Avec des équipes et des budgets de plus en plus petits, il n'est pas rare que les responsables demandent une justification avant d'autoriser les achats d'outils. Ici, l'élément clé est le retour sur investissement (RSI) ou combien de temps va-t-il falloir pour économiser suffisamment d'argent en utilisant l'outil pour amortir le coût d'achat.
Les scénarios les plus simples sont lorsque les outils vous permettent de réduire le nombre d'heures de travail ou de personnes requises pour réaliser une tâche. Par exemple, installer un hublot infrarouge dans un panneau et utiliser une caméra infrarouge permet à une personne d'inspecter les composants clés d'un panneau en 5 minutes, contre deux personnes travaillant pendant une demi-heure ou plus et devant s'équiper des EPI adéquats. Dans ce cas, calculez le coût en temps et en main-d'œuvre et multipliez-le par la fréquence d'inspection pour déterminer combien de cycles d'inspection seront nécessaires pour amortir les coûts du hublot et de la caméra.
Mais qu'en est-il pour cet outil qui résout le problème intermittent, très agaçant, qui vous a fait courir à travers toute l'installation au lieu de vous concentrer sur vos tâches régulières ? Comment calculer les coûts ? Ou un outil qui améliore la productivité générale ? Ou qui rallonge la durée de vie d'un équipement ? Ou qui permet de remplacer des composants plutôt que des unités ? Ou qui vous aide à prévenir les coupures non planifiées ? Ou qui vous permet de faire des réparations en interne plutôt que d'appeler un sous-traitant la nuit ou le weekend pour 250 $/heure ? Parfois, le plus dur est d'estimer le prix à investir pour que tout fonctionne correctement.
Si vous ne pouvez pas calculer le coût en temps et en main-d'œuvre, prenez en compte le coût de l'équipement. Un composant par rapport à l'unité complète, par exemple. Ou, si vous prolongez la vie d'un appareil, combien économisez-vous par année en n'achetant pas de nouvelle unité ? Et les responsables doivent connaître le coût approximatif des opportunités commerciales manquées et des frais par heure d'arrêt non planifiée.
Dans la plupart des cas, un peu de bon sens vous aidera à estimer au moins grossièrement les coûts. Les scénarios suivants vous indiquent comment procéder.
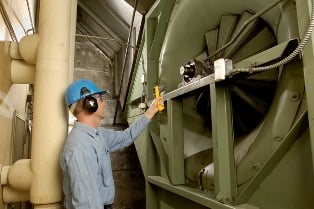
Exemple 1 : Une installation avec un important système de refroidissement central, en général, fait appel à une société de services pour vérifier l'isolation des ventilateurs des tours de refroidissement, des pompes à eau glacée et des pompes à eau du condenseur. Cette société de services coûte 125 $/heure. Cette année, l'équipe souhaiterait réaliser ce travail en interne, si possible, ils ont donc acheté un contrôleur de résistance d'isolement pour 450 $. Ce nouveau contrôleur de résistance d'isolement est amorti en moins de quatre heures, certainement en moins d'une saison de refroidissement. À partir de ce point, l'outil fait gagner de l'argent à chaque fois qu'il est utilisé ! Comme les moteurs des systèmes de refroidissement sont contrôlés au début de la saison de refroidissement, la probabilité d'un arrêt non planifié coûteux et d'appels de service d'urgence est réduite. En outre, le contrôleur est disponible et peut être utilisé avec d'autres équipements, comme les pompes à eau chaude et les moteurs de traitement d'air, ce qui améliore la productivité globale et réduit la période d'amortissement d'autant.
Retour sur investissement : un outil amorti en quatre heures.
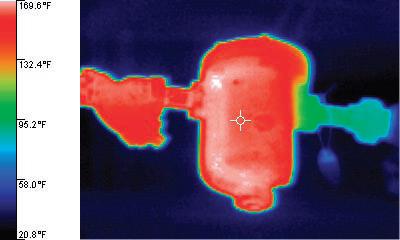
Exemple 2 : Une installation utilise une centrale de production de vapeur pour distribuer de la vapeur sous haute pression à travers l'installation. Les purgeurs de vapeurs sont utilisés pour collecter le condensat et le renvoyer vers la centrale pour qu'il soit utilisé comme eau d'alimentation. Les purgeurs de vapeur doivent être vérifiés régulièrement, car s'ils tombent en panne en position ouverte, la vapeur sous pression s'introduit dans le condensat, ce qui gâche de la vapeur et donc de l'énergie. À cause de réductions du personnel, les purgeurs de vapeur n'ont pas été vérifiés récemment et il y a probablement des défauts actuellement. Selon les calculs d'un fabricant de purgeurs de vapeur, une fuite de 2,5 cm sur un purgeur de vapeur avec une pression de 10 psig, pour un coût de production de 5 $ pour 450 kg de vapeur, entraînera un gaspillage d'une valeur de 4 725 $ par an. Et cela ne prend en compte qu'un seul purgeur. L'équipe s'est donc penchée sur le retour sur investissement pour l'achat d'une caméra infrarouge pour vérifier rapidement tous les purgeurs de vapeur sur place. Le modèle qu'ils envisageaient d'acheter coûte 4 500 $. En d'autres termes, si un seul purgeur défectueux est détecté et réparé, la caméra infrarouge est déjà plus qu'amortie. Tous les autres purgeurs détectés par la suite ajouteront 100 % d'économie générées directement sur le bénéfice net, saison après saison. En outre, ils peuvent utiliser la caméra infrarouge pour inspecter et dépanner de nombreuses autres zones de l'installation et peut-être stabiliser leur budget d'exploitation et de maintenance. La productivité par membre de l'équipe augmentera également.
Retour sur investissement : un outil payé dès la détection d'un seul purgeur de vapeur défectueux.
Exemple 3 : Une installation souffre continuellement de détérioration du compresseur de réfrigération, à 9 000 $ par compresseur. Ces détériorations ont conduit à la perte de lots de produits, qui doivent être stockés dans un environnement contrôlé, à 0,60 $ par unité et avec des lots de 1 500. En outre, les irrégularités d'approvisionnement font que des clients principaux importants annulent leurs commandes. Les détériorations du compresseur de réfrigération coûtent également des milliers de dollars en appels de service onéreux. Les causes de ces détériorations continuelles restent inconnues. L'équipe a décidé d'acheter un énergimètre, pour 7 500 $. Ils ont attaché l'énergimètre au point d'entrée d'un des compresseurs et ont découvert que la source d'alimentation présentait des fluctuations de tension et de phase majeures, qui étaient probablement la cause de compresseurs prématurément grillés. Ils ont continué leurs tests en amont et sont remontés jusqu'à la source du problème au niveau de l'alimentation d'entrée du fournisseur d'électricité. Le fournisseur a été contacté et le problème d'alimentation corrigé. Les compresseurs ne grillent plus. Même avec le coût d'achat, l'argent économisé en évitant un nouveau compresseur grillé amortira l'outil. Ils évitent le rachat de l'unité, les appels de service d'urgence, la perte de produit et la baisse de ventes. En outre, ils peuvent utiliser l'énergimètre pour d'autres applications, ce qui améliore la performance de l'équipement dans toute l'installation et permet à une équipe limitée de résoudre davantage de problèmes et de passer moins de temps à courir réparer ce défaut.
Retour sur investissement : un outil payé immédiatement, qui coûte moins cher que les gaspillages actuels pour chaque incident.
Une fois que vous avez établi tous les coûts, ces trois exemples semblent être des usages pertinents d'un budget limité. La question n'est peut-être pas de savoir si vous pouvez vous permettre d'acheter l'outil, mais plutôt : pouvez-vous ne pas l'avoir et subir des coûts élevés et des appels de services onéreux ?