Von Jack Smith
Wie hohe Kosten entstehen Ihnen durch unerwartete Stillstandzeiten Ihrer Anlage pro Minute, Stunde oder Tag? Wie viele dieser unerwarteten Stillstandzeiten können Sie in Ihrem Betrieb verhindern? Wenn Sie die richtigen Instandhaltungsmaßnahmen durchführen bzw. wohlüberlegte Investitionen tätigen, dann können Sie diese unerwarteten Ereignisse begrenzen.
Das Federal Energy Management Program (FEMP) (www1.eere.energy.gov/femp), als Teil des US Dept. of Energy (DOE) (www.energy.gov) veröffentlichte im August 2010 die jüngste Version seines „Operations & Maintenance Best Practices, a Guide to Achieving Operational Efficiency“ (Bewährte Praktiken bei Betrieb & Instandhaltung, Leitfaden zur Steigerung operativer Effizienz). Dieser unter Führung der FEMP entwickelte 320-seitige Leitfaden wurde im Hinblick auf hilfreiche Informationen über Betrieb, Instandhaltung, Management, Energieeffizienz und Kostenreduzierung entwickelt.
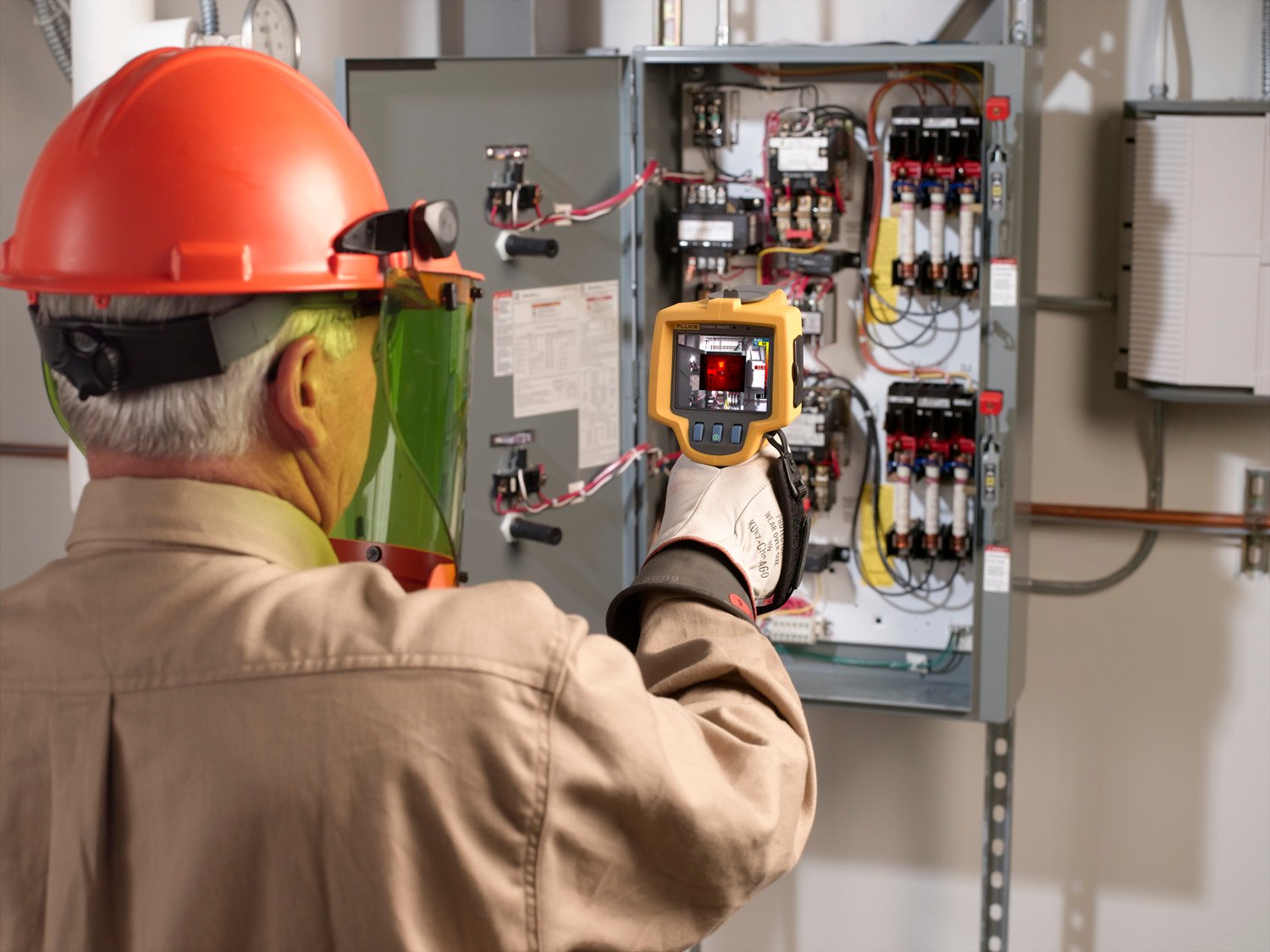
Einer der interessantesten Aspekte dieser Publikation liegt in der Betonung der Wichtigkeit von vorausschauender Instandhaltung. In Kapitel 5 werden zwar Vergleiche und Beispiele hinsichtlich verschiedener Arten von Instandhaltungsprogrammen definiert und erklärt, der Leitfaden widmet jedoch ein gesamtes Kapitel (Kapitel 6) den Programmen zur vorausschauenden Instandhaltung. Drei der in diesem Leitfaden enthaltenen Programme zur vorausschauenden Instandhaltung umfassen Thermografie, Schwingungsanalyse und die Trenddarstellung der Betriebseigenschaften. Ich komme hierauf später zurück.
Im Leitfaden werden reaktive, vorbeugende (PM), vorausschauende (PdM) und zuverlässigkeitsorientierte Instandhaltung (RCM) als Instandhaltungsprogrammtypen aufgeführt und die Unterschiede zwischen ihnen beschrieben:
- Reaktive Instandhaltung – hier laufen Geräte bis ein Ausfall auftritt
- PM – hier führt das Personal Instandhaltungsmaßnahmen auf der Grundlage von zeitbasierten oder Hauptlaufzeitintervallen durch
