att skapa disciplin i granskningsprocessen. Kontrollera så snart reparationen har utförts för att avgöra om läckor har eliminerats eller behöver åtgärdas ytterligare.