ROI på kostnadsbesparingar inom industriell energieffektivitet
Vad har mätning med energibesparing att göra? Allt handlar om ROI och slutresultatet.
Industrianläggningar måste förbruka energi för att kunna producera – produkter, data eller något annat – och de flesta anläggningar slösar bort för mycket elektricitet. De är ineffektiva energianvändare. För tjugo år sedan brydde sig inte anläggningsledningen om energieffektivitet – energi var billigt. När energi blev dyrare blev cheferna intresserade av att sänka elräkningen, men åtgärderna måste omvandlas till affärsbegrepp.
Vid vilken ROI-punkt är förlusten så pass stor att den bör tas itu med?
För att svara på den frågan måste du mäta hur mycket energi du förbrukar på de olika lasterna (systemen) i din anläggning och jämföra med standarder. Då ser du hur stora energiförlusterna är. Med ytterligare mätningar kan du identifiera grundorsaken till förlusten. De tre punkterna i en ROI-ekvation är: 1) mängden avfall kombinerat med 2) orsaken och 3) kostnaden att åtgärda.
När är det vettigt med en minskad energiförbrukning?
Minskad energiförbrukning är en god idé för anläggningar som vill minska omkostnaderna för att öka produktiviteten – anläggningar som vill får ut mer av mindre, inte bara förbruka mindre.
Vid en energiinspektion identifieras möjligheter för att öka effektiviteten och anläggningschefen får de uppgifter som behövs för att kunna förstå vilka energibesparande åtgärder som är vettiga att genomföra med tanke på anläggningens primära mål, och vilka som inte ger tillräckligt med ROI eller faller utanför prioriteringarna. De största möjligheterna finns vanligen i anläggningar som har gamla, stora, energikrävande system som inte har optimerats. Andra bra kandidater är produktionsanläggningar som inte har infört automatisering eller styrreglage i någon större omfattning samt anläggningar med stora ång- eller tryckluftssystem.
Hur mycket går det att spara?
Enligt det amerikanska energidepartementet (Department of Energy, DOE), kan anläggningarna sänka sina elräkningar med 25 %, men de faktiska besparingarna beror på några olika saker. För det första, vilken typ av system och laster finns i anläggningen? Stora belastningar som aldrig har jämförts med elpristabellen för att dra nytta av de billigaste tidpunkterna kan innebära betydande besparingar. En anläggning som mest producerar mindre mängder kanske inte har samma möjligheter. För det andra, hur ineffektiva är byggnadssystemen? En nyare, väl underhållen anläggning kan inte erbjuda lika många besparingsmöjligheter som en äldre anläggning där system och utrustning inte längre uppfyller rekommenderade inställningar och underhållsmetoder.
När du tänker på energiförluster hemma tänker du förmodligen på kall luft som läcker in genom fönstret eller så byter du ut gamla glödlampor mot LED-lampor. Men vilken typ av ”energiförlust” sker i en tillverkningsanläggning eller anläggning för blandad användning?
När energi används för att värma eller kyla luft och tvingas genom ventilationssystemet, för att sedan läcka ut genom fönstren, tvingas systemet att överproducera och därmed förbruka för mycket. Hur många andra system i anläggningen arbetar hårdare än de borde, på grund av igentäppta filter, överdimensionerade motorer med mera?
Så ja, en tillverkningsanläggning eller en anläggning för blandad användning kan ge förluster både när det gäller belysning och byggnadsskal. Men är det de förlusterna man först bör ta itu med?
Det går inte att svara på den frågan utan att du först loggar strömförbrukningen för alla större belastningar, jämför den med både pristabellen och driftsschemat och beräknar ROI. Ganska ofta får en anläggning tillräckligt stora underhålls- och driftsbesparingar från stor utrustning, vilket inom några år ger tillräckligt med pengar för att snabba upp bytet av utrustning till snålare modeller.
Hur kan man börja minska energiförbrukningen när budgetar, tid och resurser alltid är begränsade
Arbeta utifrån en referensmätning.
Utgångspunkten är att identifiera var – och när – energi används och av vad. När anläggningsägare, chefer och tekniker förstår exakt hur mycket energi som krävs för att driva verksamheten, jämfört med hur mycket energi som går till spillo, kan de fatta beslut och skapa en plan. För att komma dit börjar du med att ta fram kopior av de senaste elräkningarna och leta efter uppgifter om straffavgifter och tilläggsavgifter för belastningstoppar. Hämta en kopia av pristabellen från elbolagets webbplats, så att du vet hur mycket olika energienheter kostar vid olika tidpunkter på dagen, jämfört med ditt driftschema. Om du vill kan du kontakta elbolagets kundtjänst direkt. De svarar gärna på dina frågor.
Sedan kan du antingen instruera dina egna elektriker eller en elentreprenör att logga effekten på huvudservicenivån samt vid försörjningspanelerna för de största systemen och belastningarna. Registrera kW, kWh och effektfaktor under en representativ period. Det ger en mycket exakt bild av den verkliga strömförbrukningen för trefaskretsar och belastningar. De största besparingarna uppstår ofta när man flyttar drift med hög belastning till tidpunkter på dagen då elpriset är billigare.
Vilka system är de största energislukarna?
Förutom kartläggning av elförsörjningssystemet bör du utvärdera de elektromekaniska systemen, ång- och tryckluftssystemen. Där finns ofta stora energiförluster att hitta, men som går att åtgärda relativt enkelt.
Elektromekaniska system
Det finns fem vanliga typer av energislöseri i ett elektromekaniskt system: 1) elektrisk, 2) mekanisk/friktion, 3) schemaläggning, 4) kontroller och 5) dimensionering/effektivitet.
