When it comes to detecting leaks and ensuring efficient operations, the choice of an acoustic imaging camera can be crucial. In this article, we will compare two popular models from Fluke, the ii900 Industrial Acoustic Imager and ii910 Precision Acoustic Imager. By examining their similarities and differences, we aim to assist customers in making an informed decision.
Applications for acoustic imagers
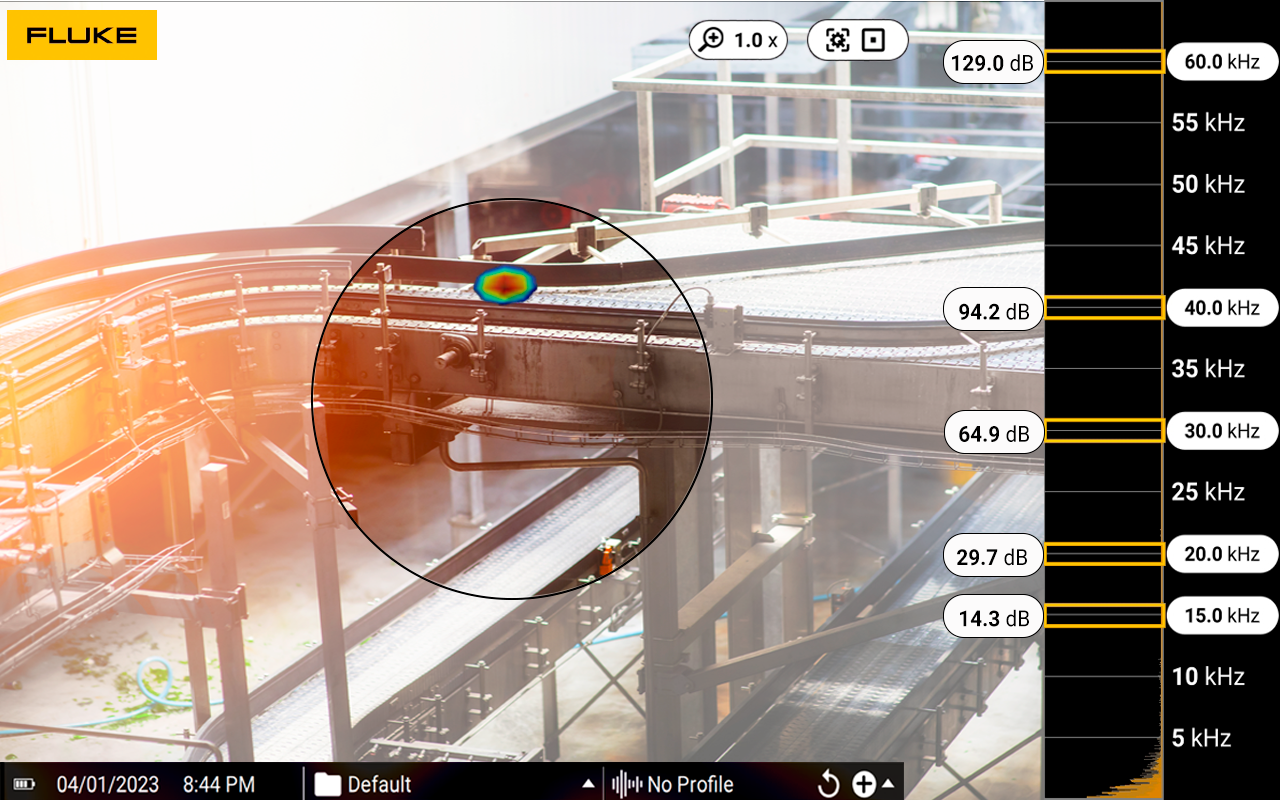
The ii910 MecQ™ Mode enables the detection of mechanical deterioration in conveyor systems. This is especially useful for large, hard-to-access systems. The ii910 is equipped to detect electrical partial discharge (PD) issues on insulators, transformers, switchgears, and high-voltage powerlines.
The ii900 and ii910 are designed to detect air, gas and vacuum leaks quickly and easily. Compressed air, gas and vacuum leak detection has never been simpler. These devices can identify the repairs needed in compressed air and gas systems.
Fluke acoustic imagers are similarly designed
- Leak detection technology utilizes an array of microphones. These microphones detect sounds outside the human hearing range. Two such technologies are the Fluke ii900 and ii910 Acoustic Imagers.
- The pitch of a detected leak is converted into a Visual SoundMap™ image. This image allows users to see the location of the sound source.
- Both tools allow users to quickly scan an area for issues. When an issue is detected, a quick press of the button captures shareable photos and videos.
- Equipped with 7" LCD touchscreen displays, these cameras provide an intuitive interface for seamless operation.
- Technicians can use the interfaces of both cameras to isolate sound frequencies, even in loud environments.
- Cameras offer enhanced efficiency for plant inspection. They can inspect the entire plant or system during peak operations in just a few hours.
The specifications of the two acoustic imaging cameras are similar. However, the frequency range, distance, minimum frame rate and reporting functionality vary significantly.
ii900 leak detection | ii910 corona, PD and leak detection | |
---|---|---|
Frequency range | 2 kHz to 52 kHz | 2 kHz to 100 kHz |
Distance | 0.5 to > 50 meters (1.6 to > 164 feet) | 0.5 to > 120 meters (1.6 to > 393 feet)* |
Minimum frame rate | 12.5 FPS | 25 FPS |
Reporting functionality | LeakQ | LeakQ PDQ mode |
Acoustic imaging reporting tools
- The LeakQ Report Generator is a useful tool for compressed air, gas, and vacuum leak detection. It is available for both ii900 and ii910 cameras. It gives users the power to create organized and detailed reports. It includes captured images, leak size analysis, and leak cost estimations.
- Exclusively for the ii910, the PDQ reporting tool allows users to create comprehensive reports for PD detection. It includes images captured by the camera and the ability to share these results with relevant stakeholders.
Selecting the right acoustic imager
Choosing the right acoustic imaging camera can significantly impact leak detection and functional efficiency. Both Fluke models share common features such as leak detection, visual SoundMap™ images, quick scanning, and user-friendly interfaces. However, the ii910 offers additional capabilities, including mechanical deterioration detection and electrical partial discharge identification.