NIF bringt Sternenenergie auf die Erde
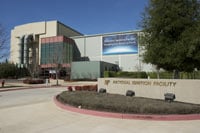
Man könnte dies als Fabrik bezeichnen, aber eine solche Anlage hat man höchstwahrscheinlich noch nie zuvor gesehen.
Der „Herstellungsprozess“ besteht hier in kurzen „Laserstößen“, die auf ein Ziel von der Größe eines BB gerichtet sind.
Das Produkt: Eine nukleare Reaktion, die sechs Mal heißer ist als die Sonne ... und ein wachsendes Verständnis von Fusionsreaktionen, die den Planeten eines Tages von der Abhängigkeit von fossilen Kraftstoffen befreien können.
Hier in der National Ignition Facility (NIF)des Lawrence Livermore National Laboratory in Kalifornien, USA, erzeugen Wissenschaftler nukleare Fusionsreaktionen, die mehr Energie freisetzen als ihre Laser einbringen – die Definition von „Zündung“. Dies ist der erste Schritt in einem Prozess, der eines Tages die „Sternenenergie“ – saubere nukleare Fusionsenergie – auf die Erde bringen kann.
Jeder Laserimpuls bündelt die Energie von 192 separaten Laserstrahlen aus allen Richtungen in einen Impuls, der nur den Bruchteil einer Sekunde andauert, um das kleine Ziel aus Tritium und Deuterium zu erhitzen und zu komprimieren. Diese 192 Laserstrahlen erzeugen zusammen bis zu 1,8 Millionen Joules ultraviolette Energie und müssen mit äußerster Präzision fokussiert werden. Um dieselbe Genauigkeit wie diese Anlage zu erhalten, müsste man auf der Baseball-Werferplatte in San Francisco stehen und den Ball in das Dodger Stadium im 350 Meilen entfernten Los Angeles werfen.
Es erfordert eine äußerst moderne Einrichtung und das beste Equipment, um einen solchen Impuls zu erzeugen. Das Hauptgebäude der NIF ist zehn Stockwerke hoch und rund um die Uhr im Einsatz. In diesem Gebäude befindet sich der hochenergetischste Laser der Welt und die größten jemals gebauten optischen Messinstrumente, die aus 7500 großen und über 26.000 kleineren optischen Vorrichtungen bestehen Die Zündimpulse setzen Strahlung frei, sodass die Strahlensicherheit hier eine wesentliche Rolle spielt.
Alles wird von einem der größten automatisierten Steuersysteme betrieben, das jemals für eine wissenschaftliche Maschine gebaut wurde; dieses System umfasst über 60.000 Steuerpunkte und 850 Computer. Der Erfolg hängt von über 6000 Messinstrumenten und Ventilen sowie Druck-, Temperatur- und Feuchtigkeitssensoren und Transmittern ab, die alle einzeln in der NIF-Datenbank gespeichert sind. Und jedes einzelne dieser Geräte muss kalibriert werden.
Eine Welt von Kraft und Präzision
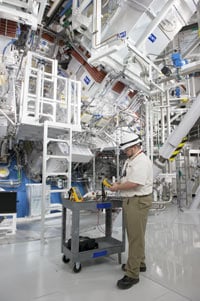
„Das Einzige, das sich mit dem vergleichen lässt, was wir hier tun, ist ein NASA-Countdown für den Start eines Shuttle“, sagt Travis Averill, NIF Calibration Program Manager. „Wenn die Sachen nicht gewartet und kalibriert werden, dann arbeiten sie nicht zuverlässig und auf reproduzierbare Weise. Darum ist die Kalibrierung vom kleinsten Drehmoment-Schraubendreher für die Montage der optischen Geräte bis hin zu den Oszilloskopen, welche die Neutronenausbeute berechnen, von so wesentlicher Bedeutung. Wenn wir unsere zweistöckige Klimaanlage nicht regelmäßig warten, bekommen wir Probleme mit der Temperatur. Die Art und Weise, auf die die Laserstrahlen durch das Gas verlaufen, würde sich ändern, und wir würden nicht mehr da treffen, wo wir es möchten.“
Wie verwalten die Techniker eine derart riesige und komplexe Einrichtung? „Wir verwenden grafische Benutzeroberflächen im Hauptkontrollraum, in dem der Großteil unserer Einrichtungsüberwachung stattfindet“, so Averill. „Hier werden uns die dynamischen Echtzeit-Anzeigen angezeigt, und wir können beinahe alles steuern.“
Das Wichtigste ist, sicherzustellen, dass die tausenden vernetzten Komponenten und Sensoren, die ihre Signale an den Kontrollraum übermitteln, über das 24-V-Gleichstrom-Steuernetzwerk zu den Bildschirmen der grafischen Benutzeroberflächen genaue Werte liefern. Averill prüft also an den Anzeigen auf den Bildschirmen, ob zum Eingangssignal das passende Ausgangssignal geliefert wird, und nicht an den Ausgängen an den dezentralen Sensoren und Transmittern. „Wir kalibrieren die Bildschirmanzeigen der grafischen Benutzeroberfläche jedes Mal, um so viele Fehler zu verhindern, wie wir können. Ich glaube fest an die Full-Loop-Kalibrierung“, sagt er weiter.
