Although there are many kinds of heat transfer, radiation is the most important type in relation to thermography. Radiation is the mode by which energy is transferred from the target surface to an infrared camera (also known as a thermal imager). The content visible in a thermal image is almost entirely based on the amount of radiation emitted from or reflected by the surface. No matter the application—from buildings to aerospace, to medical, to industrial—they all present infrared thermography emissivity and reflectivity issues.
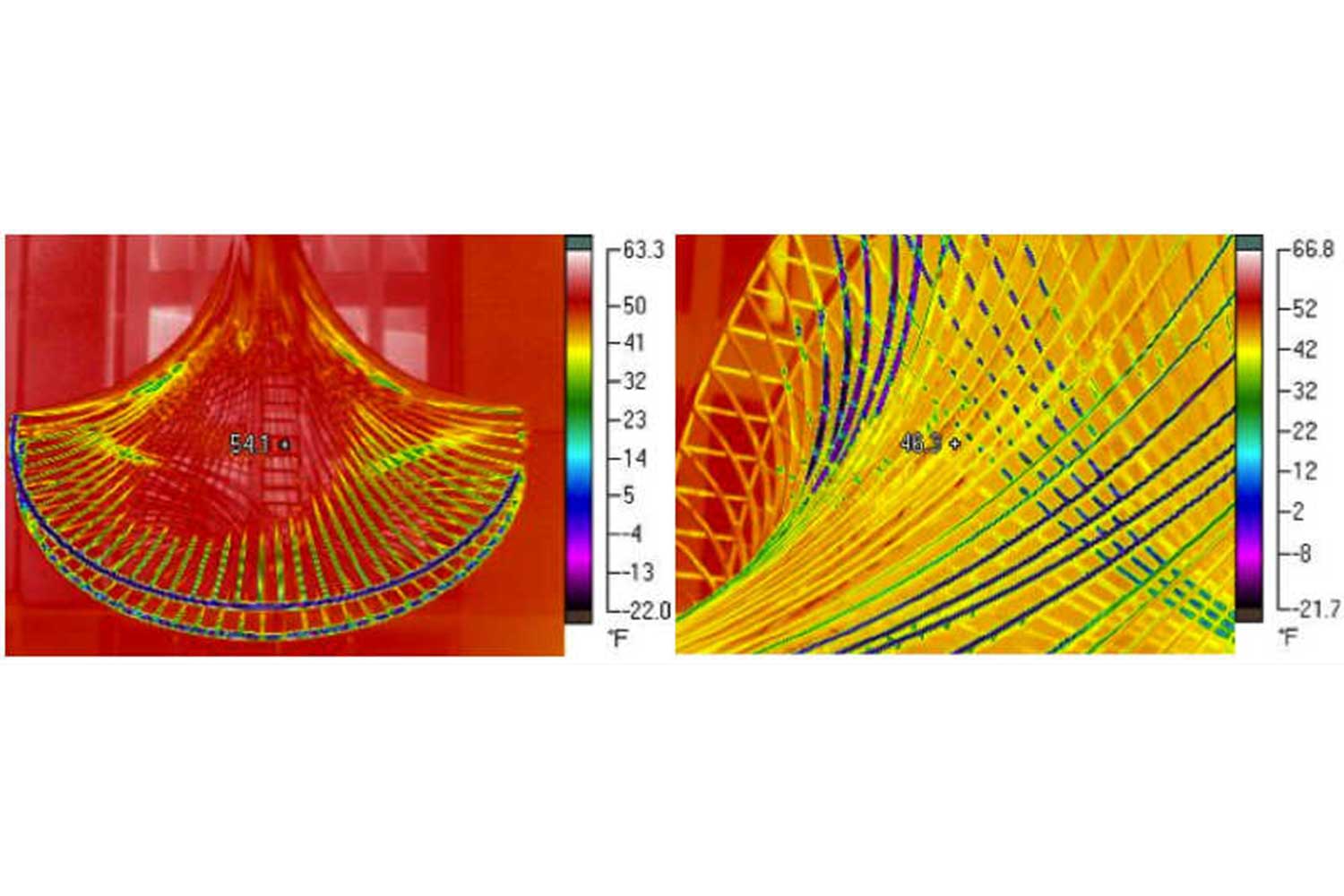
These thermal images are from two different angles of a stainless-steel sculpture located outside on a city street. Looking at it with our naked eyes, we would probably assume that the object must all be the same temperature—the same or close to the surrounding air temperature. The thermal images, however, tell a different story.
Reflective surfaces are inefficient emitters
The presence of reflections is obvious, but as we move our position the objects being reflected typically change. And, as shown in the images above, the apparent temperature we see on the sculpture changes. In these images, we might recognize the cold areas as reflecting the clear sky and the warmer ones as those of surrounding buildings or even ourselves. The reflections are actually “thermal lies,” because the truth about reflective surfaces is that they are inefficient emitters.
