By Sean Anderson, Fluke Application Specialist
Rotary encoders are critical components in conveyor systems, providing essential feedback on shaft motion to ensure smooth, efficient operation. Yet diagnosing faults — particularly intermittent or subtle electrical problems — can be difficult. While a digital multimeter (DMM) can capture static measurements, it cannot visualize real-time signal behavior. That’s where an oscilloscope comes in: it provides a detailed view of dynamic signals, helping technicians detect noise, timing discrepancies, or waveform distortions.
In this article, we’ll explore how to use an oscilloscope to diagnose rotary encoder issues in conveyor systems. You’ll learn the step-by-step process, key signal parameters to measure, and why focusing on root causes of rotary encoder issues can lead to more reliable, long-term solutions.
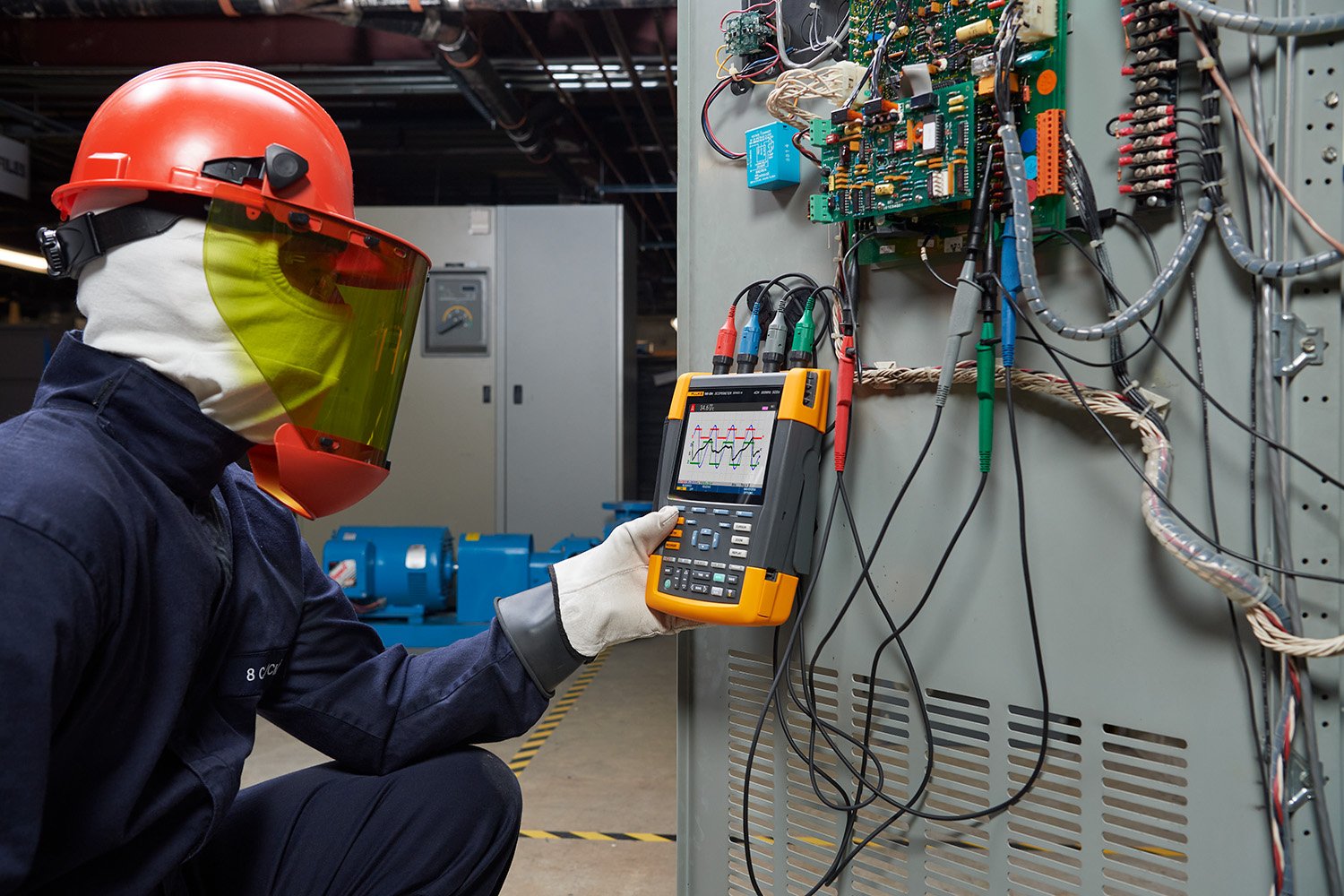
Understanding Rotary Encoders
Rotary encoders convert rotational motion into electrical signals, which can indicate shaft position, direction, or speed. Conveyor systems use this feedback to maintain accuracy and avoid production delays. Two common types of encoders include:
- Incremental encoders: Generate pulses that track movement but lack an absolute reference for position.
- Absolute encoders: Provide a unique code for each rotational position, enabling more precise monitoring and control.
Why an Oscilloscope vs a Multimeter?
While a DMM can detect voltage levels or check continuity, it cannot capture the rapid, time-based variations that often characterize rotary encoder output. Problems such as high-frequency noise, erratic pulse spacing, or missing pulses remain invisible without the real-time visualization provided by an oscilloscope.
Using an Oscilloscope to Diagnose Rotary Encoder Issues
- Connect and Configure
- Identify encoder channels: Determine which output lines (e.g., Channels A and B) you need to examine and select the correct probes for the signal you’ll be measuring.
- Attach oscilloscope probes: Connect the probe tip to the encoder signal line and ground the scope properly. With encoder circuits, the ground reference may vary from standard configurations. Verify that the oscilloscope’s ground aligns with the encoder wiring. If necessary, use differential or isolated probes to prevent ground loops and accurately measure common-mode voltages.
- Set time base and vertical scales: Choose an appropriate time scale to see multiple pulses. Set the voltage scale to capture the expected signal amplitude clearly.
Why this matters: Proper time-base settings allow you to see if pulses are consistently spaced (timing) and have sharp transitions (signal integrity). An improperly-set time scale can compress or expand the signal too much, making anomalies easy to miss.
- Observe and Measure
Once connected, power up the conveyor (or rotate the encoder shaft manually, if possible) and observe the waveform:
- Frequency or pulse rate: Confirm the measured rate matches the encoder’s documented specification.
- Duty cycle: Many encoders produce roughly 50% on/off pulse widths. Significant deviations may indicate an internal fault or wiring issue.
- Waveform integrity: Check that square waves have clean transitions with minimal ringing or distortion.
- Investigate Common Signal Issues
An oscilloscope excels at revealing:
- Noise: Look for high-frequency spikes or irregular oscillations on what should be a stable square wave. Noise often originates from poor shielding or electromagnetic interference from nearby machinery.
- Pulse skew or missing pulses: If the encoder is skipping pulses or producing uneven intervals, your control system may report inaccurate position or speed.
- Timing errors: Measure intervals between pulses to see if they’re consistent. Erratic timing disrupts the encoder’s feedback loop, leading to conveyor misalignment or sporadic stops.
Key Parameters to Measure
To streamline diagnostics, focus on these critical measurements:
- Voltage amplitude (high/low levels) – Confirm the output voltage is at the expected high and low states.
- Frequency or pulse rate – Verify that the pulse frequency aligns with the encoder’s specification at a given shaft speed.
- Duty cycle – Assess whether pulses are balanced or if there’s an unexpected shift in pulse width.
- Rise/fall time – Observe how quickly the signal transitions from low to high (and vice versa). Slow edges can hint at wiring or encoder circuit problems.
- Noise – Scan for unwanted spikes or irregular waveforms that may indicate grounding or interference issues.
The Value of a Root Cause Approach (and Why It’s Useful)
Identifying anomalies in the encoder’s signal is the first step, but true reliability comes from fixing the underlying factors. By tracing noise or timing errors back to their source — be it a shielding problem, faulty wiring, or internal encoder wear — you can implement a lasting solution rather than repeatedly troubleshooting recurring issues. This “root cause” approach reduces downtime, saves costs on replacement parts, and ensures smoother long-term conveyor performance.
Real-World Case Study: Conveyor Stops and Position Errors
A conveyor system experiences frequent, unpredictable halts. Basic checks with a DMM reveal no obvious electrical faults. Technicians then use an oscilloscope for in-depth analysis.
- Scope connection: They attach the scope to the rotary encoder’s A and B channels.
- Waveform analysis: The live waveform shows sporadic high-frequency noise and inconsistent pulse intervals.
- Root cause findings: Further inspection points to a damaged shield in the encoder cable and slightly worn encoder internals.
- Solution: The technicians repair the cable shielding and replace the degraded encoder. This restores stable signals and reliable conveyor motion.
The Advantages of Using an Oscilloscope
Compared to a digital multimeter, an oscilloscope uncovers deeper insight into rotary encoder performance:
- Real-time visualization: Instantly see signal shape, timing, and anomalies.
- Precision diagnostics: Accurately measure frequency, duty cycle, rise time, and pulse spacing.
- Detection of subtle issues: Catch intermittent or seldom-occurring distortions that conventional tools often miss.
By incorporating oscilloscopes into your regular diagnostic workflow, you can rapidly isolate elusive problems, reduce system downtime, and maintain more accurate process control.
Conclusion
Rotary encoders form the backbone of precision in many conveyor systems. Diagnosing issues within these devices requires a tool that can visualize their dynamic signals. An oscilloscope provides exactly that, from identifying noise and timing glitches to capturing missing pulses or subtle waveform distortions.
Equally important is tracing anomalies to their root cause — be it shielding deficiencies, wiring faults, or encoder wear — so the final fix is both comprehensive and lasting. By focusing on the critical parameters outlined here and leveraging real-time diagnostics, you can significantly enhance conveyor reliability and production efficiency.
Explore Fluke oscilloscopes to find the best fit for your application, and start harnessing the power of advanced signal visualization for a more efficient, trouble-free conveyor system.
About the Author
Sean Anderson has been a Product Application Specialist at Fluke since 2024, drawing on his AD01 Electrical Administrator background and power systems knowledge to deliver comprehensive support and expert guidance for users of the multimeter, clamp meter, and oscilloscope product lines. Since joining Fluke, Sean has focused on customer-facing research to assist in developing innovative new products and educational resources for core electrical test and measurement tools. With a commitment to customer satisfaction, great user experience, and clear communication, he continues to empower professionals in the field through hands-on service and support. Connect with Sean on LinkedIn.