Debido al precio fluctuante de las materias primas, la industria se enfrenta al desafío de ajustarse a los plazos y los márgenes de beneficio. De hecho, una de las pocas formas de controlar los costes en todo el sector consiste en alcanzar una mayor simplicidad y eficiencia.
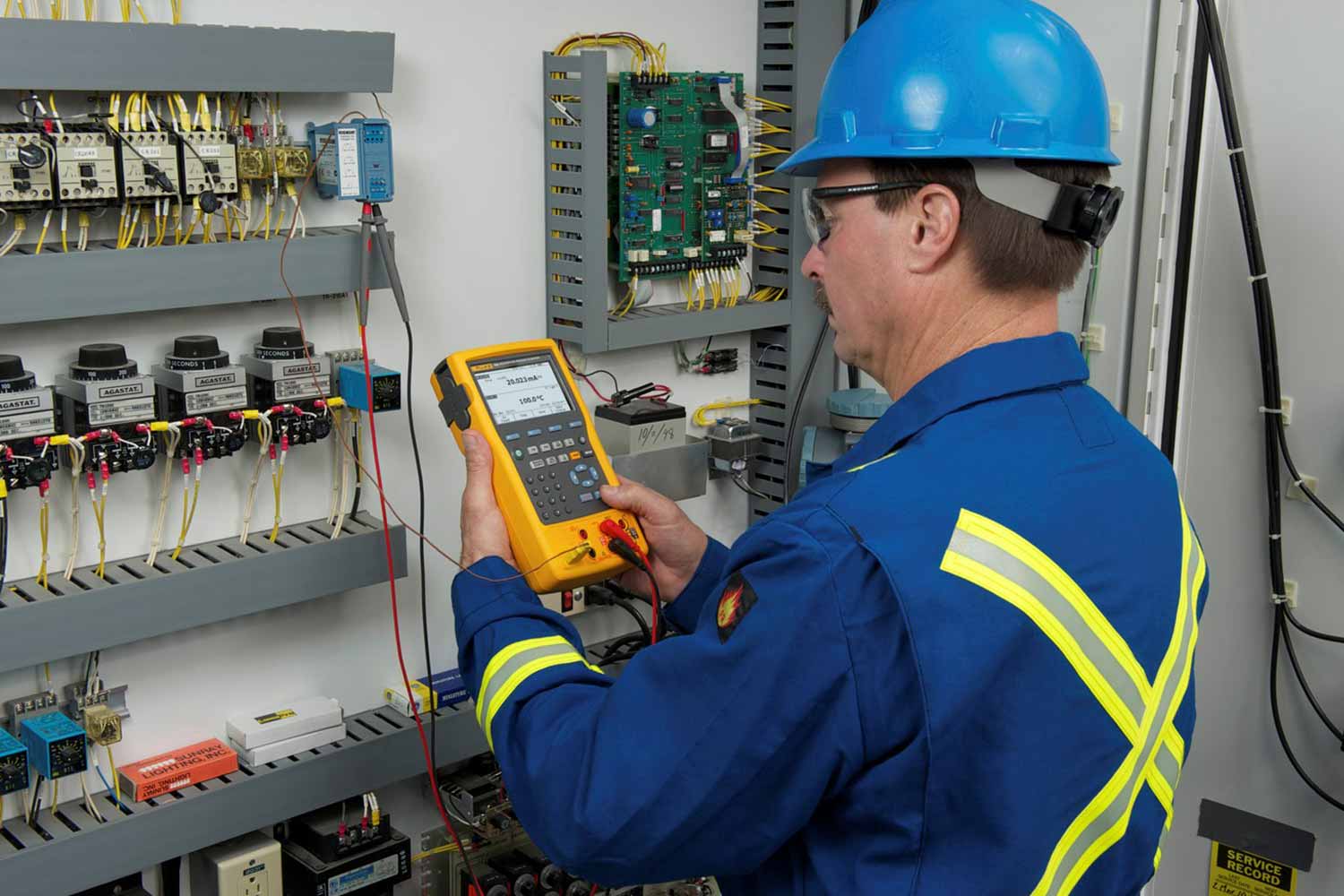
Y una de las mejores maneras de controlar esos costes consiste en averiguar qué se está desperdiciando en su proceso. Eso implica un trabajo exhaustivo de ajuste de precisión para asegurarse, desde una perspectiva de instrumentación, que se obtienen las temperaturas y presiones adecuadas para una producción de alta calidad y el uso eficaz de los datos de entrada.
Calibrar el equipo mejora la optimización y la calidad, y esto es igualmente cierto en otros sectores de procesos industriales, ya se trate de la industria química, la energía nuclear, la industria farmacéutica o papelera. Las plantas de fabricación requieren cientos o incluso miles de dispositivos sofisticados capaces de ejecutar innumerables operaciones críticas de forma ininterrumpida, precisa y fiable. Estos dispositivos también requieren inspección, comprobación, calibración y reparación de forma periódica.
Los siglos de experiencia industrial acumulada corroboran la importancia de registrar cuidadosamente los detalles de esas inspecciones, pruebas, calibraciones y reparaciones. Más que una práctica recomendada: las empresas y los gobiernos suelen exigir el mantenimiento de registros muy determinados para garantizar que se entrega a los clientes un producto que cumple los requisitos de calidad, y que se protege la salud y la seguridad de la población.
No obstante, las prácticas tradicionales de pruebas, calibración y documentación requieren una considerable mano de obra, y, debido a la escasez de operarios experimentados, los equipos mermados de personal a menudo optan por obviar la calibración periódica. Los hallazgos más recientes de la industria sugieren que es viable para equipos pequeños realizar y documentar las calibraciones de dispositivos, a un coste general menor y con ventajas añadidas de productividad y fiabilidad operacional.
La calibración se realiza comúnmente en el lugar en el que se encuentra el dispositivo (calibración in situ) o en un taller.
Consejo profesional:
Cuando se fabrica un instrumento de campo, tanto el elemento primario como el transmisor (o el actuador, si se trata de una válvula de control) se calibran en fábrica y la información de calibración se suministra con la unidad. Estos datos de calibración se pierden a menudo. La introducción de esta información en registros de calibración centralizados cuando el dispositivo se pone en servicio debe formar parte del procedimiento habitual y no solo por razones de eficacia.
La centralización de la información de calibración garantiza que los conocimientos se mantengan en las instalaciones aunque el personal de los equipos cambie.
Los instrumentos de campo suelen estar formados por dos partes: un elemento primario y un transmisor.
- Entre los elementos primarios se encuentran tubos de flujo, placas de orificio, sensores de presión, sensores químicos húmedos como sondas de pH, ORP y conductividad, galgas de nivel de todos los tipos, sondas de temperatura y muchos otros. Los elementos primarios suelen generar una señal, normalmente tensión, corriente o resistencia, proporcional a la variable para cuya medida han sido diseñados, como nivel, flujo, temperatura, presión o parámetro químico. Los elementos primarios están conectados a la entrada de transmisores de campo.
- Entre los transmisores de campo se encuentran dispositivos de presión, temperatura y flujo. Procesan la señal generada por el elemento primario, primero caracterizándola en formato lineal y aplicándole coeficientes de unidades de ingeniería, para, seguidamente, transmitirla en formato analógico (normalmente 4-20 mA CC) o digital (normalmente una variedad de bus de campo).
Dispositivos analógicos
Los dispositivos analógicos, a menudo denominados dispositivos de "lazo de 4 a 20 mA", se denominan así porque transmiten una señal que es una representación eléctrica "analógica" de una cantidad física medida (temperatura, por ejemplo). Transmiten una corriente eléctrica que es proporcional (análoga) a la magnitud de una cantidad física medida; 4 mA representan el valor mínimo de escala y 20 mA representan el valor máximo de escala.
Aunque ahora muchos aspectos de los sistemas son digitales, los dispositivos analógicos siguen en uso activo en el mundo de la fabricación de procesos.

Dispositivos digitales
Los dispositivos digitales convierten un valor físico medido en una señal digital. En el sector de los procesos industriales se utilizan muchos métodos de codificación digital diferentes, incluidos Foundation Fieldbus, Profibus y HART.
Existe la creencia generalizada de que los dispositivos de bus de campo (digitales) no requieren calibración, lo cual no es cierto. Aunque una señal de bus de campo (ya sea Foundation Fieldbus, Profibus o HART conectado) proporciona información de diagnóstico, no suministra información sobre la precisión del dispositivo ni comprueba si el dispositivo está informando del proceso de forma precisa.
Los tres instrumentos de calibración más importantes para optimizar sus procesos
- El calibrador documentador multifunción Fluke 754 cuenta con funciones HART y procedimientos de calibración automatizados y, por supuesto, cumple las normas de seguridad más estrictas.
- Calibrador de presión de precisión Fluke 721 de alta precisión con dos sensores aislados para aplicaciones de transferencia de custodia de gas.
- Calibrador de manómetros de precisión Fluke 700G robusto y de alta calidad para obtener resultados de prueba rápidos y precisos.
Válvulas de control
Las válvulas de control tienen actuadores que también requieren calibración para ajustarlos debido al desgaste, el reacondicionamiento de la válvula para solucionar fugas y los efectos de la adherencia o la fricción estática. A menudo, para garantizar un funcionamiento fiable, es preciso someter a estas válvulas a una prueba de carrera completa o parcial si no se han accionado con regularidad.
