Finn energitap i industrien
Når det gjelder energisparing, finnes det en intensjon og en plan. Industribedrifter i USA viser et vedvarende engasjement for energistyring. Intensjonen deres er å redusere det totale energiforbruket, eller opprettholde forbruket, men øke produksjonen per forbrukte kW.
Og planen? Den kan by på problemer.
Produksjonsplaner er bare holdbare hvis visjonen bygger på erfaringens visdom og avkastningsberegningene viser lønnsomhet. Men for energi finnes det rett og slett ikke nok forskning som fabrikksjefer kan bruke til å si hva som er rimelig energiforbruk i produksjonsanlegg. Hvordan vurderer vi så hvilken del av det nåværende energiforbruket som er rimelig og hva som er sløsing, og hvor mye av sløsingen det vil gi nok avkastning å ta tak i?
Her er det snakk om avkastning i form av sparte kostnader per kWh på strømregningen. Summene vil variere avhengig av tidspunkt på dagen og tiden av året. Besparelsen ligger i å redusere disse utgiftene. Investeringen er materialene og arbeidskraften som kreves for å endre energiforbruket. Inntjeningstiden er den tiden det tar før den lavere strømregningen betaler for investeringen. Gevinsten kommer etter at kostnaden er nedbetalt.
Tilbake til planen, hvordan utarbeider vi et estimat for avkastning når det ikke finnes noen bransjestandard for energiforbruk?
Profilering av energiforbruk i industrien
Energiforbruk i industrien varierer på grunnlag av flere variabler:
- fabrikkens alder
- lasttype og -størrelse
- driftsplan, både timer per uke og lastintensitet
- antall arbeidere
- klima
- vedlikeholdsfilosofi
Svaret er følgende: Ikke prøv å styre hver eneste kW fabrikken bruker. Det er dette som er «erfaringens visdom» i ligningen. Del fabrikken inn etter elektrisk infrastruktur og deretter de viktigste systemene.
Energisparing begynner med to grunnleggende taktikker: (1) generell inspeksjon av nøkkelsystemer og (2) målrettet datainnhenting, herunder logging av energiforbruk ved hovedinntaksboksene og nøkkellastene.
Finn ut hvor mye et system er spesifisert til å forbruke, bestem hvor mye det forbruker på nåværende tidspunkt og avdekk sløsing, enten på grunn av driftstid og -type, eller selve utstyret og systemet. Bedriften må ta tak i sløsingen, enten ved å foreta endringer i driften, i vedlikeholdet eller i utstyr og regulering, for å oppnå besparelsene.
Energikomponenter
Før vi forklarer hvordan energiforbruket kan spores, skal vi se på hvordan vi definerer og måler energi.
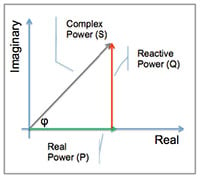
Energi uttrykkes i reell, reaktiv og tilsynelatende effekt (figur 1).
Energiflyt beskrives som
- reell (P) eller aktiv effekt i watt (W)
- reaktiv effekt (Q) i voltampere reaktiv (VAR)
- kompleks effekt (S) i voltampere (VA)
- tilsynelatende effekt, størrelsen til kompleks effekt (VA)
Det matematiske forholdet mellom reell, reaktiv og tilsynelatende effekt kan fremstilles ved hjelp av vektorer eller uttrykkes ved hjelp av komplekse tall, S = P + jQ (der j er den imaginære enheten).
Reaktiv effekt overfører ikke energi – den produserer ikke arbeid – så den fremstilles som den imaginære aksen i vektordiagrammet. Reell effekt beveger energi og er dermed den reelle aksen.
Størrelsen på energiflyten i et system avhenger av lasten – er den resistiv, reaktiv eller begge deler?
Med en rent resistiv last skifter spenning og strøm polaritet samtidig, produktet av spenning og strøm er positivt til enhver tid, og bare reell effekt overføres: Det produseres arbeid.
Hvis lasten er utelukkende reaktiv, er spenning og strøm faseforskjøvet, og produktet av spenning og strøm kan være positivt eller negativt – noe som indikerer at en del av energien overføres til lasten, og en del flyter tilbake. Netto overføring av energi til lasten er null: Ikke noe arbeid blir produsert.
I virkeligheten har alle laster en kombinasjon av resistans, induktans og kapasitans; det skaper både reell og reaktiv effekt i et system. Derfor er elektriske systemer laget for å tåle en viss mengde reaktiv effekt. Problemet oppstår når det genereres for mye reaktiv effekt. Ikke bare er det ikke nok reell effekt til å produsere det nødvendige arbeidet, men systemets totale kapasitet til å generere arbeid står på spill. Derfor ilegger strømleverandørene kundene sine gebyr hvis lastene deres skaper for mye reaktiv effekt. Det er bortkastet effekt som det koster penger å produsere, men som ikke kan benyttes. VAR (reaktiv effekt) er som oftest oppført på strømregningen, og mange leverandører beregner effektfaktor, der effektfaktoren er en klassifisering av hvor langt under 100 % reell effekt en installasjon har falt. De fleste strømleverandører krever at kundene deres holder seg over 0,95 PF (effektfaktor).
Sporing av energiforbruk
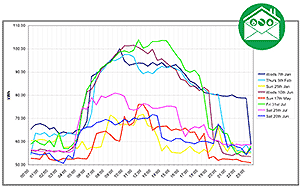
Forståelsen av basiskomponentene i energi gjør at en elektriker kan sette opp energiloggingsutstyr for å måle det totale nivået og kvaliteten på forbruket, og deretter kontrollere når og til hva energien blir brukt (figur 2).
Logg effekt ved hoved- og sekundærtavler og ved store laster. Registrer kW, kWh og effektfaktor i løpet av en representativ tidsperiode.
Dette gir et svært nøyaktig bilde av det reelle effektforbruket på trefasekretser og -laster.
De største strømbesparelsene kommer av å fastslå når effektforbruket er på sitt høyeste, evaluere effektfaktoren og det totale effektforbruket og sammenligne med strømregningene, og ombalansere lasten om mulig. Selv bare et par minutters toppforbruk kan øke strømprisen i et par timer, dager eller uker.
Utsatt kjøring av laster kan gjøre det mulig for et selskap å utnytte tidspunkt når strømmen er billigere. Se hvor langt under «1» effektfaktoren er, og kontroller strømregningene for å se om det er gebyrer for dårlig effektfaktor. Hvis det er det, kan effektloggeren bidra til å spore opp kildene. Etter at du har foretatt energioppgraderinger, kobler du til loggeren igjen, for å dokumentere fordelene med forbedringet virkningsgrad.
Forstå energitapspunkter
Hvert system og operasjon er et potensielt energitapsspunkt som kan modereres eller rettes på. Elektriske delsystemer, trykkluft, damp og spesifikke elektromekaniske systemer er gode steder å begynne, men hver operasjon har sine egne potensielle tapspunkter som bør måles.
Målet er å kartlegge energibruken for spesifikke utstyrsenheter og prosesser for å se hvor energien sløses bort, slik at du kan kvantifisere tapet og prioritere forbedringer eller utskiftninger på grunnlag av utstyrets levetid og hvilke endringer som kan gi best avkastning på investeringen.

Energikartlegging gir også basisinformasjon som du kan måle effekten av energisparingsprosjektene ut fra, for å forsvare kostnadene (figur 3).
Vanlig energitap i elektriske delsystemer:
- Laster som vanligvis blir stående på etter arbeidstid eller kjører unødig når strømprisen er høyest.
- Ingen regulering av motoren kan bety at det skapes mer effekt enn nødvendig.
- Overstrøm/overspenning kan forårsake overdrevent effektforbruk for å kompensere.
- Faseusymmetri får lasten til å forbruke effekt uten å kunne utnytte den.
Identifiser og kvantifiser:
- Foreta en termisk skanning av eltavlen og den mekaniske lasten for å se etter overoppheting.
- Logg effekten over tid: Hvor mye effekt forbrukes på hvilket tidspunkt, og hvor mye sløses bort?
Vanlige energitaps- og inspeksjonspunkter i elektromekaniske systemer:
- Overdreven friksjon fra justering, lagre, ubalanse og slark overbelaster motoren; det forbruker mer effekt enn nødvendig.
- Uregulerte laster som står på etter arbeidstid, kjører når strømprisen er høyest, skaper mer effekt enn nødvendig eller er utsatt for overstrøm/overspenning og faseusymmetri.
- Eldre mekanisk utstyr forbruker så mye mer effekt enn nye, høyeffektive modeller, at tidlig utskiftning kan forsvares bare på grunn av redusert kWh-forbruk.
Identifiser og kvantifiser:
- Foreta en termisk skanning av driftstavlen og den mekaniske lasten for å se etter overoppheting som indikerer elektrisk ineffektivitet.
- Logg effekten over tid, kontroller totale kWh, effektfaktor, toppetterspørsel, usymmetri og harmoniske oversvingninger.
- Test vibrasjonsnivåene mot standardene, og finn vedlikeholdsløsninger som ombalansering.
- Foreta en termisk skanning av koblinger/aksler/belter, lagre og vifte.
