By Jack Smith
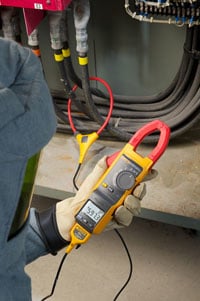
In February, I had the privilege of moderating a webcast for Consulting-Specifying Engineer magazine. The title was "Update on the 2011 National Electrical Code." The webcast speakers were Kenneth Lovorn, PE, president, chief engineer, Lovorn Engineering Associates, LLC in Pittsburgh; and Tom Divine, PE, senior engineer and project manager at Smith Seckman Reid, Inc. in Houston.
During the webcast, Lovorn and Divine focused on some of the important changes in the most recent version of the NEC: the 2011 edition. The specific topics they covered include:
- Available fault current field marking
- Shared neutral conductor restrictions
- Separately derived system grounding GFCI receptacle locations
- Parallel conductor ampacity
- Data center power distribution units
- Ground fault protection.
In the column I wrote two months ago, I discussed one of the new National Electrical Code (NEC) requirements involving available fault-current labeling. Space limitations for this column prevent me from covering all the topics Lovorn and Divine expertly covered in the webcast. So this month, I will focus on Divine's explanation of the 2011 NEC changes that involve parallel conductor ampacity.
Divine said that Section 310.4 in the 2008 version of the NEC became 310.10 in NEC 2011. NEC 2008 says that "the conductor size of 1/0 AWG and larger shall be permitted to run in parallel." NEC 2011 says almost the same thing. The difference is that the 2011 version says "only sizes 1/0 AWG and larger can be run in parallel."
Divine explained that an Authority Having Jurisdiction (AHJ) could allow smaller conductors to be run in parallel under the 2008 NEC. However, under the 2011 NEC, the AHJ can't allow it unless he or she amends the code.
In practice, this isn't a major change. "In my experience," said Divine, "AHJs have always enforced a prohibition on paralleling conductors smaller than 1/0 AWG - as if it were explicitly stated in the code. It wasn't specifically stated, but if I were to attempt to parallel #1 AWG conductors, for example, the AHJ would object."
An AHJ is the organization, office, or individual responsible for approving equipment, materials, an installation, or a procedure. Typically, the AHJ is the local electrical inspector who has been given statutory authority by a city, county, or state ordinance.
During the webcast, Divine also discussed some of the rules for parallel conductors that haven't changed from the 2008 NEC to the 2011 NEC. Parallel conductors are required to be identical to ensure the impedances of the individual conductors are as close to equal as reasonable. Because conductor impedance is very low, small changes in composition, geometry, or termination can cause a disproportionately large change in the total impedance of the conductor.
"Each individual conductor in a parallel assembly carries current in an inverse relation to its individual impedance," Divine said. "When a feeder is operated at some current near its total ampacity, a small variation in impedance between the parallel conductors can make too much current flow in the lower impedance conductors, causing them to overload and overheat."
Divine explained that parallel conductors must have the same length, material, cross-sectional area, and insulation. They must also use the same termination method and be located in the same raceway or identical cable assembly.
"The code specifically says that the similarity rule applies only to each course of conductors individually," said Divine. "For example, it's ok for the A phase conductor to be aluminum while the phase B and phase C conductors are copper. It's just necessary that all the A phase conductors be aluminum, and all of the B and C phase conductors be copper. That's an unusual situation, and it typically wouldn't arise in a new design."
Reasons for parallel conductors
The most popular reason for paralleling conductors is to provide higher ampacity than a single conductor can provide. "In a typical building design, the largest conductors are usually 500 kcmil or 600 kcmil," Divine said. "And many electrical contractors will actually object to 600 kcmil. If ampacity above 400 A is necessary, using parallel conductors is the only reasonable solution. In practice, the lower limit of 1/0 AWG conductors for paralleling doesn't have that big of an impact on electrical designs for facilities."
Another reason to parallel conductors is to keep voltage drop low - especially for motor starting or other low power-factor loads. If using single conductors with low power-factor loads, ac resistance - or inductive reactance - dominates the voltage drop. Inductance alone doesn't change much with conductor size. "The situation is different with ac resistance, which changes significantly with conductor size," said Divine. "Inductance changes very little with the conductor's cross-sectional area. However, the ac resistance changes inversely with the cross sectional area of the conductor."
In other words, increasing the conductor size doesn't help much to mitigate voltage drop caused by inductance. On the other hand, typically there will be a voltage drop due to the inductive reactance of a conductor when the power factor is low. "I've found this to be particularly useful when I'm working with fire pumps, which can be located quite a distance from the electrical service," Divine said. "Section 695.7 [of the NEC] limits the voltage drop under starting conditions for fire pumps to only 15 percent."
Situations allowing smaller parallel conductors
There are a few exceptions that allow running conductors smaller than 1/0 AWG in parallel. First, #2 AWG and #1 AWG can be used in existing installations under engineering supervision. "This exception can be important for managing harmonic current in neutrals," said Divine.
For control power, the circuit must be operating at 360 Hz or higher in order to run smaller conductors in parallel, according to Divine.
"There's an exception for elevator circuits in Section 620.12(A)(1) that allows for elevator control and elevator lighting cables to use conductors smaller than 1/0 AWG in parallel to manage the voltage drop in the long cables that are required for elevators that have a significant travel," Divine said.
As Divine said, the primary reason to parallel conductors is to provide higher ampacity than a single conductor to provide. When working with high levels of electrical current, qualified electrical workers should use high quality electrical measurement tools such as the Fluke 365, Fluke 376, and Fluke 381 clamp meters.
Until next time, keep standing on "Solid Ground."