Day-one reliability
Closing the gap from the beginning at the new Dana Incorporated Driveline Toledo Plant
By Kevin Clark
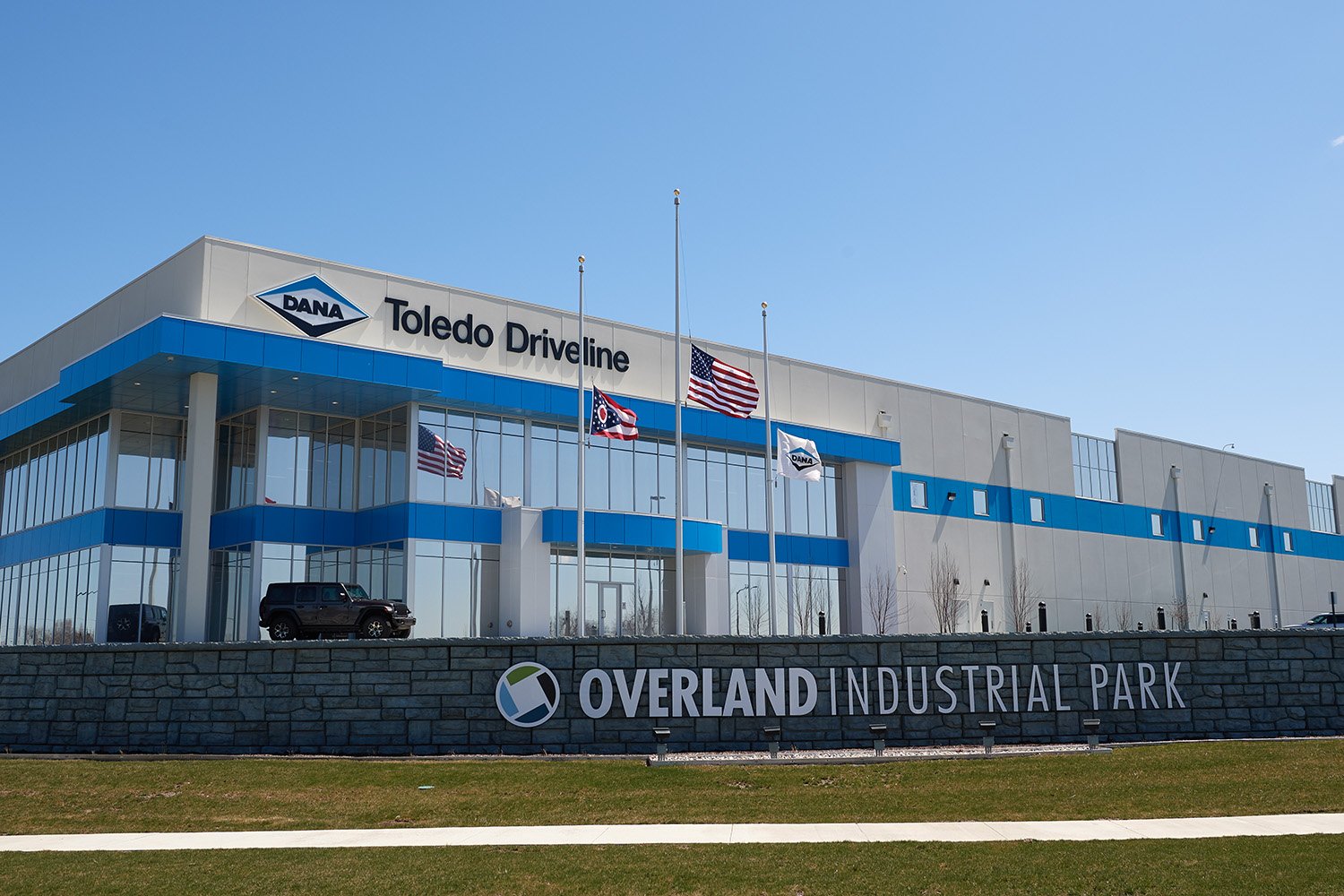
Imagine you've been given responsibility for keeping a new plant up and running and that you can add any maintenance and reliability technology you want to ensure it stays that way. What would you choose?
