How to reduce power consumption in air compressors
Everyone has the ability to make an impact on energy consumption and use. No matter how big or small your company is, or whether you work in residential or industrial settings, there are steps you can take to save energy. Because compressed air is a large portion of many industries’ energy bill, it is often one of the largest opportunities to save energy.
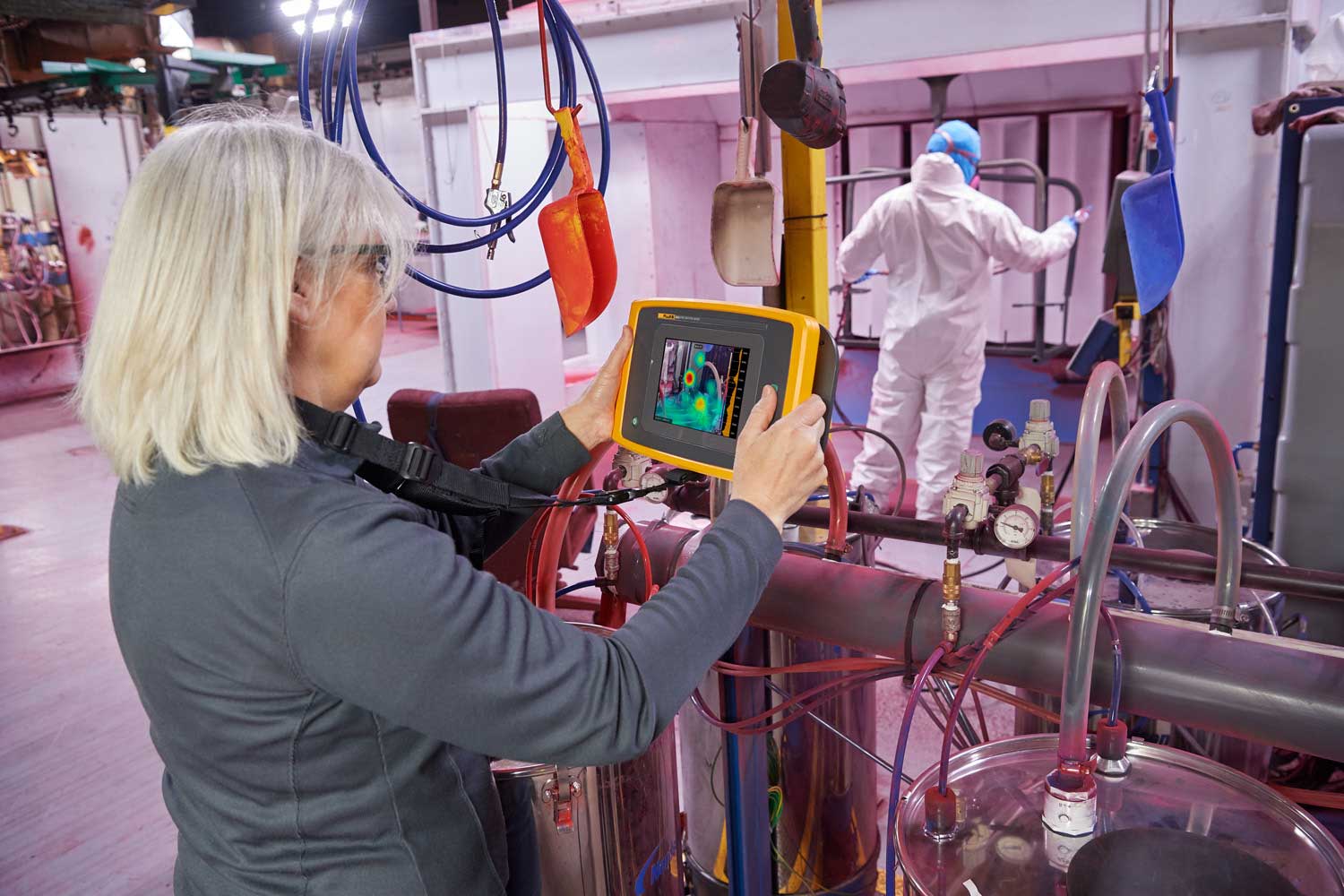
Best practices for compressed air systems
Understanding how you use air compressor energy around your facility can create many benefits for your company and help you optimize your compressed air consumption, and even your overall energy consumption over time. According to Daryll Cox, Better Plants Diagnostic Equipment Program Manager at The Department of Energy (DOE), the typical goal is to see a 25% reduction in energy intensity (MMBtu/unit of production) over a ten-year period.
