Jak kalibracja poprawia optymalizację
Ze względu na wahania cen surowców przemysł stoi przed wyzwaniem dostosowania się do ram czasowych produkcji i oczekiwanej marży. Jednym z niewielu skutecznych sposobów kontrolowania kosztów we wszystkich branżach jest wdrożenie koncepcji lean management i zwiększenie wydajności.
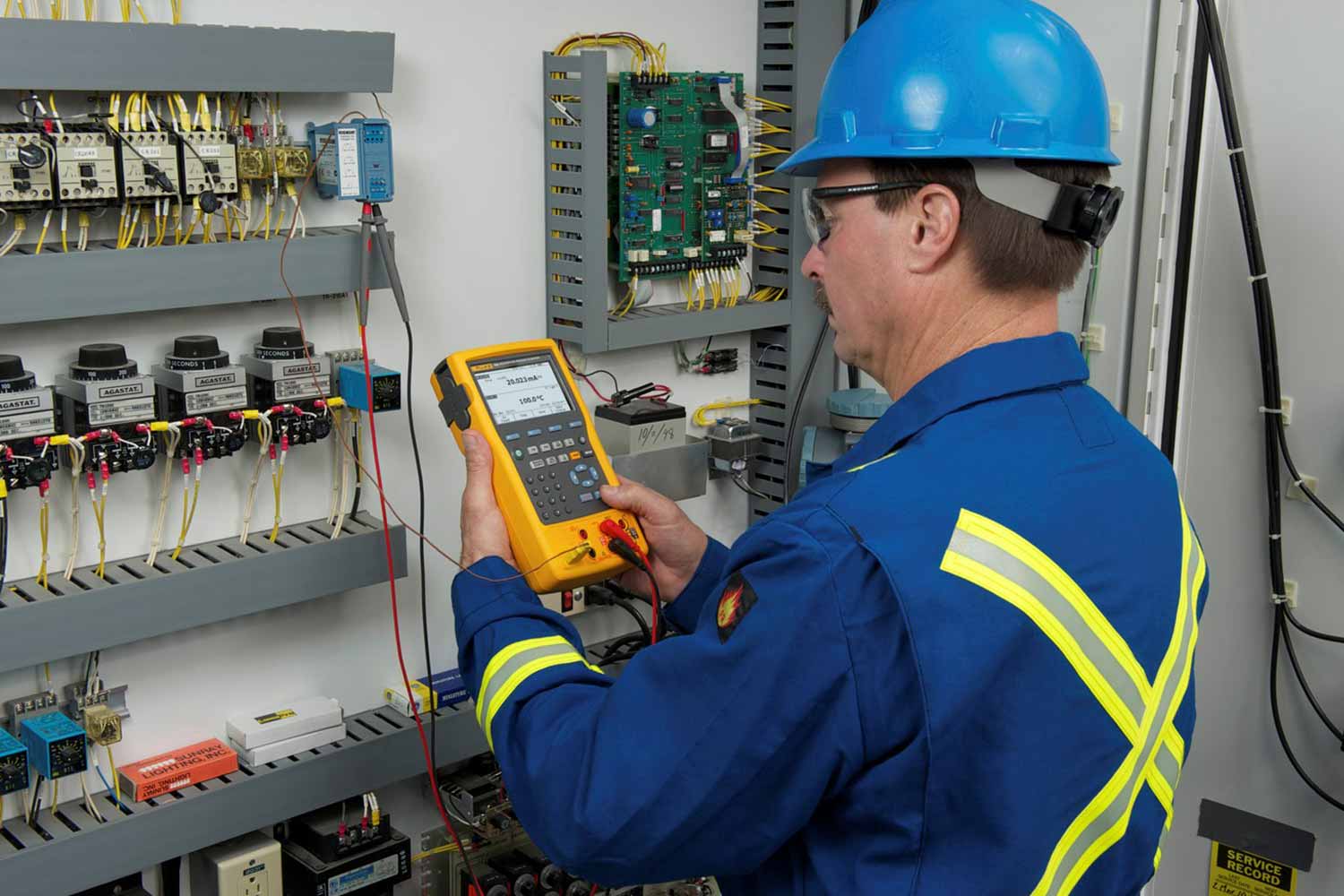
Jednym z najlepszych sposobów kontrolowania kosztów jest identyfikowanie strat w procesie. Oznacza to sporo precyzyjnych regulacji oprzyrządowania, które zapewnią odpowiednie wartości temperatury i ciśnienia przekładające się na wysoką jakość produkcji i efektywność wykorzystania surowców.
