In the industrial world, the evolution of machinery maintenance strategies from reactive 'run to failure' approaches to proactive and strategic methodologies has been monumental. This article delves into the realms of vibration monitoring and machine vibration analysis, elucidating their principles, applications, and the vibration analysis equipment that harnesses their potential.
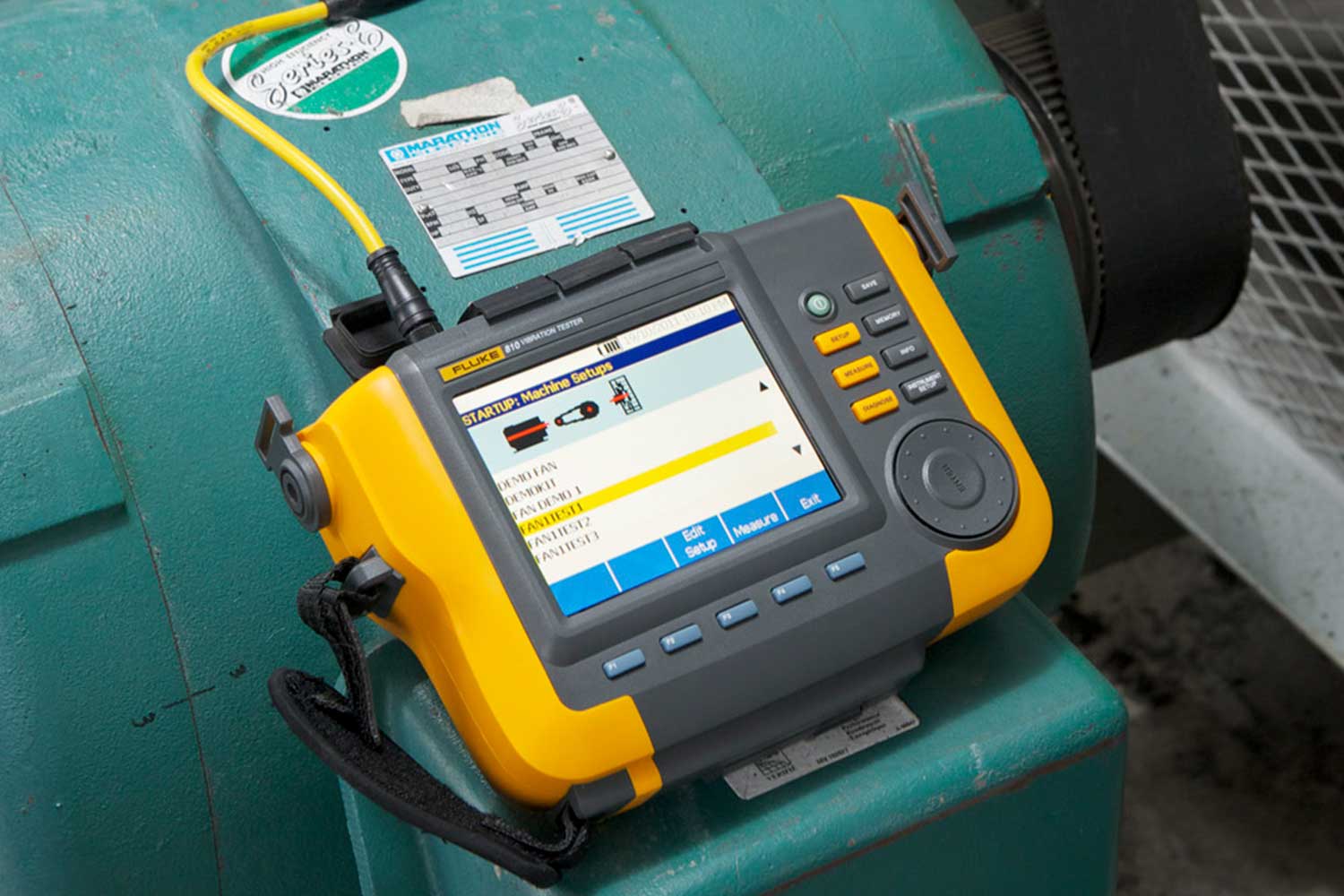
What is Vibration Analysis?
Vibration analysis, a linchpin of condition-based maintenance strategies, has been embraced by entities like the US Navy and various Fortune 500 companies over the past three decades. Moving away from traditional preventive maintenance, which operates on a calendar-based schedule and often leads to unnecessary repairs, condition-based maintenance relies on real-time data to make informed decisions. Vibration analysis is at the heart of this approach; it involves measuring and analyzing the vibrations of machinery to detect potential issues before they escalate into severe problems.
The Role of Vibration Monitoring in Machine Health
Vibration monitoring is a fundamental component of predictive maintenance strategies. It involves the continuous surveillance of machinery to identify changes in vibration patterns that may indicate mechanical wear or failure. Early detection through vibration monitoring and infrared thermography brings a host of benefits:
- Predictability: Enables maintenance staff to schedule repairs and procure necessary parts in advance.
- Safety: Proactively identifies and rectifies faults, averting potential hazards.
- Revenue Preservation: By minimizing unexpected failures, vibration monitoring helps in avoiding production halts, thereby protecting the bottom line.
- Maintenance Optimization: Extends the lifespan of equipment and aligns maintenance schedules more closely with actual needs.
- Reliability and Peace of Mind: Anticipates problems before they occur, enhancing the overall reliability of machinery and instilling confidence in maintenance schedules and budgeting.
Mechanics of Vibration Testing
The process of vibration testing is intricate yet fascinating. A transducer captures vibration signals from the machinery, particularly from bearing locations. These signals are a composite of various sources – the rotating shaft, adjacent machinery, structural resonances, and more. Deciphering these complex signals is a challenge that vibration analysis equipment, equipped with algorithms like the Fast Fourier Transform (FFT), is designed to meet. This transformation leads to a spectrum, which plots individual vibration signals against frequency, revealing the health and performance of the machinery.
The Three-Step Process of Machine Vibration Analysis
Machine vibration analysis can be distilled into a three-step process:- Identification: Recognize vibration peaks associated with specific components of the machine.
- Pattern Recognition: Analyze the data to identify patterns that adhere to known vibration rules.
- Amplitude Measurement: Assess the amplitude of the vibration peaks to gauge the severity of any detected fault.
Vibration Analysis Equipment and Vibration Monitoring Equipment
The transition from basic vibration pens to sophisticated meters and testers marks a significant advancement in vibration analysis technology. For instance, the Fluke 805 Vibration Meter not only measures overall vibration but also gauges specific variables. Its sensor tips, accommodating a broad frequency range, along with an intuitive interface, empower frontline maintenance personnel to effectively screen and diagnose machinery health.
The Fluke 810 Vibration Tester elevates the diagnostic process further. It amalgamates algorithmic prowess with a vast database of real-world measurement experience, offering a comprehensive diagnostic engine. This tool not only identifies faults but also categorizes the severity of the issues, guiding maintenance decisions efficiently. It stands as a testament to the sophistication and capability of modern vibration monitoring equipment.
Vibration monitoring and analysis emerge as critical components in the modern maintenance arsenal, transcending the limitations of 'run to failure' and preventive maintenance approaches. By offering deep insights into machinery health, enabling early detection of faults, and facilitating informed maintenance decisions, these approaches not only enhance the reliability and lifespan of machinery but also optimize operational efficiency and safety. With the advent of sophisticated tools like the Fluke Vibration Testers, the potential of vibration condition monitoring is more accessible and impactful than ever, paving the way for a new era of strategic, data-driven maintenance practices.