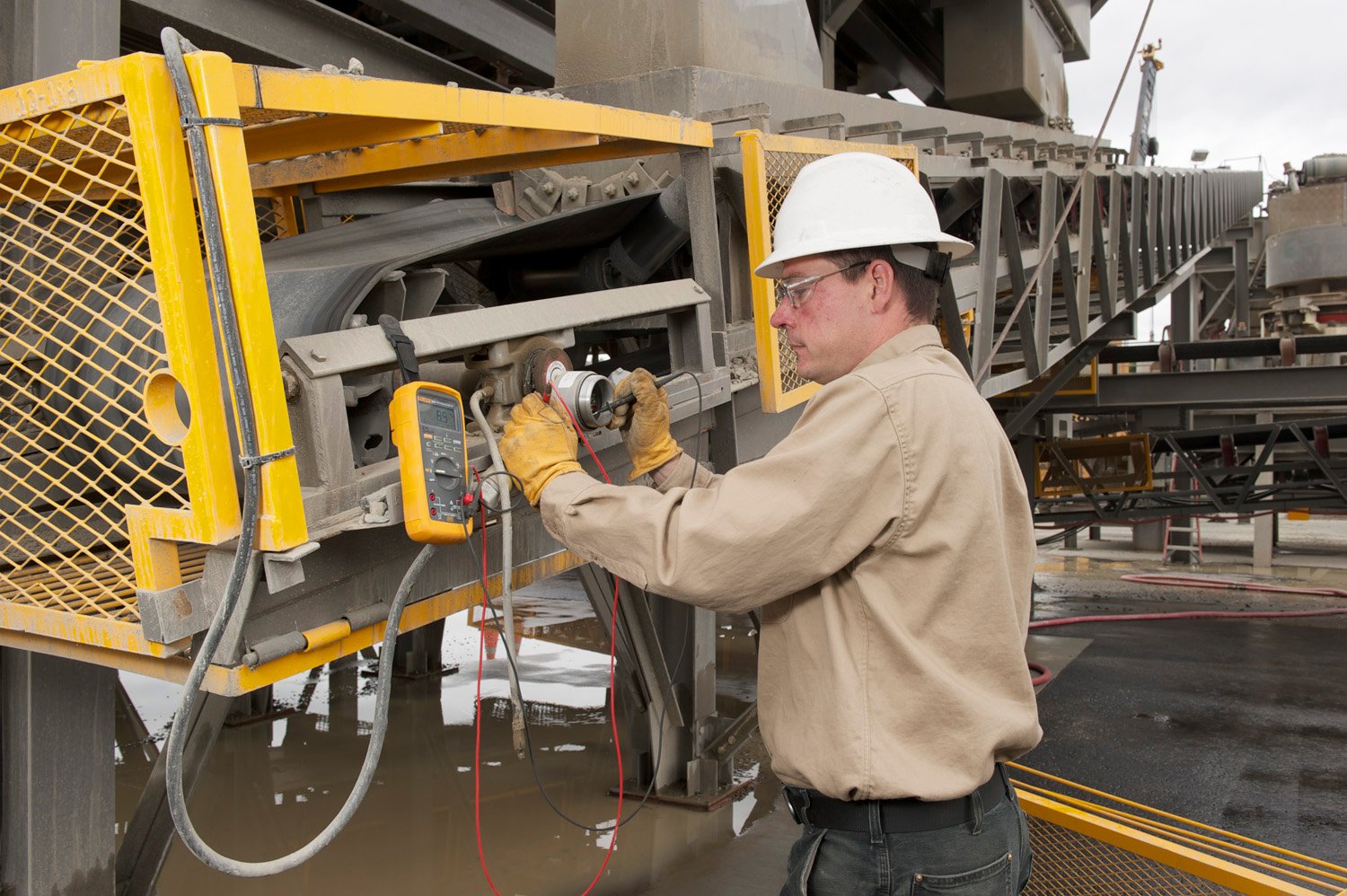
Greg Burdick tests a conveyor speed switch.
Out on the job site, concrete finishers stand ready to shape wet ready-mix into a new stretch of highway. Mixer trucks are lined up at the concrete batch plant, waiting to take on their loads. But hold on—an electrical problem has shut down the plant. It's time to call Keithly Electric.