Sprzęt do kalibracji poprawia optymalizację i jakość — to samo dotyczy innych branż procesów technologicznych, takich jak przetwórstwo chemiczne, energetyka jądrowa i przemysł farmaceutyczny czy celulozowo-papierniczy. Zakłady zajmujące się produkcją procesową wymagają setek, a nawet tysięcy zaawansowanych urządzeń, które niestrudzenie, dokładnie i niezawodnie wykonują niezliczone operacje o krytycznym znaczeniu dla procesu. Takie urządzenia wymagają jednak regularnego przeprowadzania kontroli, testów, kalibracji i napraw.
Zdobywane przez setki lat doświadczenie w przemyśle potwierdza wartość starannego rejestrowania szczegółowych danych z kontroli, testów, kalibracji i napraw. Nie chodzi tylko o najlepsze praktyki — przedsiębiorstwa i rządy często wymagają bardzo szczegółowego przechowywania danych, aby zapewnić klientom pełną wartość i bezpieczeństwo oraz ochronę ich zdrowia.
Jednak tradycyjne metody testowania, kalibrowania i dokumentowania są bardzo pracochłonne, a ograniczone kadrowo zespoły, przy ciągłym niedoborze doświadczonych operatorów, decydują się czasami na odroczenie regularnej kalibracji. Z najnowszych badań wynika, że mniejsze zespoły mogą wykonywać i dokumentować kalibracje urządzeń przy niższych kosztach ogólnych, jednocześnie podnosząc wydajność i niezawodność.
Kalibracja jest zwykle wykonywana w miejscu, w którym znajduje się urządzenie (to tzw. kalibracja in situ — z łaciny „na miejscu”), lub w warsztacie.
Porada profesjonalistów:
Podczas produkcji oprzyrządowania używanego na obiekcie zarówno element pierwotny, jak i przetwornik (lub siłownik w przypadku zaworu sterującego) kalibruje się fabrycznie, a wraz z urządzeniem dostarcza się dane kalibracji. Jednak użytkownicy często gubią te dane. Wprowadzenie danych do scentralizowanych rejestrów kalibracji podczas wdrażania urządzenia do użytku powinno być częścią standardowej praktyki.
Centralizacja danych kalibracji zapewnia, że wiedza pozostaje w zakładzie nawet w przypadku zmian w zespołach.
Większość oprzyrządowania obiektowego składa się z dwóch części: elementu pierwotnego i przetwornika.
- Elementy pierwotne to rurki przepływu, płytki z kryzami, czujniki ciśnienia, zanurzeniowe czujniki składu chemicznego, takie jak sondy pH, potencjału redoks i przewodności, wszelkiego rodzaju mierniki poziomu, sondy temperatury itp. Takie elementy generują sygnał — zwykle napięcie, prąd lub rezystancję — proporcjonalny do zmiennej wartości parametru, którą mierzą, np. poziomu, przepływu, temperatury, ciśnienia lub składu chemicznego. Elementy pierwotne podłącza się do wejścia przetworników obiektowych.
- Przetworniki obiektowe obejmują przyrządy do pomiaru ciśnienia, temperatury i przepływu. Przetwarzają sygnał generowany przez element pierwotny, najpierw charakteryzując go w formacie liniowym i stosując do niego współczynniki jednostek inżynieryjnych, a następnie przesyłając go w postaci analogowej (zwykle 4–20 mA DC) lub cyfrowej (zazwyczaj przy użyciu magistrali fieldbus).
Urządzenia analogowe
Urządzenia analogowe — często nazywane urządzeniami „pętli prądowej 4–20 mA” — noszą taką nazwę, ponieważ przesyłają sygnał, który jest elektryczną „analogową” reprezentacją zmierzonej wielkości fizycznej (np. temperatury). Wysyłają prąd elektryczny o wartości proporcjonalnej (analogicznej) do mierzonej wielkości fizycznej, przy czym prąd 4 mA odpowiada minimalnej wartości skali, a prąd 20 mA — wartości maksymalnej.
