Over the last 45 years, Linamar Corporation, headquartered in Guelph, Ontario Canada, has earned a well-deserved global reputation as a world-class designer and diversified manufacturer of precision metallic components and systems for the automotive and energy industries and the mobile industrial market.
In early 2011, the company's Advanced Systems Group (ASG) was contacted by the Linamar Camtac Manufacturing Group about a recurring problem with its compressor motors. It seems that the motors on each of the plant's three 300 HP air compressors had failed at some point within the previous three or four years. The motors were relatively new—they'd only been in service since the plant opened in 2002. They had all been serviced regularly so it was unusual for even one to fail, much less all three in such a short period of time. "One failure is a happenstance; twice is a coincidence; but the third time it happens you figure there's something else afoot here," says Leigh Copp, Chief Engineer and Business Unit Manager for the Linamar Advanced Systems Group.
The cost to get the motors rewound averages between $6,000 and $8,000 each. Then there's the downtime cost. "If your facility has to have unscheduled downtime while you change a motor out, you can easily lose tens or hundreds of thousands of dollars in a shift," Copp adds.
In addition to the cost, a sudden compressor failure can be contagious. The resulting low air pressure faults can cause failures of other machinery in the facility. "We need three things in a typical facility to run: electricity, compressed air, and cooling water," says Copp. "If any one of those goes out you're shut down and it can be a very expensive failure."
Linamar was lucky. Since the motors failed at different times, the crew was able to work around the repairs. But by the time the third motor went down, Camtac turned to the ASG for help in finding the cause of the problem. The ASG oversees and troubleshoots particularly complex problems throughout the company's 25 plants in the Guelph area as well as those in the United States, Mexico, Germany, Hungary, France, and China.
Following the clues

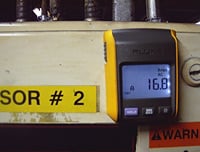
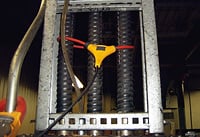
Power enters the the Camtac plant through a 5000 kVA transformer that supplies a 5000 A, 600 V main service. From there 1200 A subservice feeds are distributed throughout the plant, including the one that powers the three compressors in question. The cable tray for the subservice feed holds two parallel runs of single conductor cable for each of three phases and one grounding conductor in the middle of the tray.
Copp and his team started their investigation with the compressor motors using a Fluke 381 Clamp Meter with iFlex™ to measure voltages and currents. "We found that there was a very small unbalance—maybe 1 percent to 2 percent—in the motor voltage but almost a 10 percent unbalance in the motor current, which could cause significant overheating," says Copp.
The engineers were a bit mystified because, typically, a 1 percent voltage unbalance doesn't result in a 10 percent current unbalance. They measured the voltage at the main service and found that it was very balanced—the 1 or 2 percent unbalance in the subservice was not present at the main service. They investigated further using the Fluke 345 Power Quality Clamp Meter to look for harmonic content in the motor current, but found very little harmonic distortion. They also tested the compressor motor insulation with a Fluke 1550B digital insulation tester and found no deterioration or other problems with the insulation.
Then they compared newly rewound motors to the in-service motors and found the phase-to-phase resistance was much better matched on the new motors. That led them to believe that the in-service motors were being subjected to some kind of heating effect that damaged the windings.
Detecting high ground current
Moving from the motors to the subservice, the team found a very high ground current—about 160 A—flowing in the bond wire between the 1200 A subservice and the main service. "Although 160 A is permissible, typically there shouldn't be any ground current flowing unless you have leakage," says Copp.
The team then verified that the neutral tap was solidly bonded and that all of the ground bonds were in good shape. They also used the Fluke 1625 GEO Earth Ground Tester to verify that the ground grid was present and functioning properly.
However, when they measured the ground currents flowing from each air compressor through the cable trays and through the metal air pipe, using the Fluke 381, they found more bad news. "Those measurements revealed multiple ground paths with a significant amount of current flowing from each compressor," says Copp. "We used a Fluke ScopeMeter® 190-204 with four Rogowski coil current transducers to measure the magnitude and phase of the components of the ground currents that were flowing in the conductors and the adjacent cable tray. It became clear that some inductive effects were contributing to the ground current and that these currents might contribute to the voltage unbalance on the subservice."
Measurements at the main service showed almost 200 A of ground current flowing through the various grounding wires at the service. At that point they couldn't go any further until the next scheduled plant shutdown. In the meantime, Copp and two other engineers spent a lot of time at whiteboards sketching scenarios and analyzing where the current likely came from. They suspected that they had a ground loop in which the ground current was induced by phase currents.
Testing the suspected cause
At the end of December 2011, Copp and his team used an eight-hour shutdown at the Camtac plant to conduct as many static tests as possible to ferret out the problem. They verified that there weren't any broken strands in the cable that ran between the subservice and the main service. They measured the resistance of the parallel runs of cable with a micro ohmmeter and found that they were all closely matched. They also removed and cleaned all of the ground, bond, and phase conductor connections.
After the plant was returned to service, however, there was still an elevated ground current present.
Based on the tests conducted during the shutdown, the ASG team concluded that the problem stemmed from the arrangement of the conductors between the main service and the 1200 A subservice. "We believed that the bonding conductor was placed in the wrong physical location in the tray, resulting in an interaction between the ground conductor and the phase conductor magnetic fields, which in turn caused ground current to flow," says Copp. "The ground conductor was placed according to best practices from cable manufacturers and the NEC/CEC codes, but this investigation suggests that those practices may need to be reexamined."
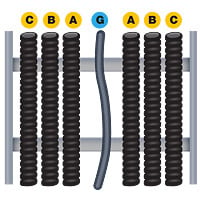
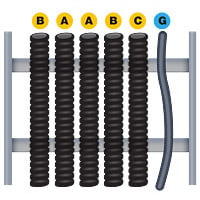
Through further testing, the ASG team and their counterparts at Camtac hypothesized that moving the ground conductor close to the side rail of the cable tray would help mitigate the induced ground currents. But that would require shutting down power to the compressor feeders. So once again they waited for a suitable window when production could be suspended for a few hours. A few months later that opportunity appeared and the Camtac engineers took care of the relocation.
Immediately after the power was reconnected, the engineers measured both the ground and side rail currents.
A significant reduction in ground current was immediately apparent after relocating the ground conductor," says Copp. "We continue to monitor the system to see if the longer-term effects are improved and the degradation of the motor windings is reduced. So far we've seen no increase in ground current, and no further compressor motor failures. We are continuing to monitor the installation to see how the motors run over time."
Equipment | Current | |
---|---|---|
Before relocation | After relocation | |
Grounding conductor | 160 A | 45 A |
Cable tray side rail | 70 A | 20 A |