With dozens of equipment operators, craft people, laborers, drivers, and highway officials all waiting for the mix to move, the pressure to get the product moving again is intense. Everybody's asking the question: How long is it going to take to get this fixed?
"They'll literally ask you that question the moment you get out of your truck," said Keithly electrician and programmer Greg Burdick. When the pressure is on and time is money, Keithly knows that having experienced people with a broad range of skills, who can get a plant up and running again fast, is the key to success.
Ever since founder Bob Keithly started this business in 1967, Keithly Electric has focused on strong relationships with both customers and employees. Today the company's thirty-five employees work all over the greater Seattle area—on ships, cranes, and barges, in buildings and in homes, in food processing and aerospace plants—building and maintaining everything from everyday conduit-and-wires jobs to complex programmable logic control (PLC) systems. As it has since the start, the company keeps many local concrete, asphalt, and construction aggregate operations up and running.
True grit
Materials plants overflow with the kinds of hazards that can bring equipment to a halt: dust and grit coat everything, and the water used to wash the gravel splatters down onto the structures and the ground. These plants run fast and lean— there's no "second line" to fire up when electrical problems stop the process—so Burdick arrives on the job knowing it's critical for plant operators to get their operations back online. It's a tough place to work, but Greg Burdick is a very tough guy.
He has faced and overcome challenges far more serious than even this difficult work environment. An infection by flesh-eating bacteria (necrotizing fasciitis) several years ago nearly killed him. He lost his left leg below the knee, and part of his right foot. But he kept his sense of humor.
"That's the personality trait that's not really part of the job," he laughed. He returned to work after an evaluation determined that he could perform "every horrible thing an electrician might ever have to do."
Burdick does more than just fix what's broken. Burdick and the Keithly team also work side by side with plant operators to re-engineer and automate plant systems to improve efficiency and reliability. The PLC systems that Keithly designs and builds connect and control variable frequency drives (VFDs), sensors, alarms, and other elements. Using touch screen control panels, a single operator can run an entire plant.
One such customer is a sprawling, 500-acre facility nearby, a major regional supplier of crushed and washed aggregates and asphalt.
Beyond the facility's asphalt batch plant, and past the main office and scales, stands the materials plant, a complex of crushers, interlocking conveyors, sorting screens and washers that resembles a funky roller coaster.
In the distance are mounds of boulders and riprap and the pits where sand, gravel, and stone, pushed here by Ice Age glaciers, are loaded into 100-ton bottom-dump haul trucks. Those trucks then carry their loads to the grizzly screens, where a series of strong parallel bars separates large rocks and other debris from material of smaller size. The sand, gravel, and small rock falls through to a conveyor to begin its trip through cone crushers, more conveyors, sorting screens, and washers. The big stuff—boulders up to four or more feet across—drops into a pit to await its trip to the jaw crusher.
A visit to the plant shows there's more than brute strength involved in breaking rocks. For instance, to prevent boulders from building up and clogging them, the grizzlies must be emptied every few truckloads. In the past, that meant the haul truck drivers had to push a button to register each load.
Keithly had a better idea. Burdick mounted inductive loops on the grizzly rails to sense when the haul trucks arrive and leave. The loops were originally designed to be placed under pavement to detect cars waiting for stop lights. The loop signals now tell the control system how many loads each grizzly has received and confirm that the haul trucks are gone and the grizzlies can be emptied. A PLC control panel mounted near the grizzlies oversees the process.
Finding a better way
The grizzly sensor is part of a redesigned control system that Keithly recently completed for the plant. A touch screen now gives the operator a graphical layout of the entire plant, with its multiple hoppers, conveyors, and crushers. Readouts show the status of each motor, sorter, and pump, and the load level in every material silo. The result: the automated system senses problems such as material overflows, and lets the operator know before they cause real trouble. Production goes up and operating costs go down.
When trouble calls come in and the pressure builds, Burdick keeps his focus on process. "It's just really a matter of being as thorough and methodical as you can—it's just troubleshooting," he said. "You don't have to understand the system, but you have to know enough about the components to hit a starting point. A lot of times you have to put the pieces together as you go."
