Guide to Insulation Resistance Testing
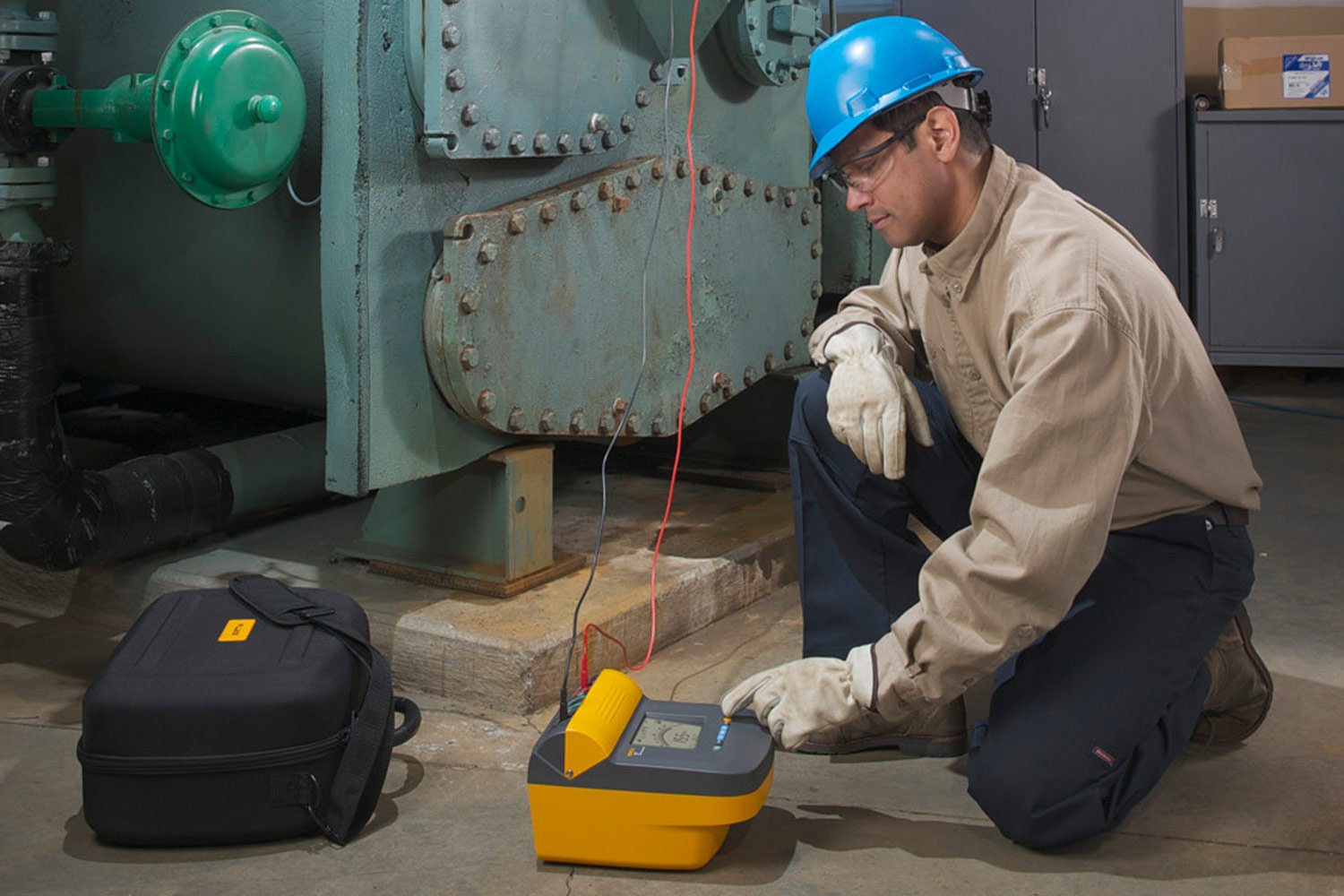
A manufacturing line that goes down, even for a few seconds, could have a serious impact on production and to the bottom line. A Preventive Maintenance Program (PMP) reduces the risk that a manufacturing plant will experience an unscheduled shutdown.
