Cuando hablamos del ahorro de energía, existen objetivos y planes. Las plantas industriales en EE.UU. muestran un interés constante por la gestión del consumo. El objetivo es el siguiente: Reducir el consumo de energía en general o mantener el uso, pero aumentar la cantidad producida por kW utilizado.
¿Y el plan? A veces eso supone un problema.
El plan solo se mantiene en la fabricación si están presentes la sabiduría que da la experiencia como guía de la visión y los números del rendimiento de la inversión para respaldar el esfuerzo. Sin embargo, no existen unas directrices sobre la energía a disposición de un director de planta para establecer las bases de referencia de lo que sería un aprovechamiento "razonable" de la energía en instalaciones como por ejemplo una fábrica. Entonces, ¿cómo se puede evaluar cuál es el aprovechamiento razonable de la energía y cuál genera un desperdicio? O, del que supone un desperdicio, ¿cuál proporciona un rendimiento de la inversión suficiente?
El rendimiento de la inversión del que hablamos aquí es el coste por kWh, tal cual lo cobra la compañía suministradora. La tarifa varía en función de la hora del día y el momento del año. La reducción de ese gasto es la que genera ahorros. Los materiales y la mano de obra necesarios para cambiar el consumo de energía constituyen la inversión. El rendimiento es el periodo necesario para que la reducción de la factura eléctrica cubra el coste de la inversión. Los beneficios se obtienen tras cubrir los gastos.
De vuelta al asunto del plan, ¿cómo se hace una estimación del rendimiento de la inversión cuando no existe ninguna norma industrial que contemple un aprovechamiento razonable de la energía?
Perfiles de consumo en la industria
El consumo en la industria varía en función de múltiples variables:
- la antigüedad de la planta
- el tipo y las dimensiones de carga
- el programa de funcionamiento, tanto las horas semanales como la intensidad de la carga
- el número de trabajadores
- el clima
- la filosofía de mantenimiento
La respuesta es la siguiente: No intente gestionar todos los kW que consume su instalación. Aquí es donde entra "la sabiduría que da la experiencia". Divida la instalación entre la infraestructura eléctrica y los sistemas clave.
El ahorro de energía se inician con dos tácticas básicas: (1) inspección general de los sistemas clave y (2) recogida dirigida de datos, incluido el registro del uso de energía en las principales entradas de suministro y las principales cargas.
Identifique el consumo nominal de un sistema, determine su consumo actual e identifique las prácticas que suponen un desperdicio, tanto en horas y tipo de operación, como en los equipos y el propio sistema. La instalación debe abordar el desperdicio para poder generar ahorros, ya sea con cambios en el funcionamiento y el mantenimiento, o en los equipos y controles.
Componentes de la energía
Antes de explicar cómo supervisar el consumo de energía, veamos cómo definirlo y medirlo.
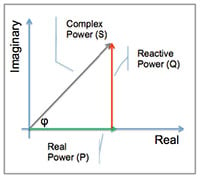
La energía se expresa como potencia real, reactiva y aparente (Figura 1).
El flujo de energía se describe como:
- potencia real (P) o activa en vatios (W)
- potencia reactiva (Q) en VA reactivos (VAR)
- potencia compleja (S) en VA
- potencia aparente, la magnitud de la potencia compleja (VA)
La relación matemática de la potencia real, reactiva y aparente puede representarse mediante vectores, o con el uso de números complejos, S = P + jQ (donde "j" es la unidad imaginaria).
La potencia reactiva no transfiere energía (no produce trabajo), por lo que se representa como el eje imaginario del diagrama vectorial. La potencia real mueve la energía, por lo que se representa como el eje real.
El flujo de energía en un sistema depende de la carga: ¿es resistiva, reactiva o ambas?
Si la carga es puramente resistiva, la tensión y la corriente invierten la polaridad al mismo tiempo, el producto de la tensión y la corriente es positivo en todo momento, y solo se transfiere potencia real; es decir, se produce trabajo.
Si la carga es puramente reactiva, la tensión y la corriente están fuera de fase y el producto de la tensión y la corriente puede ser positivo o negativo, lo que indica que una parte de la energía se transfiere a la carga y otra parte fluye de vuelta. La transferencia neta de energía a la carga es cero; es decir, no se produce trabajo.
En realidad, todas las cargas poseen una combinación de resistencia, inductancia y capacidad, y generan una potencia tanto real como reactiva en un sistema. Por ese motivo, los sistemas eléctricos están diseñados para tolerar una cierta cantidad de potencia reactiva. Los problemas aparecen cuando se genera demasiada potencia reactiva. No solo la potencia real es insuficiente para producir el trabajo necesario, sino que la capacidad general de generación de trabajo del sistema se ve en peligro. Por eso las compañías de suministro penalizan a sus clientes si sus cargas producen demasiada potencia reactiva; se trata de un desperdicio de energía que genera costes económicos, pero que no puede utilizarse. La mayor parte de las facturas de las compañías de suministro realizan un seguimiento de VAR (potencia reactiva) y muchas calculan el factor de potencia, que indica cuánto está por debajo del 100% un sistema. La mayoría exige a sus clientes que su factor de potencia sea superior a 0,95.