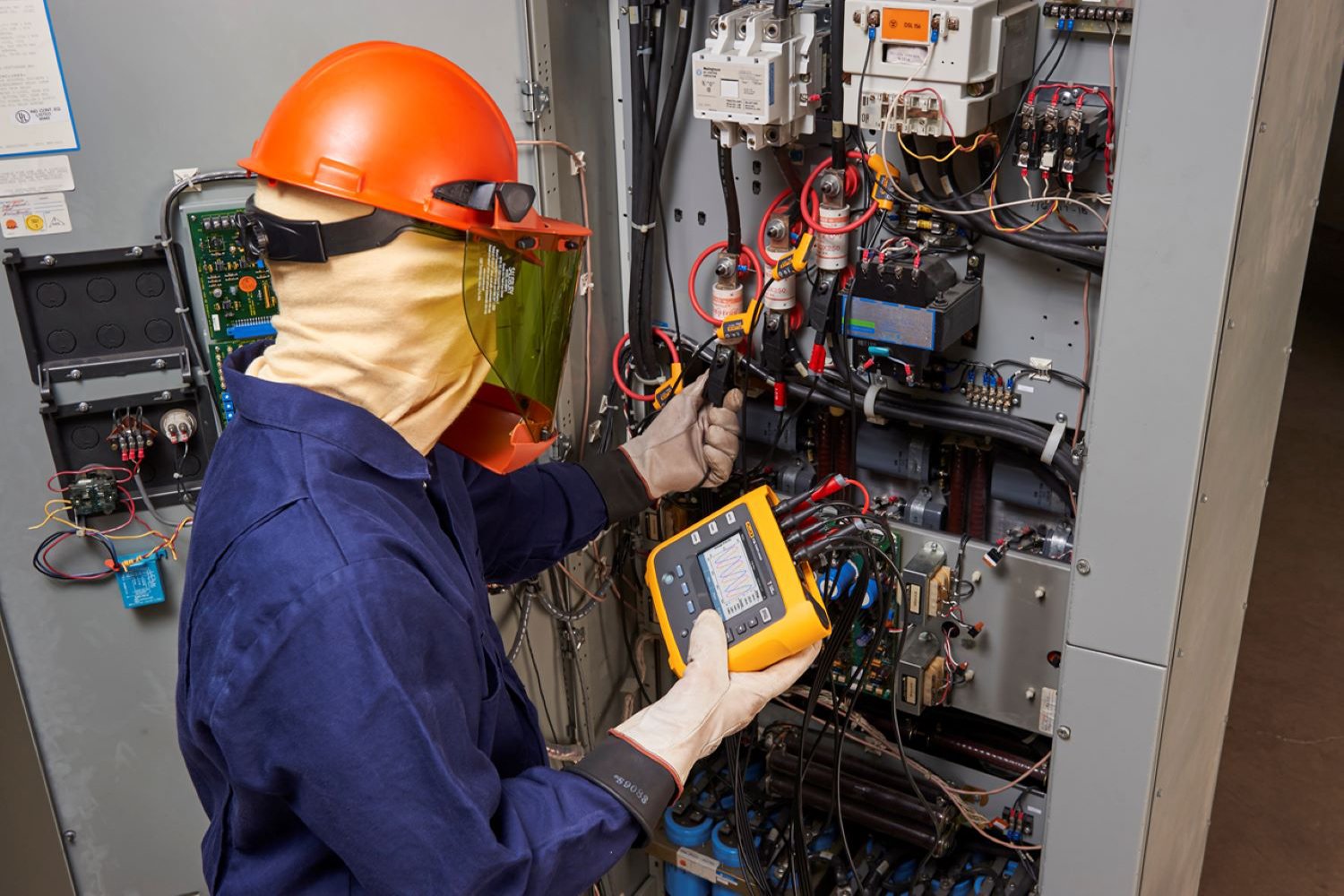
Använda effekt- och energiloggen Fluke 1738 för att utföra en energiundersökning på ett mekaniskt system
- Spännings-/strömöverbelastning och fasobalans är två stora energiförlustpunkter i elektromekaniska system. Båda elproblemen kan upptäckas med elkvalitetsanalysatorer och värmekameror.
- Mekaniska situationer med energiförluster visar sig som både överhettning och överdrivna vibrationer, vilket kan upptäckas med hjälp av värmefotografering och vibrationsmätare. Möjliga orsaker varierar, från kylning och luftflöde till inriktning av lager och andra orsaker till friktion. Värmeskanna kopplingar, axlar, remmar, lager, fläktar, elkomponenter, terminal-/kabeldosa och lindningar – allt som kan signalera ineffektiv drift, och därmed energiförluster.
- Som tidigare nämnts är en av de enklaste lösningarna för att spara energi att logga strömförbrukningen vid stora elektromekaniska belastningar i ett fullständigt driftschema. Avgör när maskinen använder mest energi (ofta vid start) och kontrollera om användningstiderna kan justeras till tider på dagen då elen är som billigast.
- Jämför driftsschemat med hur ofta maskinen använder energi utifrån samma effektlogg. Hur mycket effekt går åt när den inte används aktivt? Om styrreglage inte användes skulle de flesta maskiner behöva stängas av manuellt för att sluta förbruka energi, och manuella åtgärder sker inte alltid. Det går inte alltid att stänga av en maskin, men de flesta kan sättas i viloläge. Styrreglagen varierar från enkla varianter till helt automatiserade, och från att ha sensorer och timers för att på ett flexibelt sätt sätta maskiner i viloläge till hårdkodningar i ett PLC-system.
