Energieverschwendung in Industrieanwendungen erkennen
Für Energieeinsparungen gibt es Ziele und Pläne. Industriebetriebe in den Vereinigten Staaten zeigen ein nachhaltiges Interesse an Energiemanagement. Dies ist das Ziel: den Gesamtenergieverbrauch senken oder den Verbrauch konstant halten, aber die Produktivität je verbrauchter Kilowattstunde erhöhen.
Der Plan? Manchmal ist er das Problem.
In Fertigungsbereichen hat ein Plan nur dann eine Chance, wenn Erfahrung und Fakten das Ziel begleiten und eine positive Renditeentwicklung erfolgt. Beim Energieverbrauch haben Manager von Industriebetrieben oft nicht die Recherchekapazitäten, um Basiswerte für einen „angemessenen“ Energieverbrauch in einem Fertigungsbetrieb festzulegen. Wie lässt sich also einschätzen, welcher Anteil des aktuellen Energieverbrauchs angemessen und was Verschwendung ist bzw. welcher bisher verschwendete Anteil eine ausreichend hohe Rendite ermöglicht?
Bei der hier besprochenen Rendite werden die vom Energieversorgungsunternehmen (EVU) berechneten Kosten pro kWh betrachtet. Entsprechend des Tarifmodells des EVU ändern sich diese Kosten je nach Tages- und Jahreszeit. Durch Einsparungen lassen sich diese Ausgaben reduzieren. Die Investition besteht in den Materialien und der Arbeitskraft, die für eine Veränderung des Energieverbrauchs benötigt werden. Als Amortisationszeit bezeichnet man den Zeitraum, in dem sich die Investition durch die geringere Energierechnung bezahlt macht. Nach der Bezahlung der Kosten beginnt der positive Effekt.
Wenn wir zur Frage des Plans zurückkehren: Wie lässt sich eine Renditeschätzung vornehmen, wenn es keinen Industriestandard für einen angemessenen Energieverbrauch gibt?
Profilierung des Energieverbrauchs in Industrieanwendungen
Der Energieverbrauch in Industrieanwendungen ist von mehreren Variablen abhängig:
- Alter der Anlage
- Art und Größe der Last
- Betriebsplanung (Stunden pro Woche und Last im Zeitverlauf)
- Anzahl der Arbeiter
- Klima
- Instandhaltungsphilosophie
Die Antwort lautet: Versuchen Sie nicht, jede von Ihrer Anlage verbrauchte Kilowattstunde zu managen. Hierbei handelt es sich um den "Erfahrungsteil" der Gleichung. Unterteilen Sie den Betrieb in elektrische Infrastruktur und wichtigste Systeme.
Energieeinsparungen beginnen mit zwei grundlegenden Strategien: (1) allgemeine Prüfung der wichtigsten Systeme und (2) gezielte Datensammlung, einschließlich Protokollierung des Energieverbrauchs an den Hauptzuführungen der Versorgungskabel und an den wichtigsten Lasten.
Ermitteln Sie, für welchen Verbrauch ein System ausgelegt ist, bestimmen Sie den aktuellen Verbrauch und identifizieren Sie verschwenderische Praktiken anhand von Betriebsstunden und Betriebsart oder in der Ausrüstung und im System selbst. Um die Einsparziele zu erreichen, muss der Betrieb Verschwendungen unterbinden. Dies kann durch Änderungen im Betrieb, in der Instandhaltung oder an Geräten und Steuerungen geschehen.
Komponenten der Leistung
Ehe wir erläutern, wie sich der Energieverbrauch nachverfolgen lässt, wollen wir uns erneut ansehen, wie wir die Energie bzw. Leistung definieren und messen können.
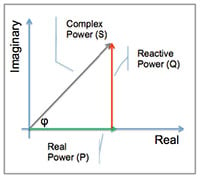
Energie besteht aus Wirk-, Blind- und Scheinanteilen. (Abbildung 1).
Energie ist definiert als Leistung multipliziert mit der Zeit, in der diese Leistung genutzt wird:
- Wirkleistung (P) in W
- Blindleistung (Q) in VAR (VA reaktiv)
- Komplexe Leistung (S) in VA
- Scheinleistung, der Betrag der komplexen Leistung (VA)
Die mathematische Beziehung von Wirk-, Blind- und Scheinleistung kann durch Vektoren dargestellt oder mit komplexen Zahlen ausgedrückt werden, S = P + jQ (wobei j die imaginäre Einheit ist).
