Vibration Monitoring Sensors
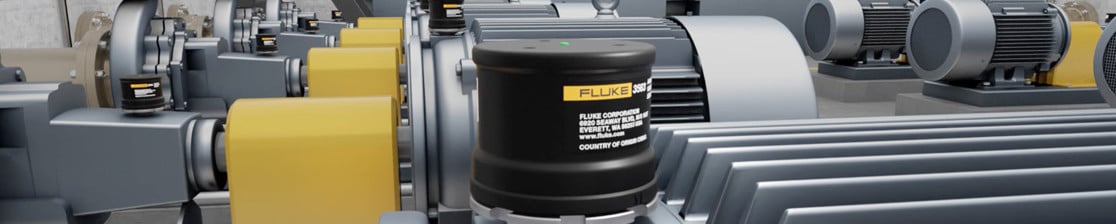
Enhance your maintenance with Fluke's vibration monitoring sensors
While all machinery vibrates, using vibration detectors to track excess vibration in rotating equipment is key to early identification of asset issues. Vibration monitoring uses sensors and tools to detect changes in amplitude, frequency, and intensity of forces that damage rotating equipment. Studying vibration measurements allows teams to discover imbalance, looseness, misalignment, or bearing wear in equipment prior to failure.
Getting the most from a vibration monitoring program
Tracking vibration measurements enhances your maintenance and reliability program by:
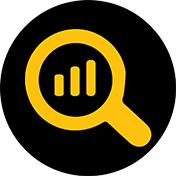
Solving common problems using vibration measurements
Vibration can prematurely wear components, shorten the life of equipment, create noise, and result in safety issues. Imbalance or misalignment in rotating assets may crack or break driveshafts and other components.

Visually illustrating the severity of vibration
Leverage customizable and auto-generated thresholds based on asset details and get warning notifications are via email and/or through the eMaint Condition Monitoring software.
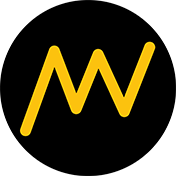
Vibration analysis services to drive your condition monitoring strategy
Our Expertise as a Service offering bolsters maintenance teams with assistance and training when they need it. Teams can take advantage of these services to launch condition monitoring programs that position them for a future of IIoT.
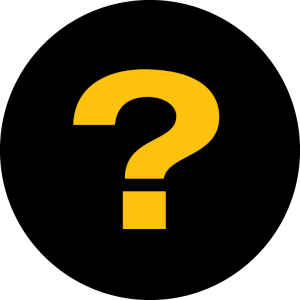
Q&A
What is vibration monitoring?
Vibration is not inherently bad — every rotating machine has a unique vibration signature. When a machine’s vibration measurements change, though, it can be an indication of potential faults. Vibration monitoring makes it possible to identify changes in vibration when they occur so that maintenance teams can diagnose and fix problems before they escalate. Taking action before failure occurs keeps equipment in peak operating condition longer.
A vibration monitoring program uses sensors and tools to measure changes in the amplitude, frequency, and intensity of forces that damage rotating equipment. Armed with this data, maintenance teams can conduct vibration analysis to discover imbalance, looseness, misalignment, or bearing wear in equipment prior to failure. Handheld vibration measurement tools and wired or wireless vibration sensors are a few options for capturing vibration data.
What is vibration measurement?
Vibration measurement is the practice of measuring vibration levels with handheld tools, sensors, or on-line systems, often to detect or diagnose faults in vibrating machinery. Measuring vibration gives you insight into the condition of your components, from shafts to fan blades and bearings. Vibration measurements can be general “overall” readings of total average vibration amplitude, or more in depth. Fast Fourier Transform (FFT) readings reveal distinct vibration signals that experts can recognize as coming from specific components. Vibration test personnel use vibration measurements for screening, continuous monitoring for new faults, and to diagnose existing problems caused by vibration.
How does vibration measurement work?
Wear and tear can change how bearings, rotors, shafts, and other machine parts vibrate. Vibration monitoring involves collecting vibration measurement data while assets are operating. Vibration sensors mounted directly on machines measure changes in the amplitude, frequency, and intensity of vibration, detecting changes early on. Analyzing vibration data enables maintenance teams to diagnose problems and prioritize their efforts.
Vibration monitoring has a broad range of applications. Rotating equipment is especially well-suited to vibration monitoring for identifying and diagnosing faults. Data captured in real time makes it possible to minimize unplanned downtime and maximize availability and uptime.
Talk to a sensor specialistHow is vibration measured?
