Uncertainty analysis is a critical step in calibration that sheds light on the accuracy of any measurement tool. As such, it can be critical to understanding the true performance and health of whatever components or systems a measurement tool is testing.
In this article, we’ll review how uncertainty analysis relates to calibration, why it’s important to a proper calibration process, and how to set your calibration services up with a good uncertainty analysis process in mind.
What Is Uncertainty Analysis?
Uncertainty analysis is the process of evaluating what’s called measurement uncertainty: the degree of doubt about a measurement. In other words, when you perform an uncertainty analysis, you evaluate how different potential sources of errors impact the accuracy of a specific measurement. By recognizing and quantifying potential errors associated with a measurement, you can estimate its total uncertainty; this uncertainty is expressed as a range, with the true measurement lying somewhere between that range.
Uncertainty analysis is essential for any professional who relies on precise measurements to provide customers with safe and effective products. This includes professionals who conduct experiments, create products, and perform quality control testing in many industries, such as:
- Pharmaceutical
- Energy
- Automotive
- Aerospace
- Research and development
- Manufacturing
Uncertainty analysis allows professionals in these fields to determine whether the specialized tools and processes they use to quantify measurements are functioning properly and capturing accurate measurements.
Why Is Uncertainty Analysis Important to the Calibration Process?
Uncertainty analysis is important to the calibration process, because it’s critical to understanding how accurate a measurement tool is and if it needs further calibration. In fact, some metrology quality standards, like the ISO 17025, require calibration laboratories to report the measurement uncertainty of a device to customers in order to remain compliant.
Additionally, performing an uncertainty analysis and reporting measurement uncertainty helps users understand whether or not an instrument is measuring within tolerance, or the range of accepted values. Understanding where an instrument falls within a tolerance range is key to determining its calibration accuracy, a percentage value that shows how close the test results are to a standard value. The closer that percentage is to zero, the more accurate the calibration is. (Note that typically, metrology labs aim for a test uncertainty ratio (TUR) of 4:1 for calibrations, meaning the standard with which the measurement tool is being calibrated should be four times more accurate than the tool or device under testing (DUT).)
After completing an uncertainty analysis and calibrating the instrument, you can test for precision and accuracy by ensuring it consistently provides the same results within specific error limits. This is essential for traceability, as it allows you to track the readings back to an industry standard — the gold standard for any good calibration service.
How To Account for Uncertainty Analysis When Setting Up a Calibration Lab
When you have an effective procedure for uncertainty analyses in place at your lab, you can prepare your customers’ equipment to manage their metrology needs successfully. Here are a few steps you can take to get started:
1. Define the Scope of Work
Whether you plan to run an on-site or mobile calibration lab, the first step to consider when determining how you’ll conduct uncertainty analyses is the scope of your work. Think about the industries you’ll serve, the families of measurement tools that are most applicable to those industries and what their calibration needs will be so you can customize your process to meet their requirements. Examples of the different families of measurements tools you might need to calibrate include:
