Energiebesparing is een tweeledig verhaal. Aan de ene kant is er de intentie en aan de andere kant is er de strategie. Industriële faciliteiten in de Verenigde Staten blijven aangeven interesse te hebben in energiebeheer. Dat is de intentie: verlaging van het totale energieverbruik of dit gebruik op een bepaald niveau handhaven, maar daarbij meer produceren per verbruikte hoeveelheid kW.
Dan is er nog de strategie. En hier kan de schoen soms wringen.
In een productieomgeving kan een strategie alleen werken als er genoeg kennis en ervaring zijn om de visie te ondersteunen, maar er moet daarnaast voldoende ROI worden gerealiseerd om te zorgen dat alles de moeite waard is. Maar wat energie betreft, is er niet ergens een onderzoeksinstituut waar een manager van een industriële installatie terecht kan om te bepalen wat "redelijk" energieverbruik is in een productiefaciliteit. Dus hoe kan men dan beoordelen welk deel van het huidige energieverbruik redelijk is en welk deel verspillend is, of welk gedeelte van dat verspilde deel genoeg rendement oplevert om ingrijpen te verantwoorden?
Het rendement waar we het hier over hebben, omvat de kosten per kWh die door het energiebedrijf in rekening worden gebracht. De tarieven hiervan variëren, afhankelijk van het moment van de dag en de tijd van het jaar. Verlaging van deze kosten leidt ook meteen tot kostenbesparing. De investering bestaat uit het materiaal en de arbeid die nodig zijn om het energieverbruik te wijzigen. Het rendement is de periode die moet verstrijken voordat de lagere energierekening leidt tot het ontstaan van rendement. Wat er overblijft nadat de kosten zijn betaald, is dan de kers op de taart.
Als we dan weer kijken naar de strategie, hoe kunnen we dan inschatten hoeveel rendement deze ingrepen gaan opleveren als er in de branche geen standaard is voor redelijk energieverbruik waartegen we dit kunnen afzetten?
Een profielschets maken van industrieel energieverbruik
Energieverbruik in de branche varieert en dat heeft te maken met meerdere factoren:
- de leeftijd van de fabriek
- het soort belasting en het formaat daarvan
- het bedrijfsschema, zowel uren per week als de intensiteit van de belasting
- het aantal werknemers
- het klimaat
- de onderhoudsfilosofie.
Het antwoord op deze vraag is: probeer niet elke kW te beheren die wordt verbruikt door uw faciliteit. Dit zijn de 'kennis en ervaring' in de vergelijking. Verdeel de faciliteit op basis van de elektrotechnische infrastructuur en vervolgens op basis van de belangrijkste systemen.
Energiebesparing begint met twee basistactieken: (1) algemene inspectie van belangrijke systemen en (2) gerichte verzameling van gegevens, waaronder het loggen van het energieverbruik bij de hoofdservice-ingangen en bij de belangrijkste belastingpunten.
Stel vast wat het gespecificeerde verbruik van een systeem is en hoeveel het systeem momenteel verbruikt. Stel daarnaast vast hoeveel verspilling er optreedt (hetzij qua uren en het soort gebruik van het systeem of qua apparatuur en het systeem zelf). Om de besparingen te realiseren, moet deze verspilling in de faciliteit worden aangepakt, door veranderingen op het gebied van procedures, onderhoud of apparatuur en controles.
Energiecomponenten
Voordat we gaan kijken hoe we energieverbruik kunnen bijhouden, gaan we nog een keer kijken hoe we energie definiëren en meten.
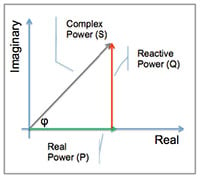
Energie kan worden uitgedrukt in werkelijk, reactief en schijnbaar vermogen (Afbeelding 1).
De energiestroom wordt beschreven als:
- werkelijk (P) of actief vermogen in watt (W)
- reactief vermogen (Q) in voltampère reactief (VAr)
- complex vermogen (S) in voltampère (VA)
- schijnbaar vermogen, de grootte van complex vermogen (VA)
De wiskundige relatie tussen reëel, reactief en schijnbaar vermogen kan worden weergegeven door vectoren of kan worden uitgedrukt met complexe getallen, S = P + jQ (waarbij j de denkbeeldige eenheid is).
Reactief vermogen brengt geen energie over - het produceert geen arbeid - en wordt dus weergegeven als de denkbeeldige as van het vectordiagram. Werkelijk vermogen verplaatst energie, dus dit is de werkelijke as.
De snelheid van de energiestroom in een systeem is afhankelijk van de belasting - is deze resistief, reactief of beide?
Bij een zuiver resistieve belasting, spanning en omgekeerde polariteit van stroom tegelijkertijd, is het product van spanning en stroom op elk moment positief en wordt alleen echt vermogen overgedragen: er wordt arbeid geproduceerd.
Als de belasting zuiver reactief is, zijn de spanning en stroom uit fase en kan het product van spanning en stroom positief of negatief zijn. Dit geeft aan dat een deel van de energie naar de belasting wordt overgebracht en dat een deel ervan terugstroomt. De netto-overdracht van energie naar de belasting is nul: er wordt geen arbeid geproduceerd.
In werkelijkheid omvatten alle belastingen een combinatie van weerstand, inductantie en capaciteit, waardoor zowel werkelijk als reactief vermogen in een systeem ontstaat. Daarom zijn elektrische systemen zo ontworpen dat ze een bepaalde hoeveelheid reactief vermogen tolereren. Problemen ontstaan wanneer er te veel reactief vermogen wordt gegenereerd. Niet alleen is er niet genoeg werkelijk vermogen om de vereiste arbeid te produceren, maar zelfs de algemene capaciteit voor het genereren van arbeid van het systeem wordt in gevaar gebracht. Dat is ook de reden dat nutsbedrijven hun klanten beboeten als hun belastingen te veel reactief vermogen produceren: het is verspilling van vermogen omdat het geld kost om het op te wekken, maar het kan niet worden gebruikt. De meeste energierekeningen tellen VAr (reactief vermogen) en op vele wordt ook de vermogensfactor berekend, waarbij de vermogensfactor een indicatie is van hoe veel een systeem gedaald is ten opzichte van 100 procent werkelijk vermogen. De meeste nutsbedrijven eisen dat hun klanten boven de grens van 0,95 PF (Power Factor, vermogensfactor) blijven.
Energieverbruik in de gaten houden
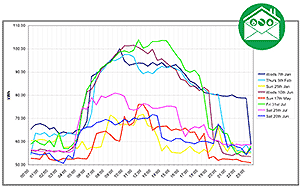
Door inzicht te krijgen in de basiscomponenten van energie kan een elektricien apparatuur voor het loggen van energieverbruik instellen om het algehele niveau en de kwaliteit van het verbruik te meten en vervolgens te traceren wanneer energie wordt verbruikt en door wat (Afbeelding 2).
Log het vermogen bij hoofd- en secundaire panelen en bij grote belastingen. Leg kW, kWh en de arbeidsfactor vast gedurende een representatieve tijdsperiode.
Zo krijgt u een zeer nauwkeurig beeld van het werkelijke energieverbruik bij driefasige circuits en belastingen.
De grootste energiebesparingen kunt u realiseren door te bepalen op welke tijdstippen het stroomverbruik pieken vertoont, waarbij u de vermogensfactor en het totale stroomverbruik evalueert ten opzicht van de facturen van het nutsbedrijf, en eventueel de belastingen opnieuw uit te balanceren. Zelfs een piekverbruik van slechts een paar minuten kan het tarief van het energiebedrijf gedurende enkele uren, dagen of zelfs weken verhogen.
Door het gebruik van de belastingen anders in te plannen, kan een bedrijf profiteren van tijden dat de energie goedkoper is. Kijk hoe ver onder '1' de vermogensfactor ligt en controleer de facturen van het energiebedrijf om te zien of er aftrek is voor een slechte vermogensfactor. Als dit het geval is, kan de Power Logger helpen om de bronnen te traceren. Nadat u wijzigingen hebt uitgevoerd op de noodzakelijke energiegebieden, sluit u de logger opnieuw aan om te controleren of u inderdaad profijt hebt van deze efficiëntieverbeteringen.