Vibration is measured in the frequency of the revolutions or oscillations around a reference point. For example, a shaft vibrates relative to the casing of a piece of machinery and a bearing vibrates relative to a bearing housing. Hertz (Hz) is the standard vibration measurement unit. The frequency of vibration is measured by accelerometers, MEMS sensors, and/or piezoelectric sensors, which convert vibration data into electrical signals for analysis.
How to measure vibration
Vibration testing personnel measure vibration with handheld analyzers, wireless vibration sensors, or through on-line vibration monitoring systems. Most vibration tools capture the time waveform of the vibration over time. This can then be translated into frequency domain readings through FFT conversion, which gives further insight into what components are responsible for which signals, and which faults are present.. Wireless sensors give you the power to monitor asset condition 24/7, sending measurements to your systems at specified intervals. These are ideal for setting up alarms when vibration readings exceed normal levels. On-line vibration monitoring systems are sophisticated wired set ups that continuously collect data. Vibration experts implement on-line monitoring to work on critical machines that need in-depth vibration analysis.
What is a vibration sensor?
A vibration sensor simply measures the vibration of the machine it is mounted on. Vibration sensors are available for a wide range of applications, priorities, and budgets. They reduce the need for technicians to go asset to asset taking measurements with handheld tools. Thanks to real-time asset condition data, teams can focus on the assets that need attention.Wired vibration sensors can take and transmit vibration measurements continuously, while wireless vibration sensors take and transmit measurements at regular intervals. Depending on the specific sensor and need, this interval can be as frequently as every minute.
Each type of vibration sensor has benefits and drawbacks. Wired vibration sensors can cost more, and the necessary cabling can add complexity and limitations, but they can collect extensive and detailed data.
Wireless vibration sensors can have their data transfer speeds impacted by a variety of factors, such as connectivity and location. But they are much simpler and less expensive to install than wired sensors, making them highly scalable.
A well-rounded vibration monitoring system can include both wired and wireless vibration sensors to balance their strengths and weaknesses.
What are the 3 key types of vibration measurement sensors?
Wireless Vibration Sensors - Screening
Wireless vibration sensors are a powerful tool for vibration measurement. Wireless vibration screening sensors in particular are ideal for monitoring semi-critical machines, where overall vibration measurements are sufficient.
Wireless Vibration Sensors - Analysis
Wireless analysis vibration sensors are best for critical machines, giving you real-time data, configurable alarms, and even recognizing the four common vibration fault signatures for you with the help of software.
Wired Vibration Sensors
A wired vibration sensor system is installed to give in-depth, 24/7 vibration measurements for production-critical machines like turbine generators. Wired sensor systems gather large quantities of high-resolution vibration data.
Why are vibration sensors used?
Vibration sensors are a key piece of predictive maintenance programs. Maintenance and reliability teams can minimize costly production interruptions and downtime when they have accurate, real-time vibration data.
Typically, the most critical assets need the most monitoring — that means more data captured more often. Some assets may be monitored effectively with overall snapshots of vibration data, or with measurements taken regularly but not continuously. An asset’s setting should be taken into consideration, too — a wired vibration sensor may not work in every location.
How do vibration sensors help prevent failures?
Take bearings, for example. In general, vibration monitoring can detect slight bearing wear 12 to 18 months before bearings actually need to be replaced. Once a vibration sensor has identified changes in vibration patterns, teams can track the progression and choose the best time to replace the bearing.
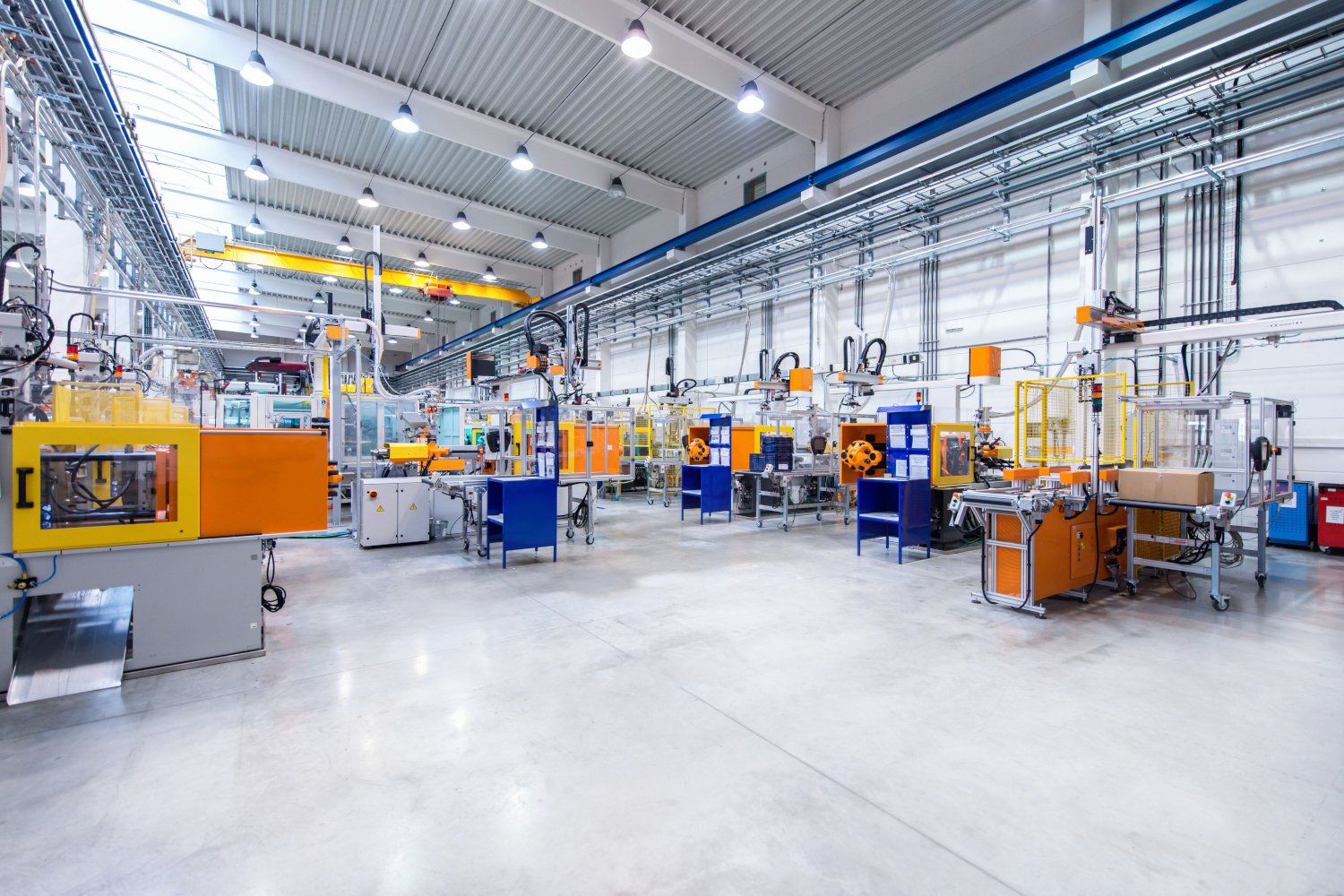
Why is vibration analysis important?
Vibration can prematurely wear components, shorten the life of equipment, create noise, and result in safety issues. Imbalance or misalignment in rotating assets may crack or break driveshafts and other components.
Analyzing vibration data enhances your maintenance and reliability program by providing insights that a surface-level look at vibration data can’t match. Spotting changes in vibration amplitude alone doesn’t uncover the whole picture. But the details of the time waveform shape can shed light on the root cause behind changes in vibration, for example. Historical data, collected and trended over time, makes it easy to pinpoint when a machine’s vibration falls outside the norm.
How does software pair with vibration sensors?
With Fluke’s eMaint Condition Monitoring software, maintenance teams can monitor the overall condition of their assets at a glance. Teams can be notified any time vibration measurements fall outside thresholds — or customize thresholds themselves.
With eMaint Condition Monitoring, vibration data can be visualized so staying updated at a glance is easy. Real-time asset vibration data helps maintenance teams be more efficient and effective, increasing asset reliability and extending peak performance.
Vibration measurement and analysis services to drive your condition monitoring strategy.
Our Expertise as a Service offering bolsters maintenance teams with assistance and training when they need it. Teams can take advantage of these services to launch condition monitoring programs that are ready for a future of IIoT. Among other things, our service offerings include:
- A wide range of remote and on-site setup services
- Vibration training covering the core principles of vibration, reading vibration data, and taking action based on vibration data
- Customized installation and training packages
Speak with a sales representative today to request your personalized consultation.
Get a free demoWhat are piezo vibration sensors?
Piezoelectricity has a wide variety of applications. Piezoelectric sensors, or piezo sensors, use the piezoelectric effect to detect changes in vibration, temperature, or other physical parameters. They are highly accurate and dependable, and they can withstand harsh environments.
How do piezoelectric vibration sensors work?
Vibration can be measured via the piezoelectric effect. The piezoelectric effect is the capability certain materials have to produce an electrical charge when experiencing applied mechanical stress. Piezoelectric sensors use these certain types of quartz or crystal. The charge they produce is directly proportional to the mechanical stress applied to them. The charge creates voltage which sends measurable electrical signals.
Related products
Benefit from remote condition monitoring sensors
Condition monitoring typically leverages remote, wireless sensor technologies, including condition monitoring and power monitoring: