Elektromotoren gehören zu den wichtigsten Komponenten für industrielle Prozesse. Ihr Anteil am Gesamtenergieverbrauch eines Industriebetriebs beläuft sich oft auf bis zu 70 %. Insgesamt verbrauchen sie bis zu 46 % der gesamten weltweit produzierten Energie. In Anbetracht ihrer großen Bedeutung für industrielle Prozesse kann der Ausfall solcher Elektromotoren schnell mehrere 10.000 Euro pro Stunde kosten. Daher müssen Instandhaltungstechniker und -ingenieure täglich vor allem dafür sorgen, dass Elektromotoren zuverlässig und mit hohem Wirkungsgrad arbeiten.
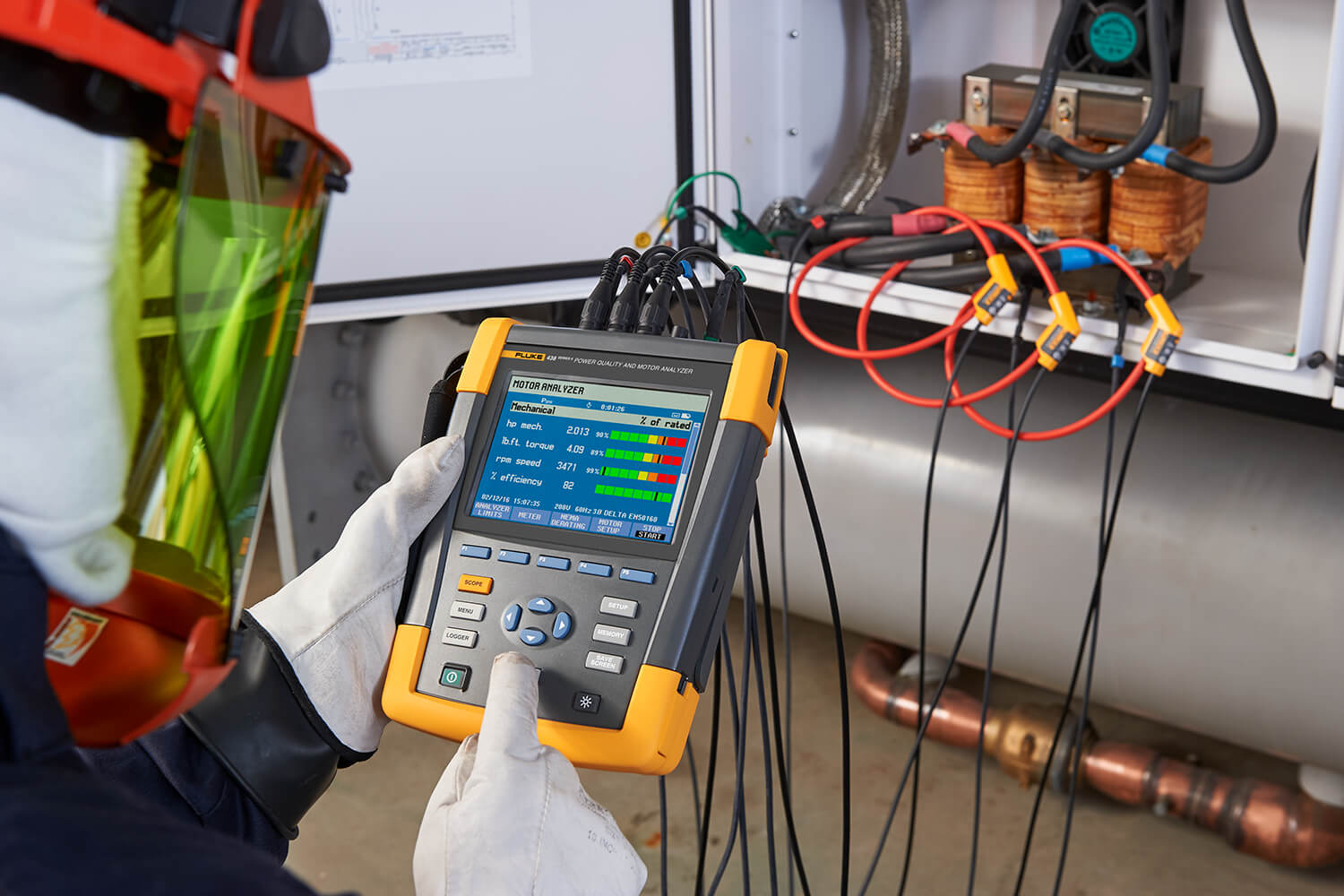
Die effiziente Nutzung elektrischer Energie ist kein Luxus. In vielen Unternehmen macht die Energieeffizienz den entscheidenden Unterschied zwischen Gewinn und Verlust aus. Und da Elektromotoren einen so großen Anteil am Energieverbrauch in der Industrie haben, setzen Betriebe primär hier an, um Einsparungen zu erzielen und die Profitabilität zu erhalten. Der Wunsch, Einsparungen durch Steigerung der Energieeffizienz zu erzielen und die Abhängigkeit von natürlichen Ressourcen zu senken, hat viele Unternehmen dazu veranlasst, ein systematisches Energiemanagement gemäß Industrienormen wie ISO 50001 einzuführen. ISO 50001 legt Anforderungen fest und bildet somit den Rahmen für den Aufbau, die Einführung und die Erhaltung eines Energiemanagementsystems zur Erzielung nachhaltiger Einsparungen.
Herkömmliche Messmethoden für Elektromotoren
Die herkömmliche Methode zum Messen der Leistung und des Wirkungsgrads von Elektromotoren ist hinreichend bekannt, aber ihre Umsetzung ist kostspielig und die Einbindung in Arbeitsabläufe oft schwierig. In vielen Fällen erfordert eine Leistungsmessung sogar das Herunterfahren des gesamten Systems, was zu teuren Ausfallzeiten führt. Um den Wirkungsgrad eines Elektromotors zu messen, muss die elektrische Eingangsleistung und die mechanische Ausgangsleistung unter vielen unterschiedlichen dynamischen Betriebsbedingungen ermittelt werden. Bei der herkömmlichen Methode zur Messung der Motorleistung müssen Techniker den Motor zunächst in einen Motorprüfstand installieren. Dabei wird der zu prüfende Motor über eine Drehmomentmesswelle an einen Generator oder eine Lastmaschine montiert.
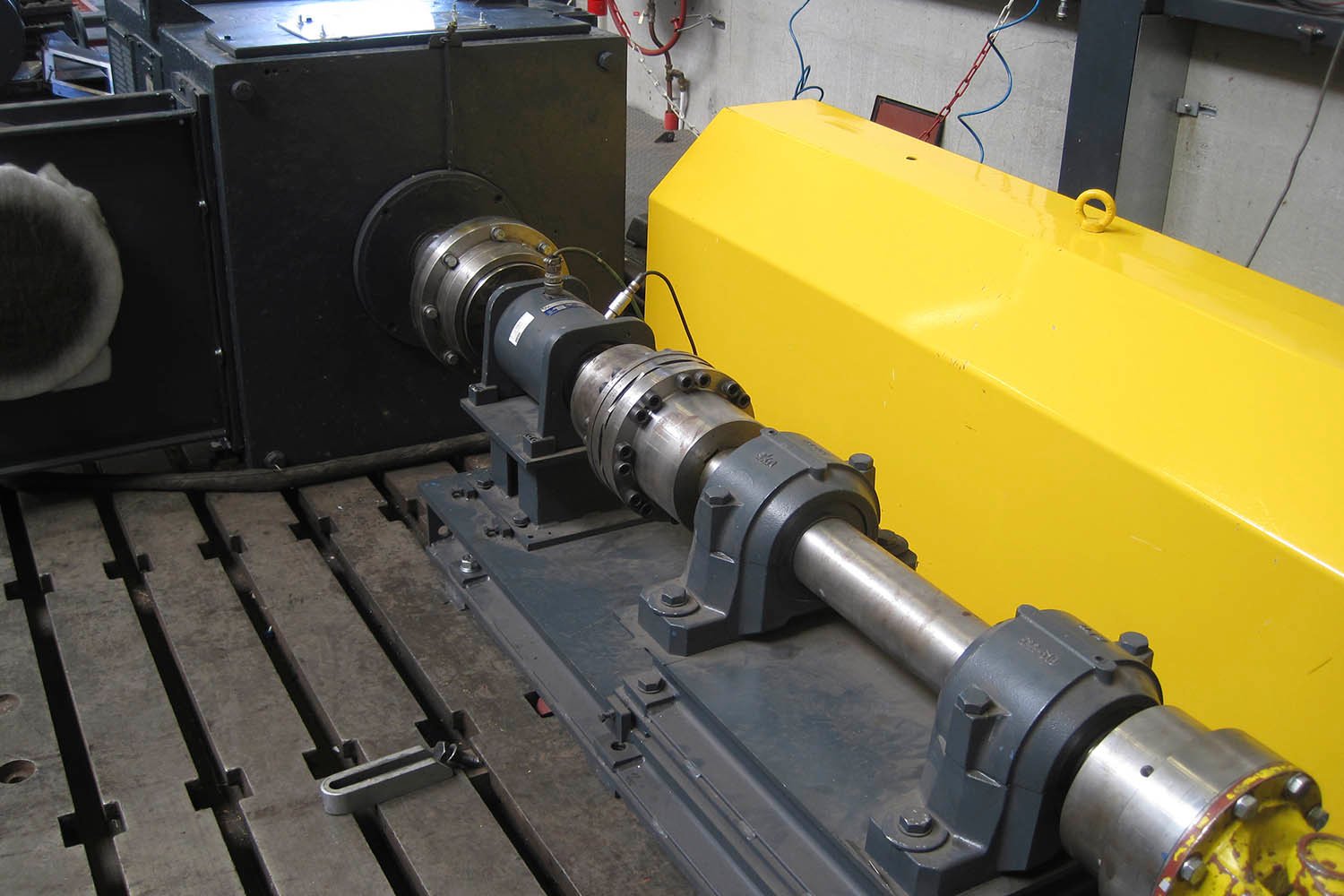
Dann wird der zu prüfende Motor über diese Welle an eine Last angeschlossen. Die Welle verfügt über einen Drehzahlsensor und mehrere Drehmomentsensoren, deren Daten die Grundlage zur Berechnung der mechanischen Leistung bilden. Dieses System liefert Daten wie Drehzahl, Drehmoment und mechanische Leistung. Einige Systeme ermöglichen auch die Messung der elektrischen Leistung, um den Wirkungsgrad zu ermitteln.
Der Wirkungsgrad wird folgendermaßen berechnet:
ɳ(Wirkungsgrad) =
Mechanische Leistung
Elektrische Leistung
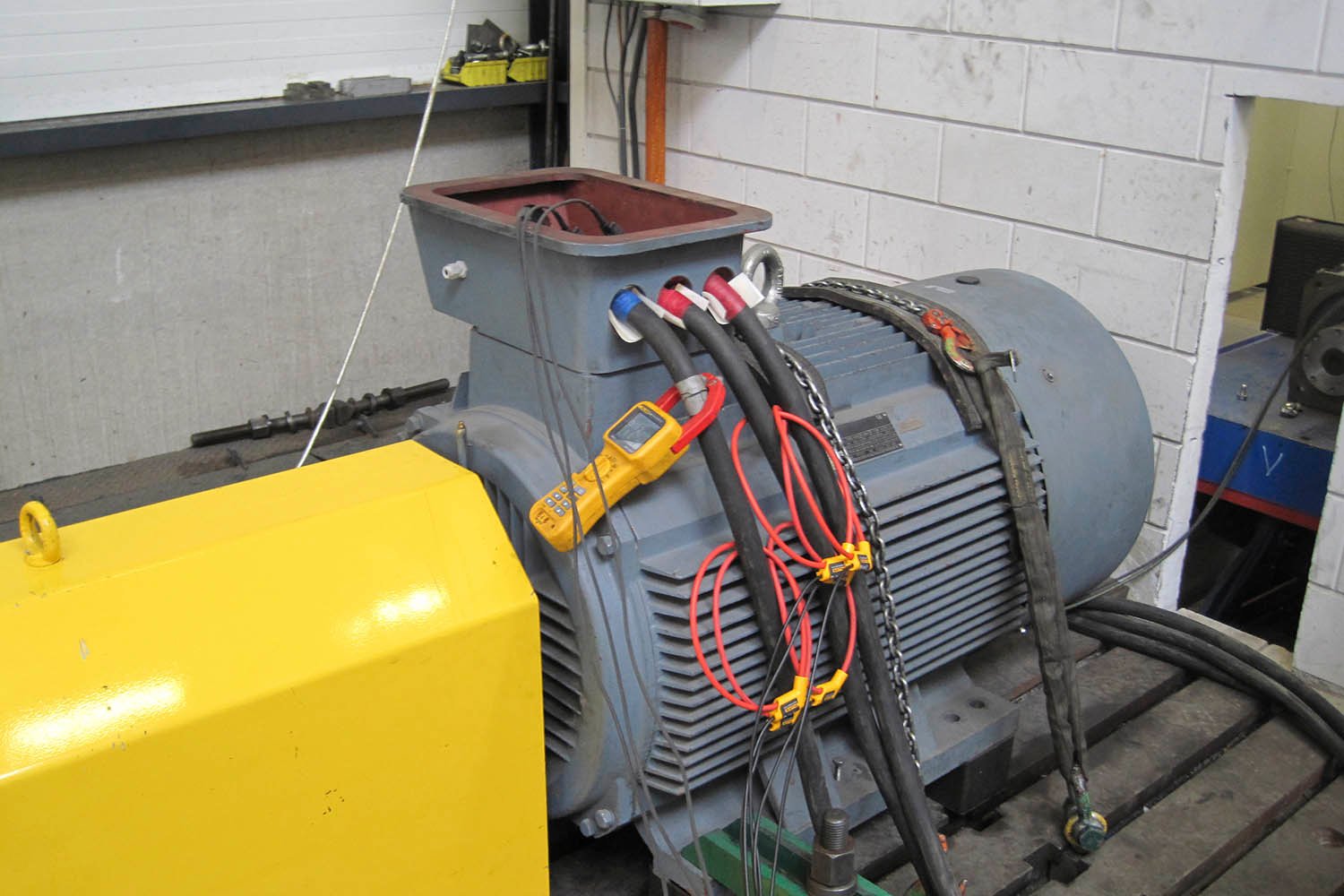
Bei der Messung werden unterschiedliche Lasten angelegt, um den Wirkungsgrad in verschiedenen Betriebsmodi zu bestimmen. Ein Prüfstand dieser Bauart erscheint auf den ersten Blick sinnvoll, aber bei genauerem Hinsehen zeigen sich einige Nachteile:
- Der Motor muss außer Betrieb genommen werden.
- Die Motorlast entspricht nicht exakt den tatsächlichen Betriebsbedingungen.
- Für die Messung muss der Betrieb eingestellt werden (führt zu Ausfallzeiten), oder es muss vorübergehend ein Austauschmotor installiert werden.
- Drehmomentsensoren sind teuer. Da sie aber nur über einen eingeschränkten Betriebsbereich verfügen, sind für die Messungen an unterschiedlichen Motoren oft mehrere Sensoren erforderlich.
- Ein Motorprüfstand für viele verschiedene Motortypen ist teuer und kann meist nur von Spezialunternehmen zur Reparatur und Entwicklung von Elektromotoren bereitgestellt werden.
- Reale Betriebsbedingungen können nicht abgebildet werden.