Weten waar energieverspilling optreedt
Elk systeem en elk proces kan een bron van verspilling zijn en deze moet worden ingedamd of worden verholpen. U kunt al beginnen door elektrische subsystemen, perslucht- of stoomsystemen en specifieke elektromechanische systemen onder de loep te nemen, maar eigenlijk kent elk proces wel potentiële verspilpunten die moeten worden gemeten.
Het doel is om het energiegebruik van specifieke apparatuur en processen in kaart te brengen, om te kijken waar energie wordt verspild zodat verspilling gekwantificeerd kan worden. Daardoor kunt u prioriteit te geven aan verbeteringen of vervangingen op basis van de levensduur van de apparatuur en kijken welke aanpassingen het meeste rendement opleveren.

Het in kaart brengen van verbruik biedt ook een uitgangspunt op basis waarvan de effectiviteit van energiebesparende projecten kan worden gemeten om kosten te rechtvaardigen (Afbeelding 3).
Veelvoorkomende bronnen van verspilling in elektrische subsystemen:
- Belastingen blijven soms ingeschakeld buiten werktijd of zijn onnodig in bedrijf op het duurste moment van de dag.
- Als er geen regeling is ingesteld op de motor kan dit betekenen dat er meer vermogen wordt gegenereerd dan nodig is.
- Processen met te hoge spanning/stroom veroorzaken overmatig stroomverbruik ter compensatie.
- Fase-onbalans zorgt ervoor dat bij belasting stroom wordt verbruikt zonder dat deze kan worden ingezet.
Identificeren en kwantificeren:
- Maak een thermische scan van het elektrische paneel en de mechanische belasting om te controleren op oververhitting.
- Log energieverbruik gedurende een langere periode: hoeveel energie wordt er verbruikt, op welk tijdstip en met hoeveel verspilling gaat dit gepaard?
Veelvoorkomende verspilling en inspectiepunten in elektromechanische systemen:
- Door overmatige wrijving vanwege uitlijnfouten, lagers, onbalans en losheid moet de motor te hard werken, waardoor te veel vermogen wordt verbruikt.
- Ongecontroleerde belastingen blijven soms buiten werktijd ingeschakeld, zijn in bedrijf op piektijden, genereren meer vermogen dan nodig is of hebben te lijden van overspanning/stroomcondities en fase-onbalans.
- Verouderende mechanische apparatuur kan zó veel meer energie verbruiken dan nieuwe modellen met hoog rendement, dat vroege vervanging alleen al vanwege het lagere kWh-verbruik gerechtvaardigd kan zijn.
Identificeren en kwantificeren:
- Maak een thermische scan van het aandrijvingspaneel en de mechanische belasting om te controleren op oververhitting. Oververhitting kan duiden op elektrische inefficiëntie.
- Log energieverbruik gedurende een langere periode: controleer op de totale hoeveelheid kWh, de arbeidsfactor, de piekvraag, onbalans en harmonischen.
- Test trillingsniveaus aan de hand van normen en stel vast welke onderhoudsoplossingen het meest geschikt zijn, zoals herbalancering.
- Voer een thermische scan uit van koppelingen/assen/riemen, lagers en ventilatoren.
- Controleer stroom- en spanningsniveaus.
- Voer een thermische scan uit van de afsluit-/aansluitdoos en wikkelingen en voer een isolatieweerstandstest uit.
Veelvoorkomende verspilling en inspectiepunten in persluchtsystemen:
- Overmatige lekkage in persluchtleidingen leidt tot overmatige werking om de toevoer te handhaven.
- Compressoren die ingeschakeld blijven buiten werktijd, verspillen energie.
Identificeren en kwantificeren:
- Log energieverbruik bij de compressor en vergelijk dit met het basisverbruik.
- Meet de druk bij de compressor en op het gebruikspunt om de drukdaling te bepalen.
- Scan leidingen met ultrasoon geluid om lekken vast te stellen.
Veelvoorkomende verspilling en inspectiepunten in stoomsystemen:
- Defecte condenspotten en ontoereikende isolatie leiden tot verspilde stoom, waardoor er onnodig veel stoom wordt geproduceerd om de noodzakelijke toevoer in stand te houden.
Identificeren en kwantificeren:
- Log energieverbruik bij de ketel en vergelijk dit met het basisverbruik.
