How To Calibrate a Clamp Meter: A Step-By-Step Guide
Technicians and other experts who work with electrical systems use clamp meters in a variety of settings, from testing products on the manufacturing floor to troubleshooting residential electrical systems. Professionals rely on these tools to measure electrical current and trust that their devices will make accurate assessments so they can do their jobs safely.
Over time, clamp meters will lose accuracy and no longer measure within the manufacturer’s specifications (specs). By periodically calibrating clamp meters, you can restore them to their original specs, instilling confidence in the measurements they take until their next calibration.
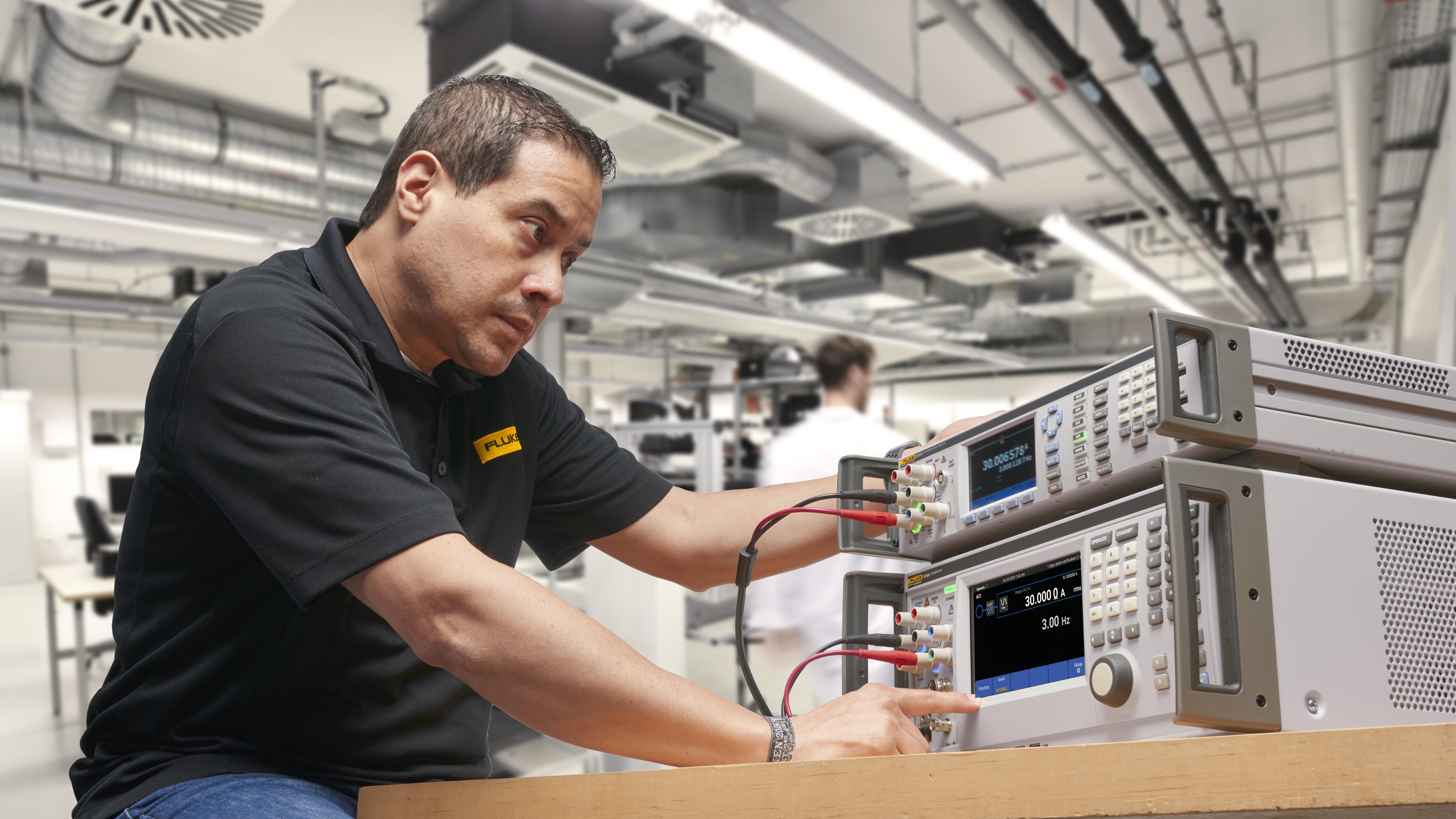
In this article, we’ll walk through the step-by-step process of calibrating a clamp meter, the necessary equipment for calibrating, and some important factors to consider before calibrating.
