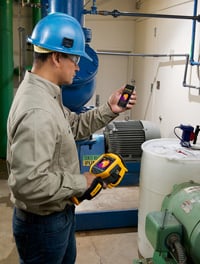
This is not an article about why you should muscle-up and dedicate specific people, time, and budget to predictive maintenance. This article is about how to get excellent asset uptime with the maintenance and reliability resources at your disposal.
The ideal situation is a dedicated predictive maintenance (PdM) or reliability team at a large industrial plant that has identified the most important (expensive) equipment in-plant; uses automated systems or a computerized maintenance management system (CMMS) to monitor equipment and store and track data; determines that sweet spot of exactly when equipment needs maintenance to optimize performance and prevent damage or failure; and has the people, time, and budget to do proactive work.
Then there are the rest of us, with a small maintenance team at small or mid-sized industrial facility with broad responsibilities but not the scope of work or budget to go full SCADA (supervisory control and data acquisition) or to dedicate people to PdM work, applying the best reactive maintenance practices we can manage, including gathering data manually as the job dictates to get the work done and solve problems as they arise.
That team knows its equipment, does some amount of scheduled maintenance, has strong troubleshooting skills, and has a team lead. However, the equipment knowledge and skills are stored in individual heads, so the information sharing part never really happens.
What the rest of us can do
Technology has advanced to the point where maintenance technicians often can use the same techniques and tools to troubleshoot and inspect, log, and share - the basics of proactive maintenance.
Another basic principle is that certain measurements can serve as warning signs of changes in equipment health. By taking those measurements regularly and comparing them to previous records, technicians can detect changes before they become problems.
If we narrow down the list of PdM must-haves to a "rest-of-us" list, it looks like this:
- Know your most important pieces of equipment and their tell-tale measurements/inspection points that inform you about their health.
- Make it standard practice to check those tell-tales and save the data points to a shared location whenever you're working on that piece of equipment, organized by equipment type and marked by the date.
- Check the data-share first whenever you're troubleshooting. It might help you identify the cause faster.
The next step involves management. The team lead can do three things to help make this work:
- Hold lunch-and-learns for the team on the tell-tales and the objective so everyone knows what to look for and feels part of the mission.
- Provide some basic how-to on using simple cloud-based spreadsheets. This helps anyone who's uncomfortable using the technology to learn what to do without feeling embarrassed.
- Share the data logs every quarter and explain what the measurements tell you. This kind of "reason-why" is more meaningful in the context of your own equipment than in the abstract. Help people understand their work makes a difference.
- Check the data share on a semi-regular basis and look for changes that might indicate a problem (in general, when measurements start to deviate by 5 or 10 percent, it's time to investigate).
- Management should be responsible for maintaining, checking, and assessing the data.
- The team should be enabled and encouraged to check the log on the job, not just for data entry; also to check the data history on that system whenever they enter a troubleshooting situation.
- Set up incentives for the team to:
- Speak up if they see something that might fall into a tell-tale category.
- Think of other ways to use the cloud log and data sharing to improve team communication.
Some problems might occur, such as team members won't write down measurements. Another possible problem is that data saved on the measurement tool never leaves the measurement tool - in other words, doesn't get shared with the team.
This is not an article about why you should muscle-up and dedicate specific people, time, and budget to predictive maintenance. This article is about how to get excellent asset uptime with the maintenance and reliability resources at your disposal.
The solution is to use that smartphone or tablet the team members already are carrying or that management has been looking for more ways to use on the job - in fact, work orders are the number one application. Here's how:
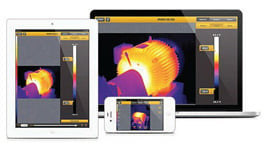
- Convert from the hand-written notebook to a smart device and a cloud-based system such as Fluke Connect®. People like using their smartphones so much, they are more willing to enter data if they can use their device to do it. It's still a two-step process (1. Take measurement 2. Enter into cloud spreadsheet) but it's better than the old three-step involving hand-written notes and data entry back at the office, and the spreadsheet does double-duty as a checklist.
- Use the mobile apps now available for many test tools to more automatically transfer data from the situation to the log and from the individual to the team.
Baselines and tell-tales for motor-drive systems
Proactive maintenance measurements aren't that different from troubleshooting tests. You're looking for signs of potential failure, so you take measurements related to failure modes, and record them.
Establish baseline data points so you know what "good" looks like and so the team lead has a point of comparison for later readings.
Equipment Key Indicators Measurements to Take and to Log Panels / switchboards Intermittent tripping, Hot circuit breakers Voltage unbalance greater than 2%, current unbalance greater than 10%, loose connections, changes inm temperature, increases in load draw Controls Process anomilies, change in system performance Voltage unbalance, current unbalance, inrush current, connection resistance Motors / loads Heat, Intermittent tripping Inrush current, insulation resistance to ground, temperature, overloading, vboltage balance, current balance, resistance, connection motor-start capacitor, mechanical misalignment, imbalance, mechanical looseness, bearing condition Proactive maintenance measurements aren't that different from troubleshooting tests. You're looking for baseline data points related to failure modes. Note: These recommendations are not a complete set of predictive maintenance (PdM) measurements or practices.
- Make quick periodic inspections using carry-along tools such as multimeters, visual thermometers, and vibration pens that are essentially stepped-down PdM tools designed for nonspecialist technicians. Make the following inspections:
- Noncontact temperature: scan the bearing housings on motors, switches in circuit breaker panels, and wiring connections at important equipment.
- Good/bad vibration readings at each bearing location along the drivetrain while the machine is running in a steady state and at normal operating temperature.
- Quick voltage and current checks, against the balance and loading thresholds.
Additional option: incremental wireless
Part of what makes a SCADA system so attractive is the automatic data capture. As your team starts to add proactive maintenance to their thinking, it'll become clear that not every large system in your facility needs active monitoring all of the time. The pinch point comes when a machine, or some of its key components, starts to degrade. At that point you need to order in parts, schedule downtime as needed, and check the system more often.
Some teams have started to use small leave-behind mini-meters that can be locked into the panel and send data wirelessly to a master meter or computer. That way, you can both complete those more-frequent data checks more quickly. In addition, you only need one set of tools that you can rotate around to different systems as needed.