Spannungsmanagement bei Frequenzumrichtern mit einem Wellenerdungssatz
Die Zugewinne bei der Motorsteuerung und beim Systemwirkungsgrad, die durch Frequenzumrichter ermöglicht wurden, haben dazu geführt, dass diese Geräte in modernen Gebäudesteuerungs- und Fertigungssystemen nahezu universell eingesetzt werden.
„Frequenzumrichtergesteuerte Motoren sind eine Standardoption in nahezu allen neuen Anlagen heute, und damit so gut wie überall zu finden“, so Dave Williams, Leiter der technischen Dienste für McKinstry, einem großen Unternehmen für Beratungs-, Bau-, Energie- und Gebäudedienstleistungen mit Sitz in Seattle. „Frequenzumrichter sind auch eine gute Nachrüstungsoption für unsere Kunden, und wenn wir uns um die Instandhaltung von Motoren kümmern, die nicht durch Frequenzumrichter gesteuert werden, empfehlen wir, dass diese installiert werden. Frequenzumrichter erlauben es uns, die Motorleistung effizient in einer Weise auf eine Last abzustimmen, wie dies früher nicht möglich war, und können unseren Kunden beträchtliche Energieeinsparungen ermöglichen.“
Durch die Steuerung von Drehzahl und Leistung eines elektrischen Induktionsmotors passt ein Frequenzumrichter die Leistung der betriebenen Geräte (z. B. Pumpen und Lüfter) präzise an die wechselnden Anforderungen an, und dies ohne die Komplikationen von Ventilen, Riemen, Lüftungsschlitzen und anderen mechanischen Steuergeräten, die von Anlagen alten Stils benötigt werden. Aber ein Kompromiss muss gemacht werden.
Herausforderung: Wellenspannungen
„Wir haben uns auf die Instandhaltung von Gebäuden und der baulichen Umgebung mittels Wartungsverträgen spezialisiert, die wir Interessenten anbieten“, erklärt Williams. „Wir haben eine Reihe von Instandhaltungsplanoptionen im Angebot, von vierteljährlichen Inspektionen bis zur Inspektion einmal pro Jahr. Wir sehen uns die Anlagen regelmäßig an, erfassen Messdaten und dokumentieren die Geräteparameter. Wir sind für die Instandhaltung einer Reihe kritischer Umgebungen zuständig, beispielsweise Rechenzentren und Fertigungsanlagen, und in diesen Umgebungen achten wir sehr genau auf den Motorbetrieb. Das tun wir unter anderem durch die Messung von Wellenspannungen.“
Ein Frequenzumrichter wandelt den eingehenden dreiphasigen Netzstrom in Gleichstrom um und erzeugt dann aus diesem Gleichstrom einen synthetischen dreiphasigen Sinuswellenausgang. Die Frequenz dieses Ausgangs kann angepasst oder variiert werden, um die Motordrehzahl und -leistung zu steuern.
„Der normale Wechselstrom, der an einen Wechselstrommotor geliefert wird, ist phasensymmetrisch“, so Williams. „Wenn Wechselstrom jedoch durch einen Frequenzumrichter geleitet wird, ist der Strom nicht mehr symmetrisch und aufgrund der schnellen Schaltfrequenzen, die von Wechselrichtern mit Pulsbreitenmodulation (PWM) verwendet werden, wird eine Spannung an der Motorwelle induziert. Das bedeutet, dass sich diese Spannung aufbaut und nach einem Erdungspfad sucht. Wenn die Motorwelle nicht geerdet ist, führt der Weg des geringsten Widerstands häufig durch die Motorlager.“
Auch wenn das Motorgehäuse geerdet ist, ist es die Welle häufig nicht. Unter diesen Umständen baut sich die Eingangsspannung an der Welle weiter auf, bis sie einen Spannungspegel erreicht, der hoch genug ist, um einen Lichtbogen über die Motorlager zum Motorgehäuse und zur Masse zu bilden. „Wenn die Spannung einen Lichtbogen über die Motorlager bildet, versagt die Lagerschmierung und Rollenlager werden beschädigt.“
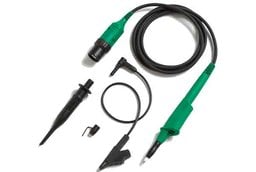
Lager schützen
Bei Motoren, die von den für PWM-Wechselrichter typischen schnellen Schaltfrequenzen angetrieben werden, kann es zu Wellenspannungen von bis zu 70 Volt oder mehr kommen. Solche Spannungen können die Isolationseigenschaften von Lagerschmierstoffen überwinden. Wenn die resultierenden Lichtbogen über ein Lager laufen, kann dies Lochfraß, Riffelungen, Schmelzkrater und letztendlich ein vorzeitiges Lagerversagen zur Folge haben. „Dieses Problem tritt häufig auf“, erklärt Williams, „und jeder frequenzumrichtergesteuerte Motor ist anfällig dafür.“
Einen gewissen Schutz bieten eine Vielzahl von Wellenerdungssätzen, die Nanogap-Technologie in Kontakt-/Nicht-Kontaktausführung und eine Ableitung der Wellenspannung kombinieren.
