Rendimiento de la inversión en ahorro de costes de eficiencia energética industrial
¿Qué tiene que ver la medida con el ahorro de energía? Se trata del rendimiento de la inversión y de los resultados.
Las plantas industriales tienen que consumir energía para poner en marcha cualquier actividad (producto, datos, etc.) y en su mayoría desperdician demasiada electricidad. Son usuarios energéticamente ineficientes. Hace veinte años, los responsables de las plantas no se preocupaban por la eficiencia energética porque la energía era barata. Empezaron a interesarse en reducir la factura cuando la energía se encareció pero tuvieron que ponerse medidas en marcha en términos comerciales.
¿Qué nivel de conversión del rendimiento de la inversión hace que el desperdicio sea demasiado elevado?
Para responder a esa pregunta necesita medir cuánta energía está consumiendo en los distintos tipos de trabajo (sistemas) en su edificio y compararla con las normas. Esto le permite conocer la dimensión del desperdicio. Aplicar medidas adicionales puede ayudarle a identificar el origen del desperdicio. Los tres puntos de una ecuación de rendimiento de la inversión son: 1) la cantidad de desperdicio junto con 2) la causa y 3) el coste a abordar.
¿Cuándo tiene sentido reducir el consumo de energía?
La reducción del consumo de energía tiene sentido en las plantas que quieran reducir los gastos generales para aumentar la productividad. Es decir, las que buscan hacer más con menos, y no solo gastar menos.
Una inspección del consumo identifica las oportunidades para aumentar la eficiencia y permite que el director sepa qué actividades son adecuadas según los objetivos principales de la instalación, y cuáles no ofrecen un rendimiento de la inversión suficiente o no son prioritarias. Las mayores oportunidades suelen surgir en las plantas con sistemas cuyo consumo es elevado, grandes y antiguos, que no han sido optimizados. Otros candidatos son las plantas de producción que no han introducido mucha automatización ni controles, así como las plantas con grandes sistemas de vapor o aire comprimido.
¿Cuánto se puede ahorrar?
Según el Departamento de Energía de EE.UU. (DOE), las plantas podrían reducir sus facturas de electricidad en un 25% pero el ahorro real depende de un par de aspectos. Primero: ¿qué tipo de sistemas tiene y qué actividades se llevan a cabo en su instalación? Las cargas grandes que nunca se han asignado al programa de tarifas de suministro para aprovechar las horas más baratas del día podrán obtener ahorros significativos. Las instalaciones que funcionan principalmente con cargas más bajas no tendrán la misma oportunidad. Segundo: ¿cuál es la ineficiencia de los sistemas del edificio? Una instalación más reciente, con un buen mantenimiento, no ofrecerá tantas oportunidades de ahorro como una instalación más antigua en la cual los sistemas y los equipos están lejos de los ajustes y las prácticas de mantenimiento recomendadas.
Si piensa en el desperdicio de energía que se produce en su hogar, es probable que piense también en el aire frío que se cuela por las ventanas o en la sustitución de bombillas antiguas por LED. Sin embargo, ¿qué "desperdicio de energía" se produce en las plantas de fabricación o de uso mixto?
El uso de energía para calentar o enfriar aire y empujarlo a través del sistema de ventilación, solo para que se cuele por la ventana, provoca que el sistema produzca de más y, por tanto, consuma de más. ¿Cuántos sistemas funcionan más de lo necesario a causa de filtros obstruidos, motores sobredimensionados, etc.?
De modo que sí, una planta de fabricación o de uso mixto puede sufrir desperdicios tanto en la iluminación como en el revestimiento del edificio. Sin embargo, ¿son los primeros que hemos de abordar?
No es posible contestar a esta pregunta hasta registrar el consumo de energía de todas las cargas principales, asignarlo de acuerdo con el plan de tarifas y de funcionamiento, y calcular el rendimiento de la inversión. Las plantas logran obtener a menudo el suficiente ahorro en costes operativos y de mantenimiento de equipos grandes como para ahorrar en pocos años el dinero suficiente para acelerar la sustitución del equipo por un modelo más eficiente.
Cómo empezar a reducir el consumo cuando los presupuestos, el tiempo y los recursos son limitados
Trabaje a partir de referencias.
El punto de partida es identificar dónde, cuándo y qué se utiliza esa energía. Una vez que propietarios, directivos y técnicos de instalación entiendan la cantidad de energía que necesitan para poner en marcha el negocio, y la comparen con la cantidad de energía que se desperdicia, entonces podrán tomar decisiones y elaborar un plan. Para llegar a ello obtenga varias copias de las facturas de electricidad más recientes y busque indicios de penalizaciones y cargos por demanda de energía en momentos pico. Descargue una copia del plan de tarifas de la web de la compañía para saber el coste por unidad de energía en diferentes momentos del día, en comparación con su plan de funcionamiento. Si es necesario, llame directamente al departamento de atención al cliente de la compañía, donde estarán encantados de ayudarle.
A continuación instruya a su propio equipo de electricistas o a un contratista para que registren la potencia tanto de las acometidas como de los cuadros eléctricos así como de los mayores sistemas y cargas. Registre los kW, kWh y el factor de potencia durante un periodo representativo. Esto proporciona una imagen precisa del consumo real en los circuitos trifásicos y las cargas. Los mayores ahorros se obtienen a menudo cuando se cambian las operaciones de carga a las horas del día en que la energía es más barata.
¿Cuáles son los sistemas que desperdician más energía?
Además de asignar el sistema de suministro eléctrico, evalúe sus sistemas electromecánicos, de vapor y aire comprimido. Suelen desperdiciar energía, algo que se puede solucionar fácilmente.
Aplicaciones electromecánicas
Hay cinco tipos comunes de desperdicio de energía en un sistema electromecánico: 1) eléctrico, 2) mecánico/fricción, 3) programación, 4) controles y 5) tamaño/eficiencia.
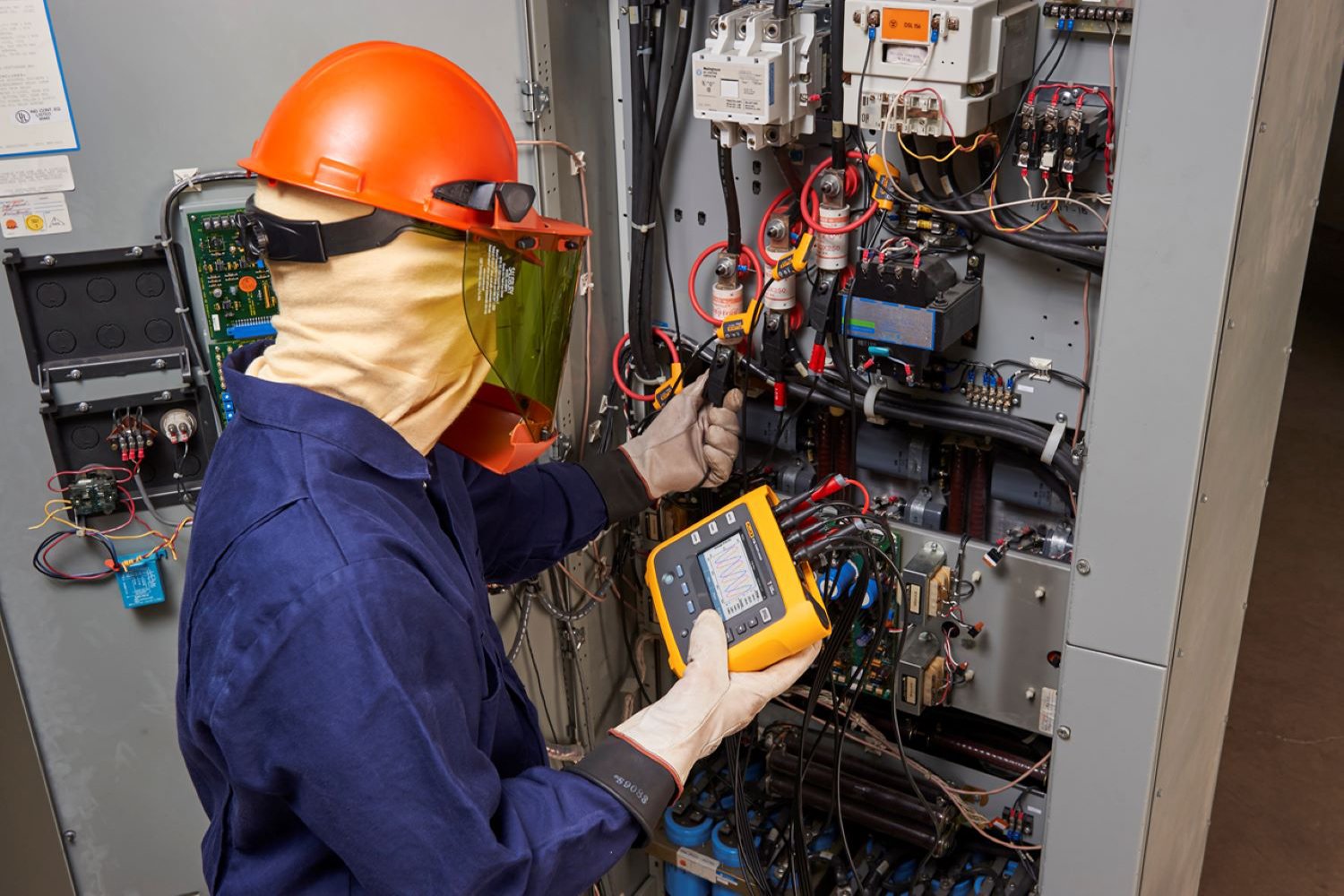
Uso de un registrador avanzado de consumo eléctrico Fluke 1738 para analizar el consumo en un sistema mecánico
- La sobrecarga de corriente/tensión y el desequilibrio de fases son dos de las principales causas de desperdicio de energía en sistemas electromecánicos. Estos dos problemas eléctricos se pueden detectar con analizadores de calidad eléctrica y cámaras termográficas.
- El desperdicio de energía se manifiesta en forma de sobrecalentamiento y vibración excesiva, problemas que se pueden detectar mediante cámaras termográficas y medidores de vibraciones. Las posibles causas varían desde la refrigeración y el flujo de aire hasta la alineación de los rodamientos y otras causas de fricción. Inspeccione con la cámara termográfica los acoplamientos, ejes, bandas, rodamientos, ventiladores, componentes eléctricos, cajas de conexiones o terminaciones, y bobinados; todo aquello que pudiese ser un indicador de un funcionamiento ineficiente y, por lo tanto, de desperdicio de energía.
- Como se mencionó anteriormente, una de las soluciones más sencillas para ahorro de energía es registrar el consumo en las grandes cargas electromecánicas a lo largo de un programa de funcionamiento completo. Determine cuándo consumen las máquinas la mayor cantidad de energía (a menudo al arrancar) y compruebe si las horas de uso se pueden ajustar a las horas del día en las que las tarifas son más bajas.
- Con ese mismo registro de corriente, compare el programa de funcionamiento con la frecuencia en que la máquina consume energía. ¿Cuánta potencia utiliza cuando no se está usando activamente? Sin el uso de controles, la mayoría de las máquinas deben apagarse manualmente para detener el consumo y las acciones manuales no siempre tienen lugar. No se pueden apagar todas las máquinas, pero la mayoría sí se puede poner en reposo. Los controles varían entre los más simples y los completamente automatizados, pasando por el uso de sensores y temporizadores, hasta la maquinaria en reposo y el funcionamiento de la codificación de hardware en un PLC.
- Tamaño y niveles de eficiencia. Los requisitos de funcionamiento cambian, en especial en las instalaciones más antiguas, pero las cargas no, lo que significa que a veces un motor grande, costoso y de arranque brusco acciona un sistema con una intensidad de caballos de fuerza menor. Todos los responsables de las plantas tienden a prolongar al máximo el ciclo de vida de una pieza grande de un equipo. Sin embargo, vale la pena registrar la potencia que utiliza el motor, en comparación con los requisitos de carga actuales y con una nueva unidad, de un tamaño correcto y de alta eficiencia. Calcule el exceso de energía que se consume y multiplíquelo por el plan de tarifas. Determine cuánto tiempo tendría que pasar para amortizar un motor nuevo. En ocasiones, es conveniente desde el punto de vista financiero reemplazar un equipo antes de que falle. De no ser así, considere si se pueden utilizar controles para modular la salida.
Vapor
Es necesario inspeccionar las cuentas del proceso de calefacción de una parte considerable de los costes de funcionamiento y el sistema, a fin de evitar varios escenarios de desperdicio de energía.
Primero, registre el consumo de energía en la caldera para obtener un punto de referencia del consumo. Después inspeccione el sistema de distribución, incluidos los purgadores de vapor, los manómetros, el aislamiento, las bombas y las válvulas. Utilice una cámara termográfica para detectar purgadores de vapor averiados, fugas, bloqueos, problemas de valores y fallos de condensación; el objetivo es devolver tanta condensación precalentada a la caldera como sea posible.
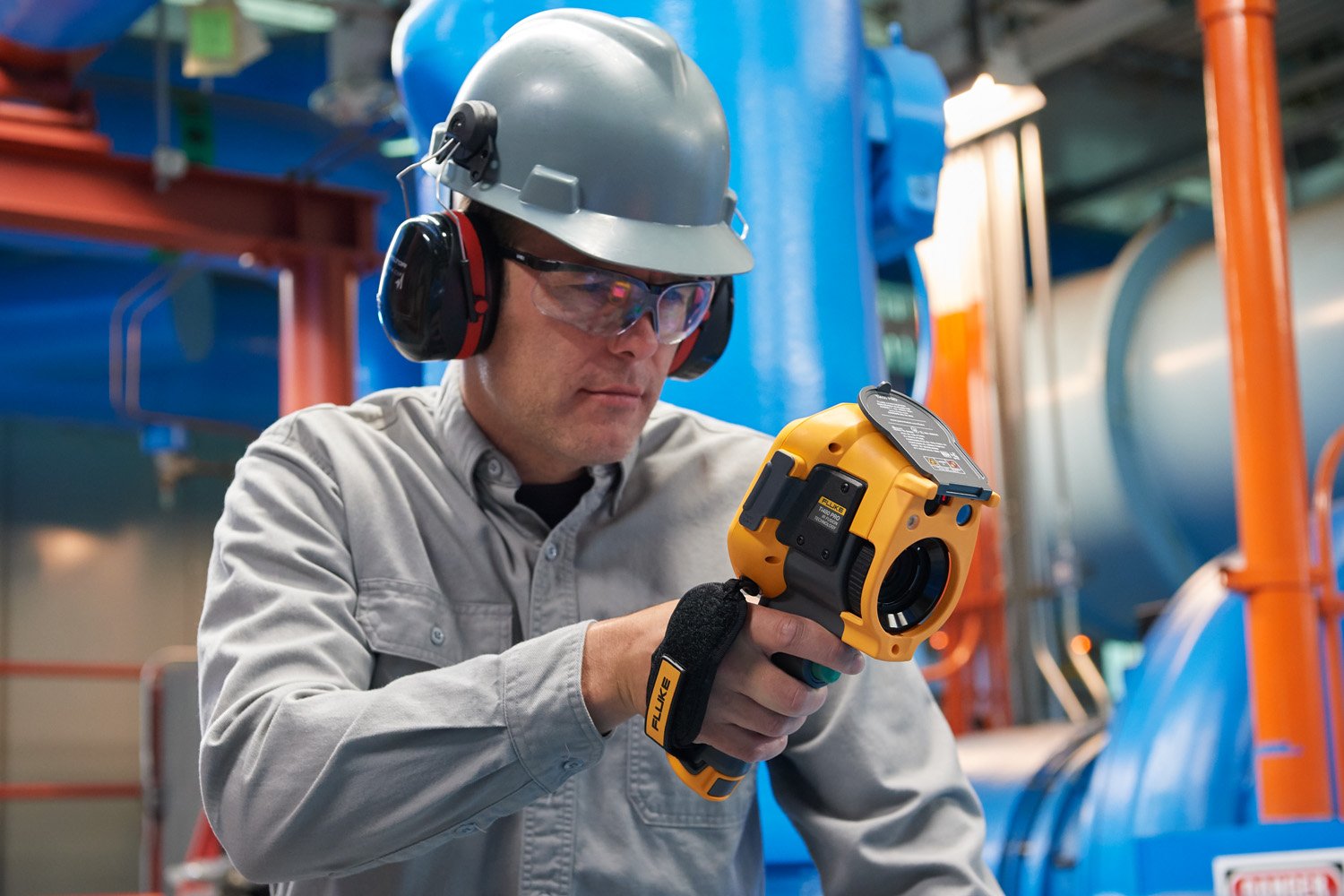
Inspección con una cámara termográfica Fluke Ti401 PRO
También se puede utilizar una cámara termográfica para buscar fugas de vapor. Asegúrese de comprobar si hay aislamiento flojo o ausente y el correcto funcionamiento de todos los purgadores de vapor; limpie el interior de las calderas y compruebe si las líneas de transmisión del vapor están bloqueadas. La unión de estos esfuerzos puede identificar desperdicios de energía y ayudar al equipo a planear soluciones de ahorro de energía, muchas de las cuales a menudo pueden aplicarse mediante el mantenimiento.
Aire comprimido
Un compresor de aire de 100 CV puede consumir electricidad por valor de 50.000 € al año y hasta el 30% de esa electricidad se destina a dar presión a aire que no se utiliza como consecuencia de fugas en la distribución y prácticas que suponen desperdicio. Sin embargo, nunca se ha evaluado la eficiencia del funcionamiento del aire comprimido de muchas instalaciones. De hecho, cuando una mayor presión de aire es necesaria, muchas instalaciones adquieren y ponen en funcionamiento un compresor adicional, sin darse cuenta de que pueden obtener más presión del sistema con el que ya cuentan.
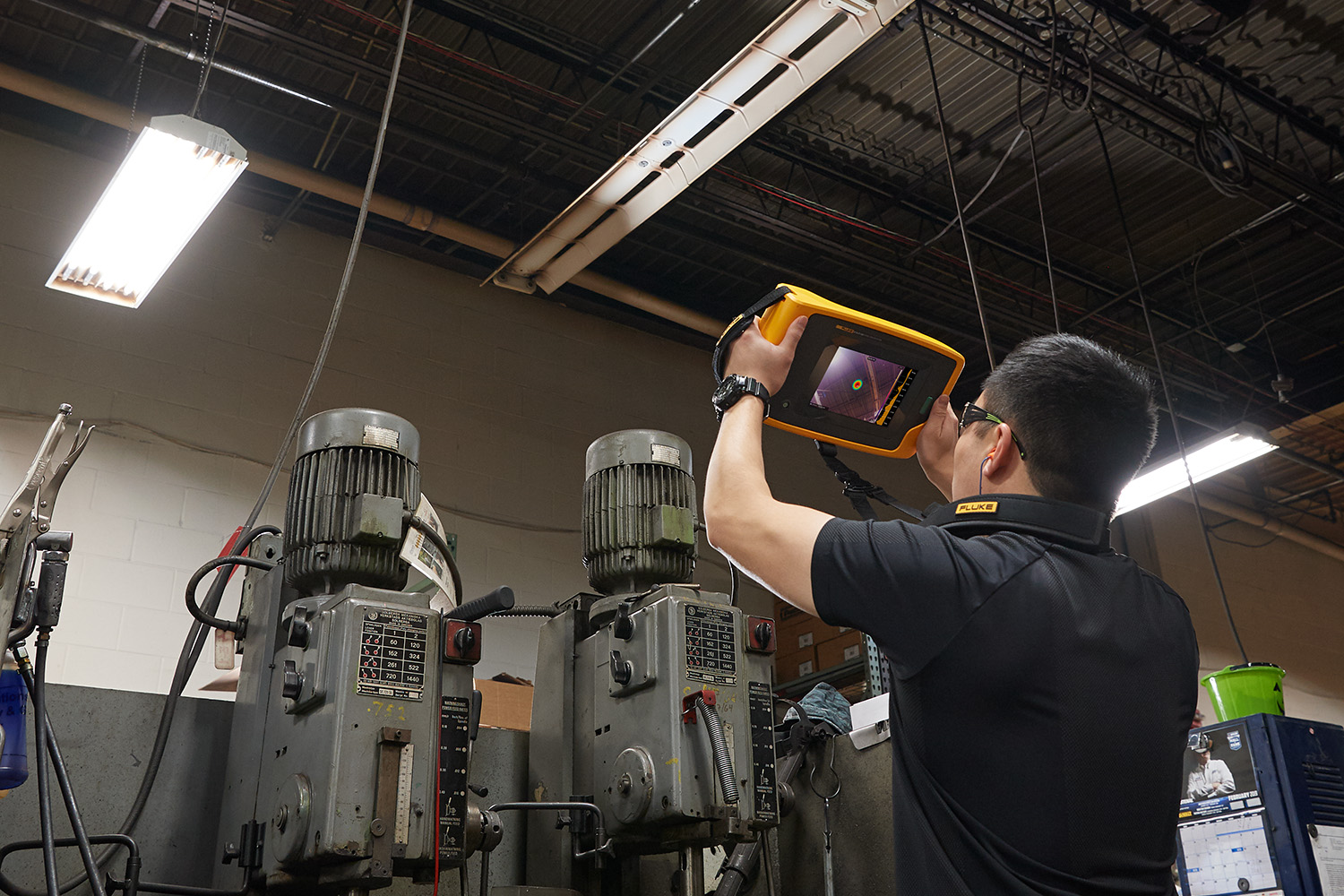
Inspección de los conductos de aire comprimido con la cámara acústica industrial Fluke ii900
Según los estudios de Compressed Air Challenge, solo el 17% de los usuarios de aire comprimido considera la eficiencia como un objetivo de la gestión del sistema de aire comprimido. El 71% simplemente desea un suministro de aire fiable y constante. Esa filosofía llega hasta el punto del uso: las instalaciones con equipos neumáticos a menudo no disponen ni siquiera de válvulas solenoides y hacen funcionar el compresor de manera continua, y el personal de base a menudo utiliza el aire comprimido como un recurso gratuito, y lo usa para limpiar el área de trabajo e incluso para refrescarse.
Para identificar y cuantificar el nivel de desperdicio, empiece por registrar la corriente en un ciclo completo de funcionamiento en todos los compresores de aire. Eso definirá cuánta energía se necesita para producir los niveles de presión de aire actuales. Utilice también un calibrador de manómetros para registrar la presión a la salida del compresor en comparación con el punto de uso. Determine el nivel de caída de presión y verifique el valor de presión exigida por el fabricante para el funcionamiento del equipo; no aplique una presión excesiva "solo porque sí". Utilizar un módulo de presión conectado a un multímetro de registro es una manera de realizar estas pruebas sin invertir en equipo especializado. Por último, utilice una cámara acústica industrial para inspeccionar todo lo que sea posible de la línea de aire con el fin de determinar la ubicación y el volumen de las fugas de aire. Calcule su rendimiento de la inversión con esta calculadora de fugas de aire.
Conclusión
Por último, puede hacer grandes progresos para mejorar la eficiencia energética a nivel de planta con estas prácticas recomendadas sencillas y directas. Aportan valor de manera individual, pero cuando se combinan, pueden convertirse en una fuente de ahorro de energía.