Getting to the true temperature
Most of the time it is quite easy to distinguish reflected radiation from emitted radiation because, like a mirror, reflected radiation moves when we move relative to the surface.
When we measure radiometric temperatures, we are only quantifying the radiation that produces the thermal image. So how do we get from quantifying the radiation, to measuring the actual temperature of the object we’re inspecting?
Thermal imagers are calibrated to correlate a temperature with a certain level of radiation intensity. If a surface emitted perfectly, we could easily know its temperature based on how much radiation it emitted. The hotter it is, the more it radiates. Unfortunately, no surface emits perfectly.
Surface Emissivity vs Reflectivity
Opaque (non-transparent) surfaces produce a combination of emitted and reflected radiation. Because the reflected radiation isn’t related to the surface temperature, we must tell the imager to disregard that portion of what it sees. To do that we correct for emissivity (E). Reflection (R) equals 1 minus E. We also need to correct for the temperature being reflected. With these two corrections the imager’s processor can provide an accurate radiometric temperature.
There are two situations where this correction is not as accurate as we would like, such as when:
- The surface being measured has an emissivity of less than 0.6.
- The reflected temperature is extremely different than the surface temperature
This limitation applies to all thermal imaging systems. It means that you cannot accurately measure the temperature of most bare metals. But there is a workaround.
Increasing thermography accuracy on reflective surfaces
When you need high level of accuracy in measuring temperature on low emissivity (highly reflective) surfaces you can apply a small piece of electrician’s tape firmly to the surface (following proper safety practices). Set the emissivity on the thermal imager to 0.95 and the background correction to the temperature of what would be reflected if the tape were a mirror. Following this process you should be able to achieve a measurement accuracy of +/–2°C or 2% of the measurement.
To build your confidence level, try some simple experiments in your office or kitchen, until you are comfortable making the corrections. Let us know how it goes or send us your questions in the comments section.
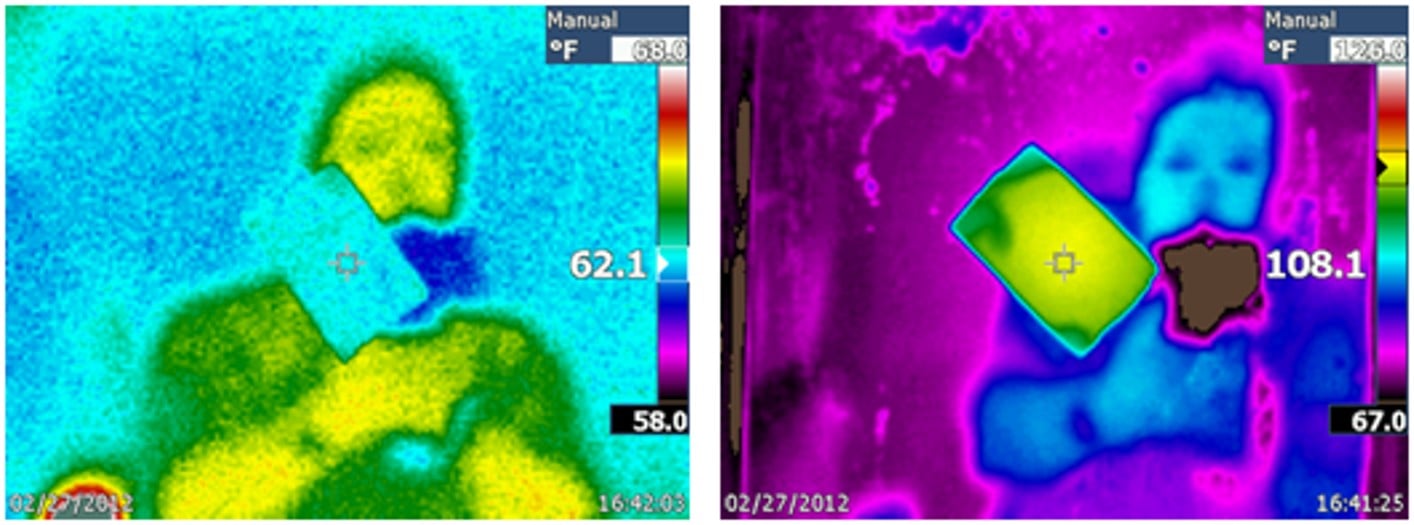
Applying a piece of electrical tape to either a cold window glass (left) or a warm sheet of steel (right) with variable oxidation allows a thermographer to consistently make accurate radiometric temperature measurements. Note both materials are quite reflective. In both cases the emissivity is set for the value of the tape (0.95) with an appropriate reflected background correction value.