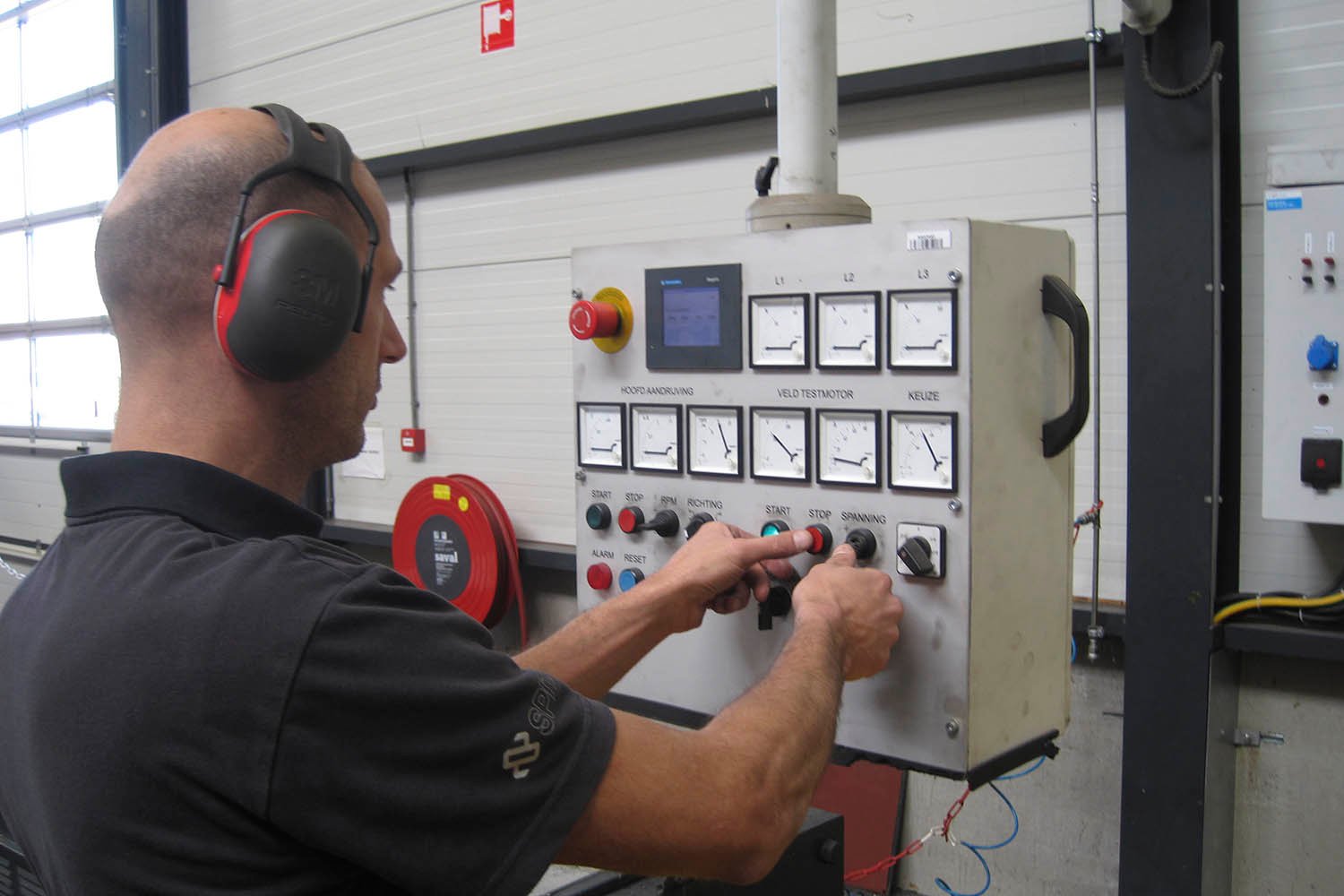
Parameter von Elektromotoren
Elektromotoren werden je nach Last individuell für spezielle Anwendungsbereiche entwickelt. Daher verfügt jeder Motor über unterschiedliche Eigenschaften. Diese Eigenschaften werden gemäß NEMA (National Electrical Manufacturers Association) oder IEC (International Electrotechnical Commission) Normen klassifiziert und haben eine direkte Auswirkung auf den Betrieb und den Wirkungsgrad des Motors. Auf dem Typenschild jedes Motors werden die wichtigsten Betriebsparameter und der Wirkungsgrad gemäß NEMA oder IEC aufgeführt. Anhand der Daten auf dem Typenschild können die Motoranforderungen mit den tatsächlichen Betriebsbedingungen verglichen werden. Durch den Vergleich dieser Werte kann man beispielsweise feststellen, ob bei dem geplanten Einsatz spezifizierte Drehzahl oder Drehmoment des Motors überschritten werden, was zu einer verkürzten Lebensdauer oder einem verfrühten Ausfall des Motors führen kann. Auch Spannungs- oder Stromschwankungen beziehungsweise Oberschwingungen aufgrund einer schlechten Netzqualität können die Betriebseigenschaften des Motors beeinträchtigen. Wenn solche Bedingungen vorliegen, muss der Motor heruntergestuft werden. Das bedeutet, dass die Motorleistung reduziert wird, was sich wiederum negativ auf den gesamten Prozess auswirkt, da nicht genügend mechanische Leistung erzeugt wird. Der Grad der Abstufung wird in Übereinstimmung mit den NEMA-Normen anhand der für den entsprechenden Motortyp festgelegten Daten berechnet. Die NEMA- und IEC-Normen weichen zwar in einigen Punkten voneinander ab, verfolgen jedoch dieselbe Richtung.
Reale Betriebsbedingungen
Das Messen der Betriebsparameter von Elektromotoren auf einem Prüfstand wird meist unter bestmöglichen Bedingungen durchgeführt. Diese Betriebsbedingungen liegen beim tatsächlichen Einsatz jedoch meist nicht vor. Solche Abweichungen bei den Betriebsbedingungen führen zu einer Verschlechterung der Betriebseigenschaften