Mimo że wiele aspektów systemu jest obecnie cyfrowych, w produkcji procesowej na całym świecie nadal używa się urządzeń analogowych.

Urządzenia cyfrowe
Urządzenia cyfrowe przekształcają zmierzoną wartość fizyczną na sygnał cyfrowy. W branży procesów technologicznych stosuje się wiele różnych metod kodowania cyfrowego, takich jak Foundation Fieldbus, Profibus i HART.
Powszechnie uważa się, że urządzenia obiektowe magistrali fieldbus (cyfrowe) nie wymagają kalibracji. To nieprawda. Mimo że sygnał magistrali fieldbus (Foundation Fieldbus, Profibus lub Connected HART) dostarcza informacji diagnostycznych, nie przekazuje informacji o dokładności urządzenia ani nie sprawdza, czy urządzenie precyzyjnie podaje wartości procesu.
3 najlepsze przyrządy do kalibracji pozwalające uprościć procesy
- Wielofunkcyjny kalibrator dokumentujący Fluke 754 z funkcjami HART i automatycznymi procedurami kalibracji, spełniający oczywiście rygorystyczne normy bezpieczeństwa
- Precyzyjny kalibrator ciśnienia Fluke 721 z podwójnymi izolowanymi czujnikami ciśnienia do zastosowań podczas transportu substancji niebezpiecznych
- Precyzyjny kalibrator manometrów Fluke 700G o wysokiej jakości i wytrzymałej konstrukcji wysokociśnieniowej, zapewniający szybkie i dokładne wyniki testów
Zawory sterujące
Zawory sterujące są wyposażone w siłowniki, które również wymagają kalibracji w celu skompensowania zużycia i rozszczelnienia zaworu, a także zapobiegania zakleszczeniu lub zatarciu. Aby zagwarantować niezawodne działanie, takie zawory trzeba często poddawać testom pełnego lub częściowego skoku, jeśli nie były regularnie używane.
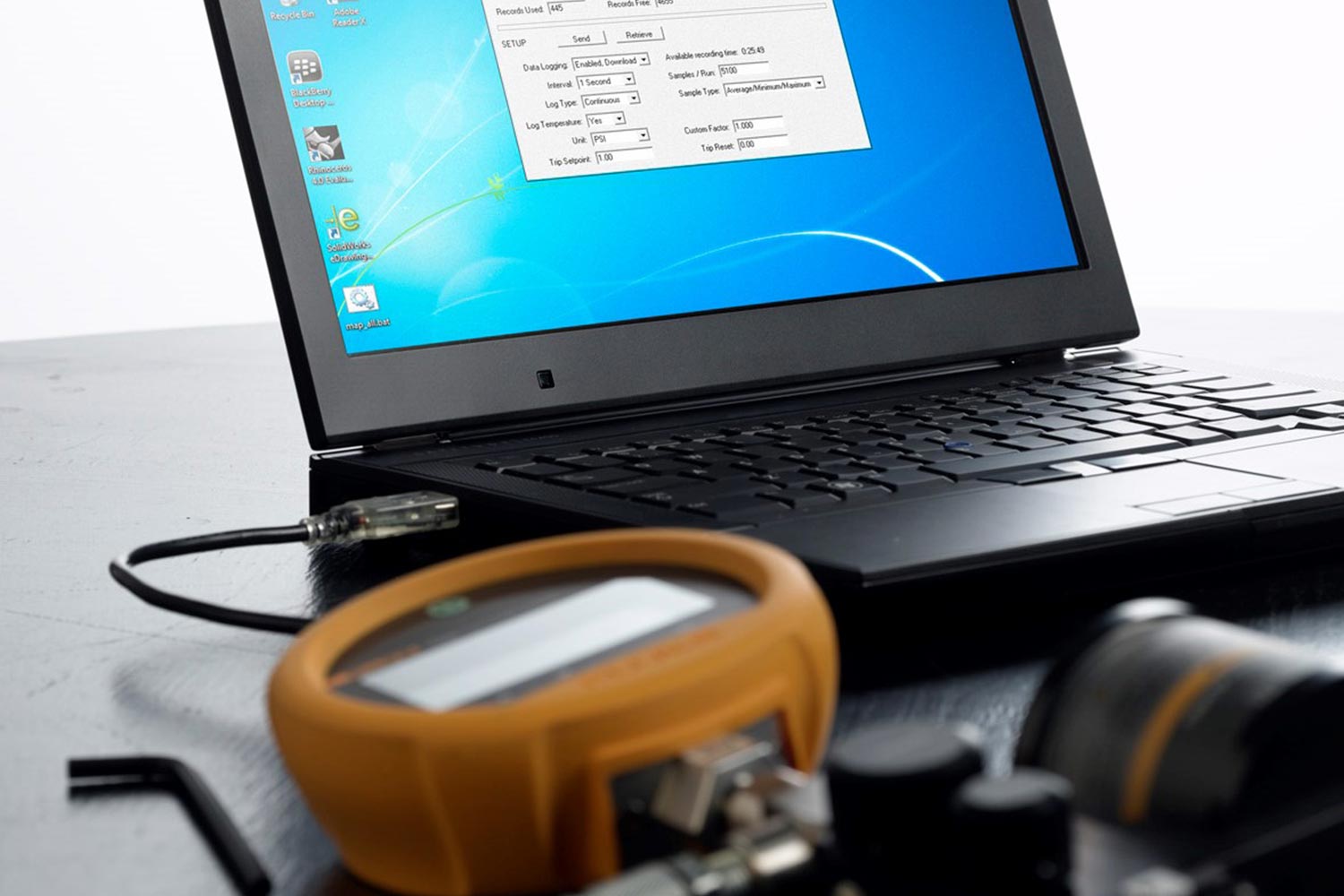
Zezwolenia i dokumentacja
Zadania administracyjne, od uzyskania zezwoleń po dokumentowanie i raportowanie wyników, mogą zwiększać koszty i wydłużać czas realizacji, nawet w przypadku kalibracji in situ. Jak powiedział Ian Verhappen z działu Industrial Automation Networks, były prezes Stowarzyszenia Użytkowników Fieldbus Foundation, w wielu przypadkach prawidłowe przygotowanie wszystkich niezbędnych dokumentów (zezwoleń, odłączeń itp.) często zajmuje więcej czasu niż sama praca.