- Electrical
- Radio frequency (RF)
- Humidity
- Pressure
- Temperature
- Flow
For instance, if you plan to serve pharmaceutical manufacturers, you need to know what sort of monitoring and measuring they conduct for their operations. They likely use an array of measurement tools to monitor and maintain humidity levels, electrical systems, pressure systems, and more. Therefore, you’ll need to set up your lab to calibrate measurement tools from the humidity, pressure, and electrical families at a minimum.
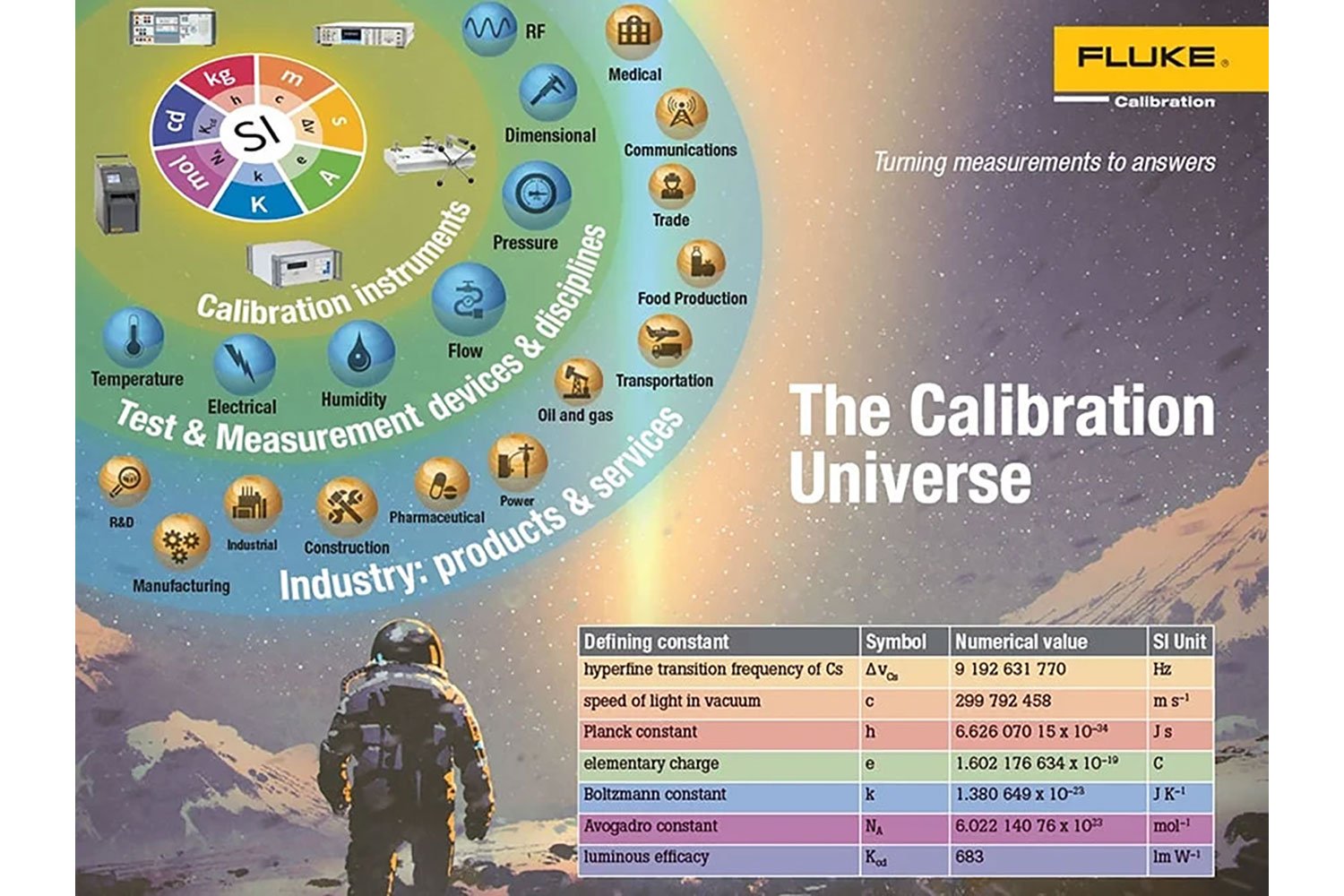
2. Identify Calibration Standards and Certifications
Next, research the calibration standards that pertain to your customers’ industries. Going back to our pharmaceutical manufacturers example, given the variety of systems and measurement tools they use, your lab will at least need humidity, pressure, flow, electrical standards.
Here are some popular standards and calibration equipment for each family of measurement tools:
- Electrical: Voltage reference standards, current reference standards, Kelvin-Varley dividers, alternating current (AC) measurement standards, alternating current/direct current (AC/DC) transfer standards, and frequency standards
- Radio frequency (RF): Low phase noise reference sources
- Humidity: Humidity generators and thermo-hygrometers
- Pressure: Piston gauges, deadweight testers, pressure monitors, and comparison test pumps
- Temperature: Calibration baths, benchtop temperature controllers, thermometer readouts, thermo-hygrometers and temperature scanners
- Flow: Gravimetric mass flow systems and gas flow standards
From here, you can choose the types of certifications you want to pursue so you can offer relevant accreditations. For example, you might want to become ISO/IEC 17025 certified so that you can provide your customers with ISO 17025 accreditation.
3. Review the Steps for Proper Uncertainty Analysis
The process of calculating a tool’s measurement uncertainty can be tedious, but that doesn’t mean it has to be difficult. To ensure that you’re being as thorough as possible, you’ll want to ensure you have a solid grasp on the right steps involved in an uncertainty analysis before you establish your lab’s processes:
- Identify and eliminate external sources of uncertainty (environmental factors, equipment limitations, etc.).
- Estimate standard uncertainties, which is a collective term for Type A uncertainties (quantitative measurements you gain from repeatable tests) and Type B uncertainties (all other uncertainties that aren’t Type A).
- Determine the probability distribution of the standard uncertainties. (This will likely be either a normal distribution or rectangular distribution.)
- Convert the standard uncertainties to standard deviations.
- Combine the uncertainties using the root sum of square.
- Calculate the expanded uncertainty using a k factor.
Of course, the above is just a general overview of the steps. Please see our more detailed guide for a deep dive on how to calculate measurement uncertainty.
4. Use the Right Tools and Software
Once you’ve decided on a standard, it’s time to purchase tools for your lab. You’ll need the right calibrators, software, and accessories to perform uncertainty analyses and calibrate your customers’ equipment accurately. A reputable calibration equipment provider like Fluke Calibration can help you stock your laboratory with all of the precise, pre-certified instrumentation you need all in one place.
Want to learn more? Review our robust calibration product offerings or review these related resources: