Eficiencia y fiabilidad de motores eléctricos: El nuevo método de pruebas emula las condiciones del mundo real
Los motores eléctricos son el componente fundamental de muchos procesos industriales, pueden representar hasta el 70% de la energía total consumida en una planta industrial y consumen hasta un 46% de la electricidad generada en todo el mundo. Ante su importancia crítica para los procesos industriales, el coste del tiempo de inactividad provocado por los motores averiados puede ascender a decenas de miles de dólares por hora. Garantizar la eficiencia y el funcionamiento fiable de los motores es una de las tareas más importantes a las que se enfrentan a diario los técnicos e ingenieros de mantenimiento.
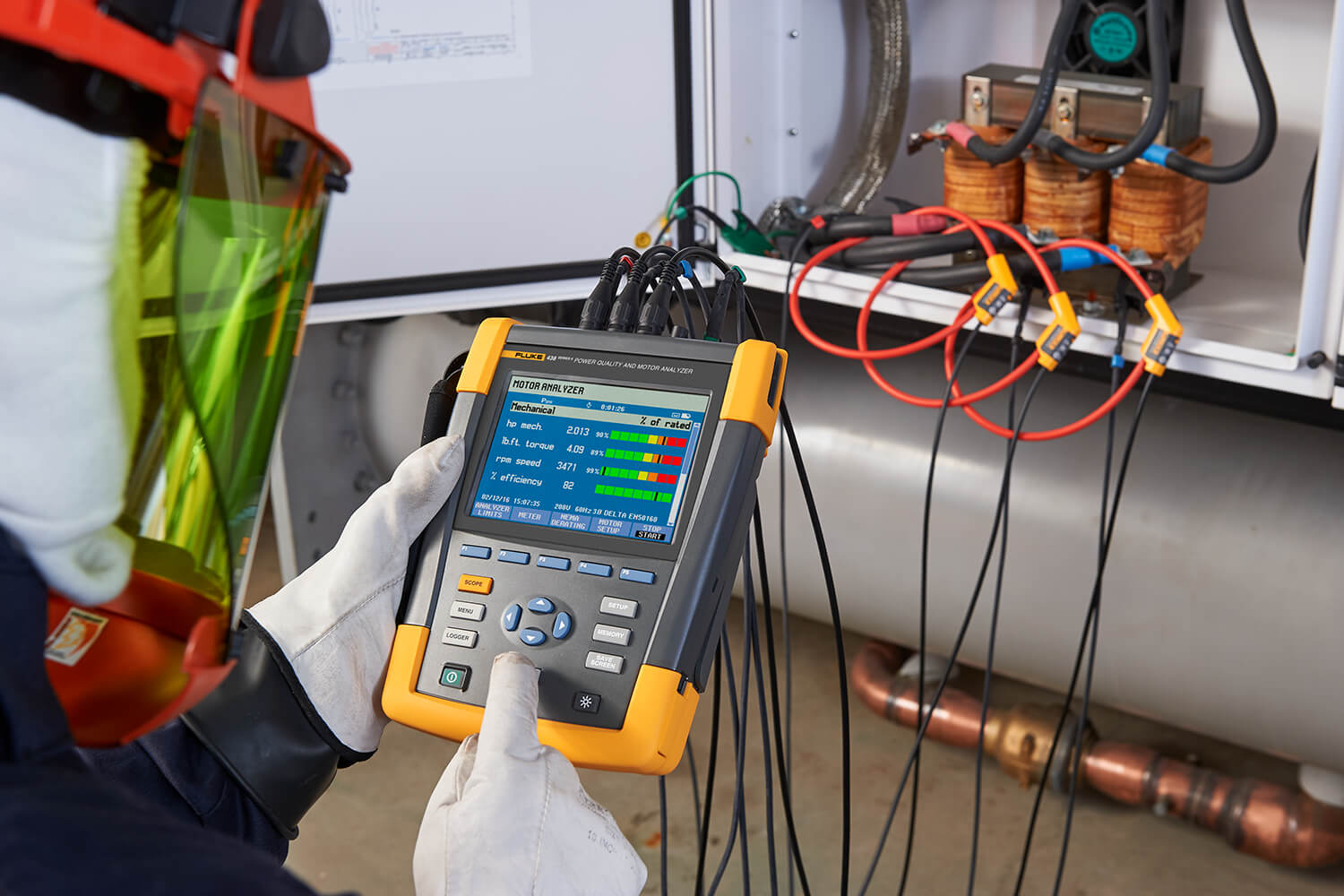
El uso eficiente de la electricidad es algo que no solo es deseable, sino que en muchas circunstancias la eficiencia energética puede significar la diferencia entre rentabilidad y pérdidas económicas. Y, puesto que los motores consumen una parte tan significativa de la energía en la industria, se han convertido en el objetivo principal a la hora de generar ahorro y mantener la rentabilidad. Además, el deseo de aprovechar el ahorro logrado mediante mejoras en la eficiencia y de reducir la dependencia de los recursos naturales está llevando a muchas empresas a adoptar normas industriales como ISO 50001, que proporciona el marco y los requisitos necesarios para establecer, implantar y mantener un sistema de gestión de la energía que ofrezca ahorros sostenibles.
Métodos tradicionales para comprobación de motores
El método tradicional para medir el rendimiento y la eficiencia de un motor eléctrico está bien definido, pero la implantación del proceso puede resultar costosa y difícil de aplicar en los procesos de trabajo. De hecho, en muchos casos las comprobaciones del rendimiento del motor exigen incluso apagar el sistema por completo, lo cual puede dar lugar a un costoso tiempo de inactividad. Para medir la eficiencia de un motor eléctrico se deben determinar la potencia eléctrica de entrada y la potencia mecánica de salida para una amplia variedad de condiciones de funcionamiento dinámicas. El método tradicional de medir el rendimiento de un motor requiere que los técnicos lo instalen en un banco de pruebas, formado por el motor que se desea comprobar montado en un generador o dinamómetro.
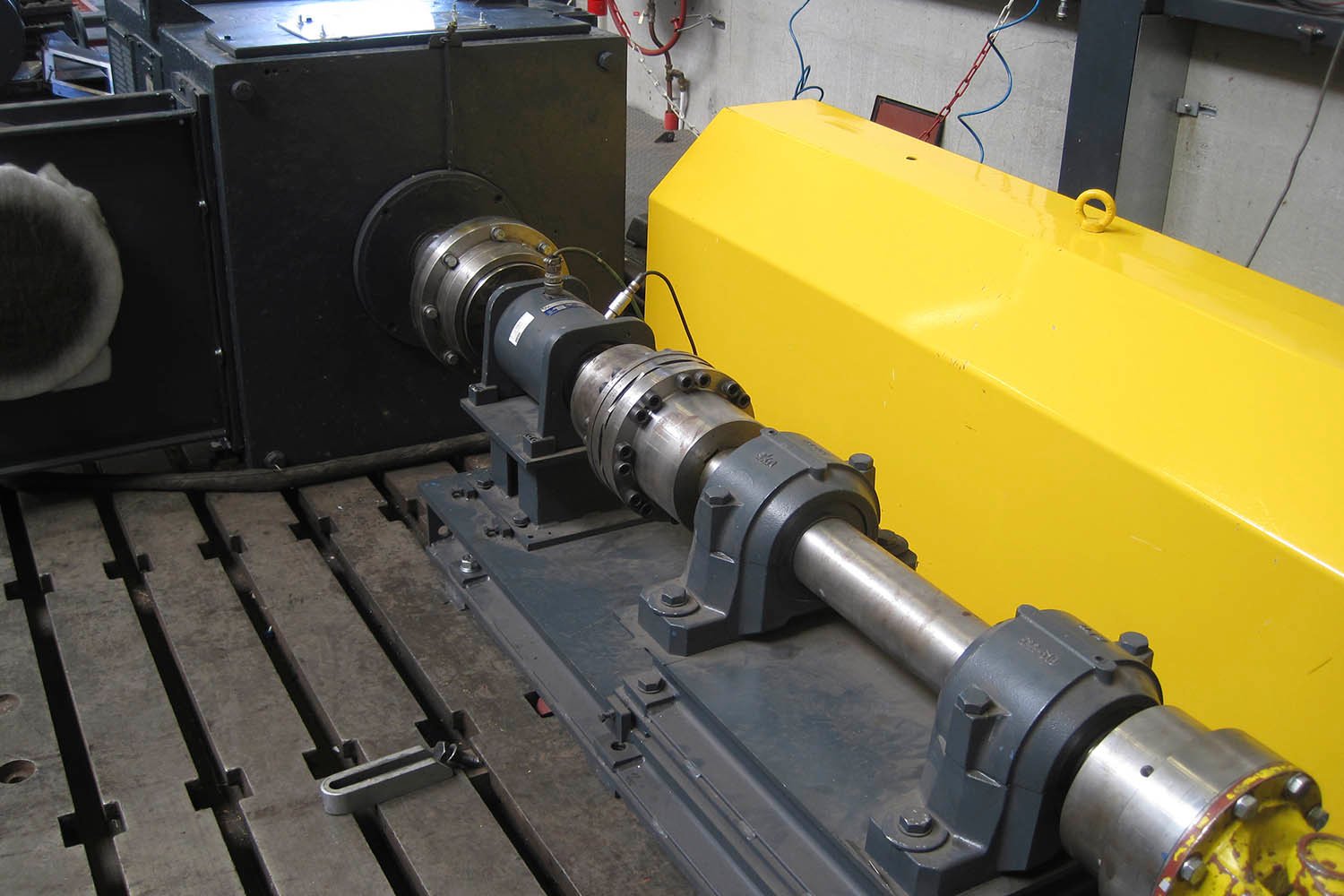
A continuación, el motor sometido a prueba se conecta a la carga mediante un eje, el cual está conectado a un sensor de velocidad (tacómetro) y una serie de sensores de par que proporcionan los datos necesarios para calcular la potencia mecánica. Este sistema proporciona datos como velocidad, par motor y potencia mecánica. Algunos sistemas también pueden medir la potencia eléctrica para facilitar el cálculo de la eficiencia.
Cálculo de la eficiencia:
ɳ(eficiencia) =
Potencia mecánica
Potencia eléctrica
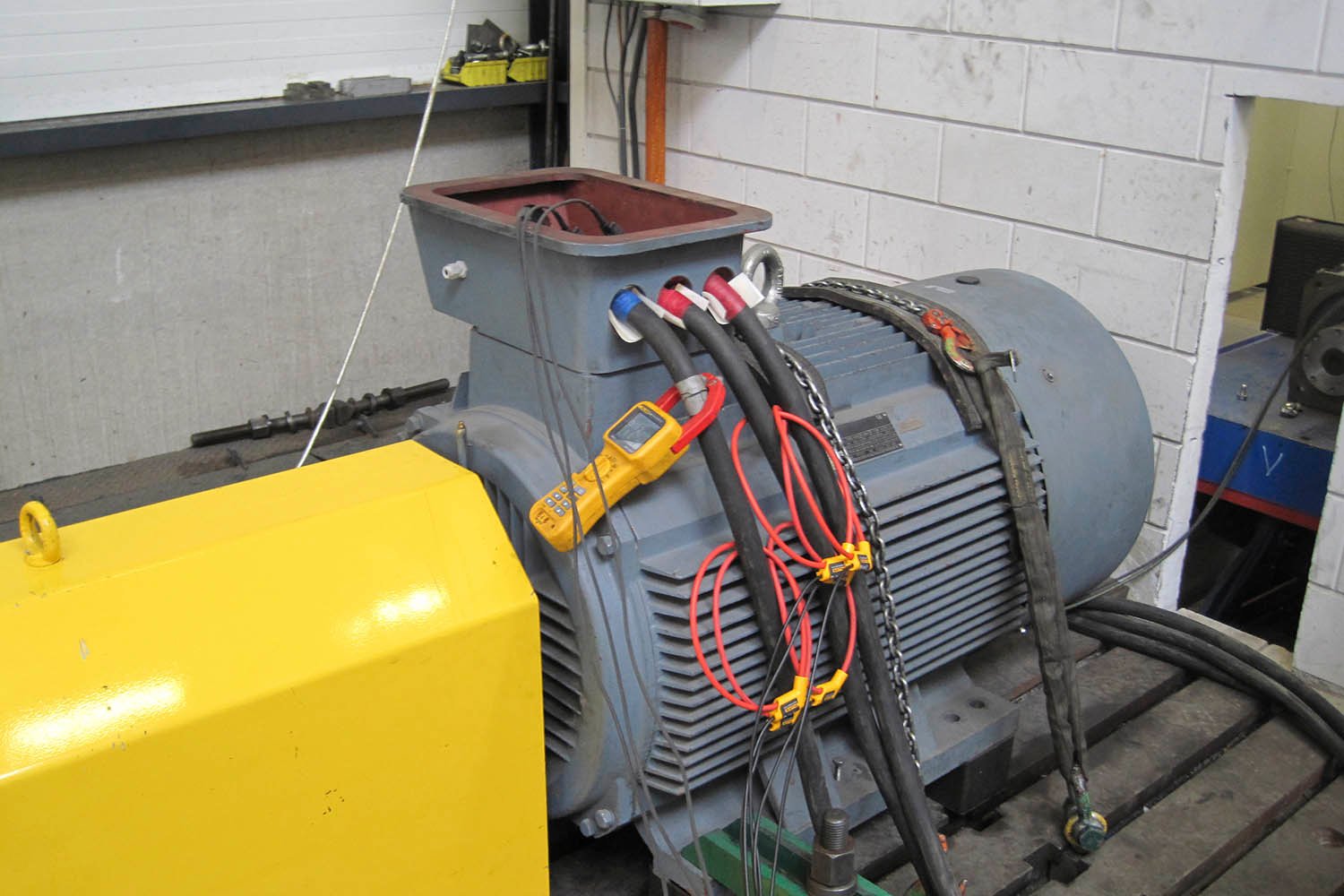
Durante las pruebas se varía la carga para determinar la eficiencia con varios modos de funcionamiento. El sistema de banco de pruebas puede parecer bastante sencillo, pero presenta una serie de desventajas inherentes:
- El motor deja de ser operativo.
- La carga del motor no es realmente representativa de la carga a la que se ve sometido el motor en funcionamiento.
- Durante la comprobación se ha de detener el motor (lo cual genera tiempo de inactividad) o se debe instalar temporalmente un motor de repuesto.
- Los sensores de par son costosos y tienen un rango de funcionamiento limitado, por lo que probablemente habrá que contar con varios sensores para probar distintos motores.
- Un banco de pruebas de motores que pueda cubrir una amplia gama de motores resulta caro, por lo que los usuarios de este tipo de bancos de pruebas suelen ser organizaciones especializadas en la reparación o el desarrollo de motores.
- No se tienen en cuenta las condiciones de funcionamiento del "mundo real".
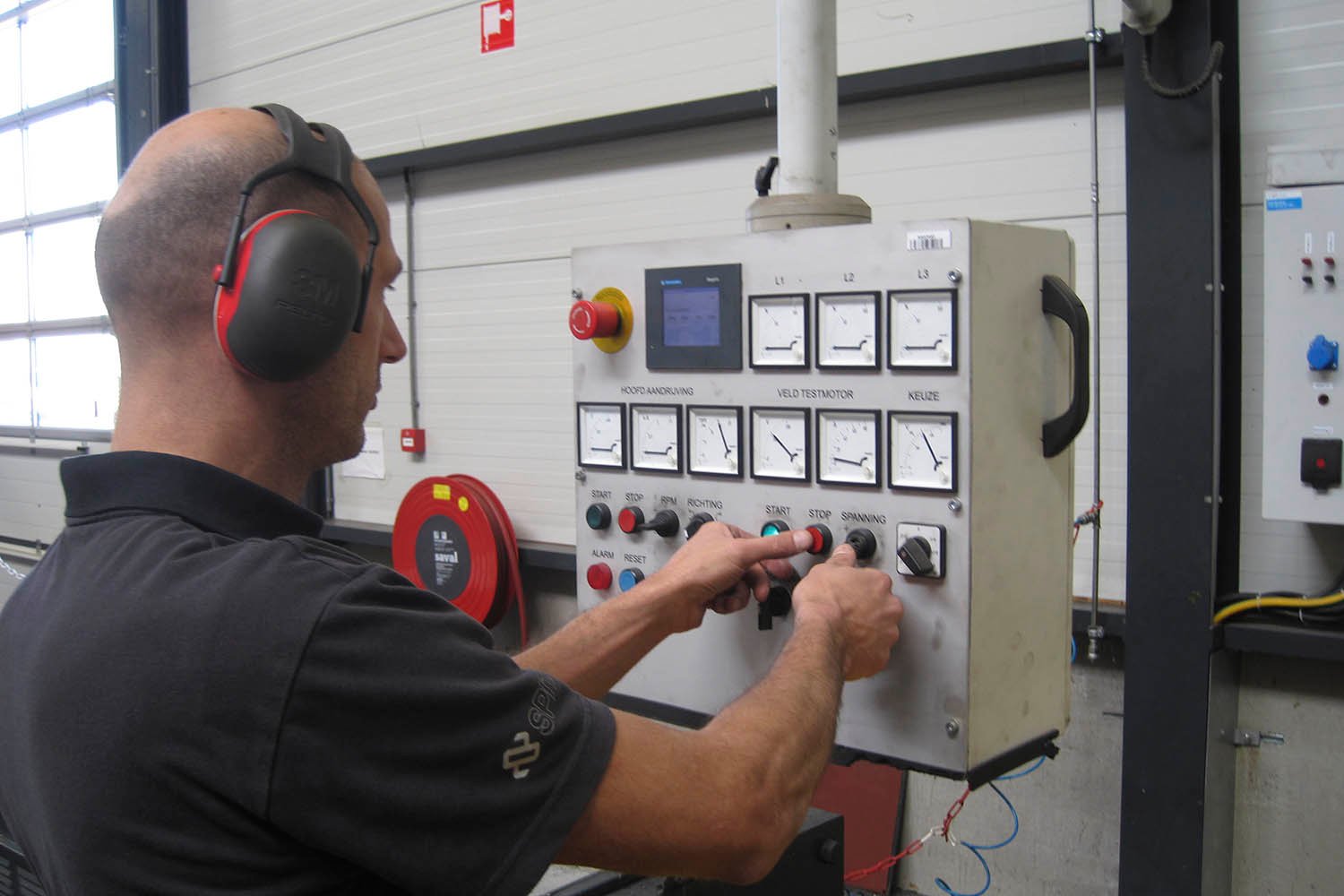
Parámetros de los motores eléctricos
Los motores eléctricos están diseñados para determinados tipos de aplicaciones en función de la carga, por lo que cada motor tiene diferentes características que se clasifican en función de las normas de la NEMA (National Electrical Manufacturers Association) o la IEC (International Electrotechnical Commission) y que tienen un efecto directo sobre el funcionamiento y la eficiencia del motor. Cada motor tiene una placa de características que detalla sus principales parámetros de funcionamiento y la información sobre eficiencia conforme a las recomendaciones NEMA o IEC. Los datos de la placa de características pueden utilizarse para comparar los requisitos del motor frente al modo de funcionamiento real. Por ejemplo, al comparar estos valores puede darse cuenta de que un motor está superando la velocidad o el par previsto en las especificaciones, en cuyo caso su vida útil puede verse acortada o puede sufrir una avería prematura. Otros efectos como desequilibrio de la tensión o de la corriente y los armónicos asociados con una mala calidad eléctrica pueden afectar al rendimiento del motor. Si se produce alguna de estas condiciones se debe "desclasificar" el motor, es decir, se debe reducir el rendimiento esperado del motor, lo cual podría afectar al proceso si no se produce suficiente energía mecánica. La desclasificación se calcula de acuerdo con la norma NEMA de conformidad dependiendo de los datos indicados para el tipo de motor. Las normas NEMA e IEC presentan ligeras diferencias, pero en general siguen las mismas líneas.
Condiciones de funcionamiento del mundo real
La comprobación de motores eléctricos en un banco de pruebas generalmente implica que las condiciones de la prueba serán las mejores posibles. Por el contrario, cuando el motor se utiliza en funcionamiento, normalmente no se dan esas condiciones ideales. Estas variaciones en las condiciones de funcionamiento contribuyen a la degradación del rendimiento de los motores. Por ejemplo, dentro de una planta industrial puede haber cargas instaladas que ejerzan un efecto directo sobre la calidad eléctrica y que provoquen desequilibrios en el sistema, e incluso armónicos. Cada una de estas condiciones puede afectar gravemente al rendimiento de los motores. Además, es posible que la carga accionada por el motor no sea óptima o compatible con el diseño original del motor. Es posible que el motor no pueda manejar la carga adecuadamente porque ésta sea demasiado grande o porque se vea sometido a una sobrecarga por controles deficientes del proceso, e incluso puede verse dificultado por un exceso de fricción provocado por un objeto extraño que bloquea una bomba o la hélice del ventilador. Descubrir estas anomalías puede resultar difícil y exigir mucho tiempo, lo cual hace que la resolución efectiva de los problemas sea complicada.
Un nuevo método
El analizador de calidad eléctrica y eficiencia de motores Fluke 438-II ofrece un método rentable y eficaz para comprobar la eficiencia de motores y elimina la necesidad de sensores mecánicos externos, así como el costoso tiempo de inactividad. El Fluke 438-II, basado en los analizadores de calidad eléctrica de la serie Fluke 430-II, está totalmente capacitado para medir la calidad eléctrica y los parámetros mecánicos de los motores eléctricos conectados directamente en línea. Con los datos de la placa de características técnicas del motor (NEMA o IEC), junto con las medidas de los datos de alimentación trifásica, el 438-II calcula datos de rendimiento del motor en tiempo real, como velocidad, par, potencia mecánica y eficiencia, sin necesidad de añadir sensores de par y velocidad. El 438-II también calcula directamente el factor de desclasificación del motor en el modo de funcionamiento.
El técnico o ingeniero introduce los datos que el Fluke 438-II necesita para realizar estas medidas, entre los que se incluyen potencia nominal en kW o HP, tensión y corriente nominal, frecuencia nominal, cos φ nominal o factor de potencia, factor de servicio nominal y tipo de diseño del motor conforme a las clases NEMA o IEC.
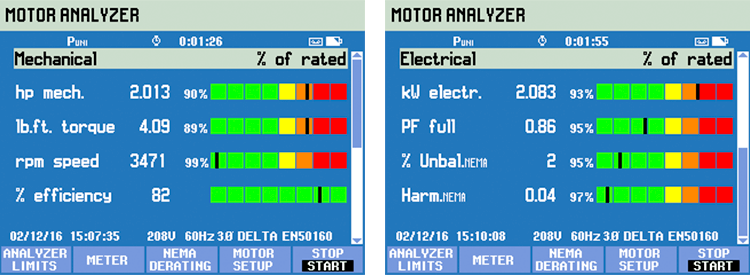
Cómo funciona
El Fluke 438-II proporciona medidas mecánicas (velocidad de giro, carga, par y eficiencia del motor) mediante la aplicación de algoritmos propios a señales eléctricas. Los algoritmos combinan modelos basados en la física y obtenidos a partir de datos de un motor de inducción sin necesidad de realizar medidas previamente, como suele ocurrir para calcular parámetros del modelo de motor, como la resistencia del estator. La velocidad del motor se puede calcular a partir de los armónicos de la ranura del rotor presentes en las formas de onda de la corriente. El par del eje del motor puede relacionarse con las tensiones, corrientes y deslizamiento del motor de inducción mediante relaciones físicas complejas pero bien conocidas. La potencia eléctrica se mide mediante las formas de onda de la corriente y la tensión de entrada. Tras obtener las estimaciones de par y velocidad se calcula la potencia mecánica (o carga) multiplicando el par por la velocidad. La eficiencia del motor se calcula dividiendo la potencia mecánica estimada entre la potencia eléctrica medida. Fluke ha realizado pruebas exhaustivas con motores instrumentados conectados a dinamómetros. Se midieron los valores reales de la potencia eléctrica, el par del eje del motor y la velocidad del motor y se compararon con los valores obtenidos con el 438-II para determinar los niveles de precisión.
Resumen
Aunque los métodos tradicionales para medir el rendimiento y la eficiencia de los motores eléctricos están bien definidos, no están necesariamente muy implantados. Esto se debe en gran parte al coste del tiempo de inactividad asociado a la desconexión de los motores, y en ocasiones de los sistemas por completo, para realizar las pruebas. El Fluke 438-II proporciona información muy útil que hasta ahora resultaba extremadamente difícil y costosa de adquirir. Además, el Fluke 438-II utiliza su capacidad avanzada de análisis de la calidad eléctrica mientras el sistema está en modo de funcionamiento real. La obtención de medidas de eficiencia del motor vitales se ha simplificado al eliminarse la necesidad de par externo y de sensores de velocidad independientes, lo que hace posible analizar el rendimiento de la mayoría de los procesos impulsados por motores industriales mientras están aún en servicio. Esto ofrece a los técnicos la posibilidad de reducir el tiempo de inactividad y la oportunidad de conocer la tendencia del rendimiento del motor a lo largo del tiempo, lo cual les proporciona una imagen más clara del estado y el rendimiento del sistema en su conjunto. Conocer la tendencia del rendimiento permite ver los cambios que pueden indicar averías inminentes en el motor y permitir sustituirlo antes de que se averíe.