Nel risparmio energetico, c'è prima l'obiettivo e poi c'è un piano. Gli impianti industriali degli Stati Uniti manifestano un interesse continuo nella gestione dell'energia. Questo è l'obiettivo: Ridurre il consumo energetico complessivo o l'utilizzo continuato, ma aumentare la produzione per kW utilizzato.
Il piano? A volte è un problema.
Nella produzione, un piano rimane valido solo se dispone sia della saggezza dettata dall'esperienza che guida la visione, sia i numeri del ROI atti a sostenere l'impegno. Tuttavia, in ambito energetico non ci sono solo gli studi che il responsabile di un impianto industriale può utilizzare per definire il riferimento di un consumo energetico "ragionevole" in uno stabilimento di produzione. Quindi, come valutare quale porzione dell'attuale consumo energetico è ragionevole e quale costituisce uno spreco o in quale misura tale spreco influisce sul ROI tanto da dovere essere affrontato?
Il ROI in questione è il costo per kWh addebitato dal fornitore di energia. Queste unità di consumo hanno una tariffa diversa a seconda del periodo del giorno e dell'anno. La riduzione di tale spesa costituisce il risparmio. L'investimento è costituito dai materiali e dalla manodopera necessari per modificare il consumo energetico. Il ritorno è il periodo di tempo necessario perché la riduzione dei costi energetici ripaghi l'investimento. Il guadagno inizia una volta ripagata la spesa.
Tornando al problema del piano, come si ottiene una stima del ROI quando non esiste uno standard industriale per un consumo energetico ragionevole?
Analisi del consumo energetico industriale
Il consumo energetico industriale varia in funzione di molteplici variabili:
- età dell'impianto
- tipo ed entità del carico
- programma operativo, che include sia ore alla settimana che intensità di carico
- numero di lavoratori
- clima
- filosofia di manutenzione.
La risposta è: non cercare di gestire ogni kW consumato dall'impianto. Questa è la "saggezza dettata dall'esperienza" che fa parte dell'equazione. Dividere l'impianto in infrastruttura elettrica e quindi in sistemi principali.
Il risparmio energetico inizia con due tattiche basilari: (1) ispezione generale dei sistemi principali e (2) raccolta di dati mirata, inclusa la registrazione del consumo energetico in corrispondenza del punto di allacciamento principale e dei carichi principali.
Identificare il consumo specificato di un sistema, determinare il consumo attuale e identificare le pratiche che danno luogo a sprechi, nelle ore e nel tipo di funzionamento o nelle apparecchiature e nel sistema stesso. Per ottenere un risparmio, la struttura deve ridurre gli sprechi apportando modifiche alle operazioni, alla manutenzione o alle apparecchiature e ai controlli.
Componenti dell'energia
Prima di spiegare come tracciare il consumo di energia, rivediamo come si definisce e si misura l'energia.
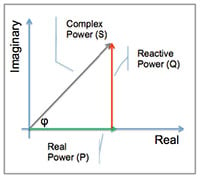
L'energia è espressa in potenza reale, reattiva e apparente (Figura 1).
Il flusso di energia è descritto da:
- potenza reale (P) o potenza attiva in watt (W)
- potenza reattiva (Q) in voltampere reattivi (VAR)
- potenza complessa (S) in voltampere (VA)
- potenza apparente, il modulo della potenza complessa (VA)
La relazione matematica tra potenza reale, reattiva e apparente può essere rappresentata da vettori o espressa mediante numeri complessi, S = P + JQ (dove j è l'unità immaginaria).
La potenza reattiva non trasferisce energia, non produce lavoro, per cui viene rappresentata come asse immaginario del diagramma vettoriale. La potenza reale trasferisce energia, per cui costituisce l'asse reale.
La velocità del flusso di energia in un sistema dipende dal carico (resistivo, reattivo o di entrambi i tipi).
Con un carico puramente resistivo, con polarità inversa di tensione e corrente contemporaneamente, ad ogni istante il prodotto della tensione per la corrente è positivo e viene trasferita solo la potenza reale: viene prodotto lavoro.
Se il carico è reattivo, la tensione e la corrente sono sfasate e il prodotto della tensione per la corrente può essere positivo o negativo, indicando che una parte dell'energia viene trasferita al carico e una parte ritorna indietro. Il trasferimento netto di energia al carico è nullo: non viene prodotto lavoro.
In realtà, tutti i carichi contengono una combinazione di resistenza, induttanza e capacità, producendo potenza sia reale che reattiva in un sistema. Per questo motivo, gli impianti elettrici sono progettati per tollerare una certa quantità di potenza reattiva. Il problema si verifica quando viene generata una potenza reattiva eccessiva. Non solo la potenza reale non è sufficiente per produrre il lavoro richiesto, ma la capacità complessiva di generazione del lavoro del sistema viene compromessa. Ecco perché i fornitori di energia penalizzano i clienti se i loro carichi producono una potenza reattiva eccessiva. Si tratta di una potenza sprecata la cui generazione comporta dei costi ma che non può essere utilizzata. La maggior parte delle fatture di fornitura dell'energia elettrica tiene traccia dei VAR (potenza reattiva) e molte calcolano il fattore di potenza, il quale è un valore che indica quanto un sistema è sceso al di sotto del 100% di potenza reale assorbita. La maggior parte dei fornitori di energia elettrica richiede che i clienti stiano al di sopra di 0,95 PF (fattore di potenza).