Ein Motorausfall in einer kritischen Anlage, beispielsweise einem Rechenzentrum, einer Fertigungsstraße oder einem Gebäudesteuerungssystem, ist störend und teuer. Daher umfassen die Programme der vorbeugenden Instandhaltung von McKinstry seit langem die Analyse von Motorlagern.
„Es gibt viele Gründe für das Lagerschäden“, sagt Williams. „Lagerschäden können durch verschmutzte Schmierstoffe, Korrosion, Mangel an Schmierung, Überschmierung, übermäßige Motorbelastung und viele andere Gründe ausgelöst werden. Aber was für uns bis zum tatsächlichen Eintreten des Schadens schwierig zu diagnostizieren war, waren Schäden aufgrund von Wellenspannungen.“
Neue Einblicke
Heute ist dieses Problem gelöst. McKinstry misst Motorwellenspannungen mithilfe eines speziellen Wellen-Tastkopfs und dem Fluke ScopeMeter® der Serie 190 II, einem tragbaren Vierkanal-Oszilloskop, das es ermöglicht, Wellenspannungsprobleme zu erkennen und zu überprüfen, ob das Problem nach einer ordnungsgemäßen Erdung der Wellen beseitigt ist. Das Verfahren wird möglicherweise ein Standardelement des vorbeugenden Instandhaltungsprozesses.
„Neben der Lagerprüfung“, sagt Williams, „und wahrscheinlich als Frühindikator für den Zustand des Lagers wäre dies eine vorläufige Prüfung, die wir für unsere Kunden nutzen würden und die eine ausgezeichnete Informationsgrundlage für uns liefern würde.
„Dies wäre tatsächlich bei jedem Kunden anwendbar, aber insbesondere bei neuen Kunden und bei Standorten mit kritischen Anwendungen würden wir Wellenströme und -spannungen prüfen, um festzustellen, welche Auswirkungen die Wellenspannungen auf den Motorbetrieb haben.“
Einfache Einrichtung
Williams erklärt, dass die Einrichtung für die Prüfung einfach ist. Der Techniker benötigen nur eine kurze grundlegende Einführung. „15 bis 20 Minuten, und sie können loslegen“, so Williams.
In vielen Prüfungssituationen müssen die Systeme vorübergehend abgeschaltet werden, um Gefahren von beweglichen Teilen oder stromführenden Schaltungen zu beseitigen. Der Techniker verwendet dann einen Magnetfuß, um einen Mikrofaser-Tastkopf in Kontakt mit der Motorwelle zu bringen. Wenn ein solches Vorgehen sicher ist und die Zugangsmöglichkeiten es erlauben, kann der Tastkopf in der Hand gehalten werden. Ein zweiter Tastkopf wird in Kontakt mit dem Motorgehäuse gebracht. Das Gerät wird dann wie normal betrieben und die im ScopeMeter aufgezeichneten Messwerte zeigen das Wellenspannungssignal an.
Die Ergebnisse können erhebliche Auswirkungen zeigen, ebenso wie der Unterschied, nachdem die Welle mit einer Manschette, die für diesen Zweck entwickelt wurde, ordnungsgemäß geerdet wurde (siehe Abb. 1 und 2).
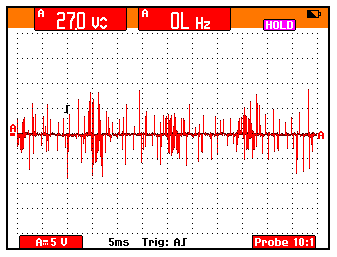
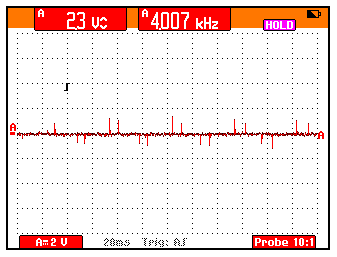
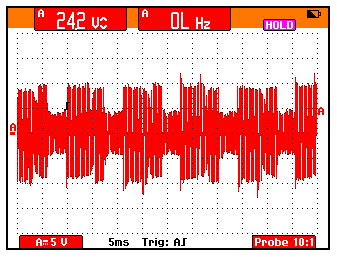
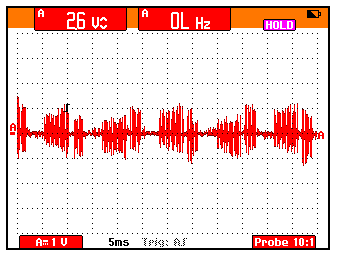
„Ich glaube nicht, dass wir einen Grenzwert festgelegt haben“, so Williams. „Einige der Spannungswerte, die wir gemessen haben, liegen im Zehnerbereich und höher. Das bedeutet sicherlich, dass Spannung durch die Welle läuft. Bei Motoren, bei denen wir das Problem beseitigt haben, ist der Wert in der Regel nahe null.“
Überzeugen Sie sich selbst!