To follow best practices for your compressed air system, start by answering these questions about your compressed air use and making adjustments to address these areas.
Is the system delivering air at the lowest practical pressure?
Operating your compressed air systems at elevated pressures not only costs more but increases the rate of leaks developing and air consumption of end uses. Instead, operating at minimum practical pressure for end uses reduces compressed air consumption, the leakage rate, and overall energy consumption.
Do we have storage and automatic system controls?
Operate only the number of compressors required to meet demand at any given time. Use an automatic sequencing of compressors to help optimize which compressors are in-use during peak demand cycles, cutting your operating costs.
What are air leaks costing me?
Identify leaks using your ii900 Industrial Acoustic Imager and understand the cost of each one. Take the time to work your way down the list of leaks, beginning with the most significant. Compressed air systems often show a 20 to 30 percent leakage rate, costing a lot over the long run. Set up a continuous program to detect these leaks and repair them regularly.
Is compressed air the best option for this application?
Although compressed air can be a very versatile utility, it’s not always the best choice for all applications. Compressed air does have a cost associated with it which should be factored in and compared against other alternatives to ensure it’s the right option.
What is the minimum practical pressure required for my application?
If you can trade out your compressor for a low-pressure blower, an electric motor, or a vacuum pump, it can cut down on your air energy costs.
Are we shutting off compressed air when it’s not needed?
Some applications do not require compressed air 100 percent of the time. Shut off the supply to those applications when it’s not needed. This will help you save money overall, but also cut down on the regular wear and tear of your pipes and hoses that often leads to leaks.
Do all parts of our process need air at the same time?
Often, all parts of your process may not need compressed air at the same times. Analyze the peak and average flow rates to determine your needs at each step in the process.
Are the equipment controls appropriate to deliver compressed air?
Check the controls, receiver sizes, pressure and flow controllers, as well as filters, regulators, and lubricators. You want to be using the right type, range, and size for your specific application and needs.
What is the cost of compressed air for each machine and process?
In order to measure air computation accurately, you need to understand the true cost of operation. Calculate air consumption and electrical power needed to run each machine and each process in your facility so you understand where money is going and where you may be able to conserve resources.
Who should be involved in this process?
Compressed air supply side personnel should be included in the process and any end use discussions that come from the above questions. Changes anywhere in your compressed air process can impact the whole system, so make sure the right members of your team are aware of what’s going on.
Once you’ve followed the questions and made the adjustments recommended above, you should start to see a corresponding reduction in your compressed air, and overall energy use.
DOE Better Plants Program
As part of the Better Plants Program, the DOE will loan participating companies instruments they can use to evaluate your compressed air use. The program is completely free and can help you gauge your current program energy management levels and review your levels after changes have been made.
Tools available to complete energy consumption evaluation
The DOE offers a full suite of diagnostic tools to borrow so you can collect energy data and improve equipment performance throughout your facility. The DOE has 22 tools available to borrow, but depending on your facility needs, you may not need to have all of them on-hand. When you’re looking at your facility’s air compressor energy use, it’s incredibly useful to have an acoustic imager throughout the process.
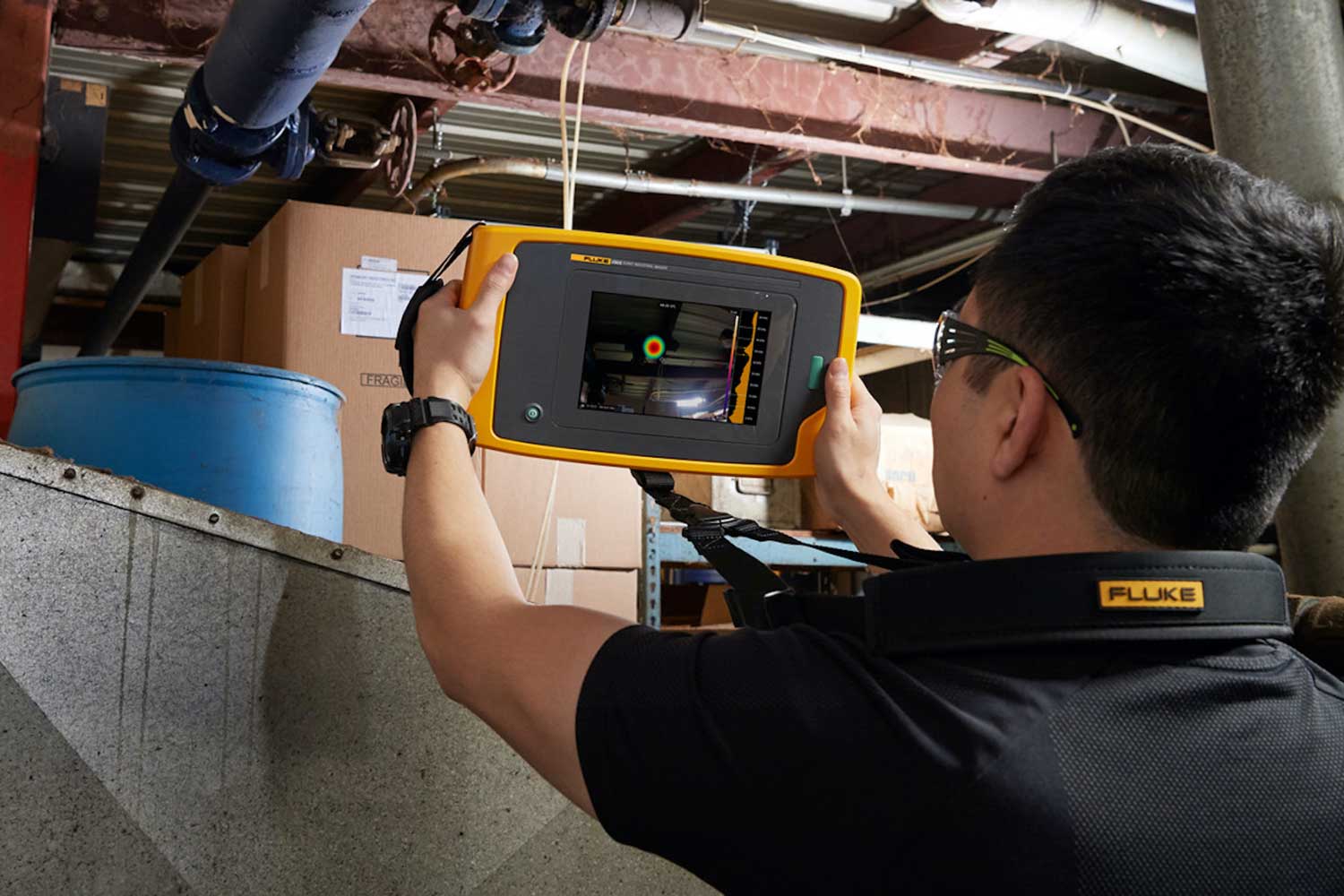
Fluke ii900 Industrial Acoustic Imager
You can visualize sound with an ii900 Industrial Acoustic Imager. This gives you a quick and easier way to find leaks in compressed air and gas lines. Find leaks faster than traditional methods to identify spots across your facility that are causing energy waste. Once you’ve repaired the leaks, you can also use the ii900 to verify the leaks are fixed and no longer causing extra air or gas to be pushed through the lines.