When Dana Inc. brought its new Dana Driveline Toledo plant online, the team recognized that they had an exceptional opportunity to stay ahead of equipment problems and failures. Already fitted with premier automation features and the eMaint computer maintenance management software (CMMS) system — also being used by 27 of its other facilities, the team knew that if they wanted to keep the reliability gap in check, they would need to add a maintenance and reliability system.
Dana Toledo Driveline is just one of Dana Inc.'s many divisions amid a network of nearly 100 engineering, manufacturing and distribution facilities in 34 countries on six continents. Dana Inc.'s driveline systems can be found in all types of wheeled vehicles, including Jeeps, commercial cars and large mining trucks. The Dana Toledo Driveline plant manufactures and assembles axles for the vehicles.
How to choose a reliability and maintenance system
Sometimes, the right solution just presents itself. That's what happened when a member of the Dana Inc.'s team attended an eMaint workshop and heard about the Fluke Accelix™ Connected Reliability Framework.
Already aware of the strong relationship with the eMaint 24/7 customer support team and the proven value of the software, the Dana Toledo Plant had every reason to believe the same strength would extend to the other offerings. Dana maintenance workers proposed the launch of a pilot project to test Accelix Accelix and its ability to integrate the Dana Driveline Toledo plant CMMS with the full suite of Fluke connected condition monitoring sensors and wireless handheld tools.
Dana Toledo managers and engineers reviewed information about Accelix and then began reaching out to Fluke to see about obtaining some of the equipment and getting it installed. The Dana Toledo plant is new, so it gave them the perfect opportunity to catch equipment baselines to use in their predictive maintenance journey.
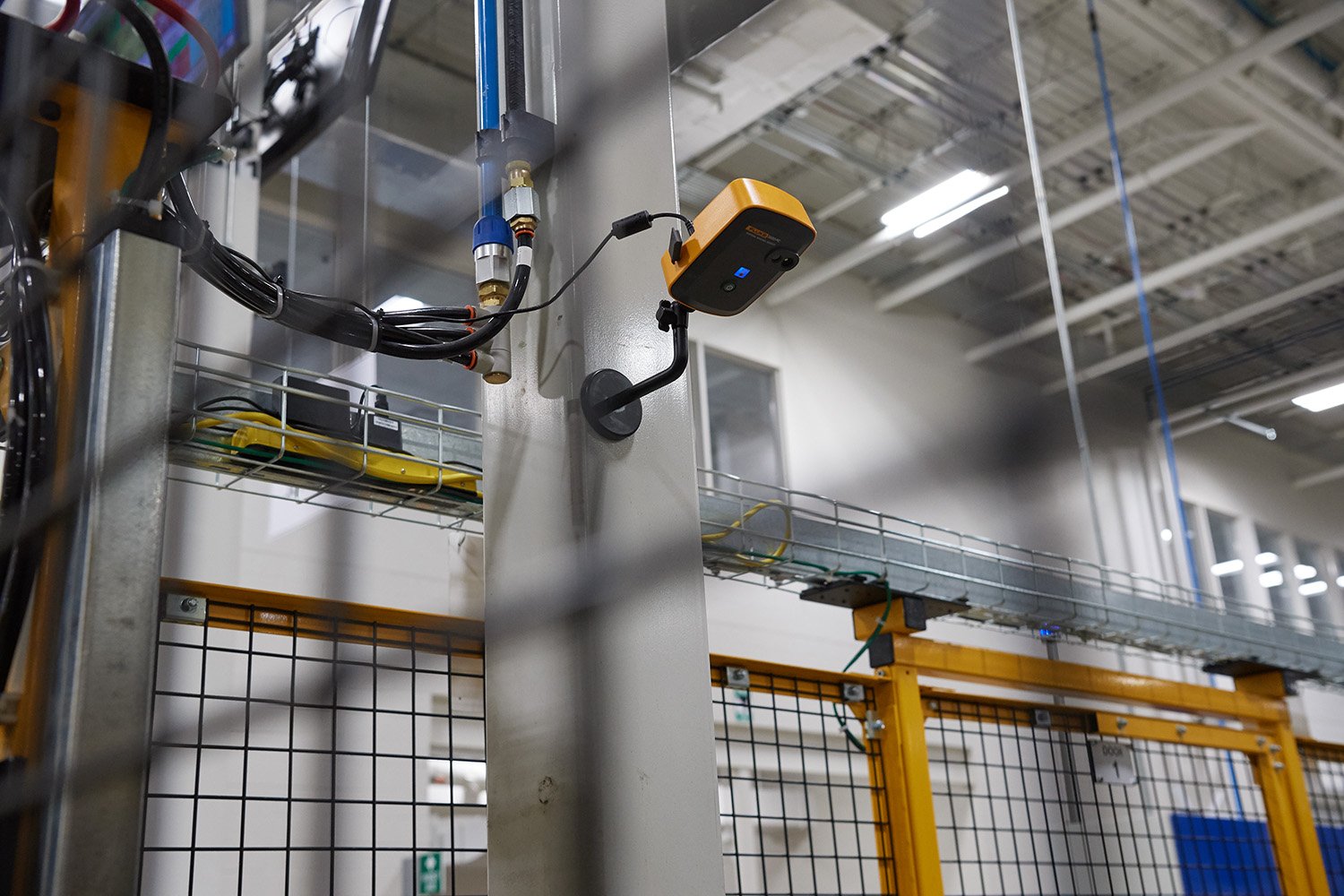
Thermal imaging sensors monitor assets without technician routes in the Dana facility.