Tracciamento del consumo di energia.
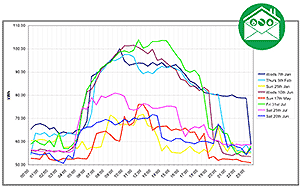
La comprensione dei componenti basilari dell'energia consente a un elettricista di configurare le apparecchiature di registrazione dell'energia per misurare il livello e la qualità complessivi del consumo e poi tracciare quando l'energia viene consumata e da cosa (Figura 2).
Registrare la potenza nei quadri principale e secondario e i carichi principali. Registrare kW, kWh e fattore di potenza in un periodo di tempo rappresentativo.
Ciò fornisce un quadro molto accurato del consumo di potenza reale sui circuiti e sui carichi trifase.
I maggiori risparmi derivano dalla determinazione dei picchi di utilizzo della potenza, dalla valutazione del fattore di potenza e dal consumo di energia elettrica complessivo rispetto alle fatture del fornitore di energia ed eventualmente dal riequilibrio dei carichi. Persino alcuni minuti di picco di utilizzo possono aumentare la tariffa per un paio di ore, giorni o settimane.
La riprogrammazione dei carichi può consentire a un'azienda di sfruttare le ore del giorno in cui il costo dell'energia è minore. Verificare di quanto il fattore di potenza è inferiore a "1" e controllare le fatture del fornitore dell'energia per scoprire se si è penalizzati a causa di un fattore di potenza scarso. In tal caso, il registratore di rete può aiutare a tracciare le sorgenti. Quindi, dopo aver apportato i dovuti miglioramenti energetici, ricollegare lo strumento per avere la prova del beneficio derivante dai miglioramenti in termini di efficienza.
Comprensione dei punti di spreco di energia
Tutti i sistemi e le operazioni sono potenzialmente dei punti di spreco che possono essere contenuti o risolti. I sottosistemi elettrici, l'aria compressa, il vapore e determinati impianti elettromeccanici sono un buon punto di partenza, ma ogni operazione ha i propri punti di potenziale spreco da misurare.
L'obiettivo è quello di mappare il consumo energetico di apparecchiature e processi specifici per individuare dove viene sprecata energia per quantificare gli sprechi e dare priorità ai miglioramenti o alle sostituzioni in base alla durata delle apparecchiature e alle modifiche che possono offrire il miglior ritorno sull'investimento.

La mappatura dell'energia fornisce anche un riferimento in base al quale misurare l'efficacia dei progetti di risparmio energetico per giustificarne il costo (Figura 3).
Sprechi comuni nei sottosistemi elettrici:
- Carichi lasciati normalmente accesi fuori dall'orario di lavoro o fatti funzionare inutilmente negli orari di punta della giornata.
- L'assenza di controlli sul motore può comportare la produzione di una potenza maggiore di quella richiesta.
- Le condizioni di sovratensione/sovracorrente provocano un consumo di energia eccessivo da compensare.
- Gli squilibri di fase fanno sì che il carico consumi energia senza poterla utilizzare.
Identificazione e quantificazione:
- Eseguire la scansione termica del quadro elettrico e del carico meccanico per verificarne l'eventuale surriscaldamento.
- Registrare l'andamento della potenza nel tempo: quanta energia viene consumata, a che ora del giorno e quanta ne viene sprecata?
Sprechi comuni e punti di ispezione negli impianti elettromeccanici.
- Un attrito eccessivo attrito derivante da problemi di allineamento, cuscinetti, squilibrio e allentamenti sovraccarica il motore, con conseguente consumo eccessivo di energia.
- I carichi incontrollati lasciati accesi fuori orario, fatti funzionare negli orari di punta, producono una potenza superiore a quella richiesta e sono soggetti a sovratensioni/sovraccorrenti e squilibri di fase.
- I dispositivi meccanici obsoleti consumano talmente più energia rispetto ai moderni modelli ad alta efficienza energetica da poterne giustificare la sostituzione anticipata anche soltanto con la riduzione dei consumi in kWh.
Identificazione e quantificazione:
- Eseguire una scansione termica del quadro dell'azionamento e del carico meccanico per verificarne l'eventuale surriscaldamento indicativo di inefficienza elettrica.
- Registrare l'andamento della potenza nel tempo, controllare i kWh totali, il fattore di potenza, il fabbisogno energetico di picco, lo squilibrio e le armoniche.
- Testare i livelli di vibrazione rispetto agli standard e identificare soluzioni di manutenzione quali la riequilibratura.
- Eseguire una scansione termica di accoppiamenti/albero/cinghie, cuscinetti e ventola.