Die Blindleistung überträgt keine Energie – verrichtet also keine Arbeit – und wird daher als imaginäre Achse des Vektordiagramms dargestellt. Die Wirkleistung überträgt Energie und ist daher die reale Achse.
Der Energiefluss in einem System hängt von der Last ab – ist es eine ohmsche Last, eine Blindlast oder beides?
Bei einer rein ohmschen Last wechseln Spannung und Strom zur selben Zeit die Polarität. Zu jedem Zeitpunkt ist das Produkt aus Spannung und Strom positiv und nur Wirkleistung wird übertragen: Es wird Arbeit verrichtet.
Bei einer reinen Blindlast sind Spannung und Strom um 90° phasenverschoben und das Produkt aus Spannung und Strom kann positiv oder negativ sein. Dies weist darauf hin, dass ein Teil der Energie an die Last übertragen wird und ein Teil zurückfließt. Die Übertragung von Wirkleistung an diese Last ist Null: Es wird keine Arbeit verrichtet.
In der Praxis beinhalten Lasten eine Kombination aus Widerstand, Induktivität und Kapazität, wodurch in einem System Wirk- und Blindleistung erzeugt werden. Aus diesem Grund sind elektrische Anlagen so konzipiert, dass sie eine bestimmte Menge an Blindleistung tolerieren. Problematisch wird es, wenn zu viel Blindleistung erzeugt wird. Einerseits reicht die Wirkleistung nicht aus, um die benötigte Arbeit zu verrichten, andererseits wird darüber hinaus die Leistungsfähigkeit der Anlage verringert. Aus diesem Grund bestrafen die EVU ihre Kunden, wenn ihre Lasten zu viel Blindleistung erzeugen: Es ist verschwendete Energie, deren Erzeugung Geld kostet, die aber nicht genutzt werden kann. Auf den meisten Stromrechnungen wird die Blindleistung in VAR angegeben und häufig wird der Leistungsfaktor berechnet. Der Leistungsfaktor ist ein Maß dafür, wie weit die Wirkleistung einer Anlage unter 100 % liegt. Die meisten Versorger fordern von ihren Kunden einen Leistungsfaktor von über 0,95.
Verfolgung des Energieverbrauchs
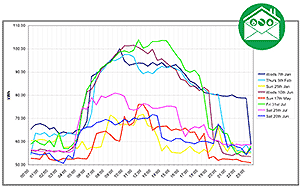
Elektriker kennen diese Energiekomponenten und können Messgeräte zur Protokollierung einrichten, um den Gesamtwert und den Leistungsfaktor der verbrauchten Energie zu erfassen und anschließend zu verfolgen, wann Energie verbraucht wird und wodurch (Abbildung 2).
Protokollieren Sie die Leistung an Haupt- und Unterverteilungen und großen Lasten. Zeichnen Sie kW, kWh und Leistungsfaktor über einen repräsentativen Zeitraum auf.
Auf diese Weise erhalten Sie ein sehr exaktes Bild Ihres tatsächlichen Energieverbrauchs in dreiphasigen Stromkreisen und Lasten.
Die größten Energieeinsparungen können Sie erzielen, wenn Sie auftretende Spitzenlasten ermitteln, Leistungsfaktor und Gesamtenergieverbrauch mit der Stromrechnung vergleichen und Ihre Lasten nach Möglichkeit umverteilen. Bereits wenige Minuten Spitzenlast können dazu führen, dass der Strompreis für mehrere Stunden, Tage oder Wochen ansteigt.
Die Umplanung von Lasten kann einem Unternehmen die Nutzung von Tageszeiten ermöglichen, zu denen die Energie günstiger ist. Prüfen Sie, wie weit Ihr Leistungsfaktor unter „1“ liegt. Sehen Sie auf Ihrer Stromrechnung nach, ob bei einem geringen Leistungsfaktor ein Aufschlag berechnet wird. In diesem Fall kann ein Power-Logger bei der Verfolgung der Quellen des Energieverbrauchs behilflich sein. Nehmen Sie Modernisierungen Ihrer Anlagen vor, und schließen Sie den Logger danach erneut an, um die Vorteile Ihrer Effizienzsteigerungen aufzuzeigen.
Ursachen von Energieverschwendung entdecken
Jedes System und jeder Betriebszustand stellt eine potenzielle Ursache für Energieverschwendung dar, die verringert oder beseitigt werden kann. Elektrische Teilsysteme, Druckluft-, Dampf- und spezifische elektromechanische Systeme sind ein guter Ausgangspunkt, aber jeder Betrieb verfügt über eigene potenzielle Ursachen für Energieverschwendung, die durch Messungen ermittelt werden sollten.