What Is a Clamp Meter?
A clamp meter is a device used to measure current, voltage, and continuity in electrical applications. Its most distinguishing feature is a hinged jaw that takes measurements by wrapping around electrical cables, wires, and conductors.
In order to measure electrical current, clamp meters sense the magnetic field that electrical flows produce. This non-contact approach allows users to take measurements without breaking a circuit or directly interacting with live voltage.
Most modern clamp meters are digital, multifunction devices, blending the capabilities of a basic digital multimeter (DMM) with a current sensor. High-quality clamp meters include the following features:
- Current-sensing jaw
- Tactile barrier to protect from electrical shock
- Hold button to freeze display reading
- Dial or rotary switch
- Display
- Backlight button
- Min/max button to show minimum, maximum, and average inputs in current, voltage, and frequency modes
- Inrush current button
- Zero button (removes Direct Current (DC) offset from DC current measurements and serves as shift button to select functions scattered around the dial)
- Jaw release lever
- Alignment marks to ensure measurement accuracy
- Common input jack
- Volt/Ohm input jack (positive and negative)
- Input for flexible current probe
Why Do You Need To Calibrate a Clamp Meter?
Like all measurement tools, clamp meters eventually lose their accuracy. Parts get dirty and wear down, and internal electrical components shift after months and years of use. That means, eventually, your meter won’t take accurate readings like it did when you first bought it — a phenomenon known as drift.
These mistakes can be costly for organizations that work with electronics and electricity. Even small measurement mishaps can cascade into huge production errors, resulting in lost or damaged inventory. Not to mention the fact that electrical work becomes more dangerous when electricians can’t get accurate voltage and current readings on components they’re trying to fix.
Calibration is a necessary part of ensuring safety and accuracy when it comes to taking electrical measurements. Clamp meters typically require yearly calibration to keep the device performing within their original specs from the manufacturer. Though sometimes, users need to calibrate more often if someone recently dropped the clamp meter or if someone plans to use it soon to take critical measurements for an upcoming project.
Necessary Equipment for Clamp Calibration
Before you start the calibration process for your clamp meter, make sure you have the following equipment:
- A multi-product calibrator, like the Fluke 5560A, 5550A, 5540A, and 5530A series of multi-product calibrators
- The appropriate current coil for the device under test, like the Fluke 5500A/COIL and 55XXA/COIL 10
- If necessary, a current amplifier or a current coil with a built-in amplifier like the Fluke 52120A/COIL3KA or the 52120A/COIL6KA coils
Because most clamp meters today are multifunction tools, you’ll need a multifunction calibrator to test and adjust all of their functions. Knowing what kind of coil you’ll need – 1-, 2-, 10-, or 50-turn, for example – is important.
Most multifunction calibrators can accommodate current up to 1,000 amperes (amps). If your application requires more than 1,000 amps, though, you’ll need an amplifier as part of your calibration system.
Seven Considerations for Clamp Meter Calibration
To ensure the process of calibrating your clamp meter is accurate and thorough, there are a number of factors to consider before you begin. Here are seven major considerations to make before beginning calibration:
- Clamp meters vary in shape and size. Varying jaw widths and ergonomics can pose challenges for calibration. It’s important to choose the right calibration instruments for your specific clamp meter.
- Most modern clamp meters have multifunction capabilities. Today’s clamp meters have many of the same functions as a DMM. In addition to measuring current, they can measure voltage, resistance, and continuity. Because of this potential variability in capabilities, knowing which functions your clamp meter can perform is important so you can calibrate each measurement function properly.
- Not all calibrators are created equal. Your calibrator must have enough compliance voltage to drive a coil. Combined coil and clamp inductance can cause issues, so be sure to use the proper coil for your application, as not all sources are designed to be used with current coils. Fluke uses inductive compensation (L-COMP) to increase compliance voltage to drive inductive loads.
Also note that all calibrators have some degree of error, so they must also have enough accuracy for your application, which you can easily find in the specification manual.
