5 ways test tools can improve safety around rotating machinery
Application note
The electrical hazards associated with electro-mechanical equipment are severe and the electrical safety PPE requirements are extensive. But what about safety concerns from the mechanical side of rotating machinery?
The three main objectives of mechanical safety are:
- Perform work from a safer distance from rotating parts and reduce number of entries/exits
- Take faulty machinery offline BEFORE a hazardous condition occurs
- Increase the safety of maintenance tasks and prove compliance by using correct tools
How to work more safely on moving parts
When the situation calls for working near operational machines with moving parts, take every opportunity to be as safe as possible.
1. Be very careful of moving shafts and other components
Wear safety glasses and other PPE. Never wear dangling lanyards or necklaces. Make sure that cables are equipped with the proper breakaways in case a cable is dropped into a moving shaft.
2. Work from a distance, further away from potential danger
If you need to get a part number from a moving machine or measure the speed of the rotating shaft, don’t use your tachometer. Touching the moving shaft is too
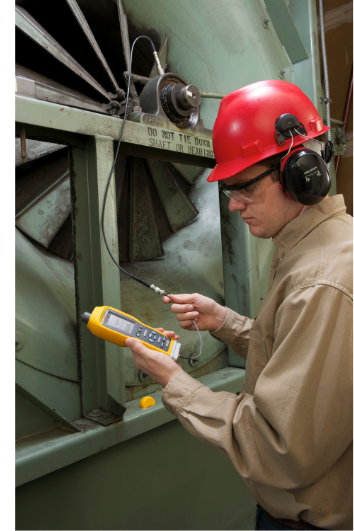
risky. Use an LED stroboscope, instead. The LED stroboscope “freezes” motion to measure speed, read information from moving parts, or identify potential problems without stopping the machinery or endangering personnel.

3. Use wireless tools whenever possible
Cables from tool to the sensor often get in the way during test measurements. And, the longer the job takes, the more time accidents have to happen.
A wireless tool doesn’t have cables
and can stay away from the immediate work area. Smart tools are designed for maximum efficiency. They walk the user through the task quickly and easily, reducing the time in the danger zone.
4. Identify faulty machines before failure
There are many ways that machine failure can cause an accident or a health and environmental problem:
- Catastrophic failure of machine causes injury to nearby personnel by release of moving parts
- Simple failure of machine releases product to environment–very high temperature, caustic chemicals, bio hazardous sewage or other, flammable material, etc.
- Secondary damage of machine leads to structural or foundation failure leading to injury
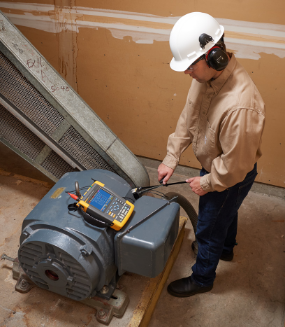
Use a vibration meter to regularly screen rotating machinery, looking for early warning signs of potential failure. Add the vibration meter to operator inspection routes and take the 30 seconds to verify machine conditions haven’t deteriorated.
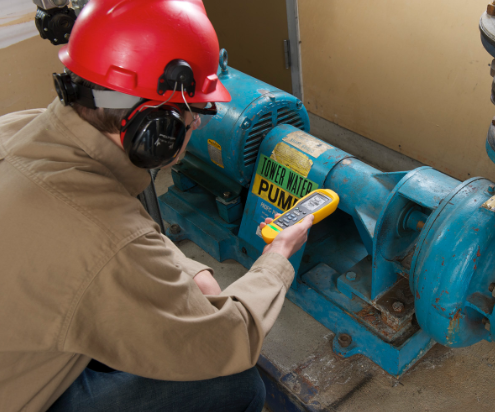
5. Quickly evaluate the risk associated with machine faults
If you do identify a change in severity of machine fault, you’ll need to quickly determine whether the fault is moderate (you still have months to go) or extreme (it could go at any time). A bear¬ing that is ready to fail can lead to a catastrophic failure that destroys the entire shaft, the entire machine, stops production, leaks caustic materials, or injures someone nearby.
Facilities running large mechanical equipment increasingly use vibration testers to diagnose the most common mechanical faults. The tester assesses the fault level and provides a detailed report of the fault, including the severity and the repair recommendation.