Das Ziel besteht darin, den Energieverbrauch von speziellen Geräten und Prozessen aufzuzeichnen, um sich anzusehen, wo Energie verschwendet wird, um Verschwendungen zu quantifizieren und Verbesserungen oder den Austausch von Geräten anhand ihrer Lebensdauer und danach zu priorisieren, welche Änderungen die höchste Rendite bewirken können.

Eine Aufzeichnung des Energieverbrauchs bietet außerdem eine Grundlage für eine Messung der Effektivität von Energiesparprojekten, um die Kosten zu rechtfertigen (Abbildung 3).
Häufige Ursachen für Energieverschwendung in elektrischen Teilsystemen:
- Lasten arbeiten oft nach Feierabend weiter oder werden unnötig zu Hochtarifzeiten ausgeführt.
- Motoren ohne Steuerungen können mehr Leistung produzieren als erforderlich.
- Überstrom-/Überspannungszustände verursachen einen übermäßigen Energieverbrauch, der kompensiert werden muss.
- Durch Phasenunsymmetrie verbraucht die Last Energie, ohne sie nutzen zu können.
Erkennen und bestimmen:
- Führen Sie thermische Untersuchungen von elektrischen Verteilungen und mechanischen Lasten durch, um Überhitzungen zu erkennen.
- Überwachen Sie die Leistung im Zeitverlauf: Wie viel Leistung wird zu welcher Tageszeit aufgenommen, und wie hoch ist die Energieverschwendung?
Häufige Ursachen für Verschwendungen und zu prüfende Punkte in elektromechanischen Systemen.
- Erhöhte Reibung durch falsche Ausrichtung, Lagerdefekte, Unwucht und Lockerung beanspruchen den Motor zu stark und verbrauchen übermäßige Energie.
- Nicht gesteuerte Lasten, die nach Feierabend nicht ausgeschaltet werden, laufen auch während Hochtarifzeiten, produzieren mehr Leistung als erforderlich oder leiden an Überspannung/Überstrom und Phasenunsymmetrie.
- Alternde mechanische Geräte verbrauchen so viel mehr Energie als neue Hochleistungsmodelle, dass ein vorzeitiger Austausch schon aufgrund des reduzierten Energieverbrauchs gerechtfertigt sein könnte.
Erkennen und bestimmen:
- Führen Sie thermische Untersuchungen von Steuertafeln und mechanischen Lasten durch, um Überhitzungen zu erkennen, die auf elektrische Ineffizienz hinweisen.
- Protokollieren Sie die Leistung im Zeitverlauf: Überprüfen Sie den gesamten Energieverbrauch sowie Leistungsfaktor, Spitzenbedarf, Unsymmetrie und Oberschwingungen.
- Prüfen Sie den Schwingungspegel im Vergleich zu Normen und Spezifikationen und finden Sie Lösungen durch Instandhaltung, beispielsweise erneute Auswuchtung.
- Untersuchen Sie mit einer Wärmebildkamera Kupplungen/Welle/Riemen, Lager und Lüfter.
- Überprüfen Sie die Strom- und Spannungspegel.
- Untersuchen Sie mit einer Wärmebildkamera Verteiler und Anschlusskästen sowie Wicklungen und führen Sie eine Isolationswiderstandsmessung durch.
Häufige Ursachen für Verschwendungen und zu prüfende Punkte in Druckluftsystemen:
- Übermäßige Undichtigkeiten in Druckluftleitungen führen zum Betrieb mit erhöhter Leistung, um die Versorgung aufrechtzuerhalten.
- Verdichter, die außerhalb der Nutzungszeit nicht abgeschaltet werden, verschwenden Energie.
Erkennen und bestimmen:
- Protokollieren Sie die Leistungsaufnahme des Verdichters.
- Bestimmen Sie den Druckverlust durch Messen des Drucks an Verdichter und Verwendungsstelle.
- Ermitteln Sie Undichtigkeiten der Anschlüsse und Leitungen mit einem Ultraschall-Leckdetektor.
Häufige Ursachen für Verschwendungen und zu prüfende Punkte in Dampfsystemen:
- Ausgefallene Kondensatableiter und unzureichende Isolierung verschwenden Dampf und verursachen eine erhöhte Leistungsaufnahme, um den erforderlichen Dampfdruck aufrechtzuerhalten.
Erkennen und bestimmen:
- Protokollieren Sie die Leistungsaufnahme am Dampfkessel.
- Führen Sie eine Untersuchung der Rohre und Kondensatableiter mit einer Wärmebildkamera durch, um fehlerhafte Isolierungen und Blockierungen zu erkennen.
