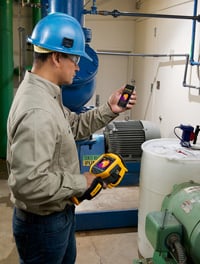
In diesem Artikel geht es nicht darum, wie Sie sich mit Nachdruck dafür einsetzen können, bestimmte Faktoren wie Personal, Zeit und finanzielle Ressourcen zur vorausschauenden Instandhaltung zu koordinieren. Dieser Artikel handelt vom Erreichen der optimalen Anlagenbetriebszeit mit den verfügbaren Ressourcen für Instandhaltung und Nachhaltigkeit.
Unter idealen Bedingungen existiert in einem Industriebetrieb ein spezifisches Programm zur vorausschauenden Instandhaltung bzw. ein Instandhaltungsteam mit dessen Hilfe die wichtigste (teuerste) Betriebsausrüstung identifiziert wird; es werden automatische Systeme bzw. ein computergestütztes Instandhaltungsmanagementsystem (CMMS) zur Geräteüberwachung und zur Datenspeicherung und -analyse verwendet; es wird außerdem genau der richtige Zeitpunkt ermittelt, wann Geräte instandgehalten werden müssen, damit sie sich stets im Optimalzustand befinden bzw. damit Schäden oder Stillstandzeiten vermieden werden; außerdem wird sichergestellt, dass genügend Personal, Zeit und finanzielle Mittel zur Verfügung stehen.
Auf der anderen Seite steht der Rest von uns, mit einem kleinen Instandhaltungsteam in einem kleinen oder mittelgroßen Industriebetrieb und einem breit gefächerten Aufgabenfeld aber ungenügenden Ressourcen für den Einsatz eines SCADA (Supervisory Control and Data Acquisition)-Systems oder zu wenig Personal zur vorbeugenden Instandhaltung. Wir reagieren auf Störungen so gut wir können, wir sammeln sogar, je nach Aufgabenbereich, manuell Daten, um ggf. Probleme lösen zu können.
Das Team kennt seine Ausrüstung, es führt geplante Instandhaltungsarbeiten durch, ist sehr flexibel bei der Fehlersuche und untersteht einem kompetenten Teamleiter. Ein Nachteil ist jedoch, dass das Wissen über den Umgang mit den jeweiligen Geräten und die Qualifikation zwar bei jedem einzelnen Teammitglied vorhanden sind, diese aber mit anderen Kollegen nicht geteilt werden.
Das kann der Rest von uns tun
Technologie hat einen Punkt erreicht, an dem alle Instandhaltungstechniker die gleichen Techniken und Messinstrumente verwenden können, um Probleme zu beheben und zu kontrollieren, zu protokollieren und zu teilen – die Grundlagen der proaktiven Instandhaltung.
Ein anderes Grundprinzip besagt, dass bestimmte Messergebnisse als Warnhinweis dafür dienen können, dass sich die Ausrüstung nicht in optimalem Zustand befindet. Wenn diese Messungen regelmäßig durchgeführt und mit den vorangegangenen Werten verglichen werden, können Techniker Änderungen feststellen, bevor diese zum Problem werden.
Wenn wir nun die Punkte der Liste eines Programms zur vorausschauenden Instandhaltung von „unbedingt notwendig“ auf „für den Rest von uns“ verringern, so können wir zusammenfassen:
- Machen Sie sich mit den wichtigsten Geräten in Ihrem Aufgabenbereich vertraut sowie mit den Schlüssel-Messverfahren/Prüfpunkten, über die Sie den Zustand der Geräte abschätzen können.
- Machen Sie es sich zur Gewohnheit, diese Schlüsselinformationen zu überprüfen und speichern Sie relevante Daten an einem Ort, auf den all Ihre Kollegen zugreifen können, wann immer Sie an dieser Ausrüstung arbeiten, und kategorisieren Sie diese entsprechend Ausrüstungstyp und Datum.
- Prüfen Sie diesen gemeinsamen Speicherort, bevor Sie mit der Fehlersuche beginnen. Hierdurch könnten Sie Zeit einsparen.