Um beispielsweise einen Temperatursensor zu kalibrieren, schließt Averill seinen Fluke 9142-P Blockkalibrator, der mit dem Fluke 5608 Referenzstandard ausgestattet ist, zusammen mit einem Prozesskalibrator Fluke 754 HART an. Er stellt die Metrologie so ein, dass eine bestimmte Prüftemperatur (z. B. 60, 70 oder 80 °F bzw. 15,6, 21,1 oder 26,7 °C) erreicht wird, und hält dann das Temperaturelement in den Sensor. Nachdem sich die Temperatur stabilisiert hat, funkt er den Kontrollraum an, um die Anzeige auf der grafischen Benutzeroberfläche zu prüfen. Ziel dieser Maßnahme ist es, einen Wert im Kontrollraum zu erreichen, der um weniger als 10 °F von der Blockkalibratoreinstellung abweicht. Eine Anzeige von 56,10 Grad würde diesem Standard entsprechen; eine Messung von 56,11 Grad jedoch nicht mehr.
„Wenn die vorliegenden Daten den Spezifikationen entsprechen, nehmen wir keinerlei Änderungen vor“, erklärt Averill. „Wenn die Daten jedoch nicht mehr im zulässigen Bereich liegen, machen wir als erstes eine Stromschleifenprüfung. Wir schließen den 754 HART-Kommunikator an, sprechen den Transmitter an und klinken uns in den Strom. Wir schalten in Reihe und überwachen die 4–20 mA. Ich lasse den Transmitter den Wert ausgeben, den das Gerät als 4 mA erkennt, und messe das Ergebnis. Gleichzeitig müssten an der grafischen Benutzeroberfläche 56,00 Grad angezeigt werden“, erklärt Averill weiter.
„Meine mA-Messung führe ich normalerweise mit dem 754 durch, da dieses Gerät über zahlreiche weitere Funktionen verfügt. Das ist das Tolle daran! Ich kann es verwenden, um meine HART-Kommunikatoren anzusprechen, und ich kann es auch verwenden, um die mA zu messen, die in diesem Fall eine Anzeige von 56 Grad produzieren sollte. Ich nehme die 4-mA-Ausgabe, loope sie durch meinen 754 Kalibrator, und messe sie dabei. Mir wird also eine analoge Ausgabe der Prozessvariable angezeigt, die widerspiegelt, was das Gerät denkt, das es ausgibt, und ich habe einen tatsächlichen Messwert meiner mA. Mit dieser Prüfung kalibriere ich eigentlich die Transmitterausgabefunktion und stelle sicher, dass sie der Spezifikation entspricht. Das sind zwei Fliegen mit einer Klappe. Dieser Vorgang ist schneller und unkomplizierter.“
Wenn die Transmitterausgabe abweicht, muss Averill sie so anpassen (die verwendeten HART-Kommunikatoren sind programmierbar), dass die Anzeigen auf der grafischen Benutzeroberfläche der Temperatur entsprechen, die der Sensor erfasst. Der Vorgang für die Druckkalibrierung ist ähnlich. Averill verwendet wieder die Fluke 754 oder 744 Dokumentierenden Prozesskalibratoren zusammen mit dem tragbaren elektrischen Fluke 719 Druckkalibrator und eine tragbare Handpumpe, die den Prüfdruck aufbaut.
Wenn mehr dahinter steckt
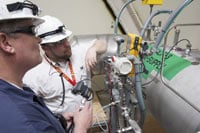
Alles, was Averill über das Kalibrieren weiß, hat er in seinen fünf Jahren als US-Marine gelernt, in denen er die Avionik von FA-18 Hornet-Kampfjets kalibriert hat. Anschließend arbeitete er zwei Jahre für einen Kalibrierungsdienstleister, vornehmlich im biomedizinischen und pharmazeutischen Bereich.