Prüfen Sie die durch Energieeinsparung erzielbare Rendite
Wie können wir herausfinden, welche Systeme die höchste potenzielle Rendite durch Energieeinsparung beinhalten, ohne dass wir auf einen Industriestandard zurückgreifen können? Unser bestes Material sind derzeit Fallbeispiele für häufige Situationen. Hier einige Beispiele für häufige industrielle Systeme.
Elektromechanische Inspektion
Anlagentyp: Stahlrecyclingwerk in Deutschland
Gerätetyp: riemengetriebener Lüfter für Prozesskühlung
Durchgeführte Messungen: Schwingungsmessungen
Festgestellte Probleme: mäßige Unwucht, zusammen mit Fehlausrichtung und Lagerverschleiß, wurde erkannt.
Einsparungen: Neue Abstimmung erforderlich. Ein 350-kW-Motor lief mit 80 Prozent Nennleistung, die gemessene Leistung lag bei etwa 280 kW. Durch die neue Abstimmung wurde die Leistungsaufnahme um 3 Prozent reduziert. Bei einem Preis von 0,11 €/kWh lagen die jährlichen Einsparungen bei 8.094 €.
Untersuchung des Druckluftsystems
Anlagentyp: Fertigung
Gerätetyp: Druckluftsystem
Durchgeführte Messungen: Ultraschallinspektion des Druckluftsystems (empfohlene vollständige Datenprotokollierung des Verdichters)
Festgestellte Probleme: Menge der erzeugten Druckluft im Vergleich zum tatsächlichen Bedarf.
Einsparungen: Mehrere Einsparmöglichkeiten wurden gefunden. Jährliche Gesamtersparnis von 50.600 $. Abschalten des Verdichters am Wochenende: jährliche Einsparungen in Höhe von 32.700 $ Montage von Magnetventilen zum Abschalten der Luftzufuhr bei Maschinenstillstand: jährliche Einsparungen in Höhe von 7.100 $ Instandsetzung von 36 Leckstellen: jährliche Einsparungen in Höhe von 4.800 $. Filter im System installiert für einmalige Kosten von 6.000 $; jährliche Einsparungen durch diese Maßnahme: 6.000 $.
Untersuchung der Dampfabscheider
Anlagentyp: Fertigung
Gerätetyp: Dampfkessel und Dampfleitungen
Durchgeführte Messungen: Thermische Inspektion der Dampfleitung
Festgestellte Probleme: sechs Kondensatabscheider funktionierten nicht ordnungsgemäß, Wärmeübertrager in den Galvanisierungstanks haben Lecks; Dampflecks an den Galvanisierungslinien; Möglichkeiten zur Kondensatrückgewinnung
Ersparnisse: Austausch von sechs fehlerhaften Dampfabscheidern zu je 500 $. Erreichte Einsparungen: 3.200 $ je Dampfabscheider, unter Berücksichtigung der bekannten Kosten für die Dampferzeugung und von Berechnungen des Wärmeverlusts. Einsparungen insgesamt: 16.200 $.
Nächster Schritt: Protokollierung der aufgenommenen Energie an der Versorgung des Dampferzeugers vor und nach dem Beheben von Leckstellen und Kondensatproblemen.
Erhöhte Produktivität oder reduzierte Gemeinkosten?
Für die nächste Frage gibt es nur gute Antworten: Wenn Sie einen Weg zur Reduzierung des Energieverbrauchs gefunden haben, nutzen Sie diese Einsparungen dann zur Aufstockung der Anlagenkapazität (mehr Volumen bei gleichem Verbrauch in kWh) oder für andere Unternehmensstrategien (Gewinnmargen, Preisrealisierung)?
Die Reduzierung des Energieverbrauchs ist in jedem Fall ein gutes Geschäft. Durch die Aufzeichnung der Betriebseigenschaften jedes einzelnen großen Systems und dem Abgleich dieser Kosten mit der Stromrechnung kann man quantifizieren, wo und wann Energie verbraucht wird. Hierdurch können die Unternehmen häufig durch einfache Veränderungen im Betrieb und in den Zeitplanungen Ersparnisse realisieren. Durch die Erkennung ineffizienter oder veralteter Geräte können die Unternehmen Austauschmaßnahmen rechtfertigen und priorisieren. Und durch eine Reduzierung des Gesamtenergieverbrauchs senken die Unternehmen ihre Betriebskosten und verbessern so ihre Wettbewerbsfähigkeit am Markt.
Diesen Artikel im PDF-Format aufrufen