Le proverbe dit que la première fois que vous branchez un moteur triphasé, il tournera en sens inverse. Si vous avez de la chance, vous aurez juste l'air bête. Sinon, cela peut gravement endommager des équipements onéreux et coûter cher à vous ou à votre employeur.
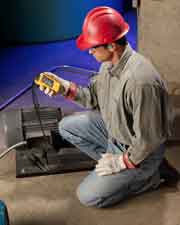
Des compresseurs abîmés
Voici un exemple de problèmes qui peuvent survenir. Un fournisseur électrique dans le Nord-Ouest installait un nouveau système de commutation informatisé. Il était destiné à prendre en charge une grande zone qui comprenait des clients industriels et diverses installations commerciales. L'équipe en charge de son installation était expérimentée, mais voyait cet équipement pour la première fois. Le contremaître, qui devait préciser où les cordons devaient être connectés, a inversé les phases par inadvertance.
Une fois l'intervention terminée, l'alimentation est réactivée.
Un peu plus loin, chez un grand fabricant, tout un ensemble de compresseurs à vis d'un système HVAC (allant de 25 à 50 ch) a commencé à tourner en sens inverse. Les compresseurs à vis sont lubrifiés par des pompes à huile internes, « et s'ils tournent en sens inverse, ils ne pompent pas l'huile », selon le responsable de la maintenance du fabricant. En quelques secondes, tous les compresseurs étaient grillés. « Heureusement que nos refroidisseurs ne s'étaient pas mis en marche avant que l'on se rende compte du problème, dit le responsable de la maintenance, car les conséquences auraient été désastreuses. »
Le fournisseur électrique a dû payer les nouveaux compresseurs, ainsi que la location des unités de remplacement temporaires. Même s'il a réalisé des études énergétiques et mis en place un nouveau système plus efficace pour le client, il en est ressorti gêné et avec une grosse facture.
Tout cela aurait pu être évité, si l'équipe du fournisseur électrique avait mieux compris les instructions du nouvel équipement et avait utilisé un indicateur de rotation de phase comme le Fluke 9040pour vérifier la rotation de phase à la sortie 480 V des transformateurs qui alimentent les compresseurs. Ces quelques minutes auraient permis au client d'éviter un temps d'arrêt important et au fournisseur d'économiser une grosse somme d'argent.
Bien faire les choses
Un autre fournisseur électrique, après avoir utilisé pendant des années d'ancien types de disque rotatif, est passé aux Fluke 9040. Ils sont fréquemment utilisés après qu'un compteur ou transformateur a été changé, afin de vérifier que la rotation est correcte avant de connecter la charge. Paradoxalement, cet élément n'est pas pris en compte dans une nouvelle installation, car s'assurer que la rotation est correcte est de la responsabilité de l'électricien du client. S'il est raisonnable, il devrait posséder un 9040.
Le fournisseur utilise le 9040 depuis environ trois ans. Au départ, cet outil a été choisi car c'était la seule unité de catégorie IV qu'il ait trouvée. Un besoin pour cet outil avait été grandement ressenti lorsque les électriciens d'un client ont testé la rotation de phase sur un transformateur dont la plaque signalétique indiquait 240 V à l'aide d'une unité de phase de disque rotatif. Malheureusement pour eux, la tension du système était en fait de 2 400 V et elle a fait fumer leur indicateur de rotation de phase. Cet événement a poussé le personnel du fournisseur à la réflexion : « Si cela leur est arrivé, et que nous avons des secondaires de 2 400 V dans notre système, il est possible que quelqu'un se trompe en lisant une plaque signalétique dans notre système. Achetons un Catégorie IV au cas où quelqu'un se trompe. »
Le fournisseur a alors fait l'acquisition du 9040. Certains des techniciens les plus âgés ont d'abord résisté, en disant qu'ils préféraient les anciens points rotatifs, mais les plus jeunes ont l'habitude des appareils électroniques. Comment faire plus simple : boutons L1, L2, L3, rouge, blanc, bleu... difficile de se tromper.
Encore des équipements abîmés
Bien sûr, il faut vraiment utiliser le 9040. Une fois, un fournisseur a acheté un nouveau moteur et a déplacé un compteur existant pour l'alimenter, mais l'électricien ne l'a pas branché comme il l'était auparavant : tandis que le compteur indiquait rouge-blanc-bleu dans le sens antihoraire, il avait été placé dans le sens horaire. Un technicien a vérifié la rotation sur un autre compteur, a constaté qu'il était correct et a manifestement supposé que c'était la même chose pour celui-ci. Il a branché le compteur, s'est débarrassé du disjoncteur et a abîmé le moteur.
Une autre fois, la tâche consistait à remplacer des transformateurs par des unités plus lourdes avec des fils plus gros. Bien que tous les techniciens fussent expérimentés, personne n'a vérifié la rotation. Ils ont terminé les raccordements, ont branché le système et l'ont activé… puis ils ont acheté tout un nouvel équipement de rotation pour le client en aval. Le coût de cet incident ne se compare même pas au coût d'un nouveau 9040 pour chaque personne de l'équipe.
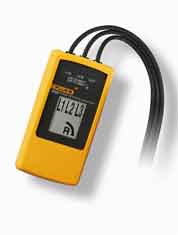
La standardisation avec le Fluke 9040
Un autre fournisseur utilisait d'anciens appareils de rotation mécanique qui étaient la norme dans l'industrie pendant des années, mais qui ont commencé à tomber en panne et des phases croisées se produisaient même intérieurement. Le fabricant a pris son temps pour répondre et n'avait même pas l'air de se préoccuper sérieusement de ce problème de sécurité.
Les techniciens de mesure et de maintenance utilisent désormais des 9040 pour vérifier la rotation des phases sur les nouvelles installations et indiquer la rotation existante des panneaux de disjoncteurs. Plus tard, lorsqu'ils devront effectuer un dépannage après une coupure ou effectuer un remplacement de routine, les équipes pourront vérifier la rotation à la fois avant et après à l'aide des indications et du 9040. L'idée est de s'assurer que le client se retrouve avec la même rotation de phase avant et après l'arrivée des techniciens. Cette vérification se déroule à l'intérieur des transformateurs, au niveau des disjoncteurs dans le panneau électrique, au niveau du pylône pour vérifier les branchements aériens, au niveau des transformateurs aériens, et dans les chambres électriques pour vérifier le dernier point de disjoncteur avant d'alimenter cette source pour le client.
Le responsable de la maintenance du fournisseur s'est pris d'affection pour les équipements Fluke ; selon lui, les produits de la marque ont prouvé leur valeur au fil des années. Il dit des équipements que « leur robustesse est adaptée au secteur. Ils peuvent se mouiller, prendre des coups et tomber des pylônes ou des poches. » Et ils sont faciles à utiliser, ils donnent une réponse par oui ou par non. « Il était temps d'avoir autre chose que ces trucs mécaniques », conclut-il.