des Motors. Ein Beispiel: In einer Industrieanlage gibt es Lasten, die einen direkten Einfluss auf die Netzqualität haben und die Schwankungen im Energieversorgungssystem und möglicherweise Oberschwingungen verursachen können. Jeder dieser Einflüsse kann negative Auswirkungen auf die Betriebseigenschaften des Motors haben. Außerdem kann die Last, die durch den Motor angetrieben wird, nicht optimal für die Auslegung des Motors sein. Möglicherweise ist die Last für den Motor zu hoch, oder es kommt aufgrund einer mangelnden Prozesssteuerung zu einer Überlast. Denkbar ist auch eine übermäßige Reibung, verursacht durch einen Fremdkörper, der eine Pumpe oder das Flügelrad eines Ventilators blockiert. Die Ermittlung dieser Anomalien ist oft sehr schwierig und zeitaufwendig, was die Fehlerbehebung problematisch gestaltet.
Eine neue Messmethode
Der Netzqualitäts- und Motoranalysator Fluke 438-II ermöglicht eine optimierte und kostengünstige Messung des Motorwirkungsgrads ohne die Installation externer mechanischer Sensoren und teure Ausfallzeiten. Fluke 438-II ist eine Weiterentwicklung des Netzqualitäts- und Stromversorgungsanalysators Fluke 430-II. Er kann sowohl die Netzqualitätsparameter als auch die mechanischen Kenngrößen von Elektromotoren ermitteln, die sich in Betrieb befinden. Anhand der Daten des Motortypenschilds (gemäß NEMA oder IEC) und dreiphasiger Leistungsmessungen ermittelt der 438-II die Motorleistungsdaten in Echtzeit, darunter Drehzahl, Drehmoment, mechanische Leistung und Wirkungsgrad, und ist dabei nicht auf externe Drehzahl- und Drehmomentsensoren angewiesen. Der 438-II berechnet außerdem direkt den Abstufungsfaktor (Derating Factor) des Motors im Betriebsmodus.
Die Daten, die der Fluke 438-II hierfür benötigt, werden vom Anwender eingegeben. Dazu gehören Nennleistung in kW oder PS, Nennspannung und Nennstrom, Nennfrequenz, Nennwerte von cos φ oder Leistungsfaktor, Nennbetriebsfaktor und Motortyp gemäß NEMA- oder IEC-Klassen.