Supervisión del consumo
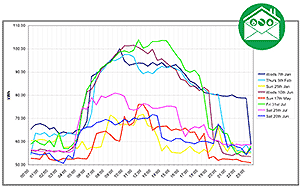
Conocer los componentes básicos de la energía permite que un electricista instale un registrador de consumo eléctrico para medir el nivel y la calidad eléctrica, así como para supervisar qué consume energía (Figura 2).
Registre la potencia de los paneles principales y secundarios, y de las cargas principales. Registre los kW, kWh y el factor de potencia durante un periodo representativo.
Esto proporciona una imagen muy precisa del consumo de energía real en circuitos trifásicos y cargas.
El mayor ahorro de energía se logra mediante la determinación de los momentos en que el uso de energía alcanza su punto máximo, la evaluación del factor de potencia y el consumo de energía total en comparación con las facturas de la empresa de servicios públicos, y posiblemente, el nuevo equilibrio de las cargas. Solo un par de minutos de uso máximo puede aumentar la tarifa de uso durante un par de horas, días o semanas.
Reprogramar las cargas permite a las empresas sacar ventaja de las horas del día en que la potencia es más barata. Compruebe el factor de potencia y cuánto está por debajo de "1" y revise las facturas para ver si existe una penalización por un factor de potencia deficiente. Si lo hay, el registrador puede ayudarle a rastrear las fuentes. Tras haber realizado las actualizaciones eléctricas, vuelva a conectar el registrador para comprobar las mejoras en la eficiencia.
Puntos de desperdicio de energía
Todos los sistemas y operaciones pueden constituir un punto de desperdicio de energía que se puede mitigar o al que se le puede poner remedio. Los subsistemas eléctricos, los sistemas de aire comprimido y de vapor, y algunos sistemas electromecánicos son un buen punto de partida, pero cada operación tiene sus propios puntos de desperdicio potenciales que se deben comprobar.
El objetivo es trazar el mapa del aprovechamiento de la energía en el equipo y los procesos para detectar los puntos en que los que se desperdicia la energía, con el fin de cuantificar el desperdicio y priorizar las mejoras o los reemplazos en función de la vida del equipo y las mejoras que pueden proporcionar el mejor rendimiento de la inversión.

También permite medir la efectividad de los proyectos de ahorro de energía para justificar los costes (Figura 3).
Desperdicios habituales en subsistemas eléctricos:
- Cargas que a menudo se dejan encendidas durante horas o en ejecución innecesaria en momentos del día en los que la tarifa es más cara.
- La ausencia de controles en el motor puede implicar más producción de la que se requiere.
- La tensión o corriente excesivas provocan un consumo excesivo de electricidad que compensar.
- El desequilibrio de fases hace que la carga consuma electricidad sin poder aprovecharla.
Identifique y cuantifique:
- Inspeccione térmicamente el cuadro eléctrico y la carga mecánica en busca de sobrecalentamiento.
- Registre la potencia a lo largo del tiempo: ¿Cuánta electricidad se consume, en qué momento del día y cuánta se desperdicia?
Desperdicios comunes y puntos de inspección en los sistemas electromecánicos.
- El exceso de fricción debido a problemas de alineación, rodamientos, desequilibrio y holgura hace que el motor trabaje en exceso y que consuma demasiada potencia.
- Las cargas sin control que se dejan encendidas durante horas, que se ejecutan durante las horas en las que la tarifa es más cara, generan más salida de la necesaria o sufren condiciones de tensión o corriente excesiva y desequilibrio de fases.
- Los dispositivos mecánicos antiguos consumen mucha más electricidad que los modelos nuevos de alta eficiencia, por lo que un reemplazo temprano puede estar justificado en el consumo reducido de kWh solamente.
Identifique y cuantifique:
- Inspeccione térmicamente el cuadro eléctrico y la carga mecánica en busca de algún indicio de sobrecalentamiento o ineficiencia eléctrica.
- Registre la electricidad a lo largo del tiempo: compruebe los kWh totales, el factor de potencia, el punto de máxima demanda, el desequilibrio y los armónicos.
- Pruebe los niveles de vibraciones de acuerdo con las normas e identifique soluciones de mantenimiento, como el reequilibrio.
- Inspecciones térmicamente acoplamientos, ejes, correas, rodamientos y ventiladores.
- Compruebe los niveles de corriente y tensión.
- Inspeccione térmicamente la caja de conexiones o empalmes y los bobinados, y lleve a cabo pruebas de resistencia de aislamiento.
Desperdicios comunes y puntos de inspección en sistemas de aire comprimido:
- Las filtraciones excesivas en líneas de aire comprimido dan lugar a una actividad excesiva para mantener el suministro.
- Los compresores que se dejan encendidos fuera de su tiempo de uso desperdician energía.
Identifique y cuantifique:
- Registre la potencia en el compresor para obtener un consumo de referencia.
- Mida la presión y el punto de uso en el compresor para determinar el volumen de la caída.
- Líneas de inspección por ultrasonidos para identificar fugas.
Desperdicios habituales y puntos de inspección en sistemas de vapor:
- Los purgadores de vapor con fallos y el aislamiento insuficiente desperdician vapor y causan una sobreproducción para mantener el suministro necesario.
Identifique y cuantifique:
- Registre la potencia en la caldera para obtener un consumo de referencia.
- Inspeccione térmicamente las tuberías y purgadores para identificar brechas y bloqueos de aislamiento
Ponga a prueba el rendimiento de la inversión
Dada la falta de normas industriales que ya hemos mencionado, ¿cómo podemos saber qué sistemas poseen el mayor potencial de rendimiento de la inversión en energía? El mejor material con el que contamos ahora mismo son los ejemplos de casos de situaciones comunes. A continuación, se presentan varios ejemplos de sistemas industriales comunes.
Inspección electromecánica
Tipo de instalación: planta de reciclaje de acero en Alemania
Tipo de equipo: ventilador accionado por correa, para refrigeración de procesos
Medidas tomadas: pruebas de vibración
Problemas detectados: se detectó un desequilibrio moderado, además de la desalineación y el desgaste de los rodamientos.
Ahorros: se tuvo que corregir el desequilibrio. Un motor de 350 kW funcionaba al 80% de la potencia nominal; la potencia medida era de 280 kW aproximadamente. Después de corregir el desequilibrio, el consumo de energía se redujo un 3%. A un coste de 0,11 €/kWh, el ahorro anual ascendió a 8094 €.
Inspección de aire comprimido
Tipo de instalación: fabricación
Tipo de equipo: sistema de aire comprimido
Medidas tomadas: inspección por ultrasonido del sistema de aire comprimido (registro de todos los datos del compresor recomendado)
Problemas detectados: la cantidad de aire comprimido producido en comparación con la demanda real.
Ahorro: se encontraron varias oportunidades de ahorro. Ahorro total anual de 50.600 dólares. Apagar el compresor los fines de semana: ahorro anual de 32.700 dólares. Instalar solenoides para cerrar el paso de aire cuando las máquinas están apagadas: ahorro anual de 7100 dólares. Reparación de 36 fugas: ahorro anual de 4800 dólares. Filtros instalados en el sistema a un coste único de 6000 dólares; ahorro anual como resultado de los filtros: 6000 dólares.
Inspección de purgadores de vapor
Tipo de instalación: fabricación
Tipo de equipo: calderas y líneas de vapor
Medidas tomadas: inspección térmica de la línea de vapor
Problemas detectados: seis purgadores de vapor no funcionan correctamente; bobinas con fugas en los tanques de galvanizado; fugas de vapor en las líneas de galvanizado; oportunidades para recuperar la condensación
Ahorros: se reemplazaron seis purgadores averiados con un coste de 500 dólares por purgador. Ahorros conseguidos: 3200 dólares por purgadores con el uso del coste conocido para generar los cálculos de pérdida de vapor y calor. Ahorro total: 16.200 dólares.
Próximo paso: Registro de energía en el panel de suministro de la caldera antes y después de abordar los problemas de fugas y condensación.
¿Aumento de la productividad o reducción de gastos generales?
Es muy interesante contestar a la siguiente pregunta: tras identificar una manera de reducir el consumo, ¿debe encaminar esos ahorros a aumentar la rentabilidad de la planta (mismo consumo de kWh con una mayor producción de volúmenes) o enfocarlos en otras estrategias de negocio (márgenes de ganancia, mejora de los precios obtenidos)?
La reducción del consumo es sin duda un buen negocio. Al registrar la potencia de cada sistema principal y asignar los costes según las facturas de la compañía de suministro en el lugar y los momentos en que sucede el consumo, las empresas pueden materializar los ahorros mediante simples cambios de programa y operativos. Cuando se identifican los equipos ineficientes u obsoletos, las empresas pueden justificar y priorizar los reemplazos. Además, cuando se reduce el consumo de energía en general, las empresas reducen los costes de funcionamiento, lo que mejora su competitividad en el mercado.
Vea este artículo en formato PDF