„Die Arbeit, die ich heute mache, entspricht meine Streben nach etwas Größerem, und das verdanke ich USMC“, sagt er. „In 10, 20 oder 30 Jahren, wenn die fossilen Brennstoffe verbraucht sind und die Welt neue Energie mit einer viel höheren Kapazität als die von heute braucht, wird es die Fusionsenergie sein, die uns antreibt.“
Bevor Averill anfing, wurden die Kalibrierungsarbeiten bei der NIF von lokalen unabhängigen Laboren durchgeführt. Heute werden mehr Aufgaben intern erledigt, wodurch die NIF ihre Zeitpläne einhalten und täglich oder häufiger Impulse absetzen kann. „Eine der schwierigsten Aufgaben ist es, eine Kalibrierung im laufenden Betrieb durchzuführen, ohne dabei die Impulse zu beeinträchtigen“, erzählt Averill. „Das Absetzen von Impulsen und jeder Schritt in Richtung Fusion bring hier das Geld ein.“
Averill arbeitet bereits seit seiner Zeit bei den Marine Corps mit Messinstrumenten von Fluke (siehe Seitenleiste), und er hat einige Tipps für andere Kalibrierungsfachleute.
Für die Kalibrierung von Temperatursensoren „kaufen Sie einen oder zwei Blockkalibratoren“, sagt er. „Damit vermeiden Sie bei Laborgeräten und Geräten im Einsatz Ölbäder. „Was Sie anfangs mehr für das Gerät bezahlen, rechnet sich bereits nach den ersten paar Einsätzen. Garantiert!“ Deutliche Verbesserungen in Steuerung und Genauigkeit mit dem Fluke 9142-P Blockkalibrator
Das Fluke 9142-P ist ein industrieller Schleifenkalibrator für die Temperaturerfassung und sehr gut für die Schleifenkalibrierung von Temperaturtransmittern, Vergleichskalibrierungen oder einfache Überprüfungen von Thermoelement-Sensoren geeignet. Das Gerät wiegt weniger als 8,2 kg, erreicht schnell die erforderlichen Temperatureinstellwerte und ist dennoch stabil, einheitlich und genau.
„Wir können Temperaturwerte festlegen und das Gerät so einstellen, dass es sich ohne jede weitere Aufsicht an unsere grafische Benutzeroberfläche anmeldet. Eine Dreiviertelstunde später kommen wird zurück und nehmen bei Bedarf Änderungen vor. In der Zeit, in der das Gerät seine Arbeit verrichtet hat, konnten wir die Transmitter anschließen und trennen. Ich habe ein zweites Gerät gekauft, weil man ziemlich einfach zwei gleichzeitig verwenden kann. Wenn ich heute im Einsatz wäre, würde ich wahrscheinlich sogar drei Geräte haben wollen, die ich abwechselnd verwenden kann, um den Prozess zu optimieren.“
Schulen des Teams
Die Kalibrierungsarbeiten bei der NIF erfordern zwei Teams von Wartungstechnikern: Ein Team arbeitet an den herkömmlichen Einrichtungen , und das andere Team arbeitet an den Systemen am Laserstrahlpfad – insgesamt handelt es sich dabei um 40 Systeme.
„Die Teams arbeiten sehr häufig zusammen und können so ihr Wissen über die Wartung und Kalibrierung und ihre Erfahrungen bei der Ausführung dieser Arbeiten mit den anderen teilen“, sagt Averill. „Dadurch ist unser technisches Fachwissen auf einem der höchsten Niveaus, die ich je erfahren konnte.“
Neben den Kalibrierungstools besteht der Schlüssel zum Erfolg laut Averill mitunter darin, dass die Teammitglieder verstehen, warum bestimmte Prüfungen erforderlich sind und wie diese durchgeführt werden. Hierzu hat er über 50 Kalibrierungsverfahren schriftlich festgehalten.
„Techniker verlieren den Weitblick, wenn sie blind Verfahren ausführen, die sie nicht verstehen“, erklärt er. „Einer der besten Tricks, die ich habe, ist es, die Verfahren aus technischer Sicht aufzuschreiben, als ob man neben den Technikern steht und ihnen erklärt, was sie tun und worauf sie achten müssen, wenn etwas schief geht.“
Für den Fall, dass Probleme auftreten, hat das Wartungsteam Zugriff auf Unterlagen zur Fehlermöglichkeits- und -einflussanalyse, die im Vorfeld verfasst wurden, sodass sie nicht alle Probleme in Echtzeit herausfinden müssen. Zudem liegen für viele Anlagen Ersatzteile bereit, sodass der Betrieb schnell wieder hergestellt werden kann.
Es gilt einfach, keine Zeit zu verlieren. Das Ziel, die nukleare Fusion zu erreichen, ist für Ende 2012 gesetzt, und Averill und seine Kollegen bei der NIF, von denen viele ehemalige Nukleartechniker der US Navy sind, wissen, dass sie Keine Zeit zu verlieren haben.
„Hieran wird schon 50 Jahre gearbeitet“, so Averill, „und uns bleibt nur noch weniger als ein Jahr. Die Zeit hier ist sehr aufregend.“