Vorgehensweise zum Messen der Ausgangsspannung von Frequenzumrichtern zum Motor
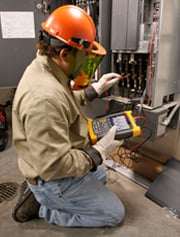
Bei der Fehlersuche bei elektrischen Signalen in einem Motor/Antriebssystem sollte man diese im Hinblick auf Eingang und Ausgang betrachten. Ein Antrieb mit variabler Frequenz, auch als Frequenzumrichter bezeichnet, wandelt die eingespeiste konstante Netzspannung- und -frequenz in einen Spannungs- und Frequenzbereich um, der variiert werden kann, um das Motordrehmoment zu regeln. Die Fehlersuche am Eingang beginnt mit der Prüfung der Netzstromversorgung und -qualität.
Die Fehlersuche am Ausgang beginnt mit der Messung der transformierten Spannung und Frequenz. In diesem Artikel wird die Messabfolge zur Beurteilung der Ausgangsleistungsfaktoren des Frequenzumrichters Schritt für Schritt beschrieben.
- DC-Zwischenkreis
- Ausgangsspannung/Strom/Frequenz
- Unsymmetrie
- Volt-Hertz-Verhältnis
- Reflexionen am Ausgang
In Abbildung 1 sind die Komponenten eines Eingangsumrichters (AC/DC-Umrichter) mit pulsbreitenmoduliertem Ausgangssignal dargestellt, mit einem Gleichspannungs-Zwischenkreis dazwischen. In einem Frequenzumrichter regelt der PWM-Umrichter (Pulse Width Modulation, Pulsbreitenmodulation) sowohl die Spannung als auch die Frequenz zum Motor. Spannung und Frequenz zum Motor werden durch eine Modulation der Pulsbreite der Ausgangsimpulse variiert, die über die Steuerung des Halbleiterschalters erfolgt.
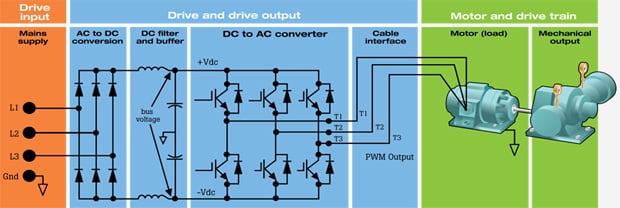
Die Eingangsdioden liefern einen konstanten Gleichstrompuffer für das Segment des Schaltwechselrichters, entsprechend dem 1,414-fachen des Spitzenwerts der Eingangsspannung. Der Kondensator fungiert als Filter, um die Welligkeit im Gleichstromabschnitt zu reduzieren.
Die Steuergeräte im Wechselrichterabschnitt sind in der Regel Bipolartransistoren mit isolierter Gate-Elektrode (IGBT) und haben heutzutage ausreichend Leistung, um Lasten bis zu 500 PS handhaben.
Schritt 1: Messen der Zwischenkreisspannung
Ein Oszilloskop kann verwendet werden, um den Absolutwert der gleichgerichteten Gleichspannung zu messen. Bei AC-Kopplung kann es auch verwendet werden, um durch eine Vergrößerung der Signalanzeige den Umfang der Welligkeit zu ermitteln (siehe Abb. 2).
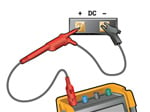
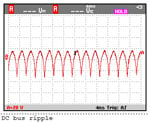
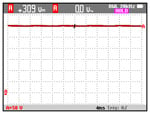
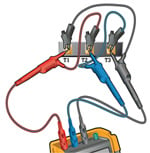
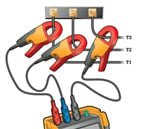
- DC-Busspannung mithilfe eines Oszilloskops oder Digitalmultimeters über die +- und --Anschlüsse messen.
- AC- oder DC-Eingangskopplung verwenden, um die Absolut- oder Brummspannung zu messen.
- Sicherstellen, dass Oszilloskop und Messfühler für die Messung des Spannungspegels angemessen spezifiziert sind.
Interpretieren von Gleichspannungsmessungen im Zwischenkreis
Die Zwischenkreisspannung steht in einem bestimmten Verhältnis zum Spitzenwert der Versorgungsspannung.
- Die Zwischenkreisspannung beträgt etwa das 1,414-fache des Effektivwerts der Netzspannung. Bei einem Antrieb, der mit 480 V Wechselspannung versorgt wird, sollte die Zwischenkreisspannung etwa ~678 V Gleichspannung betragen.
