Quel est le rapport entre la mesure et les économies d’énergie ? Il s’agit avant tout de retour sur investissement et de bénéfices nets.
Les installations industrielles doivent consommer de l’énergie pour fonctionner, que ce soit pour les produits, les données ou autres, mais la plupart des usines gaspillent trop d’électricité. Elles sont énergivores. Il y a vingt ans, les responsables d’installations ne se souciaient pas de l’efficacité énergétique : l’énergie était bon marché. Lorsque l’énergie est devenue plus chère, les responsables se sont intéressés à la réduction de leur facture énergétique, mais la conversion en termes commerciaux n’allait pas de soi.
À partir de quel point de conversion la réduction du gaspillage produit-elle un retour sur investissement positif ?
Pour répondre à cette question, vous devez déterminer combien d’énergie vous consommez sur les différents types de travail (systèmes) dans votre bâtiment et comparer ces chiffres aux valeurs de référence. Cela vous indiquera la quantité de gaspillage énergétique. Des mesures supplémentaires peuvent vous permettre d’identifier les causes de ce gaspillage. Les trois points d’une équation de ROI sont : 1) la quantité de pertes combinée à 2) la cause et 3) le coût à assumer.
Dans quels cas la réduction de la consommation d’énergie a-t-elle un sens ?
La réduction de la consommation d’énergie est nécessaire pour les installations qui souhaitent réduire leurs coûts généraux, afin d’augmenter leur productivité et optimiser ainsi leur exploitation, sans se contenter de dépenser moins.
L’analyse énergétique identifie les possibilités d’accroissement de l’efficacité et donne au responsable de l’installation toutes les données nécessaires pour identifier les économies au vu des objectifs premiers, et celles qui présentent un retour sur investissement insuffisant ou trop éloigné des priorités. Les installations anciennes avec des systèmes imposants et énergivores présentent généralement les meilleures possibilités, car elles n’ont pas été optimisées. Les installations de production faiblement automatisées ou disposant de peu de leviers d’amélioration, ainsi que les installations équipées de grands systèmes à vapeur ou à air comprimé sont également d’excellentes sources d’optimisation.
Combien peut-on économiser ?
Selon le Department of Energy (DOE) américain, dans l’absolu, les installations peuvent réduire leur facture énergétique de 25 %, mais les économies réelles dépendent de plusieurs facteurs. Premièrement, quels systèmes et activités s’exécutent dans l’installation ? Les charges importantes qui n’ont jamais été mises en corrélation avec les tarifs des fournisseurs d’énergie pour profiter des heures creuses permettent généralement de dégager des économies significatives. Inversement, les installations dont les charges sont plus réduites ne permettent pas de faire ce type d’économie. Deuxièmement, quel est le degré d’inefficacité énergétique des systèmes du bâtiment ? Une installation récente et bien entretenue ne permettra pas de réaliser autant d’économies qu’une installation plus ancienne, où les systèmes et les équipements ne correspondent plus aux réglages et aux pratiques de maintenance recommandés.
Lorsque vous pensez aux pertes énergétiques à la maison, vous pensez probablement à l’air froid qui s’infiltre par la fenêtre ou au remplacement des vieilles ampoules par des ampoules LED. Quel type de « perte énergétique » a lieu dans une usine de fabrication ou polyvalente ?
Utiliser de l’énergie pour chauffer ou refroidir l’air et le faire passer par le système de ventilation, pour ensuite le laisser s’échapper par la fenêtre, force le système à surproduire, et donc à surconsommer. Combien d’autres systèmes dans l’installation travaillent plus qu’ils ne le devraient, à cause de filtres bouchés, de moteurs surdimensionnés ou d’autres défauts ?
Il est donc possible qu’une usine de fabrication ou polyvalente souffre de pertes énergétiques à la fois au niveau de l’éclairage et de l’isolation du bâtiment. Mais ces problèmes sont-ils les plus urgents ?
Il est impossible de répondre à cette question avant d'avoir analysé la consommation d’énergie au niveau de toutes les charges majeures, de l’avoir rapprochée des tarifs des fournisseurs d’énergie et du planning d’exploitation, et d’avoir calculé le retour sur investissement. Le plus souvent, les économies d’exploitation et de maintenance réalisées sur des équipements de grande taille permettent, au bout de quelques années, d’accélérer le remplacement des équipements par des modèles plus efficaces.
Comment amorcer la réduction de la consommation d’énergie lorsque les budgets, le temps et les ressources sont tous limités
Partez d’un point de référence.
Pour commencer, identifiez ce qui consomme de l’énergie, où et quand. Une fois que le propriétaire, les responsables et les techniciens de l’installation connaissent exactement la quantité d’énergie nécessaire au fonctionnement de l’installation par rapport à la quantité d’énergie gaspillée, ils peuvent alors prendre des décisions et élaborer des plans. Pour y parvenir, commencez par rassembler des exemplaires des dernières factures énergétiques et recherchez la présence de pénalités et de frais pendant les périodes de consommation de pointe. Téléchargez un exemplaire de la grille tarifaire sur le site Web de votre fournisseur d’énergie, afin de connaître le coût de l’énergie en fonction des différents moments de la journée, par rapport à votre planning d’exploitation. Si nécessaire, appelez directement votre fournisseur d’énergie qui se fera un plaisir de vous répondre.
Demandez ensuite à vos électriciens ou à votre sous-traitant de relever la consommation d’énergie au niveau des alimentations électriques principales du fournisseur, ainsi qu’au niveau des panneaux d’alimentation des systèmes importants et des charges clés. Relevez les kW, les kWh et le facteur de puissance sur une période de temps représentative. Cela vous fournit une image très précise de la consommation d’énergie réelle sur des circuits et des charges triphasés au fil du temps. Les plus grosses économies sont parfois réalisées en déplaçant les plus fortes charges à des moments de la journée où l’énergie est moins onéreuse.
Quels sont les systèmes qui gaspillent le plus d’énergie ?
Outre la cartographie du système d’alimentation électrique, évaluez vos systèmes électromécaniques, à vapeur et à air comprimé. Ces systèmes sont généralement très gourmands en énergie, mais il est assez facile de les réparer.
Électromécanique
Il existe cinq types courants de pertes d’énergie dans un système électromécanique : 1) électrique, 2) mécanique/friction, 3) planification, 4) commandes et 5) dimensionnement/efficacité.
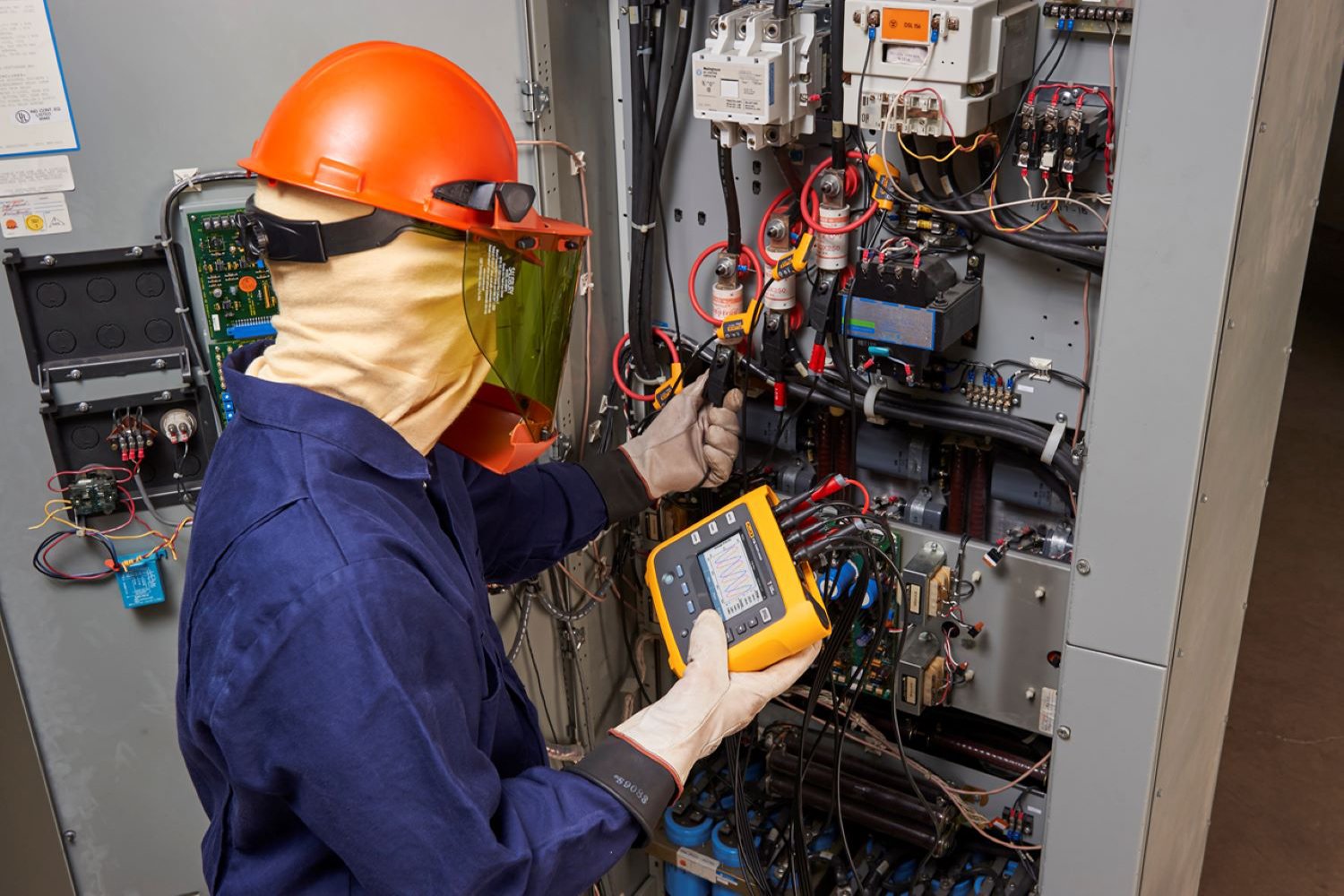
Utiliser un enregistreur évolué de la qualité du réseau électrique Fluke 1738 pour effectuer une étude énergétique sur un système mécanique
- Les surcharges de tension/courant ainsi que les déséquilibres de phase génèrent le plus de pertes énergétiques dans les systèmes électromécaniques. Ces deux problèmes électriques peuvent être détectés à l’aide d’analyseurs de la qualité du réseau électrique et de caméras thermiques.
- Les situations mécaniques qui gaspillent de l’énergie se manifestent par une surchauffe, ainsi que des vibrations excessives, qui peuvent être détectées à l’aide d’une caméra infrarouge et d’un testeur de vibrations. Les causes possibles sont variées : problèmes de refroidissement et de circulation de l’air, mauvais alignement des roulements et autres sources de friction. Effectuez une analyse thermique des couplages, arbres, courroies, roulements, ventilateurs, composants électriques, boîtiers de terminaison/raccordement et enroulements ; tous les éléments qui peuvent indiquer une exploitation inefficace, et donc des pertes énergétiques.
- Comme mentionné précédemment, une des solutions les plus simples pour réaliser des économies d’énergie est de relever la consommation d’énergie au niveau des charges électromécaniques importantes sur l’intégralité du planning d’exploitation. Déterminez à quel moment les machines consomment le plus d’énergie (souvent au démarrage) et vérifiez si les horaires d’utilisation peuvent être adaptés aux moments de la journée où le tarif du fournisseur est le moins élevé.
- À l’aide de l’analyse de la consommation, comparez également le planning opérationnel à la fréquence de consommation d’énergie des machines. Quelle quantité d’énergie les machines consomment-elles lorsqu’elles ne sont pas en fonctionnement actif ? Sans l’utilisation de commandes, la plupart des machines doivent être éteintes manuellement pour ne plus consommer d’énergie, et les actions manuelles sont rarement effectuées. Il est impossible d’éteindre toutes les machines, mais la plupart d’entre elles peuvent être mises en veille. Les commandes varient d’un système simpliste à une automatisation complète, à l’aide de capteurs et de minuteurs, de machines à mise en veille flexible ou d’un API avec codage en dur de l’exploitation.
- Dimensionnement et cote d’efficacité. Dans les installations anciennes tout particulièrement, les exigences opérationnelles changent alors que les charges restent identiques, ce qui signifie qu’un gros moteur coûteux et difficile à démarrer continue d’entraîner un système moins exigeant en matière de puissance. La tendance naturelle d’un responsable d’installation est de prolonger au maximum la durée de vie d’un équipement important. Néanmoins, cela vaut la peine de relever la consommation énergétique du moteur et de la comparer aux exigences de charges actuelles, ainsi qu’aux nouvelles unités plus efficaces et mieux dimensionnées. Calculez à combien s’élève la consommation excessive d’énergie et multipliez-la par la grille tarifaire. Déterminez le temps nécessaire pour que le moteur amortisse son coût de lui-même : parfois, il y a un intérêt financier à remplacer les équipements avant qu’ils ne tombent en panne. Dans le cas contraire, vérifiez si certaines commandes ne peuvent pas être utilisées pour moduler la puissance de sortie du moteur.
Vapeur
Le chauffage des procédés représente une part importante des coûts d’exploitation contrôlables et le système doit être inspecté régulièrement pour éviter différents types de pertes énergétiques.
Pour commencer, relevez la consommation d’énergie au niveau de la chaudière afin d’obtenir une base de référence pour la consommation d’énergie. Ensuite, inspectez le système de distribution, notamment les purgeurs de vapeur, les manomètres, l’isolation, les pompes et les soupapes. Utilisez une caméra thermique pour détecter les purgeurs défectueux, les fuites, les obstructions, les problèmes de valeurs et de condensat : le but est de renvoyer autant de condensat préchauffé que possible dans la chaudière.
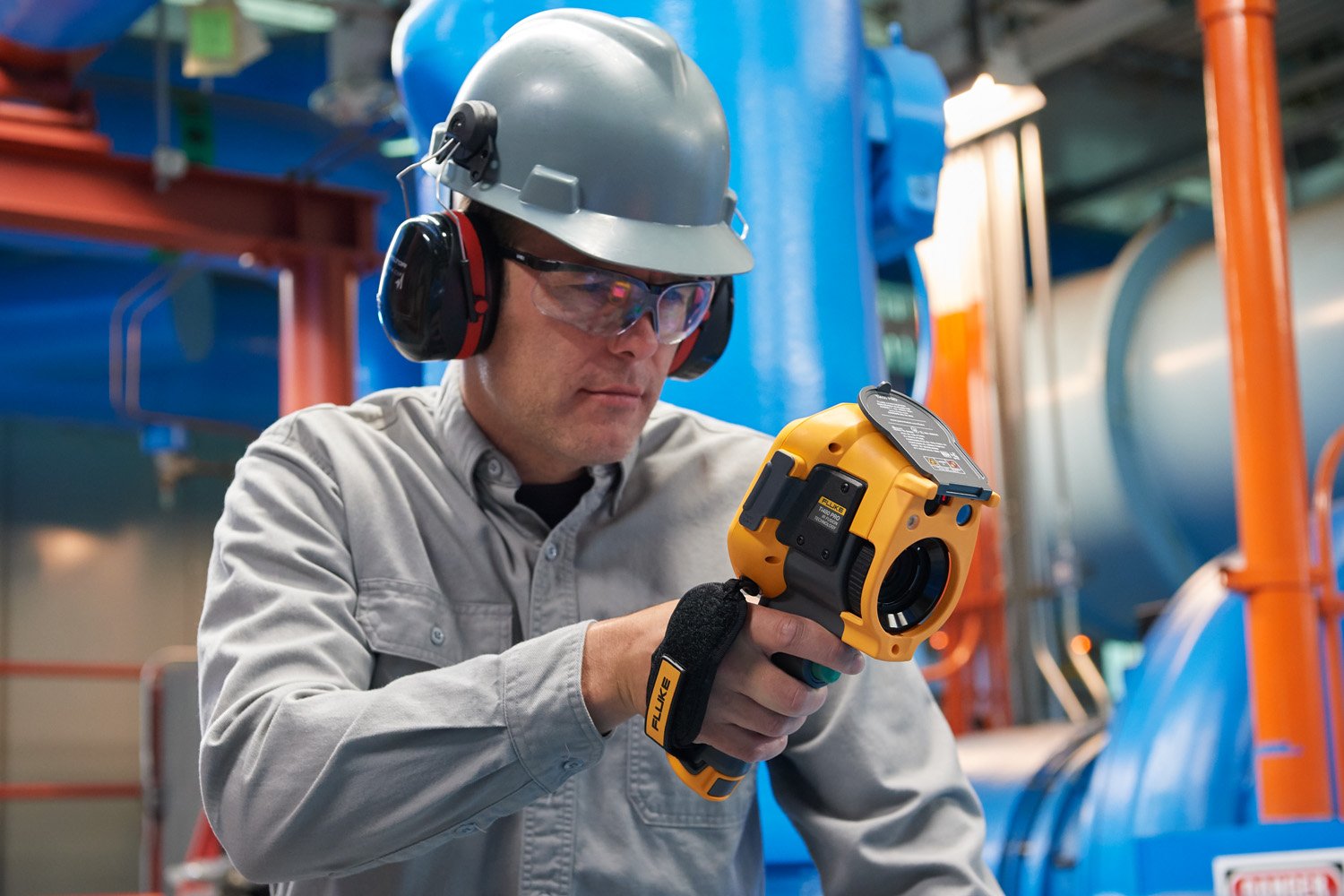
Effectuer une inspection avec une caméra thermique Fluke Ti401 PRO
Il est également possible d’utiliser une caméra thermique pour détecter les fuites de vapeur. Assurez-vous que l’isolation n’est pas décollée ou manquante et que tous les purgeurs de vapeur fonctionnent correctement, nettoyez l’intérieur des chaudières et vérifiez que les lignes de transmission de vapeur ne sont pas obstruées. Tous ces efforts permettront d’identifier les pertes énergétiques et aideront votre équipe à mettre en place des solutions pour réaliser des économies d’énergie ; souvent, beaucoup de ces solutions peuvent être mises en œuvre par le biais de la maintenance plutôt que par des dépenses d’investissement.
Air comprimé
Un compresseur avec une puissance de 100 ch peut consommer presque 50 000 $ d’électricité par an, et presque 30 % de cette électricité sert à mettre sous pression de l’air qui n’est jamais utilisé¹ à cause des fuites de distribution et de pratiques de gaspillage. Cependant, de nombreuses installations n’ont jamais estimé l’efficacité de leur système d’air comprimé. En fait, lorsqu’une plus grande pression d’air est requise, de nombreuses installations achètent et utilisent un compresseur supplémentaire, sans jamais réaliser qu’ils peuvent obtenir plus de pression à partir de leur système existant.
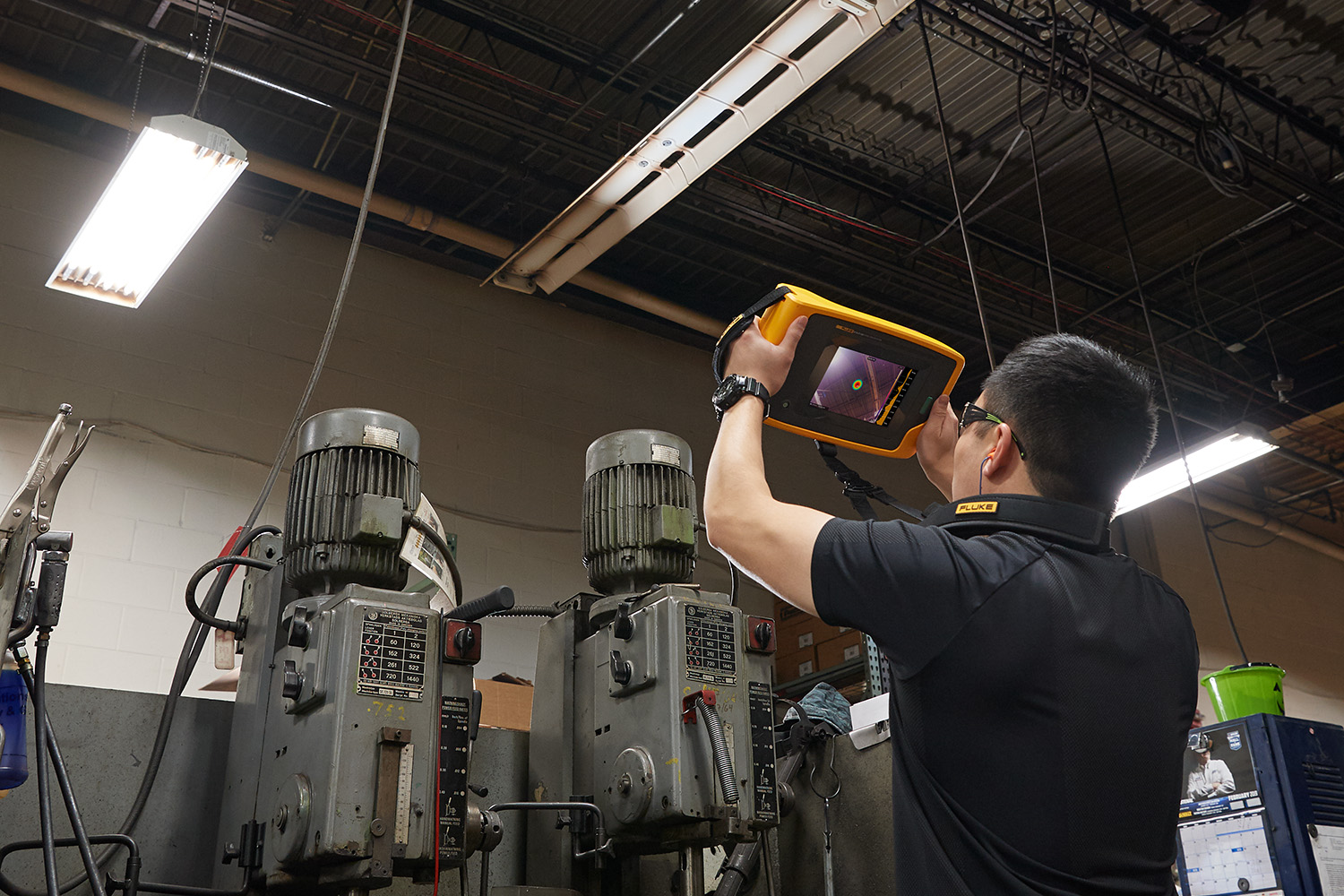
Inspecter les conduites d’air comprimé à l’aide de la caméra acoustique ultrasonore Fluke ii900
Selon les études du Compressed Air Challenge, seuls 17 % des utilisateurs considèrent l’efficacité comme un objectif de gestion d’un système d’air comprimé, alors que 71 % souhaitent simplement assurer une alimentation en air fiable et constante. Cette philosophie se transmet jusque dans l’utilisation : les installations d’équipement pneumatique manquent souvent de simples électrovannes, causant une exploitation continue du compresseur ; les personnes dans l’atelier considèrent souvent l’air comprimé comme une ressource gratuite et s’en servent pour nettoyer la zone de travail ou même pour la refroidir.
Pour identifier et quantifier les pertes, commencez par relever la consommation d’énergie au niveau de tous les compresseurs d’air pendant un cycle opérationnel complet. Cela permet d’établir la quantité d’énergie nécessaire pour produire les niveaux de pression d’air actuels. En outre, utilisez un calibrateur de pression de précision pour relever la pression (psi) au niveau de la sortie du compresseur, comparez-la à celle du point d’utilisation et déterminez le niveau de chute de pression. Vérifiez également la pression requise par le constructeur pour faire fonctionner les équipements pneumatiques, ne travaillez pas en surpression « juste parce que ». Connecter un module de pression à un multimètre enregistreur est un bon moyen de réaliser ces tests sans investir dans de l’équipement spécialisé. Enfin, utilisez une caméra acoustique ultrasonore pour vérifier l’empreinte d’autant de conduites d’air que possible afin de déterminer l’emplacement et l’étendue des fuites d’air. Calculez votre retour sur investissement grâce à ce calculateur de fuite d’air.
Conclusion
L’application raisonnée des recommandations simples et concrètes présentées ici permet d’améliorer considérablement l’efficacité énergétique de votre usine. Individuellement, mais encore plus ensemble, elles constituent un puissant levier pour économiser l’énergie.