By adding other components of the framework, the plant would gain the ability to continuously monitor equipment conditions and see real-time data to help them make immediate maintenance decisions using the baselines. As the system accumulated and stored data, analysts could then compare equipment problems with past performance and predict future behaviors.
"Our team worked very closely with Dana to look at their operations, understand at the genba (a place where value is created) what goes on at a plant," said Dave O'Reilly, president of Fluke Accelix. "We focused on the challenges they had in terms of data gathering and data integrity, and then we overlaid our solutions, our tools and our sensors, to plug that gap and provide that extra lift in terms of productivity and outcome."
Both the Dana team and the Accelix team had huge stakes in the journey. Specifically, if the pilot proved to be successful, Dana Inc. wanted to roll it out at their 60 other worldwide facilities within 2 to 3 years. But first, both teams needed to prove the concept.
"If Dana came to us and said, 'We want to monitor everything,' I think that would have really defeated the purpose," said lead application specialist Frederic Baudart, Fluke. "First of all, it would make the project way too big. To be successful, you really need to win small, first, then grow from there. Also, you really have to gain confidence from your own team, from yourself and from your leadership."
Asset protection
Before the teams could make decisions about where to collect data and whether to collect data from sensors or handheld tools, they first had to assess and rank the plant's most important equipment and create an asset criticality list.
"It's really about choosing the right measurement for the asset," said application specialist Alex Deselle, Accelix. "Making the choice between condition monitoring or route-based monitoring depends on the asset criticality ranking and what's best for the program."
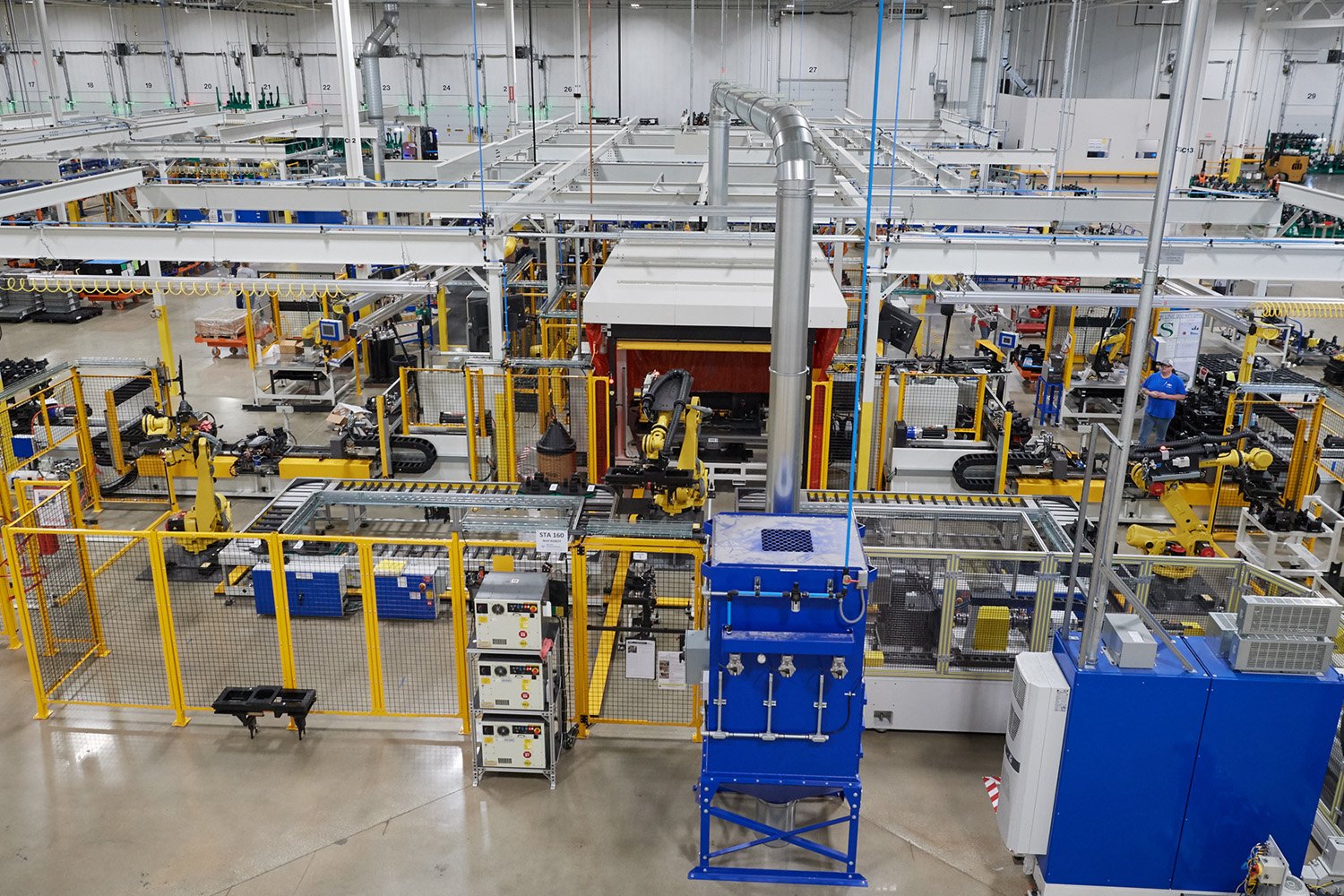
Real-time data that could be seen anywhere, any time.
"For instance, while taking a tour of the plant with the Dana team, we identified an important piece of machinery that needed to run continuously to test noise vibration harshness. If it failed, it could stop production. Knowing that made it easy to rank the criticality of that particular system — that machine."
Once the assets were ranked, the teams could then determine whether equipment needed 24/7 monitoring with sensors or if it would make more sense to schedule route-based monitoring using handheld tools, like thermal imagers and vibration meters.
"Criticality is generally a really easy conversation because everyone's goal is to get to a predictive state," said customer service manager Tara Crawford, eMaint. "Nobody wants to be running around in a reactive mode all the time. In our initial conversations we talk about critical assets — asset failures that could potentially put everyone on pause and create massive amounts of downtime."
New doesn’t mean perfect...yet
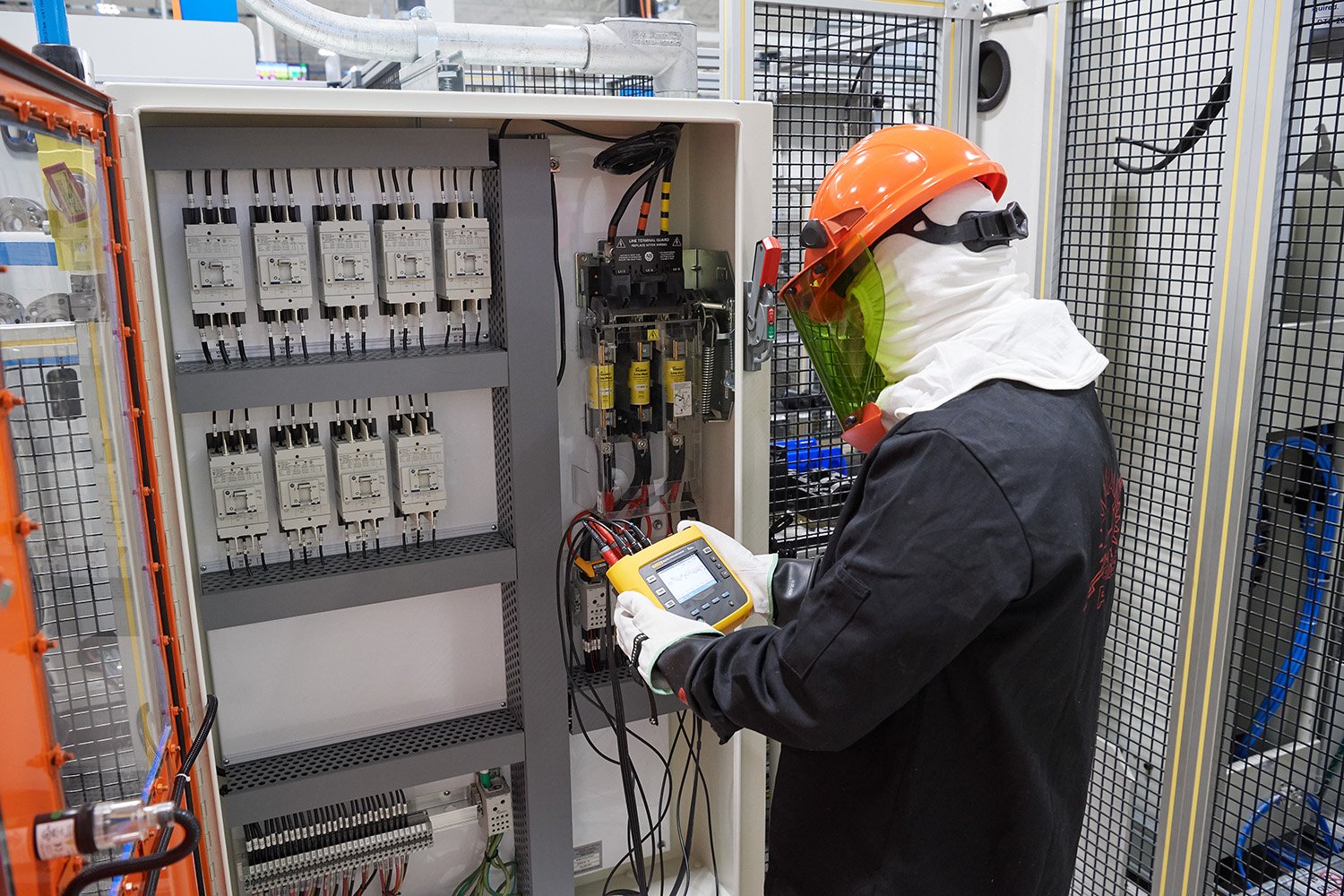
Dana technician sets up a power monitor within an electrical panel.
Shortly after implementing the maintenance and reliability system, Dana personnel began some initial condition-based monitoring of power. While doing so, they found some balance differences in the new equipment.
In Dana Toledo's center production line, there are two main electrical panels. The two power monitors installed on the main panels immediately found a problem. One of the three phases was unbalanced for one of the main panels. while it wasn't a big issues, it wasn't something they were aware of prior to installing the monitors.
Seeing the vision is believing the vision
For Dana Toledo Driveline's maintenance manager, what actually sold the system was the real-time data that could be seen anywhere, any time. With the ability to view the system in action via dashboards on a handheld tool screen and on the maintenance shop's TV monitors, managers and their teams could get ahead of equipment availability and potential failures, and ultimately increase throughput to the plant. The assets’ capacity to operate as designed could be assured.