- PdM – hier wird der Schwerpunkt bei der Instandhaltung auf den tatsächlichen Zustand bzw. den Gesamtzustand der Maschine oder des Systems gelegt
- RCM – Dieser Typ unterscheidet sich kaum von der Methodik des PdM, die Geräte werden jedoch nach Priorität und Kontext klassifiziert.
Ein anderer interessanter Aspekt, der aus dem Leitfaden der FEMP hervorgeht, ist die Tatsache, dass „mehr als 55 %der Instandhaltungsressourcen und -aktivitäten bei einem durchschnittlichen Betrieb immer noch reaktiven Charakter haben“. Obwohl die Publikation dieses Muster aus einer 10 Jahre alten Untersuchung herleitet, ist es immer noch repräsentativ, wenn die Ergebnisse mit denen einer jüngeren Untersuchung, wie der im Magazin „The Changing World of the Plant Engineer“ von Plant Engineering im April 2010 veröffentlichten Aussage verglichen werden, laut der „mehr als 60 % der Betriebe in den USA und 70 % der internationalen Betriebe über keine Instandhaltungsstrategie verfügen“.
Zurück zum Programm zur vorausschauenden Instandhaltung
Der FEMP-Leitfaden erläutert die Vor- und Nachteile von PdM und vergleicht diese mit anderen Instandhaltungsmethoden. Obwohl ein gut funktionierendes Programm zur vorausschauenden Instandhaltung schätzungsweise Einsparungen von ca. 8 % bis 12 % gegenüber einem Programm bewirkt, das ausschließlich auf vorbeugender Instandhaltung beruht, berücksichtigt der Leitfaden die nicht unerheblichen Investitionen, die zu Beginn eines Programms zur vorausschauenden Instandhaltung benötigt werden. Zu diesen Investitionen gehören Geräte zur Diagnose und Überwachung, Personalschulungen vor Ort zum Umgang mit dieser Ausrüstung und die Unterrichtung über Methoden und Konzepte bei einem Programm zur vorausschauenden Instandhaltung. Natürlich bringt ein Programm zur vorausschauenden Instandhaltung, je nach Prozessablauf, hohe Anfangskosten mit sich, aber potentielle Stillstandzeiten können zu erheblich höheren Kosten beim Anlagenbetrieb führen.