- Ein zu niedriger Gleichspannungswert kann dazu führen, dass der Antrieb ausschaltet. Wahrscheinlich ist die Netzeingangsspannung zu niedrig oder die Sinuswelle der Eingangsspannung könnte verzerrt oder abgeflacht sein.
- Wenn die Spitzenwerte der Welligkeit eine unterschiedliche Wiederholungsrate haben, liegt möglicherweise eine Fehlfunktion an einer der Gleichrichterdioden vor (lastabhängig). Welligkeiten der Spannungen über 40 V können durch defekte Kondensatoren oder eine für den angeschlossenen Motor und die angeschlossene Last zu geringe Antriebsleistung verursacht werden (siehe Abb. 3).
Schritt 2: Messen von Spannung und Unsymmetrie
- Ein Oszilloskop mit einer V-PWM-Funktion verwenden, das mit den drei Motorklemmen verbunden wird (siehe Abb. 4).
- Die Messwerte des Oszilloskops mit den Werten auf dem Antriebsdisplay vergleichen.
- Der Spannungsabfall zwischen Antrieb und Motorklemmen sollte bei maximal 3 % liegen.
- Eine Unsymmetrie von über 2 % ist problematisch.
- Prüfen Sie die Unsymmetrie der Motorspannung mit einem Mehrkanal-Oszilloskop an den drei Ausgangsphasen.
- Die Spannung an jedem Anschluss messen und jede gemessene Spannung aufzeichnen, um sie im nächsten Schritt zu verwenden.
- Die Spannungsunsymmetrie bei Volllast messen.
Schritt 3: Messen von Stromunsymmetrie
Messen Sie mit einem Oszilloskop mit jeweils einer Stromzange an allen drei Ausgangsanschlüssen des Antriebs die Stromaufnahme an jedem Anschluss (siehe Abb. 5).
Da die Strommessung in einem energiereichen Umfeld mit elektromagnetischen Störungen erfolgt, stellen Sie sicher, dass Sie Stromzangen verwenden, die eine hohe Störstrahlungsfestigkeit haben. Wenn bei Ihrer Messeinrichtung die Unsymmetrie nicht automatisch bewertet wird, siehe „Unsymmetrie manuell berechnen“.
Die Unsymmetrie sollte nicht größer als 10 % sein.
- Je einem Prozent Spannungsunsymmetrie beträgt die Stromunsymmetrie im Motor zwischen 3 % bis 4 %.
- Wenn die Spannungsunsymmetrie gering ist, ist eine zu große Stromunsymmetrie unter Umständen ein Hinweis auf kurzgeschlossene Motorwicklungen oder auf den Masseschluss einer der Phasen.
- Bei Dreiphasen-Motoren sollte die Stromunsymmetrie nicht größer als 10% sein.
- Eine Spannungsunsymmetrie bewirkt eine Stromunsymmetrie.
- Wenn die Spannungsunsymmetrie innerhalb akzeptabler Grenzen liegt, ist eine zu große Stromunsymmetrie unter Umständen ein Hinweis auf kurzgeschlossene Motorwicklungen oder auf den Masseschluss einer der Phasen.
Schritt 4: Volt-Hertz-Verhältnis
Das Verhältnis von Spannung zu Frequenz (U/f-Kennlinie oder Volt-Hertz-Verhältnis) bestimmt die Größe des von einem Wechselstrom-Asynchronmotor erzeugten Drehmoments. Wenn dieses Verhältnis konstant gehalten wird, wird auch das Magnetfeld im Motorinneren konstant gehalten. Die Folge ist ein konstantes Drehmoment.
Oberhalb der Nennfrequenz von 60 Hz nimmt die Spannung nicht mehr zu, während das Drehmoment abnimmt (siehe Abb. 6).
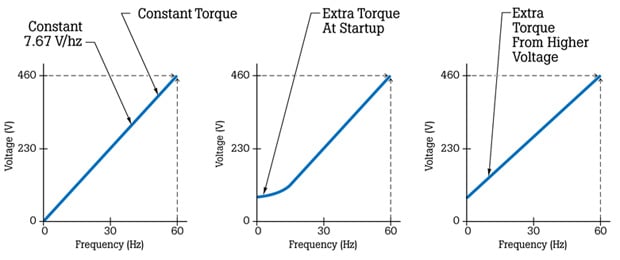
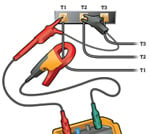
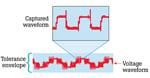
Zur Messung des Volt-Hertz-Verhältnisses wird ein Digitalmultimeter mit einer V-PWM-Option (wobei V PWM die Amplitude der Grundfrequenz widerspiegelt) oder ein Oszilloskop verwendet. Auf dem Oszilloskop sollte gleichzeitig die Frequenz des PWM-Ausgangs und eine Spannung im Bereich der Spezifikation auf dem Motor-Typenschild angezeigt werden (siehe Abb. 7).
