How a pressure balance works
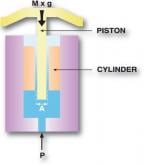
Imagine for a moment you are Bob. Bob lives in New York and recently purchased a deadweight tester from a gentleman in South Carolina. The deadweight tester came with a certificate of calibration, but the instrument appears to read 0.5 to 0.6 psi off when calibrating his 0.05% 1,000 psi gauges. Bob scratches his head, then double checks the gauges with the older equipment he is replacing. The gauges read well within tolerance on his old equipment. Bob is not happy. Can you blame him?
Bob spent a lot of money on his new deadweight tester and it is effectively useless. Or is it? Bob tells his friend Jeff about his lousy luck. Jeff asks Bob if he is correcting for local gravity. “Yeah right,” Bob laughs. But Jeff isn’t laughing. “You know differences in local gravity can easily account for the error you’re seeing, right?”
Bob overlooked the basics of pressure calibration. He assumed that a deadweight tester that is certified in South Carolina would still be in tolerance in New York, and it came back to bite him. Don’t worry, though. There is still hope for Bob and his deadweight tester, but I’m getting ahead of myself.
A deadweight tester is basically a pressure balance. A pressure balance is a very elegant solution to the pressure measurement problem. So how does it work?
Pressure is fundamental
Actually, it’s not. Pressure cannot be described by a single variable like length, time, temperature or amount of substance. Pressure is force per unit area. So what we have to do to get pressure is combine the units of length, time, and mass. The unit of pressure is the Pascal (Pa), which is defined as 1 kg*m/second2. That’s actually a very small amount of pressure. Atmospheric pressure is about 100,000 times larger than 1 Pascal. But sometimes little things can mean a lot.
How a pressure balance works
When we use a pressure balance, we are looking for the equilibrium between a downward force and an upward force. The downward force is that of a mass being accelerated by gravity. The upward force is directed by the pressure we are measuring onto the effective area of the piston, which is pressed downward by the mass. When these two forces are equal, they counter balance each other.
When the forces counter balance each other in this way, the mass will float. The trick is to know the exact force applied by the mass and the effective area in contact with the pressure we are trying to measure. Then we can calculate the pressure.
The floating piston
The beauty of this method is related to the floating mechanism. When the piston floats, it compensates automatically for a number of potential errors in our measurements. For example, we could have a leak, but instead of causing the pressure to drop the piston floats a little lower. The temperature of the medium could rise, but instead of causing the pressure to rise the piston floats a little higher. However, if the pressure actually rises or lowers then the piston no longer floats.
You may be thinking “Wait a minute, what about friction? Won’t friction between the piston and the inside walls of the chamber cause a measurement error?” You’re correct, friction is important. But the solution for friction is as elegant as the pressure balance itself. We have to spin the piston. When the piston spins, it ensures that friction will be minimized.
Deadweight tester assumptions
The type of pressure balance commonly used in industry is called a deadweight tester. Deadweight testers define pressure based on a couple of assumptions. The two big ones are:
1. Piston cylinder temperature
2. Local gravity
The pressure value determined by a deadweight tester is the result of summing the pressure values assigned to the loaded weights. Typically the weights will have a value stamped or engraved on them. The weights are called platters. When you take that platter, put it on the matching piston, and you float it, you are going to define nominal pressure as the value stamped on that platter.
However, to maintain the certified accuracy of the deadweight tester, you have to keep the environmental temperature within the stated limits of its assigned reported temperature, and you have to be at the same local gravity that the platters were manufactured and trimmed for. It is local gravity that caused big problems for Bob, and it is the single most significant source of uncertainty for a deadweight tester.
The gravity of the situation
Many people don’t realize that standard international gravity is defined at 45 degrees latitude north or south of the equator at sea level. It has a value of 9.80665 m/s2. Phoenix Arizona is closer to the equator than 45 degrees latitude, and the value of local gravity is 9.79474 m/s2. The difference is more than 1200 ppm (0.12%)! An industrial deadweight tester is typically specified to around 150 ppm, and with quality hardware and the right corrections you can even do much better than that. But if you fail to take into account local gravity, you don’t stand a chance.
So, what about Bob? It turns out Bob could apply a correction to ensure that his values are accurate. Using a ratio of his local gravity to the gravity his deadweight tester was originally designed for, he can make corrections to the pressure stamped on his platters. Of course there is more to life than pressure measurement, but if something is worth doing, it probably worth doing right.