- Voer een thermische scan van leidingen en condenspotten uit om ontbrekende isolatie en verstoppingen te identificeren.
Rendement inzichtelijk maken
Hoe weten we, kijkend naar het bovengenoemde ontbreken van branchestandaarden, nu echt welke systemen de meeste potentiële energieopbrengst hebben? Onze beste bron van informatie wordt op dit moment gevormd door de voorbeelden van veelvoorkomende situaties. Hier volgen enkele voorbeelden van gangbare industriële systemen.
Inspectie elektromechanisch systeem
Type faciliteit: recyclinginstallatie van staal in Duitsland
Type apparatuur: ventilator met riemaandrijving, voor proceskoeling
Metingen uitgevoerd: trillingsmetingen
Vastgestelde problemen: er is lichte onbalans gedetecteerd, naast verkeerde uitlijning en slijtage van het lager.
Gerealiseerde besparingen: Opnieuw balanceren was noodzakelijk. Een motor van 350 kW draaide op 80 procent van het nominale vermogen; het gemeten vermogen bedroeg ongeveer 280 kW. Na het opnieuw balanceren, werd 3 procent minder energie verbruikt. Bij een tarief van 0,11 euro/kWh levert dit een jaarlijkse besparing van 8.094 euro op.
Inspectie persluchtsysteem
Type faciliteit: productie
Type apparatuur: persluchtsysteem
Metingen uitgevoerd: test van het persluchtsysteem met ultrasoon geluid (aanbevolen volledige datalogging van de compressor)
Vastgestelde problemen: de hoeveelheid perslucht die wordt geproduceerd in vergelijking met de werkelijke vraag.
Gerealiseerde besparingen: Er zijn meerdere besparingsmogelijkheden gevonden. Totale jaarlijkse besparing van $50.600. De compressor wordt in het weekend uitgeschakeld: jaarlijkse besparing van $32.700. Er worden solenoïdes geïnstalleerd om de luchttoevoer uit te schakelen wanneer de machines worden uitgeschakeld: jaarlijkse besparing van $7.100. Reparatie van 36 lekken: jaarlijkse besparing van $4.800. Filters in het systeem geïnstalleerd tegen eenmalige kosten van $6.000; jaarlijkse besparingen als gevolg van deze filters: $6.000.
Inspectie van condenspot
Type faciliteit: productie
Type apparatuur: ketels en stoomleidingen
Metingen uitgevoerd: thermische scan van stoomleidingen
Vastgestelde problemen: zes niet goed werkende condenspotten; stoomlekkage uit spoelen van een galvaniseertank; stoomlekkage uit galvaniseerleidingen: mogelijkheden voor terugwinning van condensaat
Gerealiseerde besparingen: zes niet goed werkende condenspotten zijn vervangen voor $500 per stuk. Gerealiseerde besparingen: $3.200 per condenspot op basis van bekende kosten, voor het genereren van berekeningen van stoom en warmteverlies. Totale besparing: $16.200.
Volgende stap: log het energieverbruik op het aanvoerpaneel van de ketel voor en na het aanpakken van lekken en condensaatproblemen.
Hogere productiviteit of lagere overhead?
De volgende vraag is een leuke vraag om te beantwoorden: als u eenmaal hebt bepaald welke route u wilt volgen om energieverbruik te verminderen, kunt u die besparingen dan gebruiken om de opbrengst van de fabriek te verhogen (grotere volumes produceren bij hetzelfde kWh-verbruik) of voor andere bedrijfsstrategieën (winstmarges, prijsrealisatie)?
Het verlagen van het energieverbruik is simpelweg goed voor de zaak. Door het verbruik van elk belangrijk systeem te loggen en deze kosten in kaart te brengen aan de hand van de energierekeningen om te bepalen waar en wanneer het verbruik plaatsvindt, kunnen bedrijven vaak besparingen realiseren door eenvoudige aanpassingen van hun processen en werkschema's. Bedrijven kunnen eenvoudig vaststellen welke apparatuur inefficiënt en verouderd is en vervanging daarvan verantwoorden en prioriteit geven. En door het totale energieverbruik te verlagen, dringen bedrijven bedrijfskosten terug en verbeteren ze hun concurrentiepositie op de markt.
Lees dit artikel als PDF-bestand