In today’s rapidly evolving industrial landscape, the role of the industrial plant maintenance technician is becoming increasingly central to ensuring operational efficiency, sustainability, and a strong return on investment for industrial equipment. As companies pivot towards integrating more sustainable energy sources and technologies, such as on-site solar power generation and Electric Vehicle Supply Equipment (EVSE), the skillset and toolkit of maintenance technicians must evolve accordingly. This shift not only underscores the industry's commitment to environmental stewardship but also aims to capitalize on the economic advantages of reduced operational costs and improved energy efficiency.
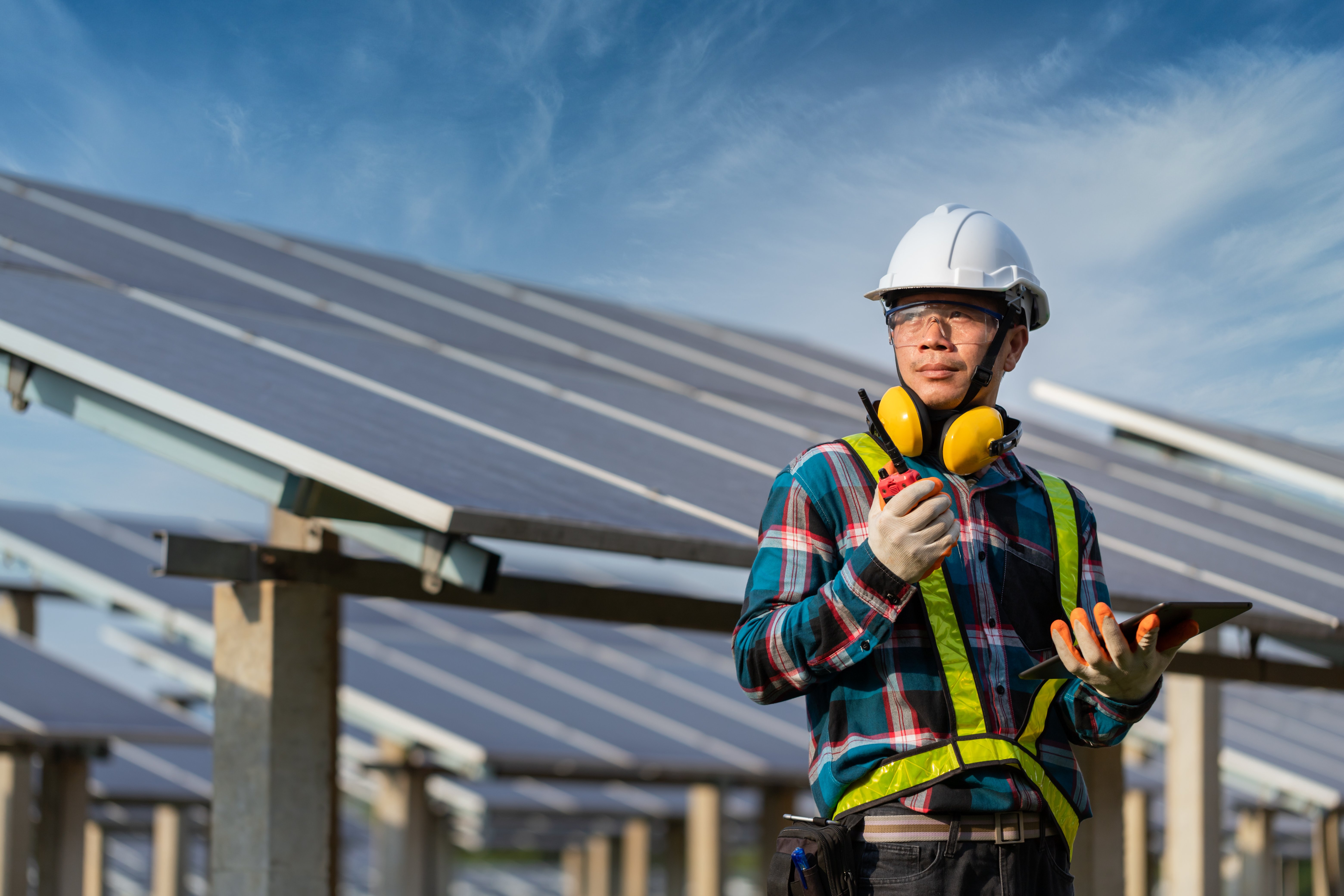
The adoption of on-site solar energy systems and EVSE reflects a broader trend towards enhancing corporate sustainability and operational efficiency. Solar power offers a renewable energy source that can significantly reduce electricity expenses and contribute to a lower carbon footprint. Concurrently, the integration of EVSE supports the burgeoning infrastructure for electric vehicles, promoting cleaner transportation methods and underscoring a company’s forward-thinking approach to environmental responsibility. For maintenance technicians, this means an expanded role that involves mastering new technologies and maintaining systems that are vital to the future of industrial operations.
The Ins and Outs of Industrial Solar
Industrial solar power systems are engineered to meet the substantial energy demands of businesses, manufacturing plants, and utility providers. These systems harness sunlight, converting it into electrical energy using photovoltaic (PV) panels. The electricity generated by these panels is in direct current (DC) form, which inverters then convert into alternating current (AC) for use in industrial operations or for feeding into the electrical grid. Additionally, these systems often include batteries for energy storage, allowing for the use of solar power even when the sun isn't shining, along with various other components like switches, fuses, and cables to ensure safe and efficient operation.
Regular Inspection and Maintenance of Industrial Solar
To ensure these systems operate at peak efficiency and to extend their operational lifespan, regular inspection and maintenance are crucial. This process involves several critical tasks:
- Inspecting PV Modules for Physical Damage: PV modules can be damaged by environmental factors such as hail, heavy snow, or debris. Regular inspections help identify and mitigate such damage early, preventing efficiency losses or potential hazards.
- Cleaning the Array: Dust, bird droppings, and other debris can significantly reduce the efficiency of PV panels. Regular cleaning ensures the panels operate at optimal efficiency by maximizing their exposure to sunlight.
- Inspecting the Wiring: Wiring within solar power systems must be inspected regularly for signs of wear, damage, or corrosion, which could lead to decreased performance or safety risks.
- Testing the Inverters: Inverters play a crucial role in converting DC to AC. Testing these ensures they are efficiently converting the generated power without significant losses.
- Assessing the Battery Storage Systems: For systems with energy storage, regular checks on the health and efficiency of batteries are vital to ensure they are charging and discharging correctly and to anticipate replacement before failure.
When to Perform Maintenance on Industrial Solar
Maintenance schedules can vary based on several factors including the system's size, location, and the manufacturer’s recommendations. Systems in areas with high dust, pollen, or frequent bird activity might require more frequent cleaning and inspections. Similarly, seasonal changes may necessitate adjustments in maintenance frequency, with some components needing more attention during periods of high usage or adverse weather conditions.
What to Look for in Industrial Solar
During maintenance, technicians pay close attention to:
- Signs of Physical Damage: Cracks, warping, or discoloration on panels, and signs of rust or corrosion on metal components.
- Electrical and Mechanical Integrity: Secure and intact wiring, properly functioning switches and fuses, and the physical condition of inverters and batteries.
- Operational Performance: Actual energy output compared to expected performance, efficiency of inverters, and health of battery storage systems.
How Maintenance is Performed on Industrial Solar
Maintenance tasks involve a combination of physical inspections, cleaning, and electrical measurements. Tools like the Fluke multimeters and clamp meters are essential for electrical testing, while insulation testers help assess the condition of wiring and components. Cleaning of PV modules typically requires specialized equipment to gently remove debris without damaging the panels.
By adhering to a regular maintenance schedule and using precise, reliable tools, technicians can significantly improve the performance and lifespan of industrial solar systems. Proper maintenance not only ensures these systems operate efficiently, contributing to energy savings and reduced carbon footprints, but also safeguards the investment by preventing costly repairs and downtime.
Exploring EV Charger Maintenance
EVSE plays a crucial role in the infrastructure supporting the adoption and use of plug-in electric vehicles. This equipment, encompassing everything from the charging stations to the software and hardware required for charging electric vehicles, ensures that electric vehicles are charged safely, efficiently, and reliably. Maintenance of EVSE systems is as crucial as maintaining any piece of industrial equipment, ensuring operational reliability and safety for users.
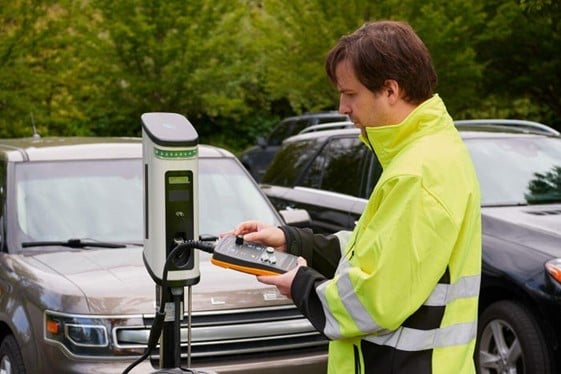
Regular EV Charger Maintenance and Inspection
Just like any critical infrastructure, EVSE systems require regular inspection and maintenance to operate effectively. This routine work involves several key tasks:
- Inspecting Charging Cables: Over time, charging cables may suffer from wear and tear due to regular use and exposure to environmental conditions. Regular inspection can identify any physical damage, fraying, or electrical faults that might compromise safety or functionality.
- Testing Charging Stations for Correct Power Output: To ensure electric vehicles are charged correctly and efficiently, it's essential to regularly test the power output of charging stations. Maintenance technicians use tools like multimeters and clamp meters to verify that the charging station is delivering the expected voltage and current.
- Ensuring Safety Systems Function Correctly: EVSE systems are equipped with various safety systems designed to protect the vehicle, the charging station, and the user. These include ground fault protection, overcurrent protection, and connectivity checks. Technicians must regularly test these systems to ensure they are operational, as any failure in these systems could lead to unsafe charging conditions.
When to Perform EV Charger Maintenance
Routine maintenance should be scheduled based on the manufacturer’s recommendations and usage patterns. High-traffic EVSE locations may require more frequent inspections and maintenance than those less frequently used. Additionally, environmental conditions such as extreme weather, dust, and humidity levels can also dictate the frequency of maintenance activities.
What to Look for When Troubleshooting EV Chargers
During maintenance, technicians are on the lookout for several key issues:
- Physical Damage: Signs of physical damage to cables, connectors, and the charging station itself.
- Electrical Issues: Incorrect voltage or current output, insulation wear, and improper grounding.
- Operational Efficiency: Charging times and efficiency, ensuring they meet the specifications.
- Safety and Compliance: Ensuring all safety measures are in place and functional, and the system complies with local electrical codes and standards.
How EV Charger Maintenance is Performed
Maintenance is performed using a combination of visual inspection, functional testing, and electrical measurements. Technicians use tools like the Fluke multimeters, clamp meters, and insulation testers to perform detailed checks on the electrical components. Software diagnostics may also be used to check the health and efficiency of the charging station's software systems.
By maintaining EVSE systems properly, technicians ensure that these systems are safe, efficient, and reliable, supporting the continued growth and adoption of electric vehicles. Regular maintenance not only prevents downtime and extends the lifespan of the charging equipment but also ensures a safe charging environment for all users.
Selecting Tools for Versatility and Performance
Industrial plant maintenance technicians are vital for ensuring the operational efficiency and safety of various industrial settings. They need to maintain a broad range of equipment, including general plant infrastructure, solar power installations, and Electric Vehicle Supply Equipment (EVSE). To achieve this, technicians utilize a range of sophisticated tools that are versatile enough to handle tasks across these domains. Here’s how four specific Fluke tools can be applied across general plant maintenance, solar maintenance, and EVSE maintenance.
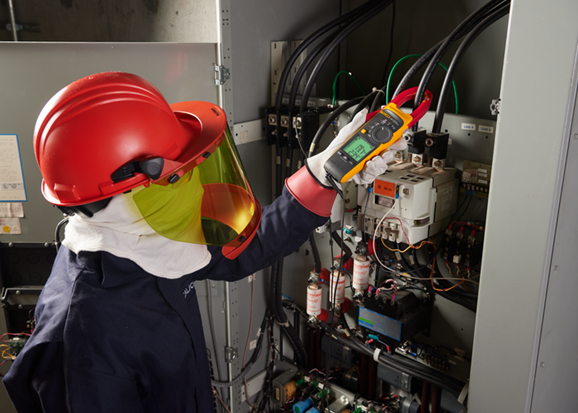
- Fluke 87V Industrial Multimeter
- CAT and Voltage Rating: CAT III 1000V, CAT IV 600V
- General Plant Maintenance: This multimeter is indispensable for troubleshooting electrical issues within the plant. It can diagnose problems in motors, pumps, wiring, and other electrical equipment by measuring voltage, current, and resistance accurately.
- Industrial Solar Maintenance: For solar installations, the Fluke 87V excels in measuring voltage, current, and resistance in photovoltaic (PV) panels or inverters, helping technicians ensure optimal performance and identify issues like underperforming panels or faulty inverters.
- EV Charger Maintenance: It's also valuable for checking power output at charging stations, ensuring they are delivering the correct voltage and current for electric vehicle charging.
- Fluke 1587 FC Insulation Multimeter
- CAT and Voltage Rating: CAT III 1000V, CAT IV 600V
- General Plant Maintenance: This tool tests the insulation in cables, a critical aspect of maintaining electrical safety and efficiency in the plant infrastructure.
- Industrial Solar Maintenance: It tests insulation resistance in strings of PV modules, identifying potential leaks or degradation that could affect the overall efficiency of the solar panels.
- EV Charger Maintenance: It also tests the insulation resistance in charging cables, ensuring they are safe and effective for high-voltage electric vehicle charging.
- Fluke 378 FC Non-Contact Voltage True-rms AC/DC Clamp Meter with iFlex
- CAT and Voltage Rating: CAT III 1000V, CAT IV 600V
- General Plant Maintenance: Plays a crucial role in monitoring power quality, helping reduce energy costs and prevent premature equipment failure by detecting power quality issues.
- Industrial Solar Maintenance: Assesses power output from inverters to ensure efficient conversion of solar energy into electrical energy.
- EV Charger Maintenance: Measures power output at EV charging stations, verifying that they function within specifications for reliable electric vehicle support.
- Fluke Ti480 PRO Infrared Camera
- Temperature Range: ≤ -20°C to 1000°C (-4°F to 1832°F)
- General Plant Maintenance: Enables technicians to detect hot spots and potential failure points in electrical systems and mechanical equipment without direct contact, facilitating preventative maintenance.
- Industrial Solar Maintenance: Helps identify underperforming PV cells or modules by visualizing temperature variations, indicating inefficiencies or faults.
- EV Charger Maintenance: Useful for spotting overheating problems in charging stations and connectors, promoting safe and efficient operation.
These tools, with their robust features and safety ratings, equip maintenance technicians to ensure the smooth operation, reliability, and safety of industrial plants, solar installations, and EV charging infrastructure, highlighting their critical role in modern industrial and energy sectors.
Embracing the Challenge
The shift towards on-site solar power and EVSE in industrial settings is not merely a nod to sustainability but a strategic move to optimize operations and embrace the future of energy. Maintenance technicians are at the heart of this transition, wielding their expertise to ensure these systems deliver on their promise of efficiency and sustainability. Their role is crucial in navigating the complexities of modern industrial maintenance, making informed choices about tool selection, and ensuring the longevity and efficiency of these cutting-edge systems. As industries continue to evolve, the value of skilled maintenance technicians, equipped to handle both traditional and emerging technologies, has never been more evident.