- Kontroller strøm- og spenningsnivåer.
- Foreta en termisk skanning av terminerings-/koblingsboks og viklinger, og gjennomfør en isolasjonsmotstandstest.
Vanlige energitaps- og inspeksjonspunkter i trykkluftsystemer:
- Overdrevne lekkasjer i trykkluftledninger fører til unødvendig drift for å opprettholde forsyningen.
- Kompressorer som blir stående på når de ikke er i bruk, sløser bort energi.
Identifiser og kvantifiser:
- Effektlogging ved kompressoren gir basisinformasjon om forbruket.
- Mål trykket ved kompressoren og brukspunkter for å fastslå størrelsen på trykktapet.
- Skann ledningene med ultralyd for å finne lekkasjer.
Vanlige energitap og inspeksjonspunkter i dampsystemer:
- Defekte kondenspotter og utilstrekkelig isolasjon sløser bort damp og fører til overproduksjon for å opprettholde nødvendig forsyning.
Identifiser og kvantifiser:
- Effektlogging ved kjelen gir basisinformasjon om forbruket.
- Foreta en termisk skanning av rør og potter for å avdekke hull i isolasjonen og blokkeringer.
Dokumentering av avkastning
Som nevnt mangler vi bransjestandarder. Hvordan vet vi egentlig hvilke systemer som kan gi størst avkastning når det gjelder energi? Vårt beste materiale akkurat nå, er eksempler som representerer vanlige situasjoner. Her er flere eksempler som gjelder vanlige industrisystemer.
Elektromagnetisk inspeksjon
Anleggstype: stålgjenvinningsfabrikk i Tyskland
Utstyrstype: beltedrevet vifte for prosesskjøling
Iverksatte tiltak: vibrasjonstesting
Problemer oppdaget: Moderat ubalanse samt forskyvninger og slitasje på lagre
Besparelser: Ombalansering var nødvendig. En 350 kW motor kjørte på 80 % av nominell effekt. Målt effekt var ca. 280 kW. Etter ombalansering ble effektforbruket redusert med 3 %. Med en kostnad på 0,11 euro/kWh, ble den årlige besparelsen beregnet til 8094 euro.
Trykkluftinspeksjon
Anleggstype: produksjon
Utstyrstype: trykkluftsystem
Iverksatte tiltak: ultralydinspeksjon av trykkluftsystemet (komplett datalogging av kompressoren anbefalt)
Problemer oppdaget: mengden trykkluft produsert sammenlignet med faktisk behov
Besparelser: Flere innsparingsmuligheter ble funnet, totale årlige besparelser på 50 600 dollar: utkobling av kompressoren i helgene, årlig besparelse på 32 700 dollar; installering av solenoider for å stenge av luften når maskiner slås av, årlig besparelse på 7100 dollar; reparasjon av 36 lekkasjer, årlig besparelse på 4800 dollar; filtre installert i systemet til en engangskostnad på 6000 dollar, årlig besparelse på grunn av filtrene: 6000 dollar.
Inspeksjon av kondenspotter
Anleggstype: produksjon
Utstyrstype: kjeler og dampledninger
Iverksatte tiltak: termisk inspeksjon av dampledning
Problemer oppdaget: seks kondenspotter fungerte ikke riktig, lekkasjer i spoler i pletteringstanker, damplekkasjer i pletteringsledninger, muligheter for kondensgjenvinning
Besparelser: Seks defekte potter ble skiftet ut til en kostnad av 500 dollar per potte. Besparelser oppnådd: 3200 dollar per potte. Damp- og varmetap ble beregnet ved hjelp av kjent kostnad. Totale besparelser: 16 200 dollar.
Neste trinn: Energilogging ved kjelens forsyningstavle før og etter at problemene med lekkasjer og kondens var løst.
Økt produktivitet eller reduserte faste kostnader?
Neste spørsmål er det hyggelig å svare på: Når du har funnet en måte å redusere energiforbruket på, bruker du disse besparelsene til å øke fabrikkens avkastning (samme kWh-forbruk produserer større volumer), eller til andre forretningsstrategier (fortjenestemarginer, prisrealisasjon)?
Redusert energiforbruk er god forretning. Ved å logge effekten i hvert av de store systemene og kartlegge kostnadene mot strømregningene for å vise hvor og når forbruket skjer, kan selskapene ofte realisere besparelser med enkle driftsendringer og justeringer av driftstidene. Selskapene kan forsvare og prioritere utskiftninger ved å identifisere ineffektivt og utdatert utstyr. Ved å redusere det totale energiforbruket kan selskapene redusere driftskostnadene og forbedre konkurranseevnen i markedet.
Gå til denne artikkelen i PDF-format.