The gains in motor control and system efficiency made possible by variable frequency motor drives (VFDs) have made these devices almost universal in modern building control and manufacturing systems.
"VFD-controlled motors are a standard option in almost all new equipment today, and at this point are nearly ubiquitous," said Dave Williams, Technical Services Supervisor for McKinstry, a major consulting, construction, energy, and facility services firm based in Seattle. "VFDs are also a good retrofit option for our customers, and if we're maintaining motors that are not controlled by VFDs then we're recommending that they be installed. VFDs allow us to efficiently match the motor output to a load in ways not previously possible and can provide significant energy savings for our customers."
By controlling the speed and output of an electric induction motor, a VFD adjusts the performance of driven equipment (such as pumps and fans) to precisely meet changing demands, and do so without the complication of valves, belts, louvers, and other mechanical control devices required by old-style systems. But there is a trade-off.
Challenge: shaft voltages
"We specialize in maintaining the built environment through service contracts that we offer potential customers," Williams said. "We provide a range of maintenance plan options from quarterly inspections to once a year. We're looking at their equipment on a regular basis, taking measurements, documenting equipment parameters. We maintain a number of critical environments, such as data centers and manufacturing facilities, and in those environments we pay very close attention to motor operation. One way we do that is by measuring shaft voltages."
A VFD works by converting incoming three-phase line power into dc current, then creating a synthetic three-phase sine wave output from that dc current. The frequency of that output can be adjusted or varied (the V in VFD) to control motor speed and output.
"The normal ac power that is delivered to an ac motor is balanced between the phases," Williams said. "However, when ac power is routed through a VFD the power is no longer balanced and, due to the high-speed switching frequencies used in pulse width modulation (PWM) inverters, a voltage is induced on the motor shaft. The significance is that this voltage builds and looks for a path to ground, and if the motor shaft isn't grounded, then the path of least resistance is often through the motor bearings."
Though the motor housing is grounded, the shaft often is not. In these conditions voltage in will continue to build up on the motor shaft until it reaches a level great enough to arc across the motor bearings to the motor housing and to ground. "As the voltage arcs across the motor bearings it breaks down the bearing lubricant and pits the bearing rolling elements, damaging them."
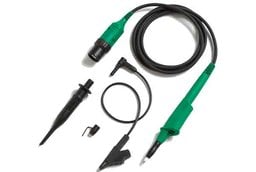
Don't lose your bearings
Motors powered by the rapidly switching frequencies inherent in PWM inverters may experience shaft voltages up to 70 V or greater. Such voltages can overcome the insulating properties of bearing lubricant. When passing across a bearing, the resulting arcs result in pitting, fluting, fusion craters, and, eventually, premature bearing failure. "It's become a common problem," said Williams, "and any motor controlled by a VFD is susceptible."
Some protection is available via a variety of shaft grounding kits that combine both contact and non-contact nanogap technology and direct the shaft voltage to ground.
A motor failure in a critical facility, such as a data center, manufacturing line, or building environmental system, is disruptive and costly. So McKinstry preventive maintenance programs have long included motor bearing analysis.
"There are a lot of reasons bearing damage occurs," Williams said. "Bearing damage can result from dirty lubricant, corrosion, a lack of lubrication, over-lubrication, excessive motor loading, and a host of other reasons. But the one that's been difficult for us to diagnose, until damage has already occurred, is damage due to shaft voltages."
A new insight
Today that problem is solved. McKinstry has been measuring motor shaft voltages using a special shaft probe and the Fluke 190 Series II ScopeMeter®, a four-channel, handheld oscilloscope that makes it possible to detect shaft voltage problems, and to verify the fix after shafts have been properly grounded. The procedure may become a standard part of their preventive maintenance process.
"In addition to the bearing test," Williams said, "and probably as a leading indicator of what's going on within the bearing, that would be a preliminary test we would use for our customers, and it would provide a great baseline of information for us.
"It really would be applicable for any customer, but especially for new customers and for sites where they have critical applications, we would go through and test shaft currents and voltages to see if anything's there on a preliminary to gauge how the motor's operating regarding shaft voltages."
Setup is simple
Williams said setup for the test is simple. Technicians need only limited instruction. "Fifteen to twenty minutes and they're good to go," Williams said.
In many test situations, systems must be shut down temporarily to eliminate hazards from moving equipment or live electric circuits. The technician then uses a magnetic base to place a microfiber probe in contact with the motor shaft. When safety and access allow it, the probe can be held by hand. A second probe makes contact with the motor case. The equipment is then operated as normal, and readings recorded on the ScopeMeter show the shaft voltage waveform.
The results can be dramatic, as is the difference after the shaft is properly grounded with a sleeve engineered for that purpose (see illustrations 1 and 2).
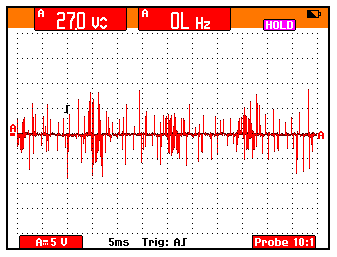
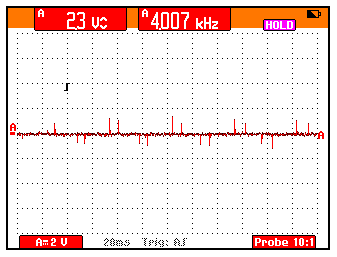
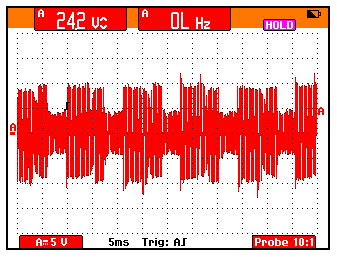
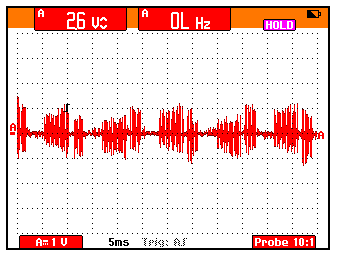
"I don't think we've set a threshold," Williams said. "Some of the voltages we've seen have been in the teens, and higher. That certainly indicates you're getting voltage traveling through the shaft. Typically, for a motor where you've eliminated the problem, it's down to close to zero."
Seeing is believing
"We've been installing what's called a shaft grounding kit," Williams said. "It consists of some sort of carbon element, either a brush or a hard carbon element, that rides on the shaft and therefore provides a path to ground for your voltage—a path of least resistance through the shaft grounding kit, instead of going through your bearings." Some kits are installed on the drive end of the motor, while others are fitted to the non-drive side. The cost of such kits can reach $400 to $500 per installation, Williams said.
Is it difficult to convince customers to pay for such a solution?
"Not for customers with critical environments," Williams said, "because there are technical people there who understand technical issues. They've heard about this issue, and understand it. And with that graph, seeing is believing. Being able to show them that is key."
Even after the sale is made and the kit installed, Williams foresees performing periodic follow-up tests to ensure the fix is still performing.
"Every mechanical system eventually fails," he said. "So you still take readings. You may not have to do them quarterly, like we do our maintenance inspections, but maybe you take them annually to make sure the system is still working. Whatever level of protection the customer wants and needs."
A higher level of service
For critical customers, like those operating data centers that house millions worth of equipment and information, top-shelf protection has proven valuable.
"Our guys have been using the tool, and the results have been dramatic," Williams said. "They've been finding transient voltages in a lot of these motors in these data centers that we maintain, and it's opening the customers' eyes. It's providing a higher level of service and protection for our customers, and giving us information we've never had before.
"One reason we're really excited about the technology is that we think it gives us the capability to provide true value for our customers when it comes to motor operation," He added. "We can catch things before damage occurs, which is key. You eliminate downtime for your customer. That's gold."
About McKinstry
Established in 1960, McKinstry is a full-service design, build, operate, and maintain (DBOM) firm with more than 1,600 employees and approximately $400 million in annual revenue. McKinstry's professional staff and trades people deliver consulting, construction, energy, and facility services. As an early adopter of the DBOM process, the company advocates collaborative and sustainable solutions that are designed to ensure occupant comfort, improve systems efficiency, reduce facility operational costs, and ultimately optimize client profitability for the life of their building.