Beim nächsten Schritt geht es um Organisation. Der Teamleiter kann die Kommunikation durch drei Dinge fördern:
- Organisieren Sie gemeinsame Mittagessen für alle Teammitglieder und diskutieren Sie Schlüsselbereiche und Zielsetzungen, damit jeder weiß, worauf er zu achten hat, und um das Gruppengefühl zu stärken.
- Veranstalten Sie regelmäßig Workshops über die Verwendung von einfachen Cloud-basierten Tabellenkalkulationen. Hierdurch können alle, die Probleme beim Umgang mit dieser Technologie haben, ohne Hemmungen Lernerfahrungen sammeln.
- Teilen Sie die Datenaufzeichnungen vierteljährlich mit dem Team und erklären Sie auch, wie aussagekräftig die Messwerte sind. Diese konkretisierte Problemanalyse und -behandlung ist bei den Geräten vor Ort aussagekräftiger als bei abstrakten Beispielen. Sie erreichen viel, wenn sich Teammitglieder mit ihrer Arbeit identifizieren können.
- Überprüfen Sie die geteilten Daten in größeren Abständen und suchen Sie Veränderungen, die auf ein Problem hindeuten könnten (wenn zum Beispiel Messwerte anfangen, um 5 % oder 10 % vom Normalwert abzuweichen, ist dies ein Grund, Nachforschungen anzustellen).
- Das Management ist für die Speicherung, Prüfung und die Datenanalyse zuständig.
- Die Teammitglieder sollten imstande sein, Protokolle vor Ort überprüfen zu können und zwar nicht nur hinsichtlich der Dateneingabe; sie müssen auch die Möglichkeit haben, den Datenverlauf zu untersuchen, wann immer sie sich in einer Situation zur Fehlersuche befinden.
- Motivieren Sie das Team zu Folgendem:
- Die Mitglieder sollten melden, wenn Ihnen etwas Ungewöhnliches auffällt, das einer Schlüsselkategorie zugeordnet werden könnte.
- Die Mitglieder sollten versuchen, alternative Verwendungsmöglichkeiten für das Cloud-Protokoll und den Prozess der Datenteilung zu finden, damit die Teamkommunikation verbessert wird.
Es könnten Probleme auftreten, zum Beispiel wenn Teammitglieder vergessen, Messwerte aufzuzeichnen. Ein anderes Problem könnte auftreten, wenn Messwerte nicht aus dem Messgerät übertragen werden – wenn Daten also nicht mit den anderen Teammitgliedern geteilt werden.
In diesem Artikel geht es nicht darum, wie Sie sich mit Nachdruck dafür einsetzen können, bestimmte Faktoren wie Personal, Zeit und finanzielle Ressourcen zur vorausschauenden Instandhaltung zu koordinieren. Dieser Artikel handelt vom Erreichen der optimalen Anlagenbetriebszeit mit den verfügbaren Ressourcen für Instandhaltung und Nachhaltigkeit.
Die Lösung besteht darin, dass Smartphones oder Tablets verwendet werden; die Teammitglieder haben bereits Erfahrung mit diesen Geräten oder das Management versucht, diese besser in Arbeitsabläufe zu integrieren – tatsächlich sind Arbeitsanweisungen die beliebtesten Anwendungen. Und so funktioniert das:
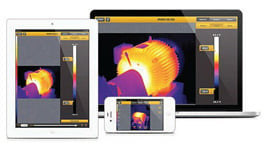
- Umwandlung und Übertragung von handschriftlichen Notizen auf ein intelligentes Gerät und eine Cloud-basierte Lösung wie Fluke Connect®. In der Regel sind die Teammitglieder so gut mit ihren eigenen Smartphones vertraut, dass ihnen die Dateneingabe über diese Geräte wesentlich leichter fällt. Das Verfahren ist zwar immer noch ein zweistufiger Prozess (1. Messungen durchführen 2. Daten in die Tabellenkalkulation in der Cloud eintragen), aber es ist immer noch besser als der alte dreistufige Prozess, bei dem handschriftliche Notizen und Daten im Büro in die Tabellenkalkulation eingegeben werden, die dann außerdem noch als Checkliste fungiert.
- Die Verwendung mobiler Apps, die mittlerweile für zahlreiche Messgeräte zur Verfügung stehen, damit ein weitgehend automatisierter Prozess zur Datenübertragung von Geräten vor Ort an ein Protokoll und von einer Einzelperson an das Team stattfinden kann.