Die meisten der Informationen in diesem Leitfaden sind zugegebenermaßen nicht neu, jedoch werden existierende bewährte Strategien für ein Programm zur vorausschauenden Instandhaltung untermauert. Dies ist wichtig, da viele Betriebe den Bereich der Instandhaltung immer noch reaktiv „verwalten“. Wir können also davon ausgehen, dass gängige Methoden helfen können, Situationen vorherzusehen oder zu verhindern, die wiederholte Stillstandszeiten nach sich ziehen.
Beispiel: die Verwendung von (IR) Thermografie zur Inspektion von elektrischen Anlagen ist eine weitverbreitete Praxis und gut dokumentiert. Elektrische Energieerzeugung, Energieübertragung und Energieverteilung sowie Endverbraucher können von Thermografieprüfungen profitieren. Thermografie kann viele drohende Ausfälle bei den meisten elektrischen Systemen wie Generatoren, Motoren und Transformatoren, Schaltanlagen, Antriebssteuerungen, Kabelkanälen und Beleuchtungsunterverteilungen erkennen.
Dies gilt aber nicht nur für die Elektrik. Thermografie wird auch zu Erkennung und Diagnose von Problemen bei mechanischer Ausrüstung verwendet. Zusätzlich zur Fähigkeit, Probleme im Zusammenhang mit rotierenden Anlagenteilen zu erkennen, wie Lagerdefekte, Wellenausrichtung, Symmetrie und lockerer Sitz, kann Thermografie auch zur Prüfung von Kesselrohren und Materialien zur Wärmedämmung, Kondensatabscheidern, Ventilen und Leitungen verwendet werden, sowie für Flüssigkeitsstände und Verstopfungen in Rohrleitungen, Strömungsbilder bei Abwasser und Luftaustritt und sogar bei der Prüfung der Unversehrtheit von Dachmembranen an Gebäuden.
