Por Jack Smith
¿Cuál es el coste derivado de las paradas inesperadas en sus instalaciones por minuto, hora o día? ¿Cuántos de esos periodos de inactividad se pueden evitar en sus instalaciones? Llevar a cabo labores de mantenimiento e inversiones adecuadas puede ayudar a reducir estas sorpresas.
El Programa Federal de Gestión Energética (FEMP) (www1.eere.energy.gov/femp), que forma parte del Departamento de Energía de Estados Unidos (DOE) (www.energy.gov), publicó en agosto de 2010 la última versión de "Prácticas recomendadas para operaciones y mantenimiento: guía para alcanzar la eficiencia operativa". Creada bajo la dirección del FEMP, esta guía de 320 páginas proporciona información útil sobre los enfoques operativos, de mantenimiento, gestión, eficiencia energética y reducción de costes.
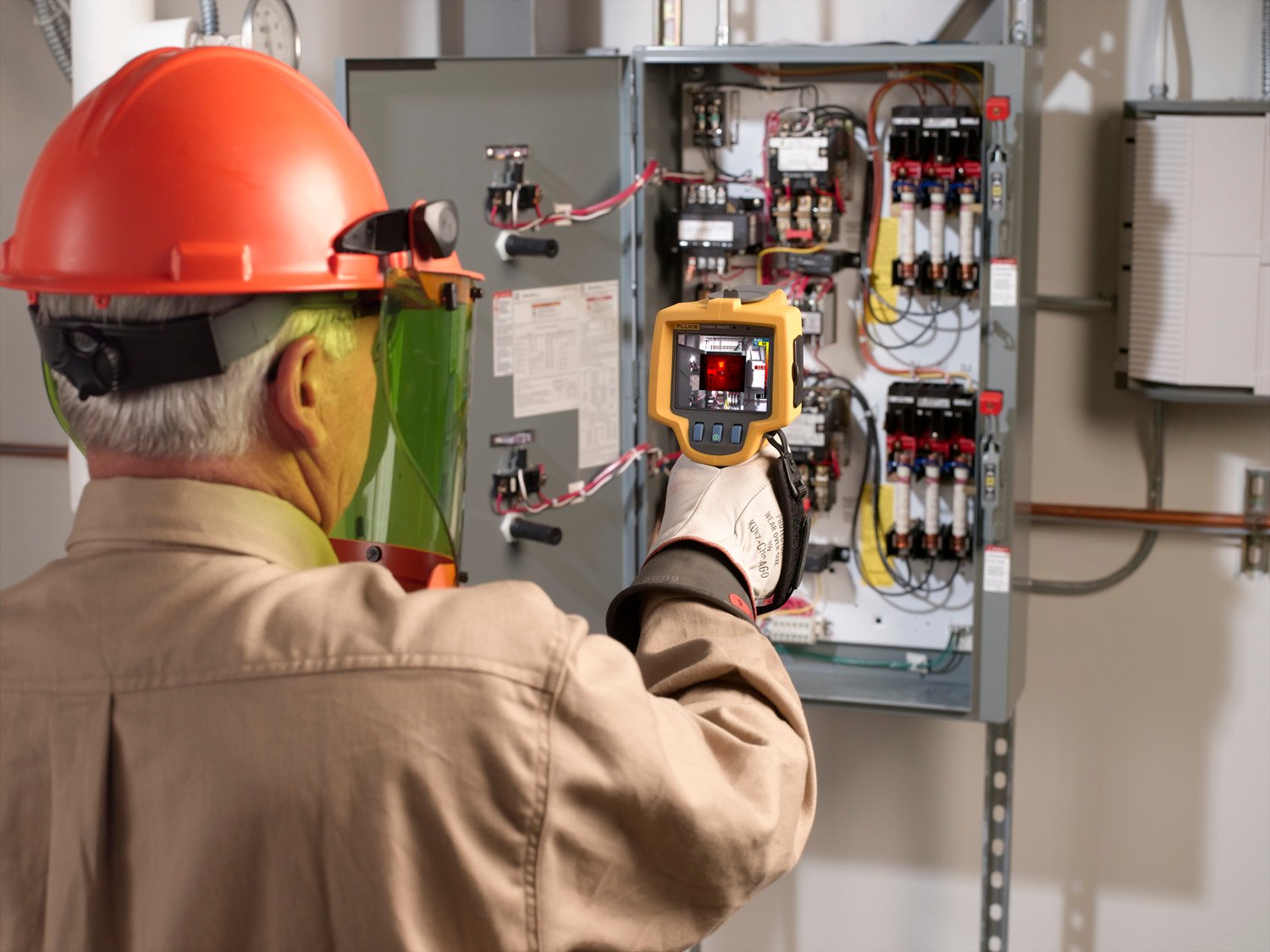
Un aspecto interesante de esta publicación es su énfasis en el mantenimiento predictivo (PdM). El capítulo 5 define, explica y ofrece comparaciones y ejemplos de tipos de programa de mantenimiento. Sin embargo, la guía dedica un capítulo completo al PdM (capítulo 6). Tres de las tecnologías de PdM presentadas en la guía son la termografía, el análisis de vibraciones y la tendencia de rendimiento. Volveremos a esto más adelante.
La guía enumera como tipos de programa de mantenimiento el mantenimiento reactivo, el preventivo (PM), el PdM y el centrado en la fiabilidad (RCM). Asimismo, describe las diferencias entre ellos:
- Mantenimiento reactivo: permite que el equipo realice un mantenimiento correctivo.
- PM: el personal lleva a cabo labores de mantenimiento según el tiempo o la programación del tiempo de ejecución del equipo.
- PdM: basa la necesidad de mantenimiento en la condición o el estado real de la máquina o el equipo.
- RCM: se parece bastante a la metodología del PdM, con la diferencia de que el RCM tiene en cuenta la importancia del equipo y el contexto.
Otro punto interesante que cabe destacar de la guía del FEMP es que "más del 55 % de los recursos y actividades de mantenimiento de una instalación media siguen siendo reactivos". Aunque la publicación atribuye estas medidas a una investigación realizada diez años antes, los números se mantienen si se comparan con estudios más recientes como el publicado en abril de 2010 en la revista de ingeniería de plantas "El cambiante mundo de la ingeniería de plantas", en el cual se afirma que "más del 60 % de las plantas estadounidenses y más del 70 % de las internacionales no cuentan con una estrategia de mantenimiento en marcha".
De vuelta al PdM
La guía del FEMP explica los pros y contras del PdM y los compara con otros métodos de mantenimiento. Aunque estima que un programa de PdM que funcione correctamente puede suponer un ahorro de entre el 8 y el 12 % en un programa que solo utilice el PM, también reconoce la inversión inicial significativa que el PdM puede requerir. En la inversión se incluyen los equipos de supervisión y diagnóstico, la formación del personal en planta para el uso de los equipos y la información que se les proporciona a estos sobre los conceptos y las metodologías de PdM. Aunque el PDM pueda originar unos costes iniciales significativos, no puede compararse con los elevados costes que podrían conllevar los tiempos de inactividad en su planta.
Aunque la mayoría de la información que se incluye en la guía no es nueva, sirve para reforzar las estrategias comprobadas de PdM que existen. Esto es importante porque muchas plantas siguen gestionando el mantenimiento de forma reactiva. Por lo tanto, merece la pena repetir las metodologías establecidas que pueden ayudar a predecir y prevenir situaciones que podrían causar periodos de inactividad.
Por ejemplo, el uso de la termografía infrarroja para inspeccionar sistemas eléctricos está consolidado y bien documentado. La generación, transmisión, distribución y uso final de la energía eléctrica puede beneficiarse de la inspección termográfica. La termografía puede detectar muchos fallos inminentes en la mayoría de sistemas eléctricos: desde generadores, motores y transformadores, hasta conmutadores, centros de control de motores, soportes de cables y cuadros de distribución de la iluminación.
Sin embargo, no solo los detecta en sistemas eléctricos. La termografía también se utiliza para detectar y diagnosticar problemas en equipos mecánicos. Además de ser capaz de detectar problemas relacionados con los equipos giratorios, como fallos en los cojinetes, alineación, equilibrio y holgura; la termografía se puede utilizar para comprobar tubos de calderas y materiales refractarios; tuberías, válvulas y purgadores de vapor; niveles de fluidos en tanques y taponamiento de tuberías; patrones de agua ambiental y de descarga de aire; e incluso la integridad de las membranas de los techos.
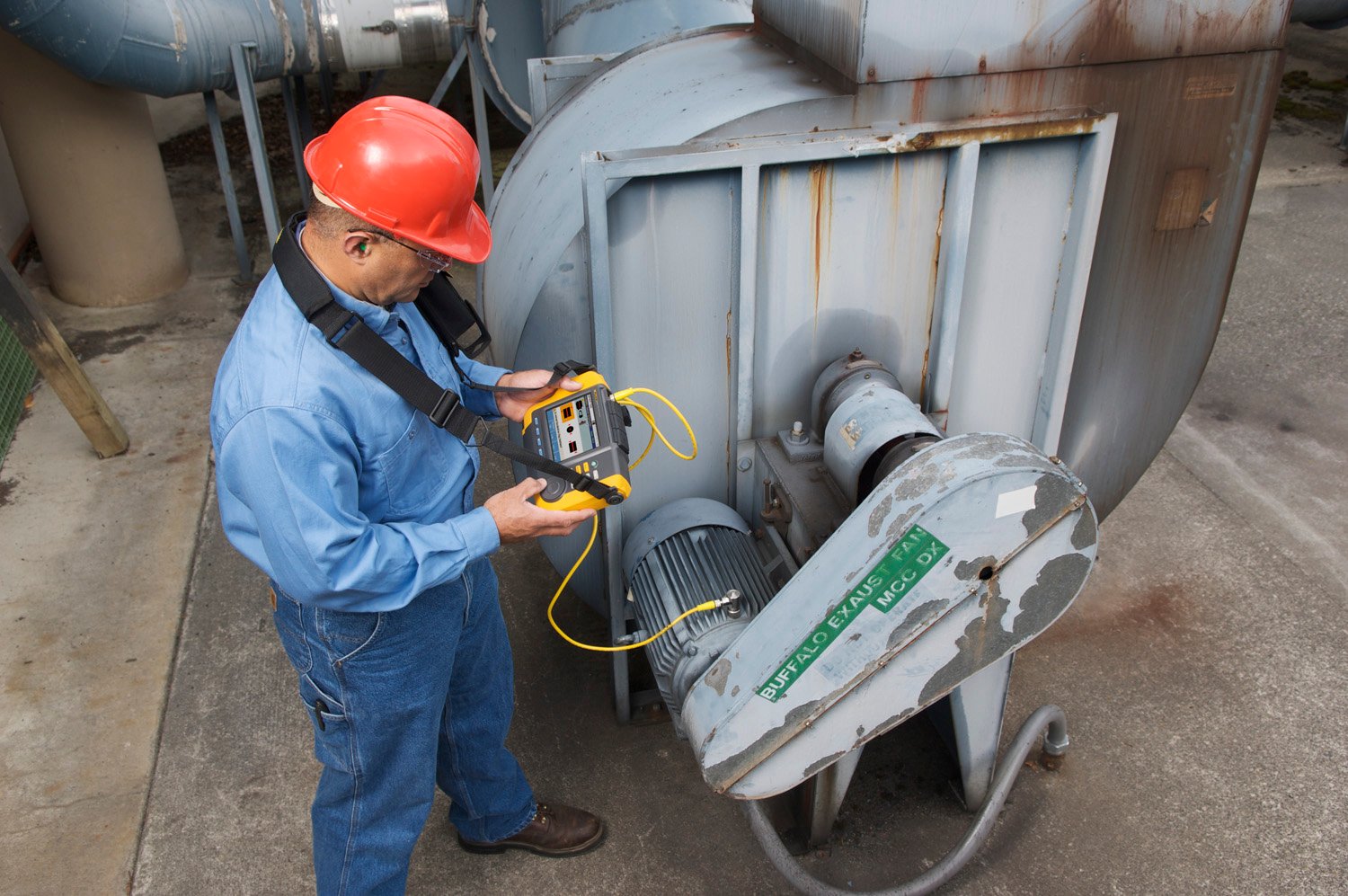
La instrumentación para la detección de vibraciones y el software para el análisis de firmas se han utilizado durante mucho tiempo para detectar condiciones anómalas en los equipos. Este tipo de tecnología de PdM puede ayudar a definir problemas existentes, como el desequilibrio mecánico, los rotores excéntricos, los errores de alineación, la vibración inducida por el flujo, y los problemas en los cojinetes de casquillo, en los engranajes y de resonancia mecánica; por nombrar algunos.
En el pasado, los equipos de análisis de vibraciones eran extremadamente caros y complejos. Las plantas que utilizaban este tipo de PdM solían externalizar a terceros los análisis y comprobaciones de vibraciones. Sin embargo, como ocurre con la termografía infrarroja, los equipos de comprobación de vibraciones ahora son accesibles, asequibles y mucho menos complejos que las tecnologías anteriores.
La tendencia de rendimiento incrementa los programas de PdM mediante la documentación de parámetros operacionales de los equipos y procesos de las instalaciones. Esto permite al personal de planta establecer referencias, hacer un seguimiento de las tendencias y detectar cuándo los parámetros de los equipos y de los procesos se encuentran fuera de sus rangos óptimos. Esta información se puede utilizar para determinar el estado o la condición de los equipos o procesos monitorizados.
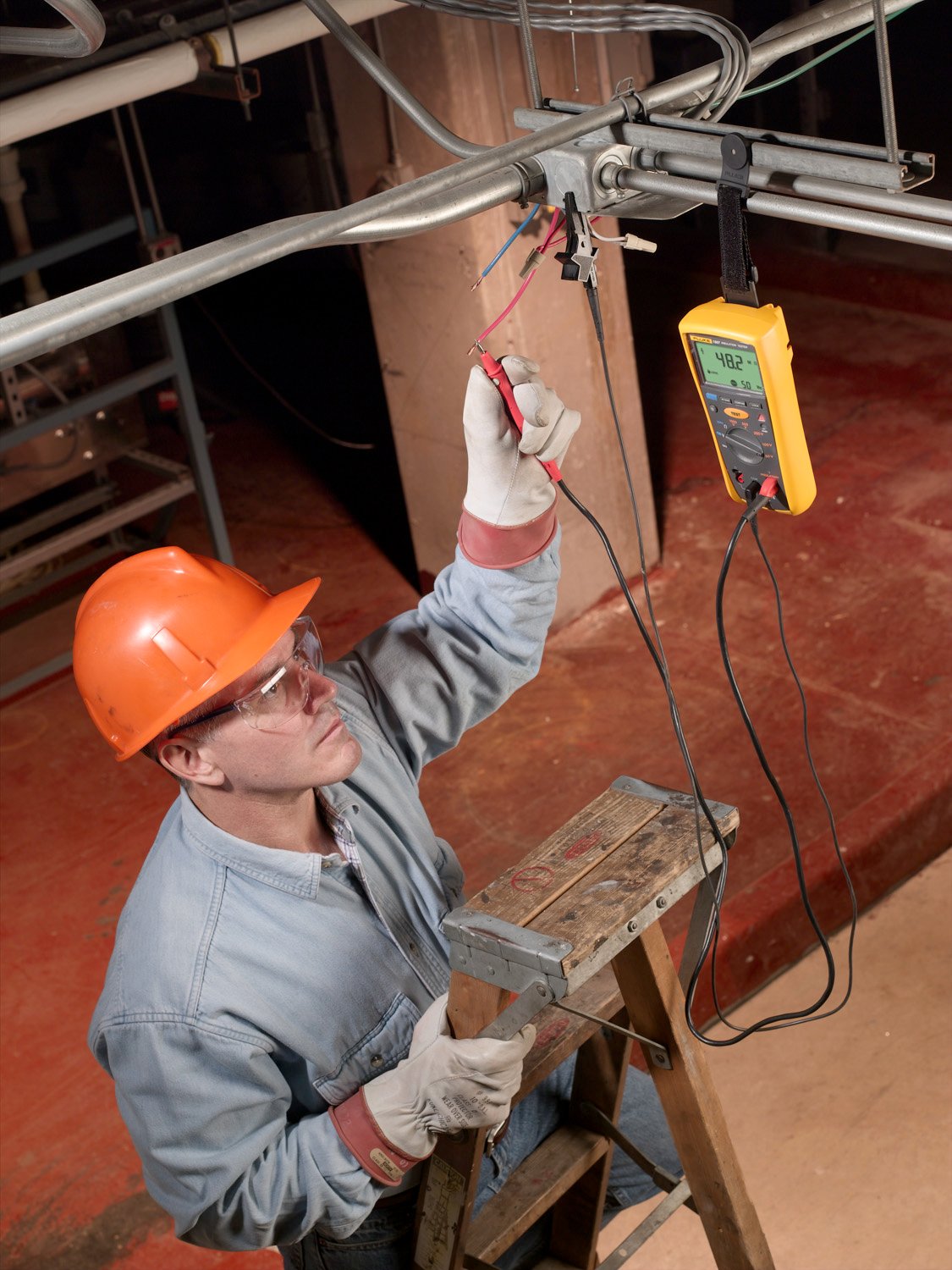
Gran parte de los equipos de muchas instalaciones ya cuentan con instrumentación que se puede utilizar para elaborar tendencias de rendimiento. Si fuera necesario, se pueden instalar sensores adicionales en las instalaciones. Registradores de datos fáciles de usar y relativamente asequibles pueden completar los requisitos necesarios para la elaboración de tendencias de rendimiento de PdM.
No nos olvidemos de los analizadores y registradores de calidad eléctrica, los registradores de potencia, los multímetros de registro o los comprobadores de aislamiento. Esta lista no está completa. Las herramientas están disponibles y son asequibles y fáciles de usar. Sin embargo, el uso más eficaz de estas o de cualquier otro equipo de comprobación de calidad depende de cómo se utilice para ayudar a predecir y prevenir fallos y no solo a reaccionar ante ellos.
Haga clic aquí para consultar una copia de "Prácticas recomendadas para operaciones y mantenimiento: guía para alcanzar la eficiencia operativa" (.pdf)
Para enviar un comentario sobre este artículo o cualquier otro publicado en mis columnas de "Tierra firme" o para sugerir algún tema, envíe un correo electrónico a jacksmith.writes@gmail.com.
Siga en "Tierra firme", ¡hasta la próxima!