- Controllare i livelli di tensione e di corrente.
- Eseguire una scansione termica della scatola di derivazione e degli avvolgimenti, ed eseguire dei test di misura della resistenza d'isolamento.
Sprechi comuni e punti di ispezione negli impianti ad aria compressa:
- Le perdite eccessive nelle tubazioni dell'aria compressa comportano un funzionamento eccessivo per mantenere inaletarato il livello di alimentazione.
- I compressori lasciati accesi fuori dall'orario di utilizzo sprecano energia.
Identificazione e quantificazione:
- Eseguire il Power Log del compressore rispetto al consumo di riferimento.
- Misurare la pressione del compressore e del punto di utilizzo per determinare l'entità della caduta.
- Eseguire la scansione agli ultrasuoni per identificare le perdite.
Sprechi comuni e punti di ispezione negli impianti a vapore:
- Gli scaricatori di condensa guasti e la coibentazione insufficiente causano sprechi di vapore, con conseguente sovrapproduzione per mantenere l'alimentazione richiesta.
Identificazione e quantificazione:
- Effettuare il Powe Log della caldaia rispetto al consumo di riferimento.
- Eseguire una scansione termica su tubi e scaricatori per identificare problemi di coibentazione e ostruzioni.
Dimostrare il ROI
Con la suddetta mancanza di standard industriali, come possiamo davvero sapere quali sistemi offrono il maggiore ROI potenziale sull'energia? Il nostro materiale migliore al momento è costituito da esempi pratici che rappresentano situazioni comuni. Di seguito sono riportati vari esempi di impianti industriali comuni.
Ispezione elettromeccanica
Tipo di struttura: impianto di riciclo dell'acciaio in Germania
Tipo di apparecchiatura: ventola con azionamento a cinghia, per il raffreddamento di processo
Misurazioni effettuate: test delle vibrazioni
Problemi riscontrati: squilibrio moderato, insieme a disallineamento e usura dei cuscinetti.
Risparmio: È stata necessaria la riequilibratura. Un motore da 350 kW funzionava all'80% della potenza nominale; la potenza misurata era di circa 280 kW. Dopo la riequilibratura, il consumo di energia elettrica è stato ridotto del 3%. A un costo di 0,11 euro/kWh, il risparmio annuo ammonta a 8.094 euro.
Ispezione dell'aria compressa
Tipo di struttura: stabilimento di produzione
Tipo di apparecchiatura: impianto ad aria compressa
Misurazioni effettuate: ispezione agli ultrasuoni dell'impianto ad aria compressa (è consigliata la registrazione dei dati del compressore completa)
Problemi riscontrati: la quantità di aria compressa prodotta rispetto al fabbisogno effettivo.
Risparmio: Sono state individuate molteplici opportunità di risparmio. Risparmio annuo totale di $50.600. Spegnimento del compressore nei fine settimana: risparmio annuale di $32.700. Installazione di elettrovalvole per disattivare l'aria quando i macchinari sono spenti: risparmio annuale di $7.100. Riparazione di 36 perdite: risparmio annuale di $4.800. Filtri installati nell'impianto a un costo una tantum di $6.000; risparmio annuale grazie ai filtri: $6.000
Ispezione degli scaricatori di condensa
Tipo di struttura: stabilimento di produzione
Tipo di apparecchiatura: caldaie e tubazioni del vapore
Misurazioni effettuate: ispezione termica delle tubazioni del vapore
Problemi riscontrati: malfunzionamento di sei scaricatori di condensa; perdite dalle serpentine nei serbatoi di placcatura; perdite di vapore nelle linee di placcatura; opportunità di recuperare la condensa
Risparmio: Sei scaricatori di condensa sostituiti per un costo di $500 ciascuno. Risparmio ottenuto: $3.200 a scaricatore utilizzando i costi noti per generare il vapore e i calcoli per determinare le perdite di calore. Risparmio complessivo: $16.200
Fase successiva: Registrazione dei dati energetici sul quadro di alimentazione della caldaia prima e dopo la risoluzione dei problemi legati alle perdite e alla condensa.
Aumento della produttività o riduzione delle spese generali?
La prossima domanda è davvero interessante: Una volta individuato un percorso per ridurre il consumo di energia, il risparmio conseguente viene utilizzato per aumentare la resa dell'impianto (stesso consumo di kWh per produrre maggiori volumi) o per altre strategie aziendali (margini di profitto, margine di realizzo sui prezzi)?
La riduzione del consumo di energia è semplicemente una buona pratica aziendale. La registrazione dei dati energetici dei principali impianti e la mappatura dei relativi costi rispetto alle fatture delle utenze per quantificare dove e quando si verifica il consumo, le aziende possono spesso realizzare risparmi con semplici modifiche operative e di pianificazione. Identificando le apparecchiature inefficienti o obsolete, le aziende possono giustificare e dare priorità alla sostituzione. Inoltre, riducendo il consumo di energia complessivo, le aziende riducono i costi operativi, migliorando la loro competitività sul mercato.
Vai a questo articolo in formato PDF