- Take note of thewinding (turns) and range of your current coil. The coil you use for calibration must have enough turns to test the entire range that an end user might measure with the clamp meter. Windings determine the amount of current; you can calculate them with this equation:
Coil windings (turns) x Source input (amps) = Apparent current (amps)
For example, a 50-turn coil with 20 amperes (amps) will generate 1,000 amps of current that you can use to test the meter.
- Don’t forget the accessories. Some clamp meters require a flexible current probe in order to expand current measurement range or measure certain types of conductors. The Fluke i2500-10 iFlex® is one such example. You must calibrate these accessories along with the clamp meter.
- Remember that high-current tests come with safety risks and time limits. When current flows through a coil, it generates heat – and gets hotter at higher currents. Fluke coils include a cover that can help dissipate heat during the calibration process. Additionally, though Fluke coils calibrate continuously at low currents, at higher currents, they have time on/time off limits. As such, always note your coil’s maximum operating time for whatever current levels you’re testing, and plan your calibration accordingly.
- Positioning is important. How you align your clamp meter with the coil can be the difference between the device being in and out of tolerance. You need to position the clamp meter axis so that it’s parallel to the coil axis. Meanwhile, you must ensure the clamp jaw plane is perpendicular to coil conductors. Newer Fluke coils include graphical guide lines on the clamp meter to help ensure proper alignment and thus, proper measurement. These guides also ensure your calibrations are repeatable.
When calibrating, also be sure your calibration system is set up in a location that’s free from interfering fields from other equipment and any current-carrying leads that might be nearby.
The Calibration Process: A Step-By-Step Guide
Once you’ve gathered the proper equipment, calibrating your clamp meter requires three main steps:
Step 1: Evaluate the Clamp Meter and Its Accessories
Whether you’re calibrating your own clamp meter or one for a customer, it’s important to note the date of the device’s last calibration and its age. This tells you what to expect when working with the instrument. For example, a 10-year-old clamp meter will require more care and attention than a newer one, and a device that hasn’t been calibrated in three years will likely require more time than one that was calibrated just a year ago.
Always thoroughly inspect the clamp meter before calibrating. End users can use clamp meters in all types of environments, so the device may require some tidying and even repair before calibration. If you do detect damage, don’t begin calibration until you can test the clamp meter to make sure it’s safe to work with.
Next, check any batteries. Changing the batteries before calibration helps ensure accurate measurements, though this step is more important for analog clamp meters than digital ones. You can take also two measurements: one measurement with the original batteries (initial reading) and one with new batteries (final reading).
Additionally, double-check that you have all of the clamp meter’s accessories ready, too, since you’ll need to calibrate them along with the tool.
Step 2: Prepare Required Calibration Equipment and Documentation
It’s important to understand the manufacturer’s specifications and required equipment for each clamp meter you calibrate. Answer the following questions during preparation:
- Are specs available for the instrument?
- Do I have the right equipment to calibrate this instrument?
- If the clamp meter is out of tolerance, how can I adjust it?
Most manufacturers list specs and adjustment processes online, but this varies between companies. If this information isn’t available, regional organizations like the European Association of National Metrology Institutes (EURAMET) have calibration guidelines available for different types of instruments.
If you’re planning any adjustments to the clamp meter after calibration, keep in mind that you shouldn’t start calibration if you don’t have an adjustment procedure ready – otherwise, you’ll only get halfway through the process. Adjustment may not be necessary in every scenario, though. Just make sure you have all the necessary documentation and know what your end goal is for the calibration process before beginning.
Step 3: Perform Necessary Calibrations
The goal of calibrating your clamp meter is to match the tool to the manufacturer’s original specifications. Most labs do what’s called an as-found calibration first, followed by an adjustment calibration and as-left calibration. However, the differences between adjustment and as-left calibration varies depending on each lab’s internal quality requirements and industry. For example, the biomedical industry typically has different requirements for adjustment and as-left calibrations than manufacturing.
Your laboratory’s internal requirements, specifications, and process for reporting results will dictate the calibration process. Make sure to acquire all necessary internal documentation to complete calibration accurately according to lab standards.
Ensure an Easy, Accurate Calibration of your Clamp Meters
By now, it’s clear that calibration is a necessary process for maintaining the accuracy of test equipment like clamp meters.
Fluke Calibration carries a flexible selection of calibrators to calibrate clamp meters and more. Want to learn more? Please check out Fluke’s multi-product calibrators and review these related resources: