- Infrared building inspection checklist
- Select the right thermal camera
- What to look for during a home inspection
- What is thermal imaging?
Thermal cameras are used as a key technology for building inspection work worldwide, allowing many building professionals to work faster, saving you time in the field, spot and document hidden issues during your inspection, and even help you to show a problem you’ve uncovered with visual proof. And, adding a new service of thermal imaging to your building inspection process can set you apart from your competition.
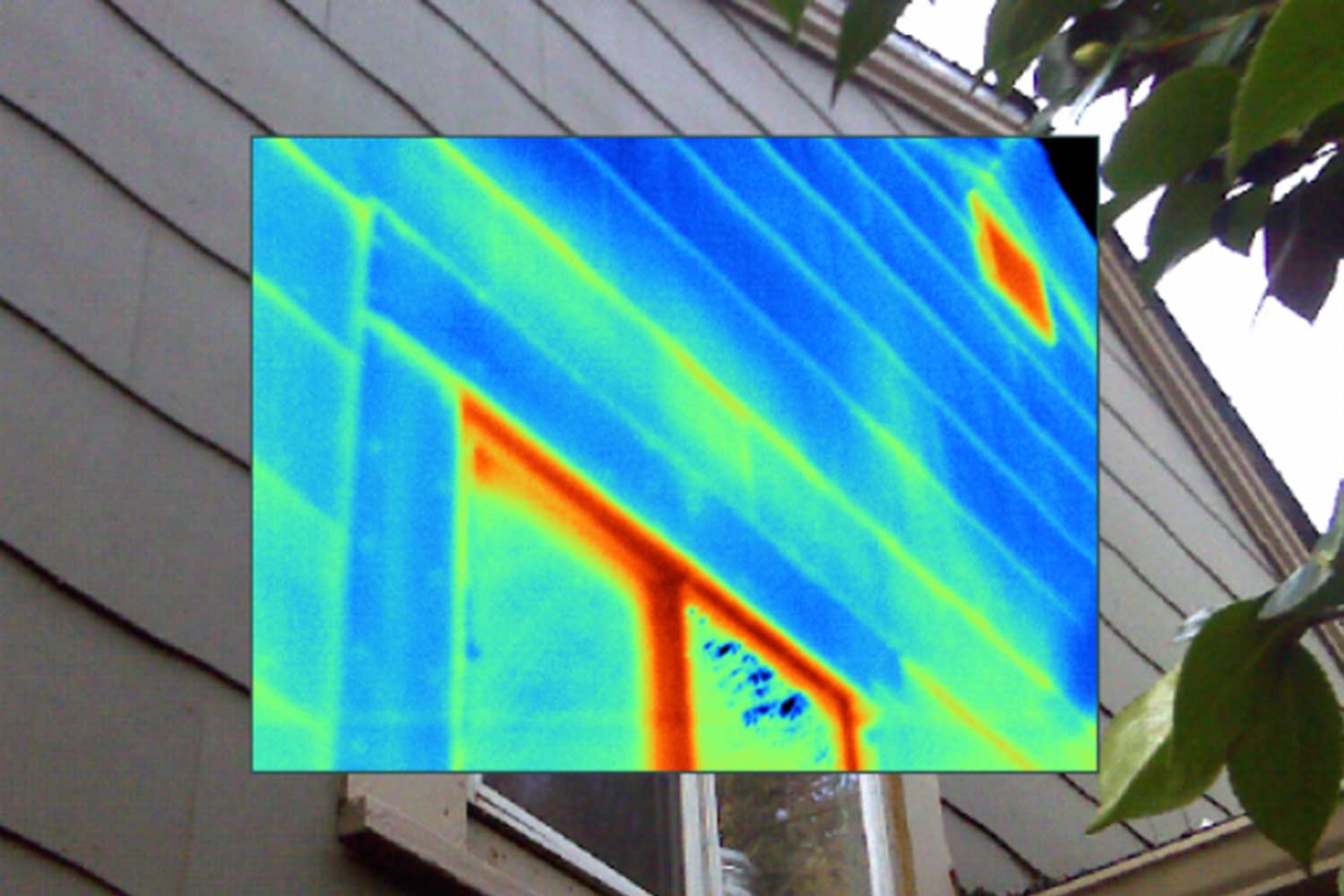
Best practices for performing an infrared building inspection
There are many steps in performing an effective residential or industrial building thermal imaging inspection. Follow this checklist of steps to set yourself up for the best report and information at the end.
Exterior inspection checklist
- Perform a visible inspection of the exterior.
- Note any unusual visible issues or areas of concern.
- Confirm there is a difference in temperature of at least 18 °F (10 °C) from interior to exterior surfaces (or confirm that conduction inspection can effectively be performed with less). Typically, a stable difference in temperature for a period of at least four hours is preferred.
- Record interior air temperature and humidity.
- Record exterior air temperature and humidity.
- Record exterior weather conditions.
- Include other environmental factors such as position of sun, precipitation, etc.
- Record exterior wind direction and speed.
- If conditions permit, perform a systematic inspection of exterior to inspect for conduction issues (insulation, thermal bridging, etc.)
- Note any anomalies or unexpected thermal patterns.
Interior inspection checklist
- Perform a visible inspection of the interior.
- Look for leaks or evidence of moisture.
- Note any unusual visible issues or areas of concern.
- Turn on the HVAC system to make sure it is heating and cooling properly.
- Check HVAC ductwork and electrical components.
- Check all electrical outlets and switches.
- Conduct an infrared inspection of the service panel.
- Note any anomalies or hot spots.
Blower door test
- Close all exterior doors and windows on the building.
- Open all interior doors.
- Turn off the HVAC system, leave it off for at least 15 minutes.
- Perform a systematic inspection of the interior.
- Check for conduction issues (insulation, thermal bridging, etc.). Note any anomalies or unexpected thermal patterns.
- Make sure that all combustion appliances (furnaces, stoves, heaters, etc.) are completely turned off. If a fireplace is present, cover all ash with damp paper or otherwise contain it so it does not spread.
- Properly install a blower door.
- Depressurize residence to approximately 20 pascals.
- Perform a systematic inspection of residence interior for air infiltration (assuming approximately 5 °C (9 °F) delta-T or appropriate confirmation that inspection can still be reasonably conducted).
- Note any anomalies, interstitial air bypasses, or areas of air infiltration.
- Reverse direction of blower door and/or pressurize house to approximately 20 pascals.
- Perform a systematic inspection of residence exterior for air exfiltration (assuming approximately 5 °C (9 °F) delta-T or appropriate confirmation that inspection can still be reasonably conducted).
- Note any anomalies, air bypasses, or areas of air exfiltration.
Select the right thermal camera
When selecting the thermal camera to carry with you on jobsites, keep the performance specifications you need, the environment you’re working in, the features that will help you do your job, and the reporting software you’ll use in mind.
Thermal camera specs and features checklist
- IR resolution: Minimum - 120x120
- Thermal sensitivity: 100mK or better (lower is better) (at least .10ºC (at 30ºC))
- Field of View (FOV): Approximately 20 degrees or more
- One-handed usage allows a free hand for ladders or crawl spaces
- No dangling parts (i.e., lens cap, wrist strap) that can get caught up
- Drop rated - 6.5 feet
- IP 54 dust and ingress protection
- Protective lens guard and integrated cap
- Fluke IR-Fusion® technology
- In-camera annotation features
- Software to help you view, annotate, and analyze images
- Software to create your final report
Infrared Performance
Many standards and guidelines exist worldwide that provide recommendations on the proper use and methodology when using thermal imagers for building inspections. The minimum equipment requirements proposed by Residential Energy Services Network (RESNET) are:
- IR resolution: Minimum - 120x120
- Thermal sensitivity: 100mK or better (lower is better) (at least .10ºC (at 30ºC))
- Field of View (FOV): Approximately 20 degrees or more
Building Inspection Environment
When shopping for a thermal camera, you want to keep your environment in mind. The ergonomics, durability, and IP rating to deal with certain weather conditions are important to pay attention to.
Having a thermal camera that allows you to operate the camera and focus one-handed is highly recommended. It is very likely that you will at some point need to use your thermal camera in an attic, crawl space, or another unstable place where having a free hand for stability will be safer for you.
Accidents happen, find a thermal camera designed to handle tough working conditions. Look for camera with a drop test rating and IP rating so you know they are protected from water and dust ingress.
Make sure that your camera has an operating and storage temperature that is suitable for the environment where you are working. Having a protective guard or integrated cap for the lens will also protect your investment when you’re on the job.
Thermal imaging camera features
Think through the kind of features that will help you do your job more accurately and quickly.
- Fluke IR-Fusion® technology, with AutoBlend™ mode, combines an infrared and thermal image for aid in detection and analysis as well as professional, easy-to-understand reports.
- Built-in IR-PhotoNotes™ allows you to capture photos of the equipment or surrounding area to be tied to the thermal image of interest. These contextual photos are often invaluable.
- Text and voice annotation capabilities also exist to save notes that can help you remember what the issues was when you’re finalizing your report.
Thermal imaging software
Software that you can use to view, annotate, and analyze your thermal images helps you finish out the job. Fluke offers multiple Thermal Imaging Software options that allow you to create fully customizable and professional reports. There are multiple software options, including Smartview Classic, Smartview R&D, Fluke Connect, and Fluke Baseline Thermography Software. You can use the software that best fits your needs.
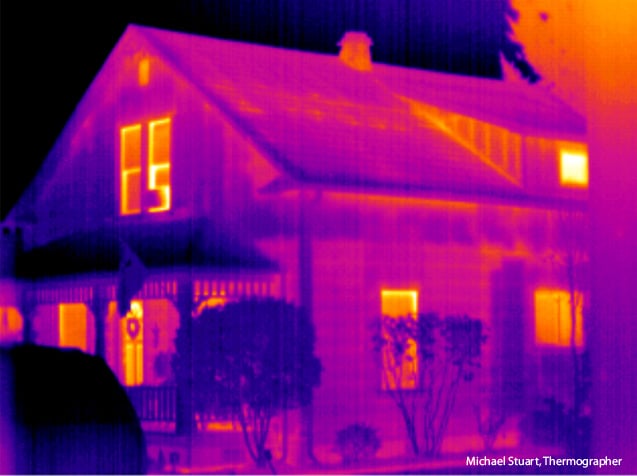
What to look for during a home inspection
Thermal imaging allows you to quickly identify many building defects and issues. When you’re running through the checklist, these are the types of issues you may find with a thermal imager.
Poor or missing insulation
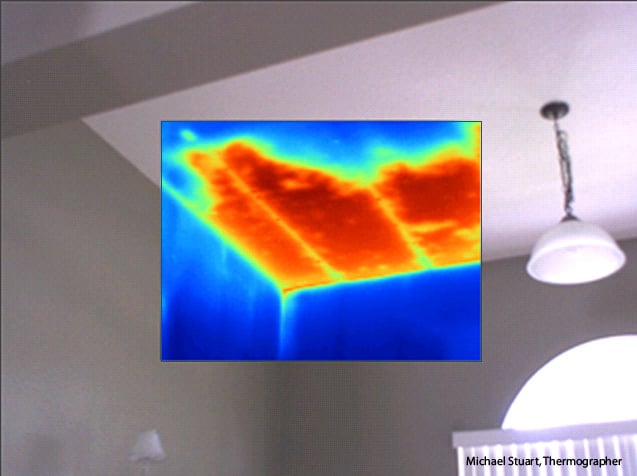
When insulation has settled over time, is missing, or damaged, a thermal camera can often pick up a different thermal pattern compared to the rest of the wall. These areas can often be a source of heat loss or gain, and, if bad enough, can lead to significantly higher energy usage.
Moisture or leak inspections
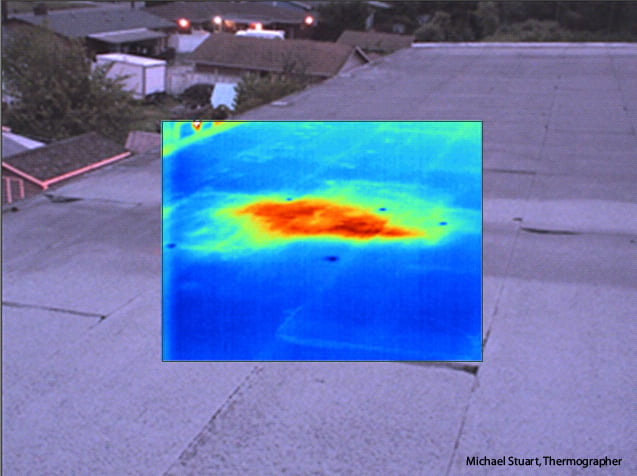
Moisture in roofing materials often leads to two scenarios:
- Water leaks into the structure
- Reduced insulating properties of the roof itself.
Due to the difference in thermal capacitance of wet building materials versus dry ones, moisture problems in flat or low-slope built-up roofs can often quite easily be detected with the use of a thermal imager. Infrared inspections can often accurately identify the critical problem areas, so a repair can be done, preventing premature full replacement costs.
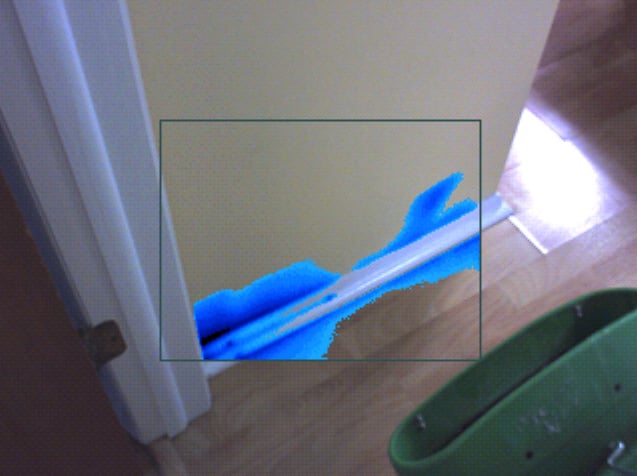
Like with roof leaks, thermal cameras can be used to find moisture trapped in walls and floors. Damp areas change temperature more slowly than dry areas, and are subject to evaporative cooling. This slow change in temperature allows them to become visible to the thermal camera. Causes of this unwanted moisture include plumbing leaks, leaks from the outside, and condensation.
Moisture in these types of situations can often be a precursor to mold, mildew, and air quality problems. This, in turn, can create both occupant comfort and health issues when subject to prolonged exposure.
Electrical inspections
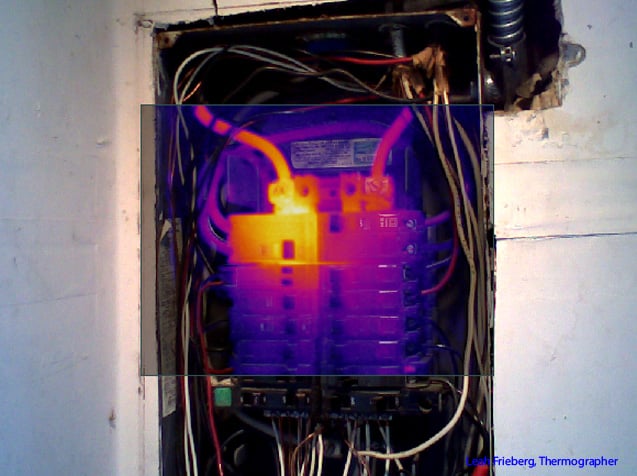
Heat can often be a sign of electrical problems such as loose, over-tightened, corroded connections, or other component failures. These areas can be seen easily with a thermal image, allowing qualified individuals to correct problems before significant damage or major failure occurs.
HVAC system inspections
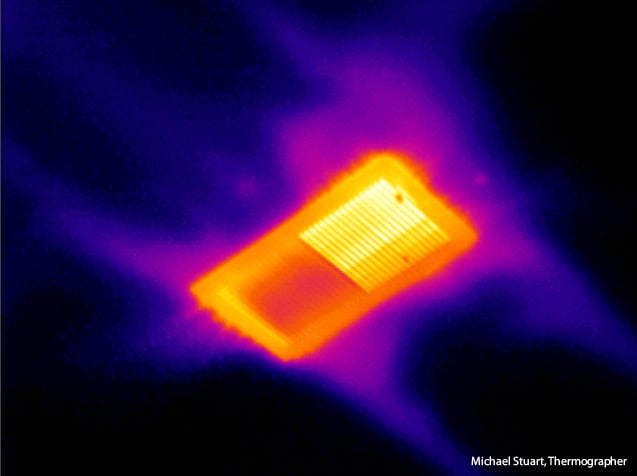
A thermal camera can be used to check whether HVAC equipment is heating or cooling properly. You can check that the electrical components are working as designed, determine if ductwork is delivering the conditioned air to the right places or if it is instead leaking, increasing the cost to heat or cool the building.
Air leaks
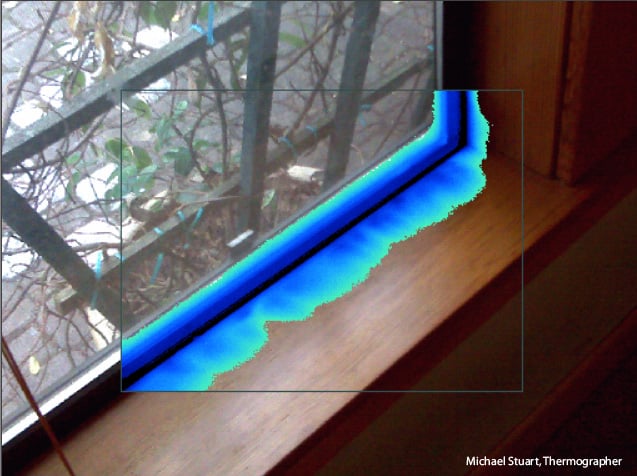
Cold air seeping through a leak will cool the areas around it, and hot air can warm the areas around it as well. In this case, the cool air leaking in through the window is visible with a thermal imager. Thermal imaging can also be used to identify heat escaping from a structure.
When combined with a blower door, an infrared camera is a powerful tool to identify potential convective energy loss. Your customers can achieve significant energy costs savings once these issues have been resolved.
Radiant floor heating system issues
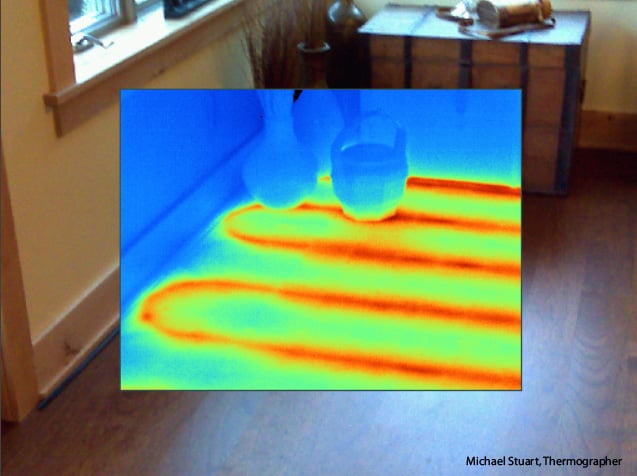
Both electrical and hydronic in-floor heating systems are subject to installation issues and failures over time. A thermal imaging camera can be used to locate where the floor heating runs, identify leaks, obstructions, or short-circuits (depending on the type of system), and troubleshoot uneven heating issues. A thermal camera can also be used to verify installations and repairs, if needed.
Thermal bridging
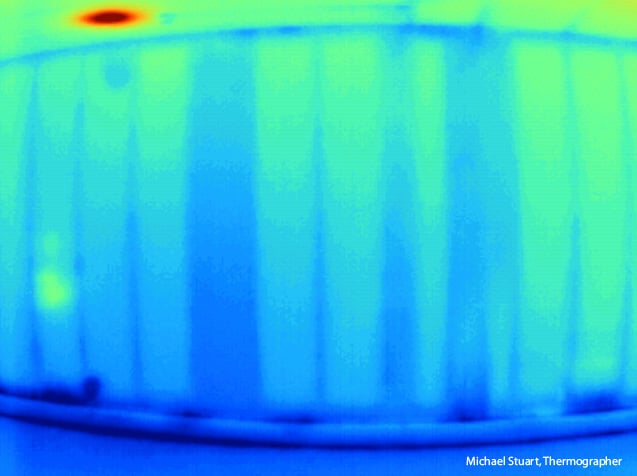
Thermal bridges are pathways by which heat can move from one place to another via conduction or direct contact between building materials. It is normal to see this in many types of construction, but minimizing it with proper design and insulation can reduce heat loss or gain within a building envelope. Under the proper conditions, a thermal camera allows the user to easily detect and document areas where thermal bridging is occurring and decide if any action is warranted.
Improper renovations
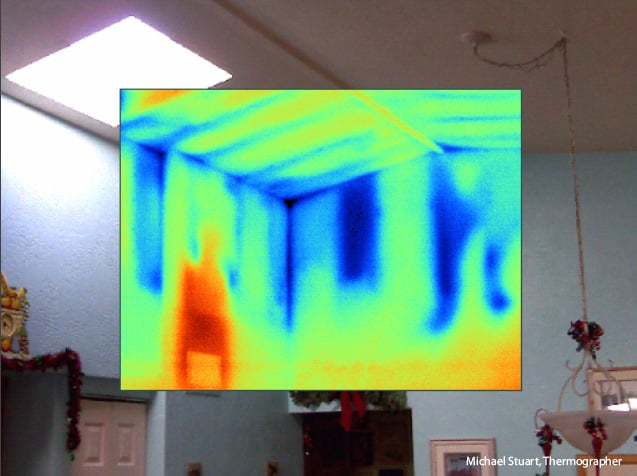
Before and after infrared images can verify that a renovation was done correctly and will be more effective at reducing energy costs. If you’re inspecting a building that is being prepared for an upcoming renovation a thermal image can often help to indicate the underlying structure and design, and even speed up both planning and construction.