Zur Messung der Frequenz wird eine Stromzange verwendet. Die Frequenz sollte bei ~7,6 für einen 460-V-Motor und bei ~3,8 für einen 230-V-Motor liegen.
Schritt 5: Reflexionen am Ausgang
Reflexionen treten als Folge einer Impedanz-Fehlanpassung oder einer Änderung des Stromübertragungswegs auf (siehe Abb. 8). In einem Motorantriebsschaltkreis kann die Spitzenspannung der Reflexion ebenso hoch sein wie die Zwischenkreisspannung.
Um dies mit einer Analogie zu beschreiben: Überlegen Sie, was mit einem Rasensprenger geschieht, wenn der Wasserfluss kurzfristig dadurch verändert wird, dass jemand auf den Wasserschlauch tritt. Der Druck im Sprinklerkopf ändert sich und nimmt einen Spitzenwert an, wenn der aufgebaute Druck freigegeben wird. Die Verwendung eines übermäßig langen Kabels (>30 Meter) kann ebenfalls zu Reflexionen über die Länge hinweg führen, die als Transienten messbar sind.
Die Reflexion selbst zeigt sich als Spitzen auf einem Oszilloskop-Display in einem breiten Bereich von Signalen, Amplituden und Dauer. Als Faustregel gilt, dass Reflexionen oder Transienten >50 % der Nennspannung problematisch sind.
Eine mögliche Lösung besteht darin, die Leiter zwischen dem Motor und dem Wechselrichter zu kürzen. Eine weitere Lösung ist es, die Kabelqualität zu erhöhen und damit die Impedanz reduzieren oder zu lastgeeigneten Wechselrichter-Motoren mit einem höheren Isolationswert von 1.600 V oder mehr zu wechseln, die den Transienten standhalten können.
Die meisten Reflexionen werden durch schnelles Schalten der Gleichspannung durch den IGBT (dV/dt) verursacht. Ein IGBT arbeitet in einem Antrieb ähnlich einem sehr schnellen Ein-/Aus-Schalter. Der IGBT gibt eine Gleichspannung als pulsbreitenmoduliertes Signal (PWM) auf einer induktiven Last aus. Dadurch werden über eine sehr kurze (Schalt-)Zeit hohe induktive Spannungsanstiege erzeugt, die auch als dV/dt bezeichnet werden.
In den IGBT ist eine Freilaufdiode integriert, um dies zu kompensieren. Es sind jedoch Transienten sichtbar, wenn die Einstellung „Glitch-Erkennung“ des Oszilloskops aktiviert ist.
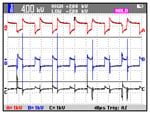
Messen und Interpretieren von Reflexionen am Ausgang
Die Abtastrate und Frequenz-Bandbreite der meisten Digitalmultimeter reicht nicht aus, um kurze, schnelle Ausgangstransienten zu erkennen. Aus diesem Grund wird ein an die Motorklemmen angeschlossenes Oszilloskop verwendet, wie in Abb. 3 dargestellt. Das Eingangssignal B in Abb. 9 zeigt, wie übermäßige Reflexionen in der Signalansicht erscheinen. Zu wissen, wie eine bestimmte Verzerrung aussieht, kann dazu beitragen, dass die Grundursache schneller ermittelt wird.
Fazit
Die Bestimmung der Grundursache für Defekte des Motorantriebssystems erfordert systematisch ausgeführte Leistungstests und Messungen an System-Schlüsselstellen. Insbesondere im Hinblick auf die Stromversorgung muss zwischen Stromeingang und -ausgang differenziert werden, auf die jeweils sowohl unterschiedliche Messtechniken als auch Bewertungskriterien anzuwenden sind. Mit etwas Kenntnis können diese Messungen dann als Orientierung bei der Fehlersuche zur Bestimmung der eigentlichen Grundursache genutzt werden, sodass das System schnellstmöglich wieder einsatzfähig ist.