Get peak variable speed drive efficiency through power quality analyzer
Variable-speed motors and drives are normally much more efficient than fixed-speed types, but even they don’t always work at peak efficiency. An analysis of VSDs at one drinking water pumping station helped save over 20% of energy costs – repaying many thousands of Euros every year.
Load measurement at input and output of a VSD
The main energy cost for water companies comes from pumping water up from the well and through the network. Variable-speed drives match output to demand and so help minimize energy costs. Even VSDs can run inefficiently, though, with any of several root causes.
Optimize the drive parameters
The most common way of improving VSD efficiency is to optimize the drive parameters. Stretching the motor ramp-up time and optimizing the pump rotation speed (the PID controller allows small speed differences) saved around 3% of the overall pumping station energy with no loss of effectiveness (the exact motor speed is not critical because the network acts like a buffer). That saving may not sound significant, but can amount to several thousand Euros a year.
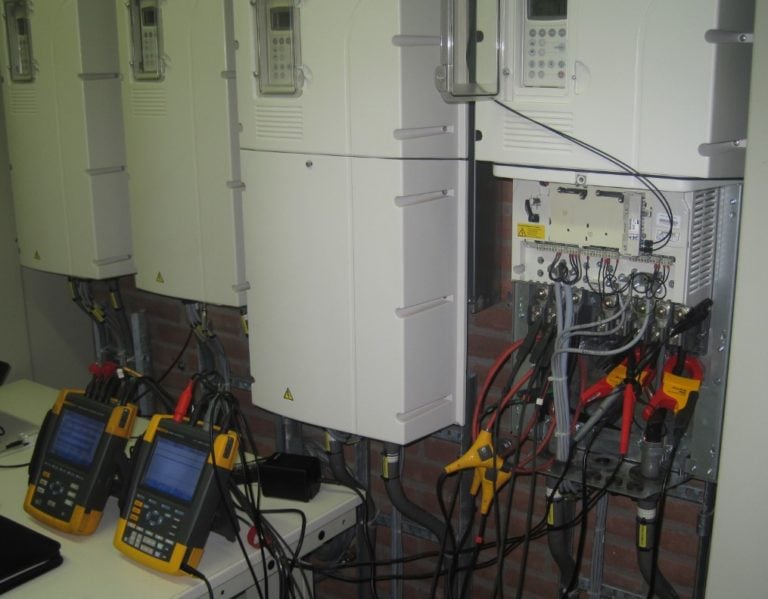
Load measurement at input and output of a VSD
Ensure motors run at nominal load
Much larger savings can come when multiple motors run in parallel, since motors (and pumps) reach their best efficiency when running at nominal load. The efficiency of a 50hp motor at nominal load is around 93% for example, but at 10% load the efficiency drops to 45%.
Each line in the pumping station has three pumps. They don’t all operate 24/7 because redundant operation is needed for ultimate reliability.
Water pumps working in parallel
The pumps have different capacities (nominal loads). Selecting the pump that that most closely matches the water demand allows it to operate close to the nominal load (all three pumps work in parallel at maximum water demand).
Simple analysis, significant savings
This simple software change needed no extra hardware, and gave the company above 20% energy savings, all stemming from a simple analysis with Fluke’s 435 Power Quality Analyzer. Two meters were used during the test, to measure both input and output power of the drive simultaneously. The second instrument in this case was a Fluke ScopeMeter, although today you can also use a Fluke 438 Power Quality and Motor Analyzer.
The savings were part of an ISO 50001 energy improvement process, and are an excellent example of how energy improvements pay for themselves.