In den letzten 45 Jahren hat die Linamar Corporation, mit Hauptsitz in Guelph, Ontario, in Kanada sich weltweit einen wohlverdienten Ruf als erstklassiger Designer und Hersteller von verschiedenartigen Edelmetallkomponenten und Systemen für die Automobil- und Energiebranchen und den Markt für mobile industrielle Anwendungen verschafft.
Anfang 2011 wurde der Bereich Advanced Systems Group (ASG) des Unternehmens von der Linamar Camtac Manufacturing Group hinsichtlich eines wiederholt auftretenden Problems mit seinen Kompressormotoren kontaktiert. Die Motoren an jedem der drei 300-PS-Luftkompressoren des Werks an einem bestimmten Punkt schienen in den vorausgehenden drei oder vier Jahren ausgefallen zu sein. Die Motoren waren relativ neu – sie waren erst bei der Eröffnung des Werks 2002 in Betrieb genommen worden. Sie waren alle regelmäßig gewartet worden, sodass der Ausfall von auch nur einem Motor bereits ungewöhnlich wäre, geschweige denn von allen drei Motoren innerhalb von so kurzer Zeit. „Ein Ausfall ist ein Zufall, zwei Ausfälle sind eine Koinzidenz, aber beim dritten Ausfall überlegt man sich, dass hier etwas anderes im Gang sein muss“, sagt Leigh Copp, leitender Ingenieur und Geschäftsbereichsleiter der Linamar Advanced Systems Group.
Die Kosten für die Neuwicklung der Motoren liegen im Durchschnitt zwischen 6.000 und 8.000 $ pro Motor. Hinzu kommen die Kosten für Stillstandszeiten. „Wenn das Werk zwei ungeplante Stillstandszeiten bewältigen muss, weil ein Motor ausgetauscht werden muss, kann das leicht einen Verlust von Zehn- oder Hunderttausenden von Dollar in einer Schicht bedeuten“, fügt Copp hinzu.
Zu den Kosten hinzu kommt, dass ein plötzlicher Kompressorausfall ansteckend sein kann. Die daraus folgenden niedrigen Luftdruckzustände können zum Ausfall weiterer Maschinen im Werk führen. „In einem typischen Werk müssen drei Dinge laufen: Strom, Druckluft und Kühlwasser“, sagt Copp. „Wenn eine dieser Komponenten ausfällt, muss man alles herunterfahren und das kann sehr teuer werden.“
Linamar hatte Glück. Da die Motoren zu unterschiedlichen Zeitpunkten ausfielen, konnte das Wartungsteam die Reparaturen durchführen. Aber beim Ausfall des dritten Motors wendete sich Camtac an ASG und bat um Hilfe bei der Ermittlung des Problems. ASG ist für die Aufsicht und Fehlersuche bei besonders komplexen Problemen in den 25 Werken des Unternehmens im Bereich von Guelph zuständig, ebenso wie für Probleme in den Werken in den USA, Mexiko, Deutschland, Ungarn, Frankreich und China.
Den Spuren nachgehen

Foto mit freundlicher Genehmigung der Linamar Corporation
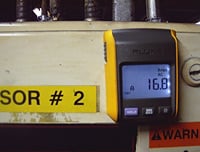
Foto mit freundlicher Genehmigung der Linamar Corporation
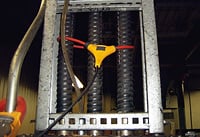
Foto mit freundlicher Genehmigung der Linamar Corporation
Der Strom gelangt über einen 5.000-kVA-Transformator in das Camtac-Werk, der eine Einspeisung von 5.000 A, 600 V liefert. Von dort aus werden 1.200-A-Unterversorgungsleitungen durch das Werk geführt, einschließlich einer Leitung, die die drei betroffenen Kompressoren versorgt. Im Kabelträger für die Unterversorgungsleitung laufen zwei parallele einadrige Kabel für jede der drei Phasen und ein Erdungsleiter in der Mitte des Kabelträgers.
Copp und sein Team begannen mit der Untersuchung an den Kompressormotoren, wo sie mit einer Strommesszange Fluke 381 mit einer iFlex™-Sonde Spannungen und Stromstärken maßen. „Wir haben eine sehr kleine Unsymmetrie – vielleicht 1 bis 2 Prozent – bei der Motorspannung festgestellt, jedoch eine Unsymmetrie von nahezu 10 % beim Motorstrom, was eine beträchtliche Überhitzung verursachen könnte“, sagt Copp.
Die Techniker waren etwas verblüfft, weil in der Regel eine Spannungsunsymmetrie von 1 % nicht zu einer Stromunsymmetrie von 10 % führt. Sie führten eine Messung der Spannung an der Einspeisung der Energieversorgung durch und stellten fest, dass sie sehr symmetrisch war – die 1 oder 2 Prozent Unsymmetrie in der Unterversorgung waren bei der Einspeisung der Energieversorgung nicht vorhanden. Sie prüften weiter mit der Netzqualitätsmesszange Fluke 345 , um nach Oberschwingungen im Motorstrom zu suchen, fanden jedoch nur einen sehr geringen Klirrfaktor. Sie prüften auch die Isolierung des Kompressormotors mit dem digitalen Isolationsmessgerät Fluke 1550B und konnten keine Verschlechterung oder sonstige Probleme der Isolierung feststellen.
Anschließend verglichen Sie die neu gewickelten Motoren mit den in Betrieb befindlichen Motoren und stellten fest, dass der Phase-zu-Phase-Widerstand bei den neuen Motoren deutlich ausgeglichener war. Das führte sie zu der Überzeugung, dass die in Betrieb befindlichen Motoren irgendeiner Art von Überhitzungseffekt ausgesetzt waren, der die Wicklungen beschädigte.