Every good PMP should include insulation measurement to ensure the thousands of motors used in manufacturing plants and facilities stay up and running. Even better, with data collection and historical analysis you can keep track of equipment status over time to potentially predict a failure in advance. Consider these equipment types and what they mean to your daily operations:
- Pumps
- Conveyors
- Compressors
- Fans
- Mixers
- Grinders
- HVAC
- Refrigeration
The wire insulation coating inside motors deteriorates over time with typical wear and tear. Other factors that can cause a motor to fail prematurely include moisture or contamination of the insulation. Failure to find degraded insulation in electromechanical equipment can lead to motor failure and lost production. The best method is to integrate regular insulation checks into your preventive maintenance schedule.
Going one step further to incorporate the benefits of data collection can mean the difference between up-and-running and unexpected shutdown.
What we learn from insulation resistance testing
"Leaking" is a term associated with a bad event. In the case of wire insulation in motors, leaks are not only bad but potentially dangerous and costly. When insulation deteriorates or has been damaged, current will leak into parts of the motor it shouldn’t, causing undo wear. The insulation keeps the current flowing along the wire exactly as intended.
Insulation testing with an instrument such as the Fluke 1555 FC 10 kV Insulation Tester with Fluke Connect® technology can detect leaks that appear as insulation resistance slowly tapers over time — a sign of normal and expected deterioration. In other cases, tests will detect a more serious issue in the moment when current suddenly drops and returns.
While motors play a significant role in industrial operations, insulated wire can be found in other critical electrical equipment as well, such as airport runway lighting or alert monitoring system cables.
Fluke insulation testers are ideal for testing capacitance and leakage current of switchgears, motors, generators, and cables, among other high voltage equipment. Timed ratio tests are used to detect insulation resistance and include the polarization index (PI) and dielectric absorption rate (DAR). The Fluke 1555 FC, Fluke 1550C FC, and Fluke 1587 FC automatically calculate the PI and DAR with no additional setup.
- PI is the ratio of the 10-minute resistance value to the 1-minute resistance value
- DAR is the ratio of the 60-second resistance value to the 30-second resistance value
These tests will identify changes in current over the specified periods of time, then produce a comparison in terms of a ratio. For example, if the current flow after 10 minutes is the same after 1 minute, that ratio would be 1:1. This ratio would be highly uncommon, however, because many other factors play a role in how current flows, including voltage and temperature. Since both voltage and temperature are not steady, they must be compensated for in determining actual insulation resistance performance.
Insulation resistance testing requires consistent temperature
Consider the perfect temperature outside and how it affects your personal performance. Now let’s say that the outside temperature is 75 °F. But what if the temperature changed just 18 °F in either direction? Do you perform differently when the temperature is 57 °F? What about 93 °F? You might say there isn’t much difference in your performance, but what if that little change in temperature increased your performance by 100% or decreased it by 50%? That’s exactly the effect temperature has on insulation resistance.
Change in temperature can drastically impact the insulation resistance values. For every 10 °C (18 °F) deviation above the baseline temperature, the resistance value halves. For every 10 °C (18 °F) below the baseline temperature, the resistance value doubles.
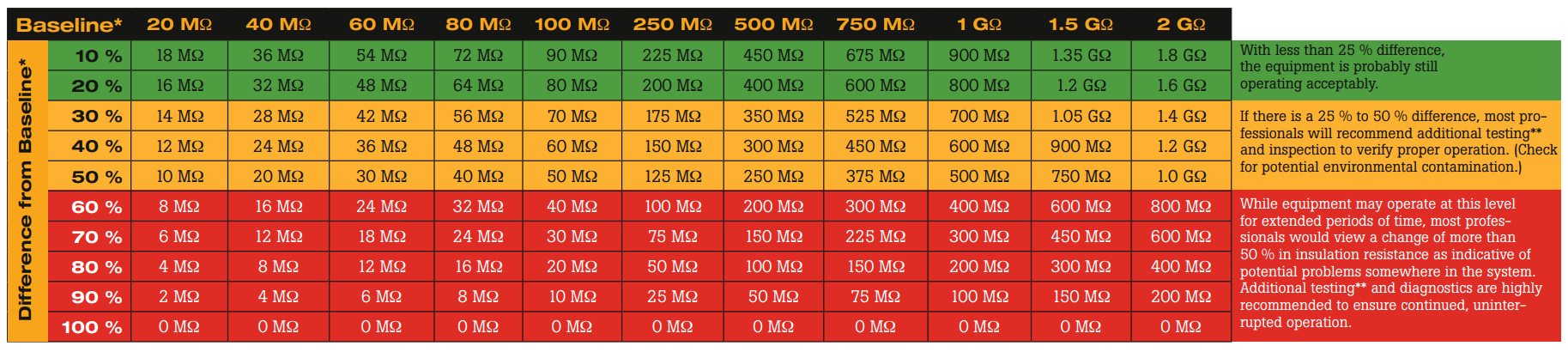
The Institute of Electrical and Electronics Engineers (IEEE) 43, "IEEE Recommended Practice for Testing Insulation Resistance of Electric Machinery," states that all resistance measurements should be corrected to use a constant, compensated temperature of 40 °C (104 °F). The consistent temperature establishes an accurate baseline and creates an opportunity for relevant historical comparisons.
