Power Reliability for Facility Managers
In the past, facility managers judged the state of electrical power quality in their facilities based on whether the lights were on or not. If the lights were on, power quality was good. If the lights were off and the occupants were complaining, then power quality was bad.
In the past, facility managers judged the state of electrical power quality in their facilities based on whether the lights were on or not. If the lights were on, power quality was good. If the lights were off and the occupants were complaining, then power quality was bad.
What's harder to identify, and what frequently gets lost in the hubbub, is the potential efficiency gain of improving power reliability and preventing the lights from ever going off.
Thankfully, the potential causes of power reliability issues are well known and relatively easy to identify. A facility manager and electrical team can determine the level of risk they likely face compared to the level of risk they are comfortable with, and with measurement data they can make the best maintenance decision for the organization's bottom line.
Top power reliability issues for facilities
- Unmanaged adds, moves, and changes. Changes in business occasionally require equipment reorganization, from installing new servers to adding new lighting as part of a workstation reconfiguration. These seemingly mundane actions actually impact the overall electrical system.
- Equipment interactions and upgrades. Sometimes different electrical equipment operating together creates unanticipated problems. Common examples of this include installation of new high efficiency lighting or electronic drives alongside older pieces of equipment.
- Backup power. Does the original system design still offer continuous operation and does it engage properly when needed? For critical systems, regular testing is essential.
- Reliability in older facilities. When older facilities were first built, sometimes the only electrical equipment they contained was lighting, elevators, and water pumps. Unless there's been a comprehensive retrofit, the hodgepodge of upgrades has likely set up conflicts between electrical system availability, capacity, and operational requirement.
- Effective electrical system management. By using some basic techniques it's possible to maximize uptime and eliminate the routine power quality problems that can affect facilities that aren't properly managed.
Adds, moves, and changes
Occupant needs inevitably change, whether it's the new medical diagnostic machine or the energy efficient motors and drives. If the electrical department or contractor learn about changes late in the game, then they can feel time pressure to complete the setup and may not assess the current state before implementing the change.
Often everything seems to be working fine, but then the complaint comes in that the new equipment keeps switching off or malfunctioning. Typically this is caused by marginal circuit overloads or disruption from electrically noisy loads on the same circuit as sensitive equipment. What to do?
- Identify changes on the overall electrical system and have electricians assess whether the malfunction is due to the electrical system or to the equipment itself.
- Improve communication between requestors and the electrical service group and allow more time for proper setup.
- Have the electrical service group follow electrical codes, including the guidelines in article 220-35 of the National Electric Code.
The ripple effect of electrical and electronic loads
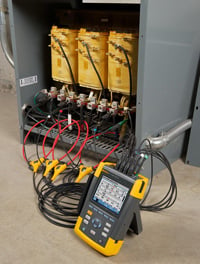
Different types of electrical equipment require different amounts of power at different levels of purity and can output corrupted power back into the system. But conflicts between these different types may only arise when they operate at the same time—at other times during the day, everything runs smoothly.
Common symptoms of equipment conflict include breakers tripping, problems at a certain time of day, and random (seemingly) equipment resets. Without knowing that a conflict between systems or equipment is at fault, the electrician may never actually find the root cause of such an intermittent occurrence and may blame the utility instead.
Managers should imagine a large facility with motors and pumps supporting the HVAC system, all controlled by automation. The automation takes in low-voltage control signals from sensors (temperatures, speeds, pressures) and calculates outputs or control signals that go to the motors and pumps.
As most facility managers know, those low-voltage signals are very sensitive and can be interfered with by the large current drawn by the larger equipment nearby. If they do get interrupted, the control system may misinterpret the signals and provide the wrong directions back to the motor.
In other cases, problems arise from harmonics generated by electronic loads such as electronic drives, energy efficient lighting, uninterruptible power supply (UPS) systems, and computing and telecommunications equipment, all operating at a variety of schedules.
Resolving this kind of problem starts with standardized queries: Where is the problem? Has something changed? When did it change? Why did it change? How do changes in the facility overlap? Facility managers must optimize communication between the affected parties and the electrical staff.
If facility staff members suspect an electrical conflict, the next step is to use electrical measurement tools—either to capture what's happening inside the equipment or to investigate what is going on with the signal itself when the problem occurs. In this circumstance, the electrician will look for the largest load in the vicinity, listen to the way equipment is operating, inspect the connections, and connect his power logger.
Emergency backup power
As a facility manager, you have final responsibility for keeping the lights on. You might not be directly responsible for the electrical, but it helps to understand the priorities.
In facilities such as hospitals, data centers, banks, and public transportation spaces, maintaining constant power is absolutely critical. Other facilities are required to test their power supply for risk assessments or insurer requirements.
The most effective maintenance approach is to regularly test the backup power system. Backup systems are usually comprised of diesel generators and UPS units that provide temporary, instantaneous power to the most critical loads. Like any system, your backup power is only as reliable as its weakest link; testing discovers where that link is.
Generators rely on batteries for startup power, and those batteries gradually weaken over time. Other potential failure points are the equipment controlling the generator and the mechanical parts of the generator set.
Many manufacturers recommend exercising the generator set at least once a month for a minimum of 30 minutes, loaded to 30 percent of the generator's capacity. A facility manager should have the electrician monitor the generator's output voltage, output current, and frequency during the monthly test.
There's also a trend where, as electronic loads within facilities increase, the backup system failure rate also increases. This is due to the way in which the electronic loads take power from the system: these "gulps" of power change frequently—and at a frequency that is not the standard 60 Hz the generator typically uses. Facility managers should have the electrician identify this by measuring voltage, current, and frequency.
Electrical power systems in older facilities
Maintaining electrical systems in older facilities provides additional challenges to standard daily work.
Older power systems were designed to support standard motors and incandescent lighting, not electronics. Modern distorting loads operate differently: 100 amps consumed by modern loads affects the system differently than 100 amps consumed by older equipment. The modern 100-amp demand may create harmonics, which in turn causes conductors and transformers to overheat. This heating effect is exacerbated by the smaller electrical service rooms in older facilities, where heat is not easily dissipated.
Older electrical systems commonly have neutral conductors that are only half the size of the phase conductors. If the loads operating on those circuits contain significant harmonic loads or the loads are not balanced, the neutral can quickly overheat (due to higher neutral currents) and, in the worst case, burn the neutral conductor out.
The latest electrical codes account for these effects and describe appropriate upgrades. If the older part of the facility can't be upgraded, then performing load studies on the older circuits is a good way to ensure safe, reliable operation.
Effective electrical system management
The changing needs of the facility's electrical power system should be considered as a whole, not just at the equipment or circuit level. Facility managers must incorporate communication between teams, take standard electrical measurements on a regular basis, and test critical backup systems. If electronic building controls are here to stay, then managing power reliability issues should become part of standard facility operations.
Go to PDF version of Power Reliability for Facility Managers