What is a vibration sensor?
A vibration sensor, or vibration detector, measures vibration levels in machinery for screening and analysis. Maintenance teams use industrial vibration sensors for condition monitoring, giving them insight into the magnitude and frequency of vibration signals. Vibration sensors often provide overall vibration levels, indicating whether your asset is under stress, but they can also give more sophisticated readings. Best-in-class industrial sensors like the Fluke 3563 Analysis Vibration Sensor go deeper. The Fluke 3563 distinguishes vibration signals from individual components and identifies what common faults are associated with their vibration levels: bearing faults, looseness, imbalance, and misalignment.
Vibration sensors are ideal both for monitoring applications – getting instant notification when faults occur – and more in-depth analysis that vibration experts can do with trended vibration data, often to diagnose complex vibration patterns or mysterious faults.
What is a wireless vibration sensor?
A wireless vibration sensor sends data to your systems with IoT technology – you can simply place the sensor on the asset, and the sensor will transmit vibration data to your systems. Wireless vibration sensors take measurements and transmit data on a set cadence. They don’t give you a continuous stream of data, like on-line vibration monitoring systems, but they do provide quick and precise measurements. You can forgo labor-intensive manual or on-line monitoring.
How does a vibration sensor work?
Vibration sensors capture vibration data with the help of sensing components like accelerometers. The most precise accelerometer technology is piezoelectric crystals: when the crystal is under stress, the signal from the sensor modulates, recreating the vibration occurring on the equipment under test. Vibration analysis software parses these signals for the frequency and intensity of vibration.
Vibration sensors are often also called vibration detectors, a term that refers to a broader category of vibration measurement and monitoring equipment.
What is a vibration detector?
A vibration detector is a device that measures changes in the vibration levels of your rotating equipment. Some vibration during operation is normal, and every piece of equipment has a certain vibration baseline or signature. However, changes to an equipment's normal vibration pattern is often the first indication of a problem.
Even relatively small changes in vibration frequency can point to an imbalance, looseness, premature wear, or other fault. Vibration detectors are sensitive enough to pick up on changes that a human might miss.
Vibration detectors are an integral part of condition monitoring and predictive maintenance. Done right, vibration monitoring can help you identify machine faults early so that your maintenance crew can resolve small maintenance issues before they become bigger problems. Over time, this can create a major shift throughout your plant. You’ll see an overall improvement in asset health, as well as increased uptime and productivity.
What are the types of vibration detectors
- Accelerometers: An accelerometer measures changes in velocity and converts them to electronic signals. The most popular type of vibration sensor.
- Handheld Vibration Analyzers: A vibration analyzer is handheld meter that often incorporates other vibration sensor technology to provide instant readings, perform measurements in the field, and take readings for later vibration analysis.
- Eddy Current / Capacitive Displacement: Eddy current sensors allow you to measure displacement without touching an asset. The sensor measures displacement by generating magnetic fields to measure relative motion.
- Laser Displacement: Laser displacement is another no-contact method for measuring vibration, triangulating the displacement of an asset with laser beams.
- Strain Gauges: A strain gauge is a foil with a conductive grid. When the asset under test vibrates, the grid’s resistance changes – undergoing “strain.” This strain helps to measure vibration
- Microphones: Microphone sensors detect vibration with advanced acoustic techniques, measuring frequencies of vibration that might otherwise be difficult to detect. They are generally not sophisticated enough to measure values or determine sources of vibration.
- Gyroscopes (MEMs): A gyroscope determines velocity and is often used in conjunction with an accelerometer for vibration measurement.
Why integrate industrial vibration sensors?
While including vibration sensors in industrial maintenance programs may seem like a daunting task, it has never been easier to screen assets for abnormal vibration. With vibration monitoring, simply install the sensor and start receiving data. With the right vibration sensor, you will have the information you need to make data-driven decisions.
Access data in the plant or across the globe by adding wireless vibration sensors to your maintenance and reliability program. Cloud-based software stores data and enables analysis, giving you actionable insights concerning asset health. Vibration screening is an economical way to monitor more assets by automating data collection, furthering your team’s predictive maintenance journey.
Nearly 90% of machinery benefits from condition monitoring. By including sensors in your industrial maintenance and reliability programs, you and your team will have a clear view of asset health and efficiency.
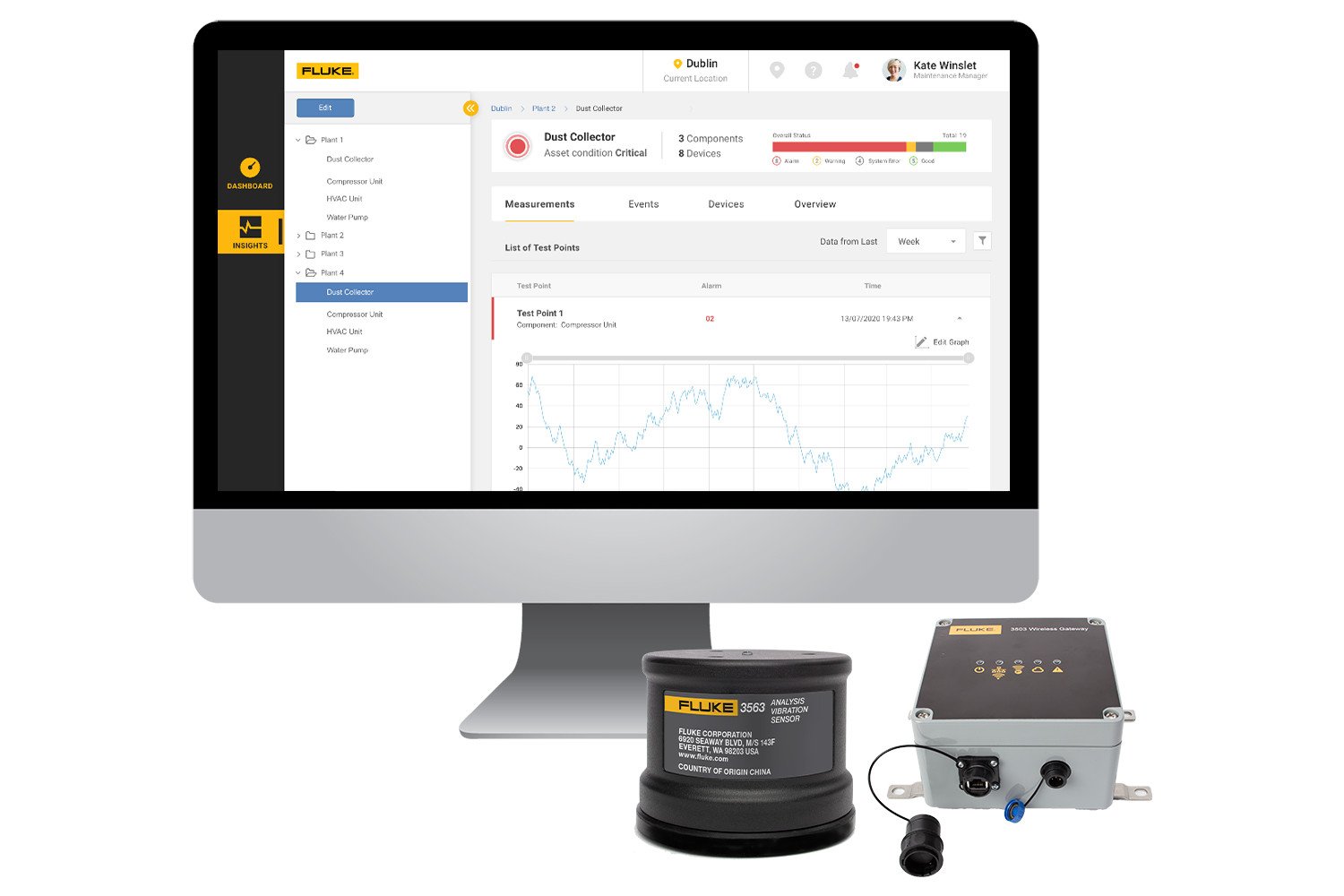
Where are vibration sensors used? Top 5 applications
HVAC Systems
Fans and compressors are critical for ensuring that HVAC systems work properly. View remote measurements on smart devices while remaining at safe distances from the assets. Keep air flowing and machinery cool by installing remote vibration sensors, helping your team pinpoint problems before they occur.
Food & Beverage
Gearboxes, chillers, and rollers drive Food & Beverage operations. Downtime in these systems can cause a ripple effect through the entire production line. Real-time and historical data collected from the assets can be trended and analyzed.
Water & Wastewater
Pump downtime in water distribution and wastewater plants not only has financial costs, but more importantly, it negatively impacts customer access and water quality. Installing vibration sensors on a greater number of assets helps water plant teams move more maintenance in-house, reduce costs, and minimize time-based routes.
Oil & Gas
Oil & Gas operators have facilities in remote places that experience weather extremes, dust, and sand. Engineers and technicians need rugged technology to live up to the rigors of these locations. Instead of traveling to outlying sites, you can see asset status from your monitor in real time.
Automotive
Scaling condition monitoring programs for enterprise-level facilities may seem cost prohibitive, but it doesn’t have to be. With a multitude of assets, cost-effective installation of vibration sensors is key. Sensors that are easy to install and use enable teams to extend coverage throughout the plant or even multiple locations.
A vibration sensor solution for all industrial applications
Using the Fluke 3563 Analysis Vibration Sensor system simplifies vibration monitoring. It combines a high-frequency piezoelectric sensor with insightful software analytics, while smart battery management lets teams extend the sensor’s battery life while still getting the data they need.
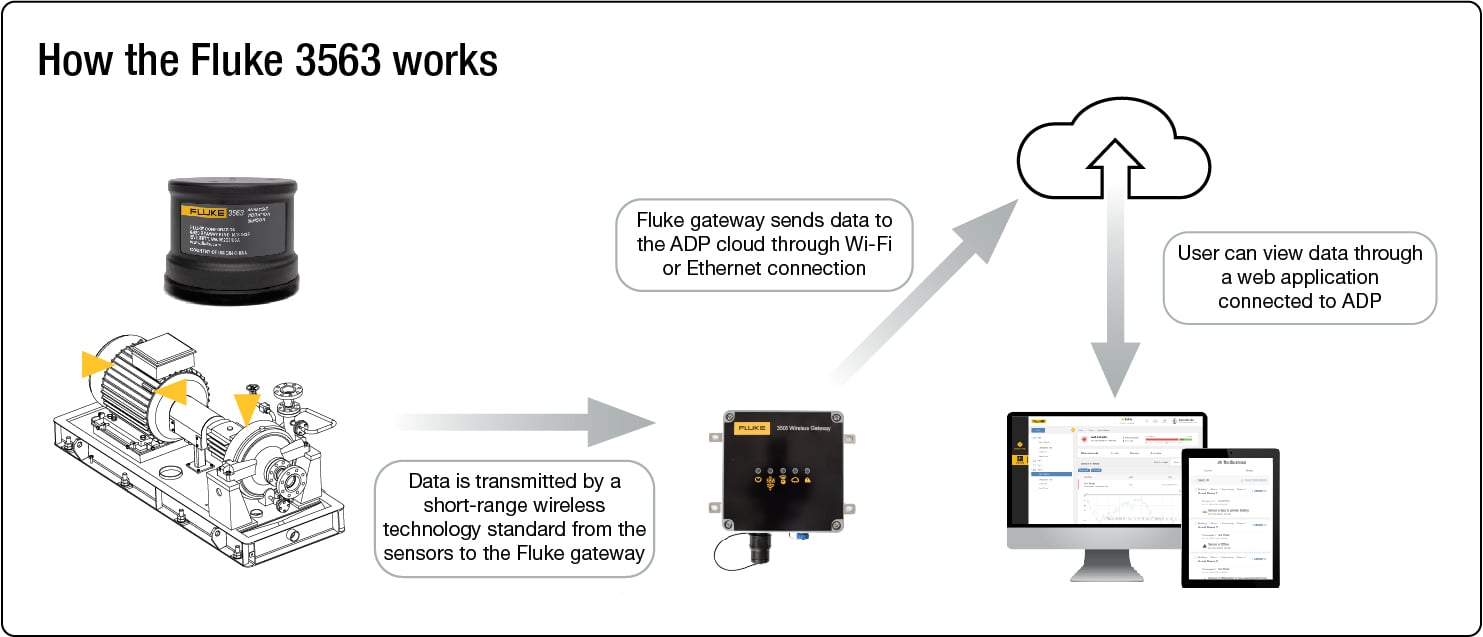
The eMaint Condition Monitoring software application is highly customizable and enables teams to identify the cause of faults and determine their next-step actions. The end result is extended peak operating performance and more efficient use of maintenance team resources.
The Fluke 3563 can be implemented into plants seamlessly, and the one-on-one setup and vibration training services enable teams to get results right away. The Fluke 3563 Analysis Vibration Sensor system is a solution that combines three core parts: hardware, software, and service.
Including industrial vibration sensors in your facility means your maintenance team can deliver more business value.
To learn more about the Fluke 3563 Analysis Vibration Sensor and how vibration monitoring will improve your predictive maintenance program, regardless of your industry, please call our sales team or visit our vibration monitoring page.