Anyone who works with electrical or electromechanical equipment knows that safety is important. But defining specifically how to achieve a safe work environment requires a broader perspective. There are all kinds of rules and standards governing best practices in the workplace that professionals must learn and follow. And there are standards for the tools used by those professionals to do their job. But when it comes right down to it, where does the buck stop when it comes to safety?
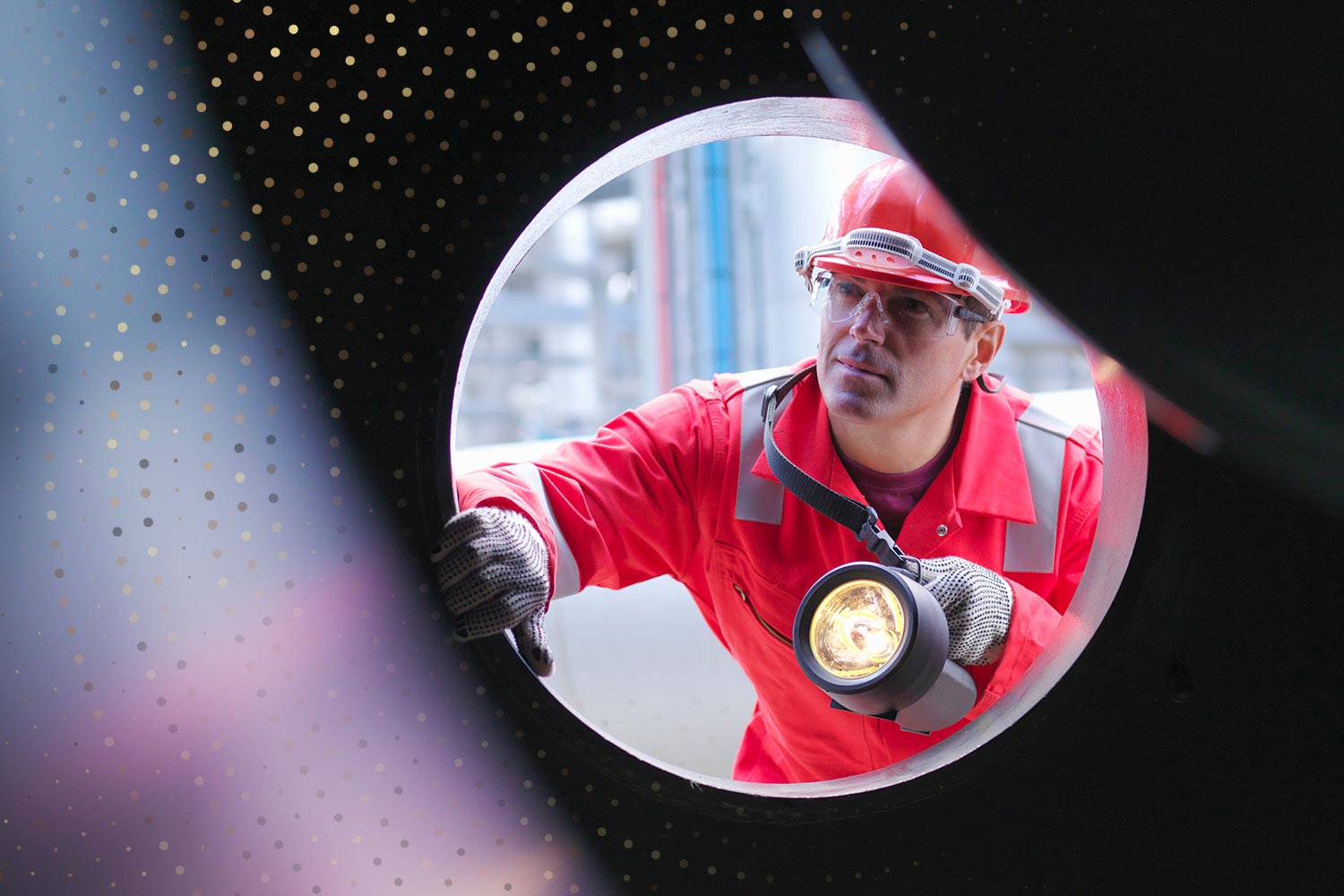
To heat the newest information from Fluke customers, we recently ran our fourth annual Safety survey. The survey received responses from a range of industries and job titles including electricians, engineers, technicians, mechanics, research scientists, safety instructors, and beyond.
Respondents came from all around the world, from every state in the US to many regions around the world and ranged in ages from 18 to 75+. Opinions varied on many of the issues and questions asked, but there was a consensus around a couple topics. All centering around: a strong culture of safety in the workplace is important to keeping worker safe. The opinions of how well companies are achieving that goal tended to be less positive.
However, there seemed to be a consensus among survey respondents regarding who is most responsible for workplace safety (individual workers) and least responsible (HR). While those opinions reflect respondents’ real-world experience in the workplace, there are clear lines of responsibility spread across multiple groups for creating and maintaining a safe and healthy workplace.
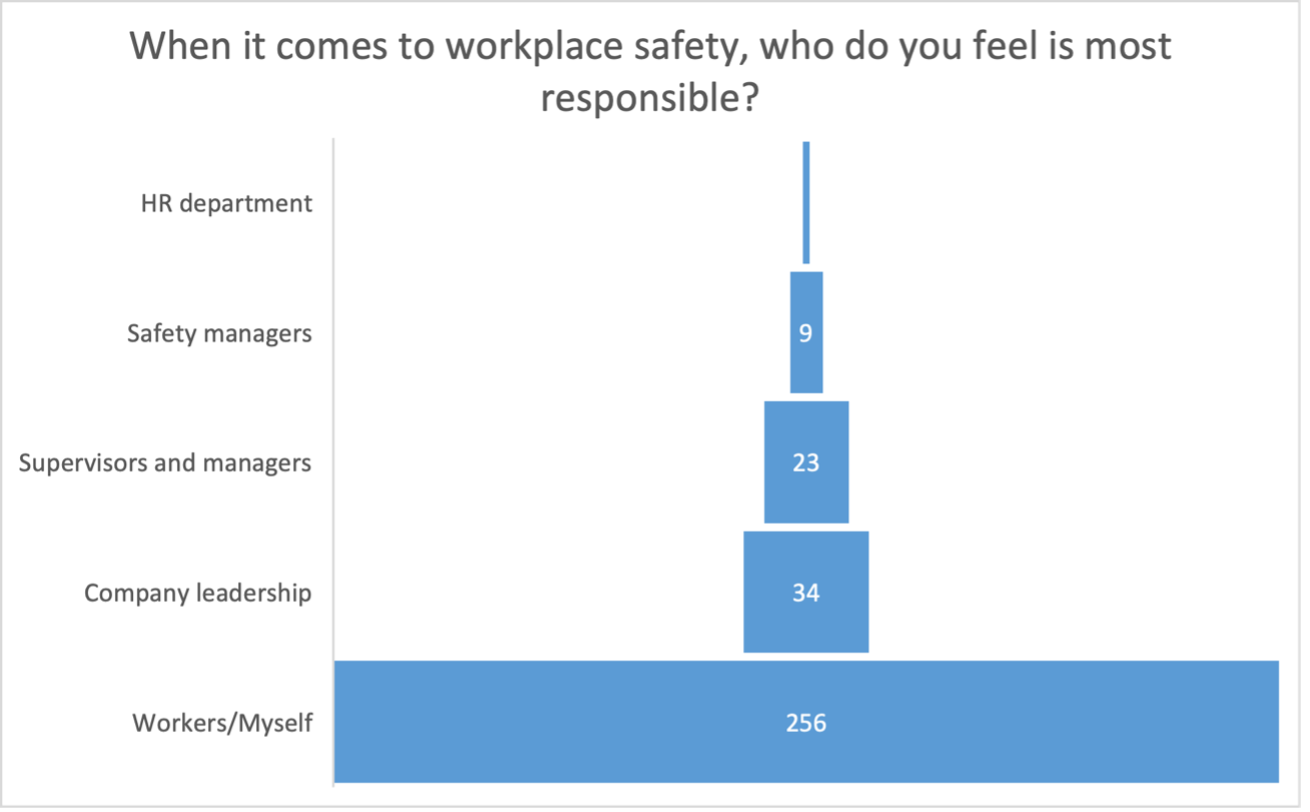
Workplace safety is everyone’s responsibility
Human Resources: HR was regarded as having the least day-to-day responsibility for workers' safety in the 2023 Fluke Safety Survey. This is a trend that has continued since the first safety survey in 2020.
However, HR is not free of all safety responsibilities in a workplace. The team plays a role in helping to create a culture of safety. From setting hiring policies, to exercising due diligence at each step in the hiring process to verify applicant qualifications, HR plays holds a responsibility in creating an environment conducive to workplace safety. They can start by establishing a safe hiring program that helps them avoid bad hiring decisions that can result in legal and financial risk. HR safe hiring resources are available from the Society for Human Resource Management.
Safety Manager: Safety Managers are responsible for the big picture on safety. They create policies, based on the latest safety research, to eliminate workplace hazards. And they train employees to make sure those policies and procedures are followed. The need for training came up frequently in comments made by Safety Survey respondents. Many respondents disagreed with the statement that most companies provide adequate electrical safety training. In fact, only 30% strongly agreed or agreed that companies are providing enough or the right safety training. One respondent noted that “most companies talk safety but are unwilling to pay for the training or pull guys out of the field for the training because it affects profits and job progress.”
Safety Managers advise the company’s administrative team to help avoid situations like that. They maintain accurate up-to-date records to document the company’s compliance with relevant safety regulations and document and investigate circumstances related to workplace accidents and illnesses. Based on the results of those investigations, safety managers may recommend changes to management to create a safer working environment.
“Ensure direct Supervisors enforce the safety culture under a "no pressure" policy. Contracts have deadlines and penalties which supervisors are afraid to encroach upon, so safety often goes unenforced for the sake of production.”
Supervisors: Survey respondents chose supervisors, second only to individual workers, as those most responsible for safety. Supervisors bear the day-to-day responsibility for maintaining the wellbeing and productivity of their employees. Part of that responsibility is to make employees aware of the training required to do their jobs and to make sure they take the training and safety measures seriously.
Supervisors need to make sure they are assigning tasks to appropriately qualified workers and strive to create a culture where following safety procedures is automatic. Above all, supervisors must create an environment where employees feel comfortable reporting unsafe workplace conditions without fear of reprisal.
“The culture of safety needs to start from the very top and be applied in every layer of the ‘command structure.’ Fine words and spreadsheets do nothing if the actions in the field are not monitored, and safety is not culturally enforced in any way.”
Company Leadership: In a break from previous years’ survey results, the 2023 respondents put Company Leadership as the third most responsible party when it comes to workplace safety. The sentiment from the comments gathered point to a need for less pressure to complete jobs quickly and a need for more training to come from company leadership.
In the US, private sector employers must comply with Occupational Safety and Health Administration (OSHA) standards for maintaining safety in the workplace. Established by federal law in 1970, OSHA sets and enforces standards and provides training and assistance to ensure safe and healthful working conditions for US workers. In addition to protecting private sector employees, OSHA standards provide the basis for similar protections for many public sector employees. Beyond simply complying with regulations, company leadership needs to make safety a core value. They need to communicate with employees at all levels—rank and file and management—that working safely on every task is the company’s highest priority.