Wyzwania związane z dokumentowaniem kalibracji
Dokumentowanie kalibracji tradycyjnie oznacza korzystanie z dziennika w celu ręcznego zapisywania daty i godziny, odczytów przed kalibracją, odczytów po kalibracji i innych obserwacji techników. Co zaskakujące, wiele zakładów w dalszym ciągu dokumentuje prace kalibracyjne ręcznie. Jednak używanie do tego celu długopisu i papieru ma wiele wad.
Po pierwsze, powoduje i utrwala błędy. Dane zawarte w dokumentach przygotowywanych ręcznie są często po prostu nieczytelne lub niepełne. Zakłady korzystające z komputerowego systemu zarządzania utrzymaniem ruchu (CMMS) muszą w takich przypadkach uwzględnić dodatkowy czas potrzebny na ręczne wprowadzanie danych, co zwiększa ryzyko powstania błędów.
Zmiany w zespołach
Kolejnym wyzwaniem w kontekście kalibracji są zmiany zachodzące w personelu.
Lata 80. przyniosły cięcia budżetowe i zwolnienia. Liczba pracowników w działach inżynierii, utrzymania ruchu i operacji została znacznie ograniczona, a rozwinęła się nowa filozofia „produkcji przy minimalnych nakładach”, która jest głęboko zakorzeniona w branży także dziś, zwłaszcza w rozwiniętych gospodarkach.
Mniejsze zespoły mają mniej czasu na mentoring i szkolenia w miejscu pracy, dlatego coraz częściej występują problemy z przekazywaniem wiedzy o sprzęcie i systemach w skali przedsiębiorstwa. Gdy starsi operatorzy i inżynierowie przechodzą na emeryturę, „zabierają” ze sobą wiedzę na temat sprzętu i systemów.
„Każdego dnia o godzinie 16.00 wiedza, którą dysponuje zakład, wychodzi poza główną bramę, a czasami już nie powraca” — mówi główny inżynier ds. oprzyrządowania i sterowania w dużej rafinerii z regionu środkowozachodniego w USA.
Tymczasem w wielu placówkach nadal potrzeba dwóch techników do każdej kalibracji in situ — jednego przy przetworniku, a drugiego przy systemie sterowania. Według szacunków Fieldbus Foundation wdrożenie do eksploatacji wymaga dostępności dwóch techników przez co najmniej dwie godziny.
Postaw na wielofunkcyjne kalibratory dokumentujące
Nowa generacja „inteligentniejszych” przyrządów do kalibracji urządzeń obiektowych zwiększa wydajność pracowników dzięki połączeniu wielu przyrządów w jeden i wykonywaniu zadań wykraczających poza podstawowe testy i pomiary, takich jak pomoc w analizie i dokumentowaniu.
Wielofunkcyjne „dokumentujące kalibratory procesów” to mieszczące się w dłoni elektroniczne przyrządy pomiarowe, które łączą wiele etapów kalibracji i liczne funkcje w jednym urządzeniu, symulując i mierząc ciśnienie, temperaturę oraz szereg sygnałów elektrycznych i elektronicznych.
Korzyści:
- Mniej przyrządów wymagających szkolenia techników i transportowania na teren obiektu.
- Podobne procesy kalibracji i dane wyjściowe dla wielu urządzeń zamiast zróżnicowanych procesów gromadzenia różnych zestawów danych z poszczególnych przyrządów i urządzeń.
- Automatyzacja procedur oznacza mniej kroków kalibracji ręcznej.
- Drugi technik nie musi rejestrować stanu urządzenia obiektowego na początku i końcu procedury.
- Krótszy czas kalibracji na urządzenie.
- Konieczność uwzględnienia błędu tylko jednego przyrządu.
Korzystaj z obchodów kalibracyjnych
Największe oszczędności wynikające z używania kalibratora dokumentującego można uzyskać za pomocą wbudowanego w urządzenie narzędzia do zarządzania trasą obchodu. Korzystanie z jednego zestawu zezwoleń i dokumentacji dla całego zestawu kalibracji znacznie obniża koszty.
Zastosuj system zarządzania zasobami, system zarządzania kalibracją lub komputerowy system zarządzania utrzymaniem ruchu (CMMS)
W przeciwieństwie do dokumentacji papierowej, dane z kalibratorów nigdy nie są nieczytelne, enigmatyczne ani niepełne. Dane z kalibratorów dokumentujących można pobierać bezpośrednio do różnych systemów CMMS bez potrzeby ich przepisywania.
Ponieważ dokumentujące kalibratory procesowe automatycznie rejestrują stan początkowy i końcowy każdego urządzenia obiektowego in situ i mogą być obsługiwane przez jednego technika, praktyki oparte na trasach obchodów i użyciu takich kalibratorów pozwalają zaoszczędzić nawet 50% czasu i kosztów w porównaniu do tradycyjnych metod ręcznej kalibracji pojedynczych urządzeń. Ten sam ograniczony kadrowo zespół może przeprowadzić dwa razy więcej kalibracji w danym czasie.
W przypadku tradycyjnego modelu taki ograniczony kadrowo zespół to recepta na błąd. Kalibracje po prostu nie są wykonywane w taki sposób, w jaki powinny. Zamiast ignorować zagrożenie, zbadaj, jak można by zwiększyć efektywność stosowanych praktyk.
Warto wdrożyć kalibrację opartą na trasach obchodów, dokumentację elektroniczną i zarządzanie danymi CMMS. Dzięki temu więcej kalibracji będzie wykonywanych w spójny sposób, wiedza będzie przekazywana poszczególnym członkom zespołu i w obrębie całego przedsiębiorstwa, a wydajność i jakość wzrosną.
Kalibracja wielu przyrządów w ramach jednego obchodu zmniejsza koszt jednej kalibracji w porównaniu z kalibrowaniem poszczególnych przyrządów.
Obniżenie kosztów utrzymania ruchu to nie wszystko — należy pamiętać, że koszty prawne i utrata dochodów wskutek wypadku mogą iść w miliony. Dobre praktyki kalibracji pomagają zmniejszyć ryzyko takiego zdarzenia. Jeśli dojdzie do katastrofy, dobra dokumentacja kalibracyjna może być elementem obrony zakładu w przypadku działań prawnych, a nieodpowiednia dokumentacja może spowodować, że taka obrona będzie znacznie trudniejsza.