„Wir haben einen sogenannten Wellenerdungssatz installiert“, sagt Williams. „Er besteht aus einer Art Kohle-Element, entweder einer Bürste oder einem harten Kohle-Element, das auf der Welle liegt und daher die Spannung erdet – auf dem Weg des geringsten Widerstands durch den Wellenerdungssatz, statt durch die Lager.“ Einige Sätze werden an derAntriebsseite des Motors installiert, während andere an der Nicht-Antriebsseite installiert werden. Die Kosten für solche Sätze können bei 400 bis 500 $ pro Installation liegen, erklärt Williams.
Ist es schwer, Kunden davon zu überzeugen, Geld für eine solche Lösung zu bezahlen?
„Nicht bei Kunden mit kritischen Umgebungen“, mein Williams, „denn das sind Techniker, die technische Probleme verstehen. Sie haben von dem Problem gehört und es verstanden. Und wenn sie das Diagramm sehen, wird es ihnen wirklich bewusst. Entscheidend ist, dass wir das Problem zeigen können.“
Auch nachdem der Verkauf abgeschlossen und der Erdungssatz installiert ist, plant Williams regelmäßige Folgeprüfungen, um sicherzustellen, dass das Problem weiterhin behoben bleibt.
„Jedes mechanische System fällt letztendlich aus“, sagt er. „Daher erfassen wir weiterhin Messwerte. Das muss nicht unbedingt vierteljährlich sein, wie wir unsere Instandhaltungsprüfungen durchführen, sondern möglicherweise reicht ein jährlicher Rhythmus aus, um sicherzustellen, dass das System weiterhin arbeitet. Das ist abhängig vom Schutzgrad, den der Kunde wünscht und braucht.“
Höheres Serviceniveau
Für Kunden mit kritischen Anlagen, beispielsweise mit Rechenzentren, die Geräte und Daten mit Millionenwert beherbergen, hat sich ein Schutz höchster Klasse als wertvoll erwiesen.
„Unsere Mitarbeiter haben das Messgerät eingesetzt, und die Ergebnisse waren beeindruckend“, sagt Williams. „Sie haben Transientenspannungen in vielen der Motoren in den von uns gewarteten Rechenzentren gefunden, und das hat den Kunden die Augen geöffnet. Damit können wir ein höheres Serviceniveau und mehr Schutz für unsere Kunden bieten und Informationen in einem Umfang wie nie zuvor erlangen.
„Ein Grund, aus dem wir wirklich begeistert von der Technologie sind, besteht darin, dass wir durch sie unserer Meinung nach die Fähigkeit bekommen, unseren Kunden in Bezug auf den Motorbetrieb einen echten Mehrwert zu bieten“, ergänzt er. „Wir können Probleme sehen, bevor der Schaden eintritt, und das ist entscheidend. Damit werden Stillstandszeiten für den Kunden vermieden. Das ist Gold wert.“
Über McKinstry
Das Unternehmen McKinstry, 1960 gegründet, bietet umfassende Dienstleistungen in Bereich Planung, Bau, Betrieb und Instandhaltung an (Design, Build, Operate, Maintain, kurz DBOM). Es beschäftigt über 1.600 Mitarbeiter und hat einen Jahresumsatz von etwa 400 Mio. USD. Das Fachpersonal und die Verkäufer von McKinstry erbringen Beratungs-, Bau-, Energie- und Gebäudedienstleistungen an. Nachdem das Unternehmen bereits frühzeitig den DBOM-Prozess übernommen hat, berät es seine Kunden dabei, auf die Zusammenarbeit ausgerichtete, nachhaltige Lösungen zu finden, die im Hinblick auf den Komfort der Bewohner, die Verbesserung der Systemeffizienz, die Reduzierung der Betriebskosten von Gebäuden und letztlich die Optimierung der Kundenprofitabilität für die Lebensdauer ihres Gebäudes gestaltet sind.