Endroits difficiles, outils robustes
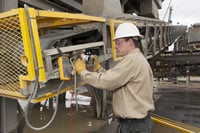
Sur le terrain, les cimentiers-finisseurs se tiennent prêts à former du béton pré-mélangé humide à destination d'un nouveau tronçon d'autoroute. Les bétonnières sont alignées devant l'usine de mélange de béton, dans l'attente de leur chargement. Mais attendez ! Un problème électrique a arrêté l'usine. Il est temps d'appeler Keithly Electric.
Des dizaines d'opérateurs d'équipements, artisans, ouvriers, conducteurs et administrateurs des routes attendent que le mélange soit en route, la pression est intense. Tout le monde se pose la question : Combien de temps va prendre la réparation ?
« Ils vous poseront cette question mot à mot dès que vous sortirez de votre camion » a déclaré l'électricien et programmateur Keithly, Greg Burdick. Lorsque la pression est là et que « le temps c'est de l'argent », Keithly sait que la clé du succès est d'avoir un personnel expérimenté disposant d'une large gamme de compétences pour remettre rapidement en marche l'usine.
Depuis que le fondateur Bob Keithly a lancé cette entreprise en 1967, Keithly Electric s'est concentré sur des relations étroites avec ses clients et ses employés. Aujourd'hui, les trente-cinq employés de l'entreprise travaillent dans toute la zone du grand Seattle, sur des navires, des grues et des barges, dans des bâtiments et des logements, dans l'agroalimentaire et les usines aéronautiques, en construisant et entretenant tout, des conduits et fils de tous les jours aux automates programmables industriels (API) complexes. Comme elle l'a fait depuis ses débuts, l'entreprise maintient en fonctionnement de nombreuses usines de béton, d'asphalte et d'agrégats de construction.
Un vrai caractère
Les usines de matériaux présentent de nombreux risques pouvant faire s'arrêter leurs équipements : la poussière et le sable recouvrent tout, et l'eau utilisée pour laver les éclaboussures de gravier descend dans les structures et le sol. Ces usines sont légères et rapides, il n'y a pas de « plan B » à déclencher lorsque des problèmes électriques arrêtent le processus. Burdick arrive donc sur le terrain en sachant qu'il est essentiel pour les exploitants de l'usine de reprendre leurs activités. C'est un terrain difficile, mais Greg Burdick est un gars très solide.
Il a relevé des défis bien plus sérieux que cet environnement de travail difficile. Une infection par une bactérie mangeuse de chair (fasciite nécrosante) l'a presque tué il y a plusieurs années. Il a perdu sa jambe gauche en dessous du genou, et une partie de son pied droit. Mais il a gardé son sens de l'humour.
« C'est un trait de caractère qui ne fait pas vraiment partie du job », plaisanta-t-il. Il est retourné au travail après qu'une évaluation ait conclu qu'il pouvait réaliser « toutes les choses horribles qu'un électricien peut avoir à faire ».
Burdick ne se contente pas de seulement réparer ce qui est cassé. Burdick et l'équipe de Keithly travaillent avec les exploitants d'usine pour restructurer et automatiser les systèmes de l'usine afin d'améliorer leur efficacité et leur fiabilité. Les systèmes API que Keithly conçoit et fabrique connectent et commandent des variateurs de fréquence (VFD), des capteurs, des alarmes et autres éléments. À l'aide de panneaux de commande à écran tactile, un seul opérateur peut faire fonctionner toute une usine.
L'un de ces clients est un gros fournisseur régional d'agrégats broyés et lavés et d'asphalte, une installation tentaculaire de 250 hectares dans les environs.
Au-delà de l'usine d'asphalte de l'installation et après le bureau principal et les balances, se dresse l'usine de matériaux, un complexe de broyeurs, convoyeurs interconnectés, tamis de criblage et laveurs qui ressemblent à des montagnes russes.
Un peu plus loin on trouve des tas de blocs de roche et les puits où le sable, le gravier et la pierre, poussés ici par les glaciers de l'ère glaciaire, sont chargés sur des camions-bennes de 100 tonnes. Ces camions transportent alors leur chargement vers les tamis à grille, où une série de barres parallèles très résistantes sépare les gros cailloux et autres débris des matières de plus petite taille. Le sable, le gravier et les petits cailloux tombent sur un convoyeur pour commencer leur périple à travers les concasseurs à cônes, d'autres convoyeurs, tamis de criblage et laveurs. Les gros éléments, des blocs de roche allant jusqu'à 1,20 mètres ou plus de large, tombent dans un puits pour attendre d'être déplacés vers le concasseur à mâchoires.
Une visite de l'usine vous montre que la force brute n'est pas la seule à être impliquée dans le concassage de la roche. Par exemple, pour éviter que les blocs ne s'accumulent et ne les bouchent, les grilles doivent être vidées après quelques chargements. Par le passé, cela voulait dire que les conducteurs de camions devaient appuyer un bouton pour enregistrer chaque chargement.
Keithly a eu une meilleure idée. Burdick a monté des boucles à induction sur les rails des grilles pour détecter le moment où les camions arrivent et repartent. Les boucles ont été à l'origine conçues pour être placées sous la chaussée pour détecter les voitures attendant aux feux. Les signaux de boucle indiquent à présent au système de commande le nombre de chargements que chaque grille a reçu et confirment que les camions sont partis et que les grilles peuvent être vidées. Un panneau de commande d'API monté à proximité des grilles supervise le processus.
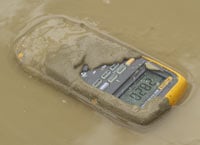
Trouver une meilleure méthode
Le capteur de grille fait partie d'un système de commande remanié que Keithly a récemment réalisé pour l'usine. Un écran tactile montre à présent à l'opérateur une représentation graphique de toute l'usine, avec ses multiples trémies, convoyeurs et concasseurs. Les afficheurs présentent l'état de chaque moteur, trieur et pompe, ainsi que le niveau de charge de chaque silo de matériau. Résultat : le système automatisé détecte les problèmes tels que les débordements de matériau, et les signale à l'opérateur avant qu'ils ne deviennent vraiment gênants. La production augmente et les coûts d'exploitation se réduisent.
Lorsqu'il reçoit des appels pour des interventions et que la pression monte, Burdick reste concentré sur le processus. « Il s'agit d'être aussi complet et méthodique que possible, ce n'est que du dépannage », a-t-il déclaré. « Vous n'avez pas à comprendre le système, mais vous devez en savoir assez sur les composants pour trouver un point de départ. Très souvent, vous devez rassembler les pièces au fur et à mesure. »
Le processus peut n'impliquer qu'un test électrique, allant des contrôles directs de tension, courant et de terre, au dépannage des VFD de plus en plus répandus. « J'ai testé beaucoup de variateurs, et les tests de l'extrémité avant et de l'extrémité arrière des variateurs, l'unité motrice, reviennent principalement à un contrôle de diodes », a déclaré Burdick. « Le contrôle de diodes est une fonction du multimètre. Il mesure la tension qu'il faut pour qu'une diode s'allume. »
Burdick contrôle également la fréquence synthétique du VFD, en utilisant la fonction que l'on trouve sur quelques multimètres numériques Fluke. « Le nouvel instrument que j'ai, le Fluke 28 II, a un filtre passe-bas pour contrôler les variateurs de vitesse. Je l'ai utilisé pour vérifier que l'afficheur sur le variateur était correct, » a déclaré Burdick.
En fait, le multimètre Fluke 28 II, avec son indice de protection IP67, pour la protection contre l'eau et la poussière et son coefficient de chute de trois mètres, a été précisément conçu pour les conditions rudes dans lesquelles Burdick travaille.
« Le problème des chutes vient habituellement des échelles », plaisantait Burdick. « Chaque fois que vous travaillez en hauteur, vous courrez le risque de secouer l'échelle ou de faire quelque chose pour la faire tomber. La meilleure chose que j'utilise avec mes instruments est probablement le kit d'aimants (le kit de suspension magnétique pour multimètre Fluke ToolPak™). »
Il y a aussi l'eau.
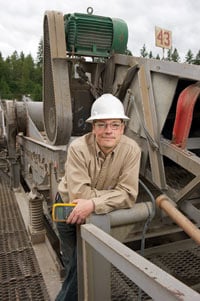
Le problème de l'humidité
« Une fois, j'ai failli ruiner mon autre bon instrument », a déclaré Burdick. « Je suis allé d'un panneau de contrôle à une cabine de commande sous la pluie. Le temps d'arriver à la cabine de commande pour contrôler l'autre extrémité du circuit, le cadran s'était rempli d'eau car je tenais l'instrument vers le haut. »
Et avec le Fluke 28 II ? « Je ne m'en préoccupe plus », a-t-il déclaré. « J'ai vu le 28 II à la Rockwell Automation Fair de 2009 en Californie, reposant dans un réservoir d'eau. Je me suis dit ok, c'est ce qu'il me faut. »
Pour travailler sur les panneaux de commande, Burdick utilise à la fois son Fluke 28 II et des multimètres Fluke 189. « Pour la basse tension, généralement les signaux DC, et si je réalise des mesures de courant, je fais davantage confiance au 189 », a-t-il déclaré. « J'utilise la pince multimètre Fluke 771 assez souvent lorsque je travaille sur des signaux analogiques. Vous n'avez pas à rentrer dans le circuit pour faire un relevé. Je n'ai trouvé aucune différence significative entre cette mesure et les mesures où vous entrez dans le circuit et l'exécutez via votre instrument. »
Lorsqu'il teste des panneaux de centre de contrôle des moteurs, Burdick fait confiance à un contrôleur de résistance d'isolement plus ancien, le Fluke 1520. « La plupart des charges de nos clients sont des charges motrices », a-t-il déclaré. « Je l'utilise tout le temps pour tester si un moteur a sauté ou si un câble est court-circuité. »
La mise à la terre d'un équipement est une autre chose essentielle à prendre en considération. Les usines de matériaux suivent le règlement de l'US Mine Safety and Health Administration (MSHA), qui comporte des exigences strictes concernant la mise à la terre. « Il y a un programme d'assurance de mise à la terre », a déclaré Burdick. « Toutes les usines doivent être testées tous les ans. La continuité de mise à la terre de chaque moteur doit être testée. Si je dois réaliser une de ces tâches, j'utilise ce Fluke 1520 avec les valeurs basses en ohm.
« Si le moteur est en court-circuit ou si le câblage n'est plus raccordé à la boîte de raccordement, il doit y avoir un chemin de faible résistance vers la terre afin de déclencher le disjoncteur. J'ai déjà vu un cas où la terre n'était pas continue, et où il n'y avait pas de chemin efficace vers les tiges de terre du système. En cas de défaut, la structure sera effectivement sous tension. Avec des moteurs 480 volts, lorsque vous agrippez le rail et que vous êtes dans une flaque d'eau, cela peut être très inconfortable. »
Tenir la distance
Parfois, un service client a besoin de littéralement tenir la distance. Un jour, une usine de mélange de béton a signalé que son gros tambour mélangeur, la partie qui s'incline pour remplir les bétonnières, faisait des siennes. Le mécanisme de bascule, qui normalement fonctionnait à vitesse variable pour amortir le choc lorsque le réservoir lourd se déplaçait, ne fonctionnait qu'à une vitesse. L'usine ne pouvait pas s'arrêter, donc le diagnostic a dû être réalisé pendant que le système était en marche.
À l'aide de son multimètre Fluke 189, Burdick a restreint son investigation au tableau de contrôle.
« Le tableau de contrôle n'envoyait plus de signal DC. Et la seule manière de le détecter était que lorsque j'ai relié l'instrument à la borde de sortie, le diagramme à barres analogique en bas de l'instrument dansait, » a-t-il déclaré.
«Un signal DC, c'est fiable. Mais quelque chose n'allait pas avec le déclenchement du signal DC par le tableau de contrôle. Il sautait partout, entre deux et huit volts. L'électrovanne a fini par moyenner le signal. Le tableau était tout simplement défaillant. »
Il a fallu une connexion spéciale pour remplacer le tableau de contrôle défaillant sans arrêter l'usine pendant des jours. Dan Keithly connaissait une autre usine de mélange de béton, qui n'était pas en service, équipée des mêmes contrôles. Il a contacté le propriétaire et s'est arrangé pour emprunter le tableau. Il lui a fallu deux heures et demie de route pour récupérer le tableau de contrôle de remplacement.
Mais ce temps a été bien mis à profit. Le client a pu continuer à faire tourner l'usine. Et pour Keithly Electric, c'est l'essentiel.