- Dimensionering och effektivitetsklassificering. Särskilt i äldre anläggningar ändras driftskraven, men belastningarna förblir desamma, vilket ibland innebär att en stor, dyr, svårstartad motor får fortsätta att driva ett system som kräver färre hästkrafter. Det naturliga för alla anläggningschefer är att vilja få ut maximal livslängd av en stor utrustningsdel. Det är dock värt att logga hur mycket effekt motorn använder, jämfört med både faktiska belastningskrav och en ny, högeffektiv enhet i rätt storlek. Beräkna hur mycket överskottsenergi som förbrukas och multiplicera det med pristabellen. Fastställ hur lång tid det skulle ta för en ny motor att betala sig: ibland är det ekonomiskt klokt att byta ut utrustning innan den går sönder. I annat fall bör du överväga om styrreglagen kan användas för att reglera resultatet.
Ånga
Processuppvärmning utgör en stor del av de kontrollerbara driftskostnaderna och systemet måste inspekteras regelbundet för att du ska undvika flera olika energiförlustscenarier.
Börja med att logga energiförbrukningen vid pannan för att få en referenslinje för energiförbrukningen. Inspektera sedan distributionssystemet, inklusive ångventiler, tryckmätare, isolering, pumpar och ventiler. Använd en värmekamera för att upptäcka trasiga ångventiler, läckor, blockeringar, värdeproblem och kondensatfel: målet är att återföra så mycket förvärmt kondensat till pannan som möjligt.