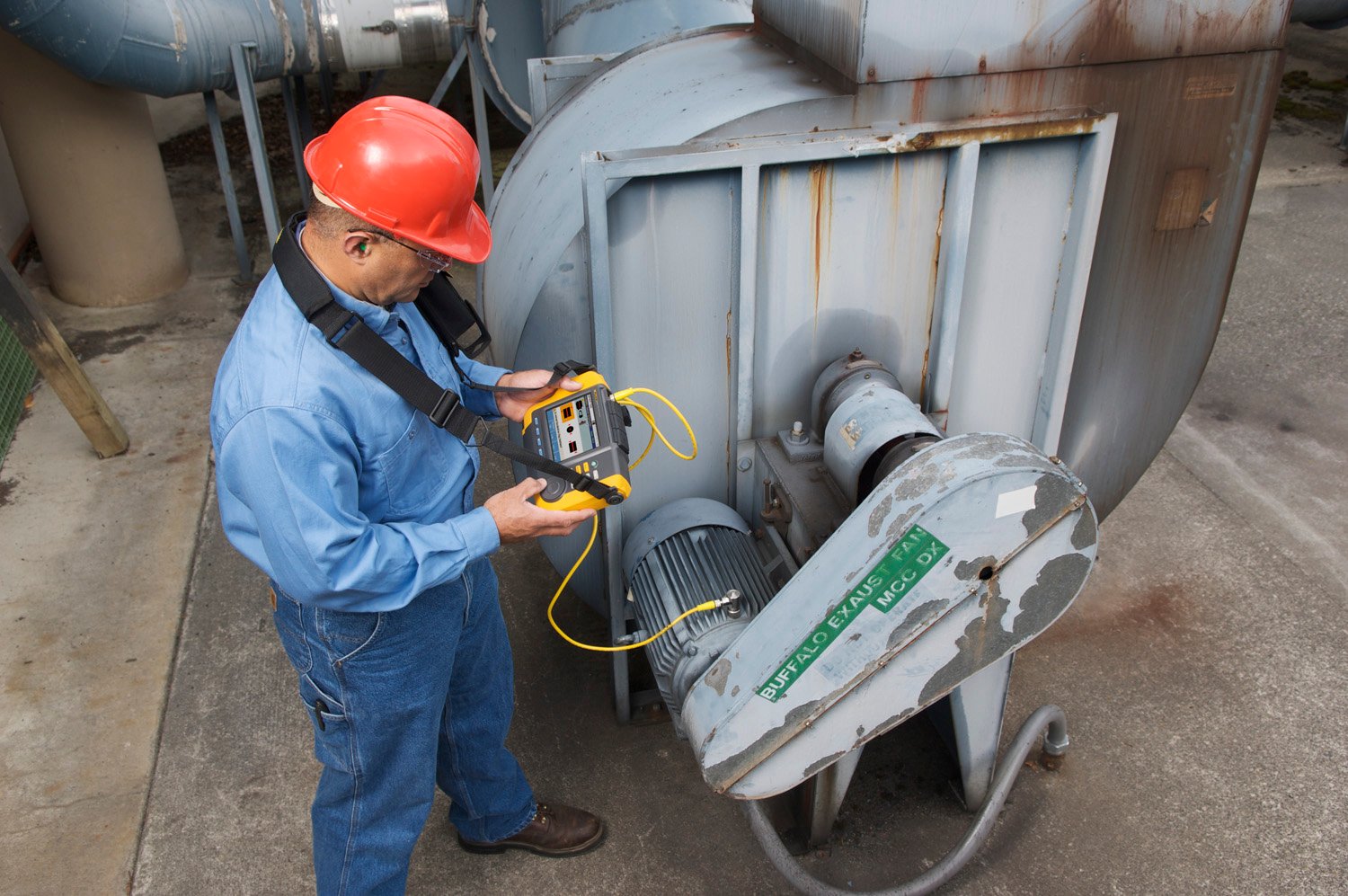
Instrumente zur Schwingungserkennung und Signatur-Analysesoftware werden schon seit langem zur Suche von untypischen Anlagenbedingungen verwendet. Mit diesen Technologien können latent vorhandene Probleme wie u. a. mechanische Unsymmetrie, Exzenterrotoren, Fehlausrichtungen, mechanische Schwingungsprobleme, Gleitlagerprobleme, strömungsinduzierte Schwingungen, Getriebe- und Riemenantriebsprobleme erkannt werden.
In der Vergangenheit waren Messgeräte für die Schwingungsanalyse unerschwinglich und kompliziert. Betriebe mit dieser Art von Programmen zur vorausschauenden Instandhaltung vergaben Schwingungsprüfungen und -analyse in der Regel an Drittanbieter. Heutzutage sind, ähnlich wie bei der IR-Thermografie, Messgeräte für Schwingungsprüfungen jedoch erhältlich, erschwinglich und anwendungsfreundlicher als ältere Technologien.
Die Trenddarstellung der Betriebseigenschaften komplementiert die Programme zur vorausschauenden Instandhaltung durch die Dokumentation von Betriebsparametern der Anlagenausrüstung und -prozesse. Hierdurch kann das Anlagenpersonal Werte für Ausgangsdaten festlegen, Trenddarstellungen erfassen und erkennen, wenn Prozess- und Systemparameter sich außerhalb ihrer Optimalbereiche befinden. Diese Daten können dann zur Zustandsbestimmung der Anlagenausrüstung und -prozesse verwendet werden.
