Power monitoring

Power monitoring
Studying power measurements allows teams to observe equipment performance, discover electrical problems, assess how an asset is consuming power, and even if assets are on or off. Examine power variables to detect underlying electrical or mechanical issues.
Top benefits of power monitoring
Condition monitoring strengthens your maintenance and reliability program by:
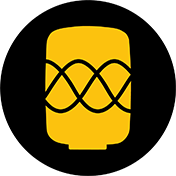
Examine single, split, and three phase systems
Examine voltage, current, and frequency from electrical systems to detect mechanical problems or component wear in assets. When pumps experience issues, such as dirty fans or build up in pump orifices, the motor will show changes in power consumption or load.
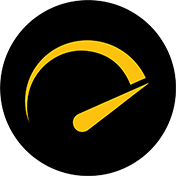
Using one tool for multiple measurements
Find patterns in energy consumption or monitor equipment wear by plotting power measurements over time. By measuring power variables, you can visualize asset health and gain insights into reliability strategies.
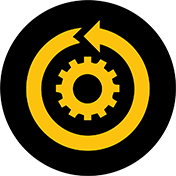
Monitor equipment safely from anywhere
Of equal importance to energy consumption is the quality of power being consumed and the effect on equipment and operations. Total Harmonic Distortion (THD) is a key indicator of potential power problems. Ensure that energy running to assets meets specification.
Speak with a sales representative today to request your personalized consultation.
Related products
Benefit from remote condition monitoring sensors
Condition monitoring typically leverages remote, wireless sensor technologies, including: