Case study: Energy logger helps cut utility surcharges and power waste
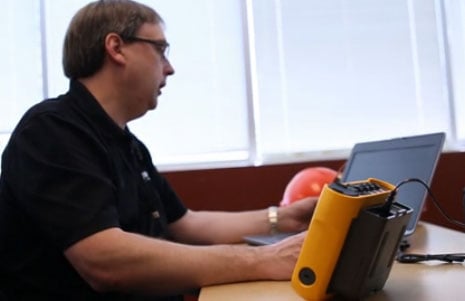
At commercial buildings and industrial plants, energy costs can quickly add up, especially when older lighting systems are in place, motors age and the compressed air lines snaking around the plant leak, requiring unnecessary cycling of compressors.
In many cases, utilities tack on power factor and demand penalties for customers whose power systems have reactive loads that pass out-of-phase voltage and current into the grid. Power factor is sometimes compared to the froth in beer that bartenders must scrape off. Carrying that analogy forward, the pub (utility) would charge for dealing with the foam from the beer.
Energy surveys are commissioned from special consultants or done in-house with the idea that the cost of the service can be offset by the savings realized by identifying how power factor can be managed and where more efficient equipment is in order.
Often, single-phase measurement devices were used in such surveys. Those loggers typically only provided amperage readings and maybe voltage readings over a specified time period. The true power was then derived using another meter from a spot check on the power supply, then calculated out. Calculations were done for kilowatt hours and then finally into potential cost savings.
Relief from cumbersome ways
"The problem is that it didn't pick up variability in different things, like voltage variability and power factor variability, so you're making an assumption that there are some variables that are locked down and constant that might not be," says Mark Nieman, Energy Engineering Manager at McKinstry, an energy service company in Seattle, Wash.
With the Fluke 1730 Three-Phase Energy Logger, energy consultants, plant electricians and electrical contractors now have a powerful yet simple tool to record power parameters and harmonics, and capture voltage events that can uncover electrical energy waste.
"The 1730 is a true-RMS power logger," Nieman says. "The way we use it is for base-lining energy use in typical equipment within commercial buildings. So we use it if we want to figure out if a fan system is modulating or how much power a pump system is pulling or if compressors are cycling within a piece of equipment."
It's a tool that sets up in minutes and includes a color display and flexible current probes. "One of the easiest loggers I've ever seen," Nieman says. "The CT cables are thin and easy to get around the conductors in tight spots."
The logger helps give visibility into what is going on in electrical systems. "The logging function allows us to record data anywhere from two weeks to a month or more," Nieman says. "And we can use that for our base-lining basis of energy savings calculations."
The 1730 measures voltage, current, power, and power factor and associated values.
Easy data download
Once all the data is captured, it can be downloaded via any USB thumb drive or other USB device, right into a computer for further analysis.
The Fluke Energy Analyze application software helps determine the energy savings potential.
"I use the program to look at the calendar view of the demand modulation of the device I'm testing," noted Nieman. "We also get some good summary tables."
The data can be further exported to a spreadsheet where it can be correlated with other data sets—such as temperature data in an HVAC scenario for deeper analysis. All of the analysis can then be compiled to report out to the customer or company management for possible corrective measures such as the addition of a capacitor bank to correct power factor, the acquisition and installation of new motors or variable frequency drives, or other actions.
After those measures are completed, you can use the 1730 to verify the power is working as predicted by the team that initiated the survey. You can generate a report on the actual energy use afterward. "We have found that resulting energy savings can be from hundreds of dollars to hundreds of thousands of dollars for a large commercial customer," Nieman says.
As an energy services company, McKinstry has performance guarantees that are tied to their projects, so coming up with the proper data is a vital deliverable—required under the contracting process.
"Because of the ease of using the logger you reduce time in terms of deployment. And the quality of the data is better so you don't have to do as many work-around calculations. That makes it easier to substantiate findings in your reports when you're working with the utilities for rebates and things of that sort. Depending on the size of the job you can easily save from 4 to 20 hours on each job because of the quality of the data and the ease of launching the study and pulling the data."
$46,000 in savings found
Indeed, in one case at a Seattle-area laboratory, the 1730 helped uncover substantial electrical cost savings as well as a rebate from the local utility.
The logger proved inefficiencies and justified the acquisition of a new air handler with heat recovery, updated lighting and new HVAC terminal boxes.
"In that project, the electrical savings was in the order of 111,000 kilowatt hours," Nieman says. "Based on the trending I got off the logger we're getting a one-time payment from the utility for $42,000 and a savings year-over-year at current rates of $46,000. That was a project we used the Fluke on."
That savings was from monitoring all input legs of the three-phase power for both the supply and exhaust fans of the air handler. These fans already had older variable frequency drives that were at the end of their service life, but the existing system did not allow for much modulation in the system and weren't capable of saving as much energy as possible. Addition of the new terminal boxes and the new air handler will allow for modulation of the system and save energy.