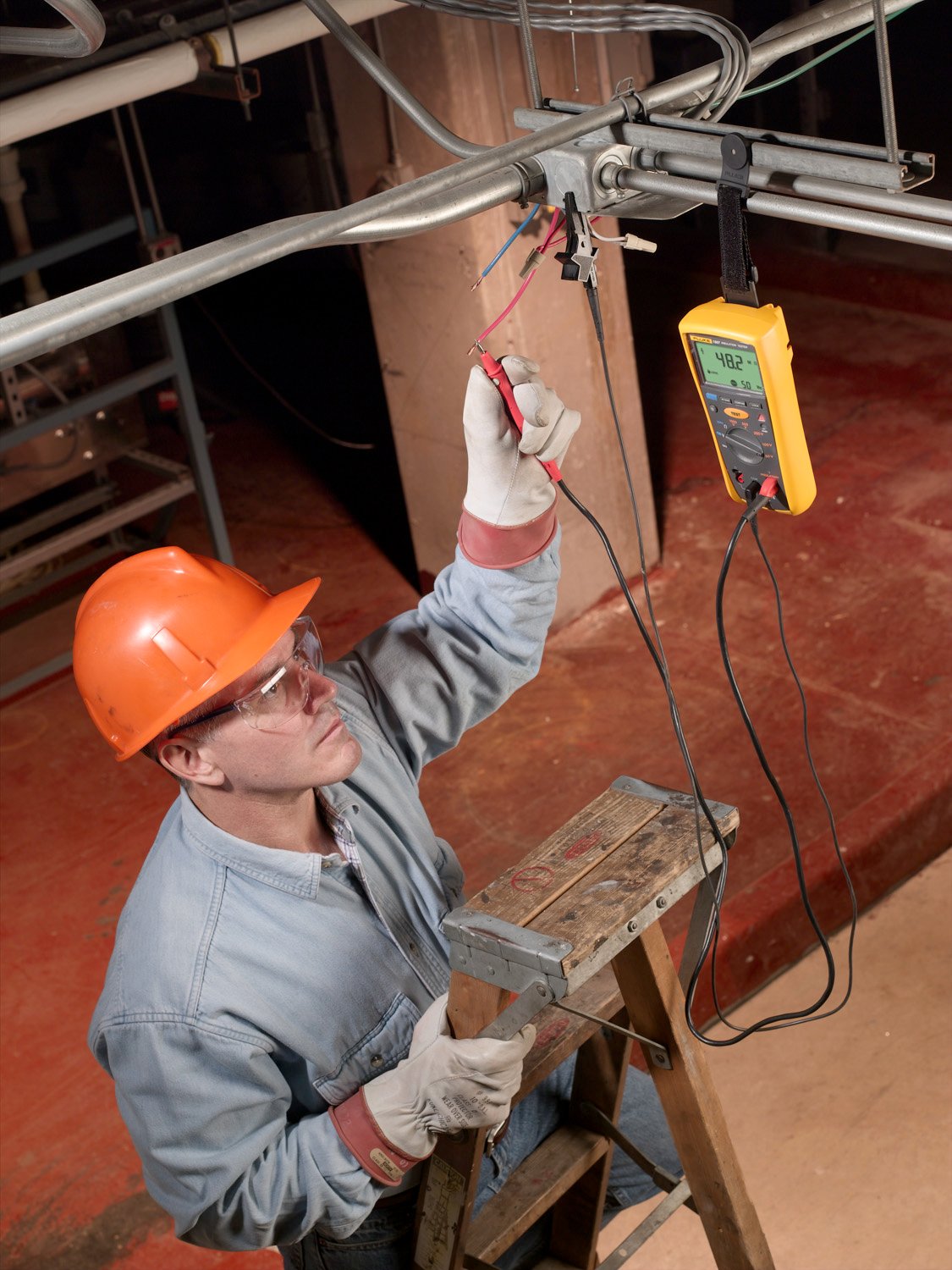
In vielen Betrieben existieren bereits Messinstrumente, die zur Trenddarstellung der Betriebseigenschaften verwendet werden können. Betriebe können gegebenenfalls zusätzliche Sensoren installieren. Bedienungsfreundliche und relativ günstige Datenlogger können die Anforderungen für die Trenddarstellung der Betriebseigenschaften bei Programmen zur vorausschauenden Instandhaltung vervollständigen.
Vergessen wir nicht Netz- und Stromversorgungsanalysatoren, Netzqualitätslogger, Leistungsrecorder, Logging-Multimeter und Isolationsmessgeräte. Diese Liste ist nicht vollständig. Die Messgeräte sind verfügbar, erschwinglich und die Geräte sind bedienungsfreundlich. Die effektivste Verwendung dieser und anderer Qualitäts-Prüfgeräte hängt jedoch davon ab, wie sie angewendet werden, um Ausfälle vorherzusehen und zu verhindern – und nicht nur darauf zu reagieren.
Eine Kopie von Operations & Maintenance Best Practices, a Guide to Achieving Operational Efficiency (.pdf)
Wenn Sie Kommentare zu dieser oder anderer Kolumnen von „Solid Ground“ oder Themenvorschläge haben, dann schicken Sie mir eine E-Mail unter jacksmith.writes@gmail.com.
Bis zum nächsten Mal und bleiben Sie stets auf „Solid Ground.“