“Safety begins with me. I am responsible to make sure that what I am doing is safe. Having the correct tools, clothing and area to work is up to me to use them.”
Individual Workers: A vast majority of survey respondents agreed that individual employees carry the most responsibility for their own safety in the workplace, 79% responded with workers/myself. No matter how many safety policies are established, or how much PPE is provided, if workers don’t follow those safety procedures and wear the proper PPE, the policies are of no use.
While there are always temptations to cut corners to complete tasks faster or not wear all the required PPE due to time constraints or discomfort, in the end it is each individual’s life on the line. Here is a brief reminder of some common practices that can improve safety in the field:
- Always follow proper lockout/tag out procedures
- Always properly inspect test instruments and test leads for damage or contamination.
- Always verify proper operation of test tools. Conduct an operational readiness test or absence of voltage test, as outlined in NFPA 70E 110.4(A)(5).
- Do not use outdated or defective test equipment. Today’s test tools contain new safety features that can help prevent a trip to the emergency room.
- Always use test tools that are properly rated for the job at hand. Make sure your test tool holds the correct CAT rating for each job you do.
- Always replace original fuses with the same kind of authorized fuse
- Do not work on a live circuit, unless absolutely necessary. If you have to work on a live circuit, use properly insulated tools, follow all preparation procedures, and wear proper PPE.
- Use well maintained tools and appropriate PPE according to NFPA 70E. Wear appropriate safety glasses, use insulated tools, insulating gloves, arc-rated closing, arc shields, flash suits, insulating mats, etc., as your worksite calls for it.
Multiple respondents shared similar sentiments when it came to safety being their own responsibility first, but that the rest of the team played a role as well. Safety is a team effort.
- “It's everyone's job to keep each other safe. If another employee is being unsafe, call them out on it. I fully expect all employees to watch out for each other and keep each other safe.”
- “All employees have a role to play when it comes into workplace safety. Safety at a workplace is dynamic thus we ought to be updating ourselves”
- “Everyone present at a worksite is responsible for workplace safety. Safety Officers are good for larger areas and, ultimately, managers and other Monday-morning quarterbacks. By the time an incident reaches that point its more about placing blame and liability.”
Over the past four years of running this survey, the responses have seen a clear shift from who is considered most responsible. Each year, the percent of respondents who have said someone else is responsible for their safety in the workplace has decreased considerably. The first year we ran this survey, in 2020, 50% of respondents said someone other than “workers/myself” was most responsible for workplace safety. In 2023, only 23% said someone else was most responsible.

Safety standards and compliance
In addition to OSHA, there are several organizations that create safety standards for tool and equipment manufacturers. These include the International Electrotechnical Commission (IEC), National Fire Protection Association (NFPA), and the Canadian Standards Association (CS A), to name a few.
One of the most critical standards for electrical test equipment is the IEC 61010 product safety standard that establishes Measurement Category (CAT) and voltage ratings for electrical environments. These ratings (CAT II, CAT III, and CAT IV) identify the voltage transient level that electrical test tools have been designed to withstand. The higher the CAT rating the higher the level of voltage the tool has been rated for.
An interesting note about safety standards for tools and equipment is that the standardization bodies are not responsible for enforcing them. So, in addition to complying with the standards in designing and manufacturing the tools, each manufacturer should have its tools certified by at least one independent testing agency such as CSA, Underwriters Laboratories (UL), TÜV (Technischer Überwachungs-Verein), and ETL/Intertek.
Fluke has its own Product Compliance Laboratory where, as part of the development process, a team of safety engineers tests Fluke tools to at least one level beyond the standards. This allows Fluke to find design weaknesses or errors so they can be corrected in the final instrument.
The Fluke Product Compliance Lab is regularly audited to ensure that it meets the requirements of the national and international testing authorities and standards.
To learn more about the state of safety in today’s workplace review the results from the 2023 Fluke Safety Survey.