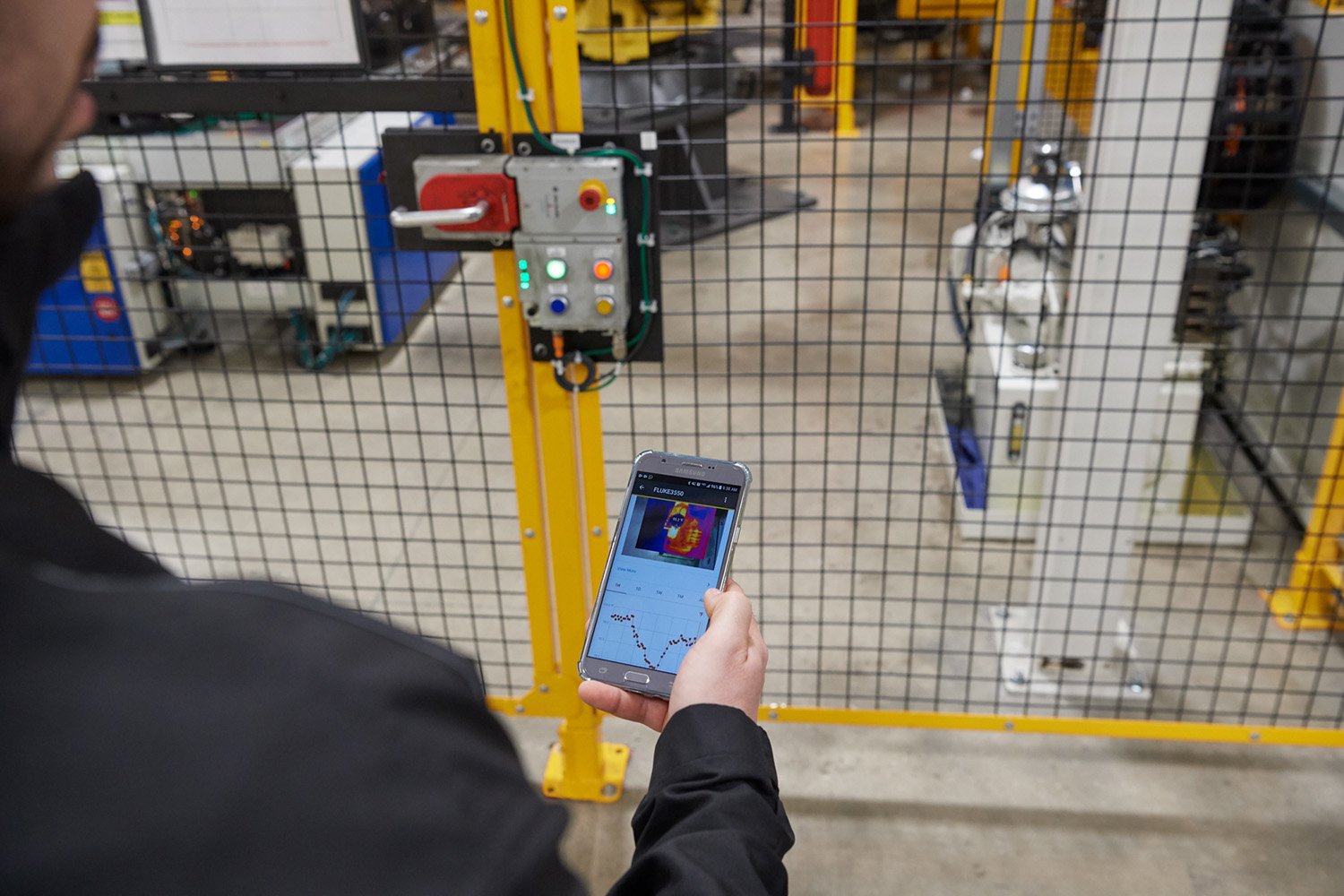
The team views up-to-date information on the dashboards displayed on the maintenance shop’s TV monitors.
For Dana Toledo's workers, seeing was believing. Now, they receive feedback from equipment in real-time, enabling them to increase the reliability of assets. Teams can visually walk through corrective and sustainment activities to make sure everyone is on the same page. It also helps them more effectively communicate complex ideals with less-technical people by visually representing data.
Think big, start small
When many companies start using a maintenance and reliability system, they want to begin by putting sensors on everything. The starting point for any company doesn't have to be big; you don't have to boil the ocean.
"In Dana's case, they started; they piloted; then they grew the pilot," said O'Reilly. "Having a true partnership between Dana and Fluke created by our joint vision and desired outcomes, helped us overcome any problems, together.
"What we did with Dana was help them start gathering data in context to a part of their environment, and then we allowed them to react. We learned what happens in their maintenance operations and then augmented those data sources, so that they could deliver a real result, rather than an imagined one. Regardless of where you are on the maintenance maturity curve, we have a solution where we can meet you at that point and join you on the rest of your journey."
To learn more, watch this video case study.