The process can include just about any electrical test there is, from straightforward voltage, current, and ground checks to troubleshooting the increasingly common VFDs. "I do a lot of drive testing, and testing the front end and back end of drives—the power unit—is done primarily with a diode check," Burdick said. "The diode check is a function on the multimeter— it measures the voltage it takes to get a diode to fire."
Burdick also checks the VFD's synthetic frequency, using the function found on some Fluke digital multimeters. "The new meter I've got, the Fluke 28 II, has a low pass filter for checking variable speed drives. I've used it to check that the readout on the drive is correct," Burdick said.
In fact the Fluke 28 II multimeter, and it’s newer option, the Fluke 87V MAX True-rms Digital Multimeter, feature an IP67 rating for waterproof and dustproof protection. The 87V MAX also boasts a four-meter drop rating, showing it was designed for exactly the harsh conditions where Burdick works.
"The droppable issue usually comes along with ladders," Burdick laughed. "Any time you're working on something up high you run the risk of shaking the ladder or doing something to knock it off. Probably the best thing I use with my meters is that magnet kit (Fluke ToolPak™ Magnetic Meter Hanging Kit)."
Then there's the water.
The trouble with moisture
"My other good meter, I almost ruined that once," Burdick said. "I walked from a control panel to a control house through the rain. By the time I got to the control house to check the other end of the circuit I had filled the dial with water because I was holding the meter facing up."
And with the Fluke 28 II? (upgraded to the Fluke 87V MAX True-rms Digital Multimeter) "I don't even think about it anymore," he said. "I saw the 28 II at the 2009 Rockwell Automation Fair in California, sitting in a tank of water. I said okay, that's for me."
For work on control panels, Burdick uses both his Fluke 28 II and Fluke 189 multimeters (these tools have been replaced by the Fluke 87V MAX True-rms Digital Multimeter and the Fluke 289 True-RMS Data Logging Multimeter). "For low voltage stuff, generally DC signals, and if I'm doing current measurements, I trust the 189 more," he said. "I use the Fluke 771 milliamp clamp meter quite a bit when I'm doing analog signals. You don't have to break into the circuit to take a reading. I haven't found any significant difference between that and measurements when you do get into the circuit and run it through your meter."
When testing motor control center panels, Burdick relies on an older Fluke 1520 insulation resistance tester (replaced by the Fluke 1507 Insulation Resistance Tester). "Most of our customers' loads are motor loads," he said. "I use that all the time to test whether a motor's blown or a cable is shorted."
Equipment grounding is another key consideration. Materials plants follow the rules of the US Mine Safety and Health Administration (MSHA), which include rigorous requirements for grounding. "There is a grounding assurance program," Burdick said. "All of the plants have to be tested every year—every motor has to be tested for ground continuity. If I end up doing one of those jobs I'll use that Fluke 1520 on the low ohm reading.”
"If the motor shorts out or the wiring comes undone in the junction box, there must be a low-resistance path to ground in order to trip the breaker. I've seen it before where the ground is not continuous and there is no effective path back to the ground rods of the system. In a fault condition it will actually energize the structure. With 480-volt motors, when you grab the railing and you're standing in a puddle of water, that can be very uncomfortable."
Going the distance
Sometimes customer service requires literally going the distance. One day a concrete batch plant reported that their big drum mixer—the unit that tilts to fill the mixer trucks—was acting up. The tilting mechanism, which normally ran at variable speed to cushion the shock as the heavy vessel moved, was running at only one speed. The plant couldn't shut down, so testing had to be done with the system running.
Using his Fluke 189 multimeter (now replaced with the Fluke 289 True-RMS Data Logging Multimeter), Burdick narrowed his focus to the control board.
"The control board was no longer sending out a DC signal. And the only way we caught that was that when you hooked your meter up to the output terminal, the analog bar graph on the bottom of the meter was dancing," he said.
"A DC signal, that's solid. But there was something wrong with how the control board was firing the DC signal. It was jumping all over the place, between two and eight volts. The valve ended up averaging the signal. The board was just broke."
It took a special connection to swap out the faulty control board without shutting the plant down for days. Dan Keithly knew of another batch plant, not in service, equipped with the same controls. He contacted the owner and arranged to borrow the board. It took two and a half hours on the road to retrieve the substitute control board.
But it was time well spent. The customer kept running. And for Keithly Electric, that's the bottom line.