Capturing insulation resistance testing data
You’ve tested. You have data. Now what? Maintaining historical tracking and trending of equipment helps identify degradation over time; patterns of performance become clearer, thereby allowing you to predict the need for maintenance and repairs, and avoid costly hiccups in plant operations. Data collected during insulation resistance testing should include the following, at a minimum.
- Insulation resistance values
- Testing time stamps
Contextual information
- Output test voltages
- Test durations
- Temperature compensations
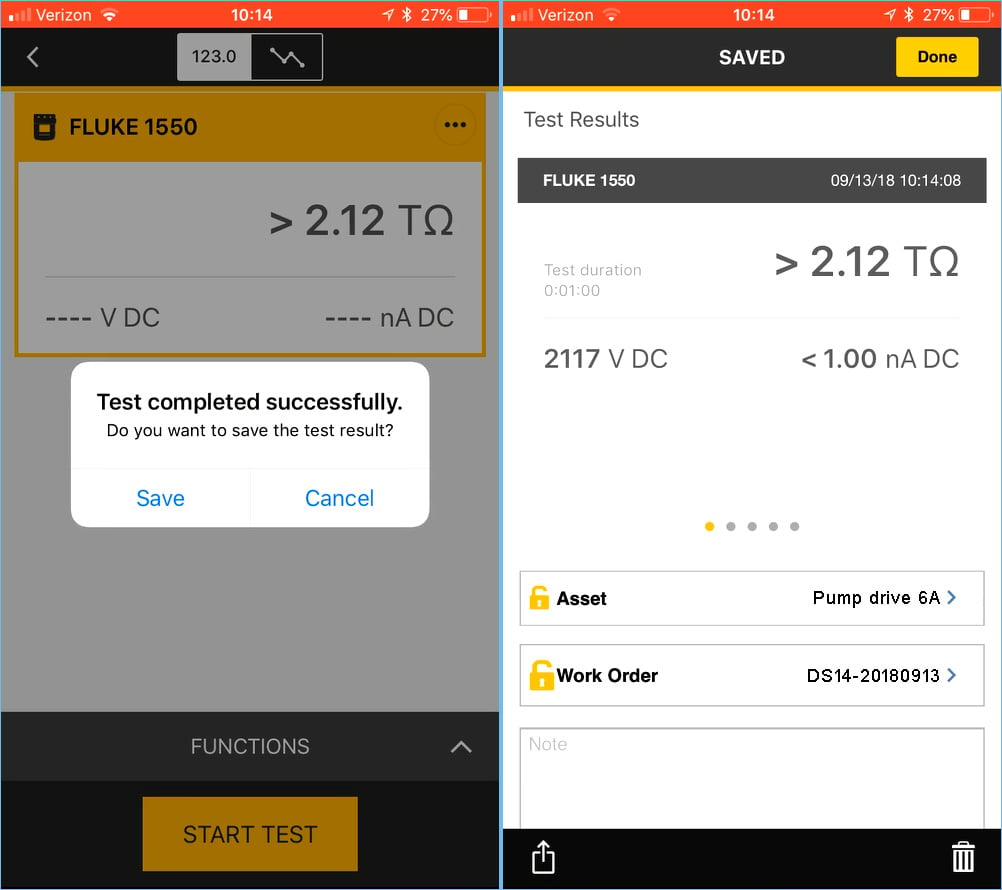
Insulation resistance testing should begin at the time of installation and continue throughout the lifetime of the equipment. Identifying and correcting problems before they result in a failure occurs through regularly scheduled preventative maintenance. Through insulation resistance testing and data collection, you may be able to predict possible system failures and take earlier action to prevent them.
The power to detect issues before they surface is literally in your hands. The Fluke family of insulation resistance testers give real-time information with a clean user interface, and Fluke Connect data collection, storage, and sharing capabilities provide an enhanced review of performance over time.