Erkennen eines hohen Erdstroms
Als die Motoren von der Unterversorgung getrennt wurden, stellte das Team fest, dass ein sehr hoher Erdstrom – etwa 160 A – im Ausgleichsleiter zwischen der 1.200-A-Unterversorgung und der Einspeisung der Energieversorgung floss. „Obwohl 160 A zulässig sind, sollte kein Erdstrom fließen, solange kein Leck vorhanden ist“, sagt Copp.
Das Team prüfte dann, dass der Neutral-Anschluss fest verbunden war und dass alle Erdungsdrähte in gutem Zustand waren. Auch das Erdungsmessgerät Fluke 1625 GEO wurde eingesetzt, um zu überprüfen, ob das Erdungsraster vorhanden war und ordnungsgemäß funktioniert.
Als jedoch mit der Strommesszange Fluke 381 die Erdströme gemessen wurde, die von jedem der Luftkompressoren durch die Kabelträger und durch die Luftleitung aus Metall flossen, gab es weitere schlechte Nachrichten. „Diese Messungen zeigten mehrere Erdungspfade mit einer beträchtlichen Menge an Strom, die aus jedem Kompressor floss“, sagt Copp. „Wir haben ein Fluke ScopeMeter® 190-204 mit vier Rogowski-Spulen als Stromwandler verwendet, um die Größe und Phase der Komponenten der Erdströme zu messen, die in die Leiter und den angrenzenden Kabelträger flossen. Es wurde klar, dass einige induktive Effekte zum Erdstrom beitrugen und dass diese Ströme zur Spannungsunsymmetrie an der Unterversorgung beitragen könnten.“
Die Messungen an der Einspeisung der Energieversorgung zeigten, dass nahezu 200 A Erdstrom durch die verschiedenen Erdungsleitungen dort floss. An diesem Punkt konnten sie bis zur nächsten geplanten Abschaltung der Anlage nicht weitergehen. In der Zwischenzeit verbrachten Copp und zwei weitere Ingenieure viel Zeit damit, Szenarien auf Whiteboards zu zeichnen und zu analysieren, woher der Strom möglicherweise kommen konnte. Sie vermuteten, dass eine Erdschleife vorhanden war, in die der Erdstrom durch Phasenströme induziert wurde.
Prüfung der vermuteten Ursache
Ende Dezember 2011 nutzten Copp und sein Team eine achtstündige Abschaltung im Camtac-Werk, um so viele statische Prüfungen wie möglich zur Aufspürung des Problems durchzuführen. Sie vergewisserten sich, dass keine gebrochenen Litzen im Kabel vorhanden waren, das zwischen der Unterversorgung und der Einspeisung der Energieversorgung verlief. Sie maßen den Widerstand der parallelen Kabeltrassen mit einem Mikro-Ohmmeter und stellten fest, dass sie alle sehr symmetrisch waren. Sie entfernten und reinigten auch alle Erdungs-, Bond- und Phasenleiterverbindungen.
Nachdem die Anlage wieder in Betrieb genommen wurde, war jedoch weiterhin ein erhöhter Erdstrom vorhanden.
Auf der Basis der während der Abschaltung durchgeführten Prüfungen zog das ASG-Team den Schluss, dass das Problem in der Anordnung der Leiter zwischen der Einspeisung der Energieversorgung und der 1.200-A-Unterversorgung begründet war. „Wir waren der Meinung, dass der Ausgleichsleiter im Kabelträger physisch falsch platziert war, was zu einer Interaktion zwischen dem Erdleiter und den Magnetfeldern des Phasenleiters führte, was wiederum das Fließen des Erdstroms bewirkte“, sagt Copp. „Der Erdleiter war gemäß den bewährten Verfahren der Kabelhersteller und den NEC/CEC-Bestimmungen platziert worden, aber unsere Untersuchung führte zu dem Schluss, dass diese Verfahren neu überprüft werden müssen.“
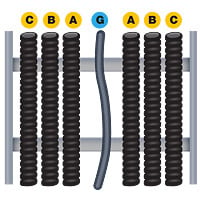
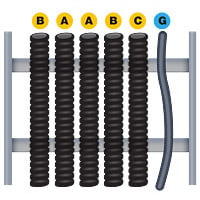
Nach weiteren Prüfungen stellten das ASG-Team und sein Gegenstück bei Camtac die Hypothese auf, dass eine Verlegung des Erdleiters in die seitliche Schiene des Kabelträgers helfen würde, die induzierten Erdströme abzumildern. Aber dies würde das Abschalten der Stromversorgung zu den Kompressorspeiseleitungen erfordern. So wurde wieder bis zu einem geeigneten Zeitfenster abgewartet, an dem die Produktion erneut für ein paar Stunden unterbrochen werden konnte. Einige Monate später ergab sich die Gelegenheit und die Camtac-Techniker führten die Verlegung durch.
Sofort nach Wiederherstellen der Stromverbindung maßen die Techniker den Erdstrom und den Strom in der seitlichen Schiene.
Eine deutliche Reduzierung des Erdstroms wurde sofort nach der Verlegung des Erdleiters deutlich“, sagt Copp. „Wir setzten die Überwachung des Systems fort, um zu sehen, ob sich die langfristigen Effekte verbessern und die Verschlechterung der Motorwicklungen reduziert wird. Bisher haben wir keine Zunahme des Erdstroms und keine weiteren Ausfälle bei den Kompressormotoren festgestellt. Wir setzen die Überwachung der Installation fort, um zu sehen, wie die Motoren über die Zeit hinweg laufen.“
Gerät oder Anlage | Strom | |
---|---|---|
Vor Verlegung | Nach Verlegung | |
Erdleiter | 160 A | 45 A |
Seitliche Schiene des Kabelträgers | 70 A | 20 A |