Ausgangswerte und Schlüsselinformationen bei Motorantriebssystemen
Proaktive Instandhaltungsmessungen unterscheiden sich kaum von den Prüfungen zur Fehlersuche. Da Sie nach Anzeichen für potenzielle Ausfälle suchen, führen Sie Messungen im Zusammenhang mit Ausfallmustern durch und zeichnen diese auf.
- Legen Sie Werte für Ausgangsdaten fest, damit Sie schnell abschätzen können, wie „gute“ Werte aussehen und damit der Teamleiter über Vergleichswerte für spätere Messwerte verfügt.
Gerät oder Anlage Wichtige Indikatoren Auszuführende und zu protokollierende Messungen Schaltschränke / Schalttafeln Intermittierendes Auslösen, überhitzte Leistungsschalter Spannungsunsymmetrien größer als 2 %, Stromunsymmetrien größer als 10 %, lockere Anschlüsse, Temperaturänderungen, Lastanstieg Überwachung und Steuerung Prozessabweichungen, Unregelmäßigkeiten bei den Betriebseigenschaften des Systems Spannungsunsymmetrien, Stromunsymmetrie, Einschaltstrom, Anschlusswiderstand Motoren / Lasten Überhitzung, intermittierendes Auslösen Einschaltstrom, Isolationswiderstand gegen Erde, Temperatur, Überlastung, Spannungssymmetrie, Stromausgleich, Widerstand, Verbindung des Anlaufkondensators des Motors, mechanische Fehlausrichtung von Wellen, Unsymmetrie, Lockerung mechanischer Komponenten, Zustand der Lager Proaktive Instandhaltungsmessungen unterscheiden sich kaum von den Prüfungen zur Fehlersuche. Achten Sie auf Grunddaten im Hinblick auf Ausfallmuster. Hinweis: Diese Empfehlungen stellen keinen umfassenden Maßnahmenkatalog für die Vorgehensweise bei vorausschauender Instandhaltung dar.
- Führen Sie Untersuchungen in kurzen Abständen durch, bei denen Sie Handgeräte wie Multimeter, visuelle Thermometer und Schwingungsmessstifte verwenden. Dies sind im Prinzip vereinfachte Instrumente zur Durchführung von Programmen zur vorausschauenden Instandhaltung und für Techniker mit einem geringeren Ausbildungsgrad geeignet. Führen Sie die folgenden Prüfungen durch:
- berührungslose Temperaturmessungen: Untersuchung der Lagergehäuse bei Motoren, der Schalter in Leistungsschalterfeldern und der Kabelanschlüsse bei wichtigen Anlageteilen.
- Schwingungsmessungen mit Gut/Schlecht-Beurteilung bei jedem Lager des Antriebsstrangs, während die Maschine gleichmäßig und bei normaler Betriebstemperatur läuft.
- Spannungs- und Strommessungen im Schnellverfahren und Vergleich der gemessenen Werte mit Schwellenwerten für Symmetrie und Last.
Zusatzoption: schrittweise Integration von Drahtlos-Technologien
SCADA-Systeme sind u. a. so beliebt, weil sie über eine automatische Datenerfassung verfügen. Ihr Team beginnt mit fortschreitender Integration von proaktiven Instandhaltungsmaßnahmen in seine Verfahrensschritte festzustellen, dass nicht alle umfangreichen Systeme Ihrer Anlage jederzeit aktiv überwacht werden müssen. Ausschlaggebend ist der Punkt, an dem eine Maschine oder eine der Hauptkomponenten anfängt zu verschleißen. An diesem Punkt müssen Sie Ersatzteile bestellen, gegebenenfalls Stillstandzeiten einplanen bzw. das System häufiger prüfen.
Manche Teams haben damit begonnen, handliche Testgeräte im Kleinformat zu verwenden, die im Schaltfeld angebracht werden und Daten drahtlos zu einem Hauptmessgerät oder einem Computer übertragen können. Auf diese Weise ist es möglich, diese häufiger auftretenden Datenprüfungen schneller durchzuführen. Hinzu kommt, das nur ein Satz von Messgeräten verwendet wird, der nach Bedarf an einem beliebigen System eingesetzt werden kann.