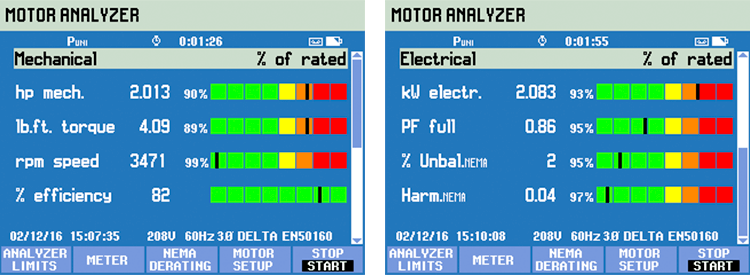
Funktionsweise
Der Analysator Fluke 438-II ermittelt mechanische Messdaten (Drehzahl, Last, Drehmoment und Wirkungsgrad), indem er proprietäre Algorithmen auf elektrische Signalformen anwendet. Diese Algorithmen bestehen aus einer Kombination physikalischer und datengestützter Modelle eines Induktionsmotors, ohne dass sie dafür auf die normalerweise erforderlichen Vormessungen zur Einschätzung von Modellparametern (z. B. Statorwiderstand) angewiesen wären. Die Motordrehzahl kann aus den Oberschwingungen der Signale ermittelt werden, die im Rotorschlitz erfasst werden. Das Drehmoment an der Motorwelle kann anhand bekannter, aber sehr komplexer physikalischer Beziehungen ins Verhältnis zu den Spannungs-, Strom- und Schlupfwerten des Induktionsmotors gesetzt werden. Die elektrische Leistung wird anhand der gemessenen Eingangsströme und -spannungen bestimmt. Auf Basis der Anhaltswerte für Drehmoment und Drehzahl wird die mechanische Leistung (oder Last) mittels Drehmoment mal Drehzahl berechnet. Der Motorwirkungsgrad wird ermittelt, indem der Anhaltswert der mechanischen Leistung durch die gemessene elektrische Leistung dividiert wird. Fluke hat das Verfahren umfassend mit Elektromotoren überprüft, die mit Messinstrumenten ausgerüstet waren und auf Prüfständen mit Lasten beaufschlagt wurden. Tatsächliche elektrische Leistung, Motorwellendrehmoment und Motordrehzahl wurden gemessen und mit den vom 438-II ermittelten Werten verglichen, um die Genauigkeit zu überprüfen.
Zusammenfassung
Obwohl herkömmliche Verfahren für die Messung der elektrischen Betriebseigenschaften und des Wirkungsgrads von Elektromotoren hinreichend bekannt sind, werden sie nur selten genutzt. Dies liegt vor allem an den teuren Ausfallzeiten, die mit diesen Methoden einhergehen, da Motoren und manchmal sogar ganze Systeme für die Überprüfung außer Betrieb genommen werden müssen. Der Analysator Fluke 438-II liefert äußerst hilfreiche Daten, die bisher nur sehr schwer und mit hohem Kostenaufwand ermittelt werden konnten. Außerdem nutzt der Fluke 438-II seine hervorragenden Analysefunktionen für die Netzqualität, um den Zustand des Netzes unter realen Betriebsbedingungen zu überprüfen. Die Messung wichtiger Daten zum Motorwirkungsgrad wird vereinfacht, da keine externen Drehmoment- und Drehzahlsensoren mehr benötigt werden. So können die Betriebseigenschaften der meisten motorbasierten Industrieprozesse bei laufendem Betrieb analysiert werden. Techniker sind damit in der Lage, Ausfallzeiten zu reduzieren und Trenddarstellungen der Betriebseigenschaften von Motoren zu erstellen, um so einen besseren Überblick über den allgemeinen Zustand und die Leistung des Systems zu erhalten. Durch die Trenddarstellung der Betriebseigenschaften lassen sich Veränderungen ermitteln, die auf einen bevorstehenden Ausfall des Motors hindeuten können. So können Reparaturen durchgeführt werden, bevor es zu einem solchen Ausfall kommt.