Fuel injector pulse width directly affects how much fuel is delivered to the engine. A faulty injector or control signal can result in rich or lean operation, hard starting, poor fuel economy, or performance issues.
Using a tool like the Fluke 88V Deluxe Automotive Multimeter allows you to view the duration of each injection event in milliseconds, helping you spot irregularities in fuel delivery. In this guide, we’ll cover the step-by-step instructions on how to measure fuel injector pulse width with a multimeter.
Why the Fluke 88V Is Ideal for Automotive Use
The Fluke 88V is a trusted multimeter for engine diagnostics. It’s designed for technicians who work on automotive systems and features a 10 MΩ input impedance, which minimizes loading on sensitive circuits while you probe live wiring.
With capabilities such as pulse-width measurement, duty cycle, and high-speed MIN/MAX capture, it lets you see exactly how long injectors stay open. This is vital for diagnosing drivability problems or verifying engine-control-module (ECM) function.
Step-by-Step Guide to Measuring Fuel Injector Pulse Width with a Multimeter
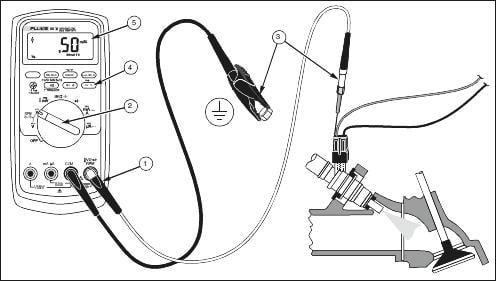
Before you get started, familiarize yourself with the functions on your multimeter that will help you measure injector pulse width:
- Pulse width mode – Press the Hz % button three times to enter pulse-width (ms) mode. Pulse width is the length of time (in ms) that a voltage signal is active.
- Correct jacks – Insert the red lead into V/Ω and the black lead into COM.
- MIN/MAX – Captures the highest and lowest pulse widths under changing engine conditions.
Safety first: Work with the engine off until you’re ready to take live readings. Use proper back-probing techniques, avoid piercing insulation whenever possible, and be cautious around hot components and moving belts. Always secure a solid ground connection so you don’t short adjacent ECM wires.
Quick reference note: Numbers appearing in parentheses after steps—e.g., (3)—correspond to callouts in the Reference Figure: Measuring Pulse Width on a Port Fuel Injector above.
Step 1. Prepare the Multimeter
- Insert the black lead into the COM (1)
- Insert the red lead into the V/Ω (1)
- Set the dial to V DC. (2)
- Press the Hz % button three times until ms appears on the display. (4)
Step 2. Connect to the Injector Signal Wire
- Consult a wiring diagram to locate the injector’s control wire. On most vehicles this is the ground-side driver that the ECU switches low (0 V).
- Back-probe the control wire with the red lead. (3)
- Connect the black lead to a solid engine-block or ground. (3)
Step 3. Start the Engine
- Start the vehicle and let it idle.
- Observe the injector pulse-width reading (ms) on the display. (5)
Step 4. Vary Engine Conditions (optional)
- Lightly press the throttle or vary engine load/RPM.
- Use MIN/MAX mode to capture the injector’s minimum and maximum pulse durations as demand changes.
Step 5. Compare Measurements to Manufacturer Specs
- Typical idle pulse widths range from 5 to 5 ms and increase under load.
- Values too low or too high may indicate:
- Clogged or leaking injectors
- Faulty wiring or poor grounds
- ECM driver issues
Step-by-Step Guide on Testing a Fuel Injector Resistance with a Multimeter
Step 1. Turn Off the Engine and Disconnect the Injector
- Ensure ignition is off.
- Unplug the injector’s electrical connector.
Step 2. Set the Multimeter to Ohms (Ω)
- Turn the rotary dial to Ω
Step 3. Measure Across Injector Terminals
- Touch one lead to each injector pin.
- High-impedance (saturated-drive) injectors usually read 12 to 16 Ω.
- Low-impedance (peak-and-hold) injectors typically read 1 to 4 Ω.
- Always verify the correct range of service data.
Step 4. Compare to Specifications
- Readings outside spec can point to an open coil or internal short. If this is the case, replace the injector.
Tips and Best Practices
- Use MIN/MAX to log injector changes during quick throttle blips.
- Compare cylinder-to-cylinder pulse widths to spot weak or sticking injectors.
- Avoid piercing wires; use back-probe pins or a breakout harness.
Conclusion
Measuring fuel injector pulse width with a multimeter confirms whether the ECM is commanding the fuel system correctly and reveals injector performance under real-world conditions. With its high input impedance, dedicated pulse-width mode, and fast capture features, the Fluke 88V is uniquely suited for this kind of troubleshooting.
Click here to learn more about the meter’s automotive-specific functions.