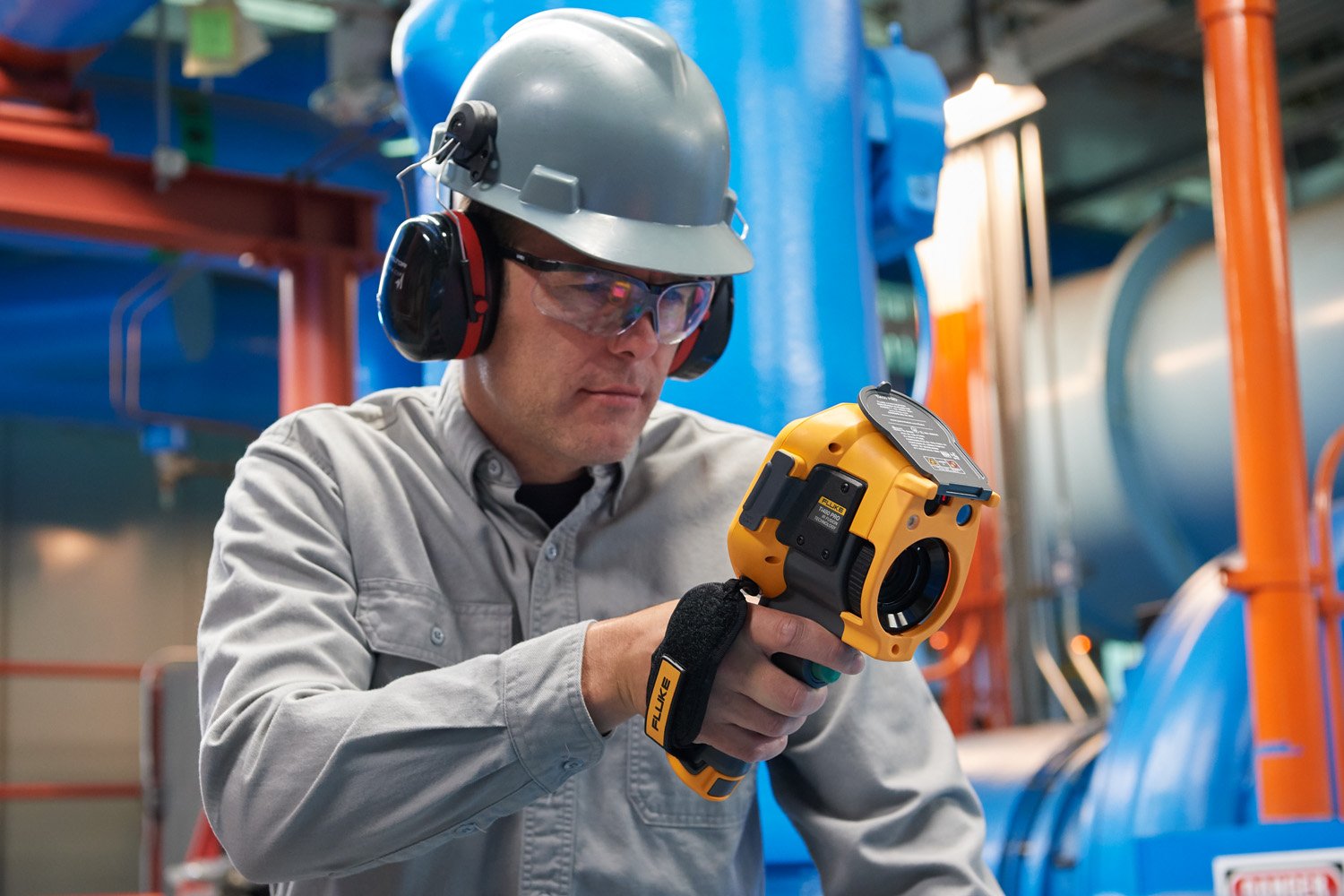
Utföra en inspektion med en Fluke Ti401 PRO-värmekamera
En värmekamera kan också användas för att kontrollera om det finns ångläckage. Kontrollera om isoleringen är lös eller saknas och kontrollera att alla ångventiler fungerar som de ska. Rengör insidan av pannorna och kontrollera att ångledningarna inte är blockerade. De här åtgärderna identifierar energiförluster och hjälper gruppen att hitta energibesparande lösningar – varav många ofta går att implementera via underhåll istället för kapitalkostnader.
Tryckluft
En luftkompressor på 100 hästkrafter kan förbruka runt 50 000 USD i el årligen och så mycket som 30 % av den elen går till tryckluft som aldrig används på grund av läckage och slösaktig användning. Många anläggningar har dock aldrig utvärderat effektiviteten i sin tryckluftsdrift. Faktum är att när mer tryckluft behövs är det många anläggningar som köper och använder en extra kompressor utan att inse att de kan få ut mer tryck ur sitt befintliga system.
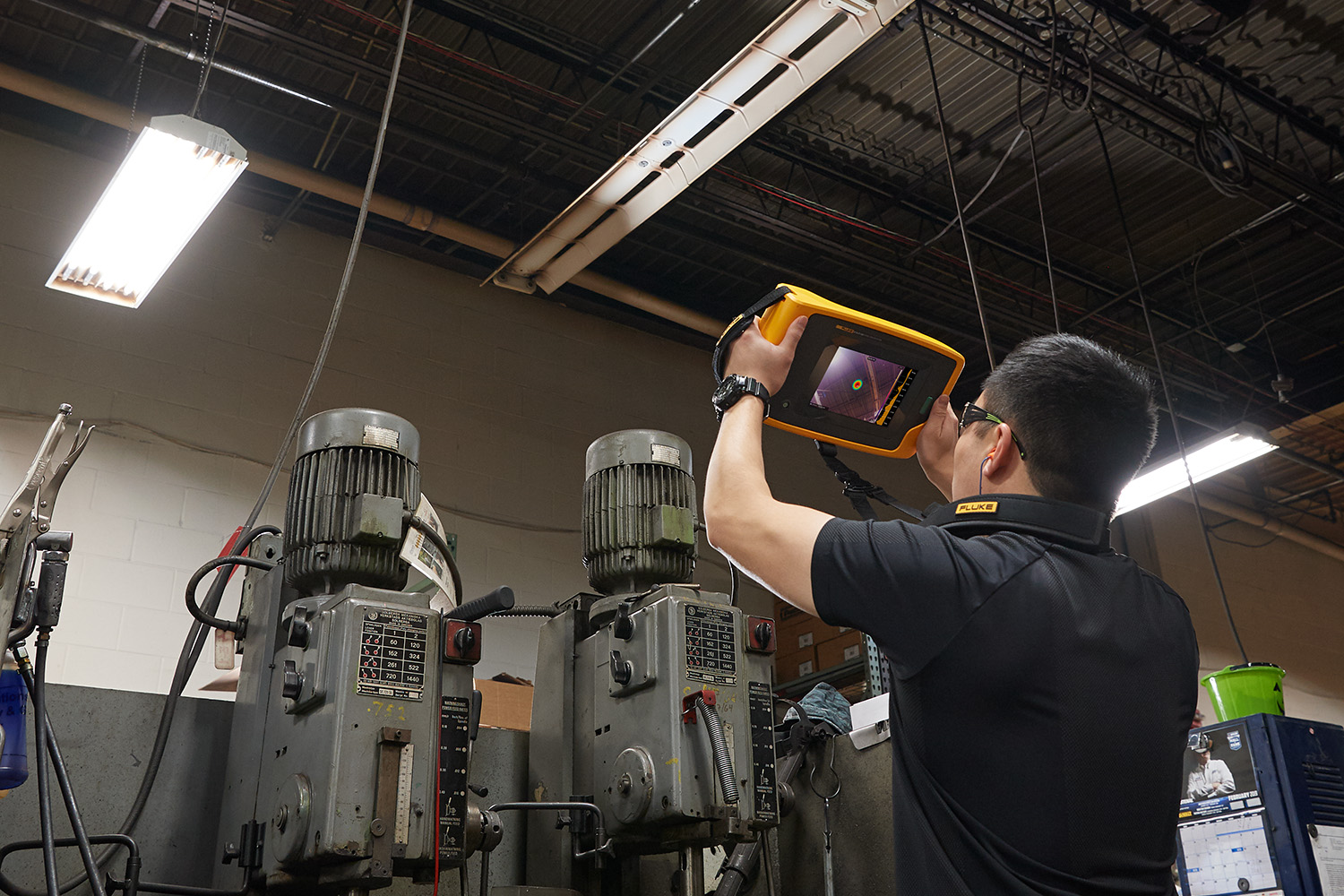
Inspektera tryckluftsledningar med Fluke ii900 Sonic Industrial Imager
Undersökningar av Compressed Air Challenge visade att bara 17 % av användarna av tryckluft värderar effektivitet som ett mål för hantering av tryckluftssystem, men ändå vill 71 % helt enkelt leverera en jämn och tillförlitlig lufttillförsel. Den filosofin visar sig i användningstillfället: installationer av pneumatisk utrustning saknar ofta till och med enkla magnetventiler för avstängning, kompressorn körs hela tiden och verkstadspersonalen behandlar ofta tryckluft som en gratisresurs som de använder för att rengöra arbetsområdet och till och med för avkylning.
För att identifiera och kvantifiera förlustnivån ska du börja med att logga effekten under en hel driftcykel vid alla luftkompressorer. Då kan du slå fast hur mycket energi som krävs för att producera aktuella lufttrycksnivåer. Använd också en tryckmätarkalibrator för att logga psi vid kompressorns uteffekt jämfört med användningspunkten, fastställa hur stort tryckfallet är och kontrollera att tillverkarens psi är vad som krävs för att driva pneumatisk utrustning. Använd inte för mycket tryck ”bara utifall”. En tryckmodul ansluten till en loggmultimeter är ett sätt att utföra testerna på utan att investera i specialutrustning. Slutligen, använd en sonisk industrikamera för att skanna så mycket av luftledningens avtryck som möjligt för att fastställa platsen och omfattningen av luftläckorna. Ta reda på hur stor ROI blir med hjälp av den här luftläckageberäknaren.
Slutsats
Du kan göra mycket för att förbättra energieffektiviteten på anläggningsnivå med de här enkla och okomplicerade metoderna. Var och en har ett värde i sig, men när de kombineras kan de ge stora energibesparingar.