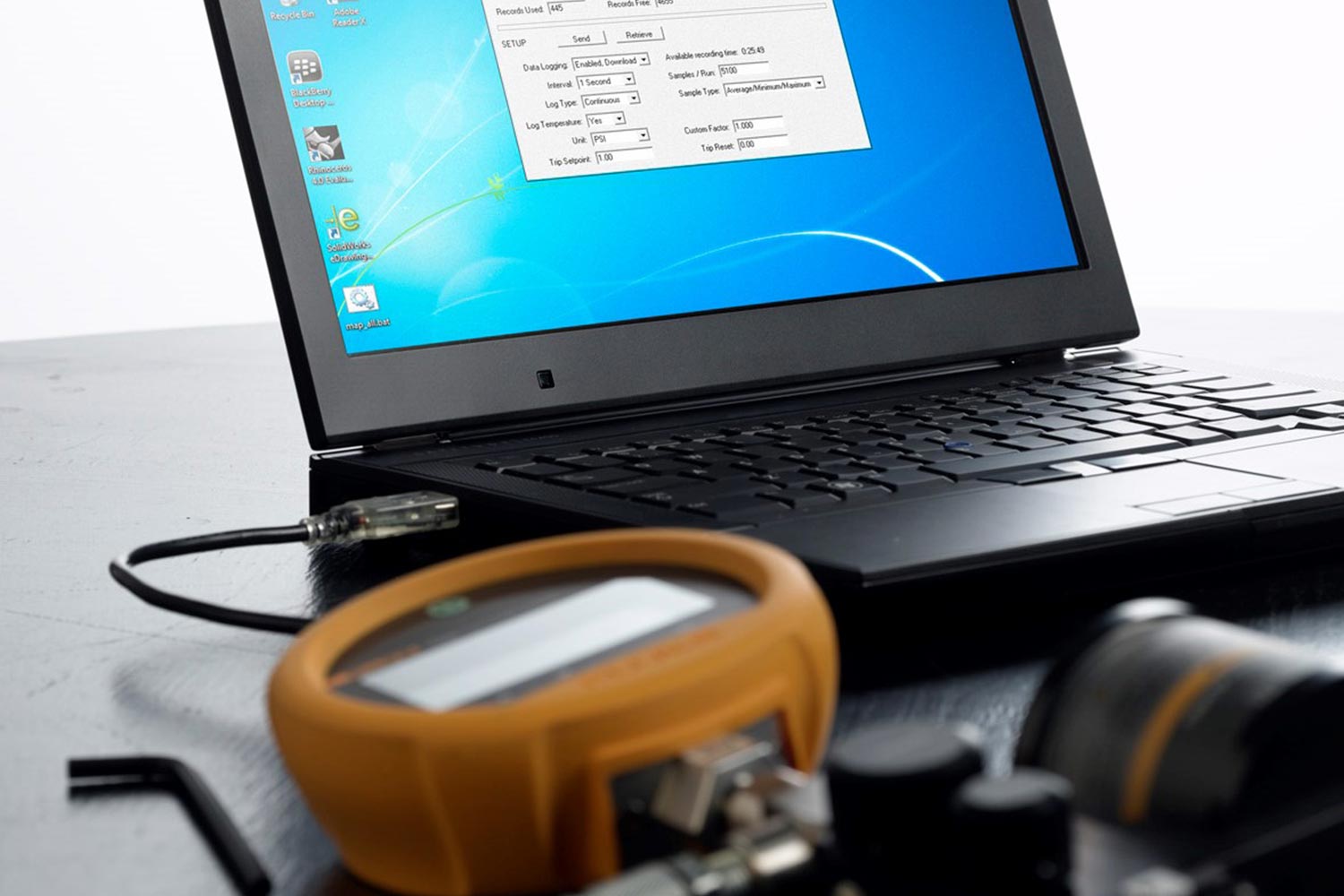
Permisos y trámites
Las tareas administrativas, desde obtener permisos hasta documentar y archivar resultados, pueden aumentar el coste y el tiempo necesarios para realizar incluso una calibración in situ. Como ha afirmado Ian Verpasme, de Industrial Automation Networks, y expresidente del Grupo de usuarios de Fieldbus Foundation, "En muchos casos, preparar todos los documentos necesarios (permisos, aislamiento, etc.) a menudo lleva más tiempo que el propio trabajo".
Retos que plantea documentar la calibración
Documentar una calibración ha consistido tradicionalmente en anotar a mano en un libro de registro la fecha y la hora de la calibración, así como las lecturas previas y posteriores a la calibración y cualquier otra observación de los técnicos. Sorprendentemente, muchas plantas continúan documentando a mano los trabajos de calibración. Pero la documentación en papel y lápiz tiene muchos inconvenientes.
En primer lugar, contribuye a generar y perpetuar errores. Los datos en los registros escritos a mano son a menudo insuficientes, cuando no ilegibles. Las instalaciones que utilizan un sistema de gestión de mantenimiento informatizado (CMMS) deben tener en cuenta el tiempo adicional necesario para introducir manualmente datos escritos a mano, con posibilidades adicionales de error.
Rotación de personal
Otro reto al que se enfrenta la calibración es el de cambios en la plantilla.
Los años ochenta trajeron consigo recortes presupuestarios y despidos. El personal de ingeniería, mantenimiento y operaciones se redujo sustancialmente, dando lugar a una nueva filosofía de "fabricación simplificada" que se mantiene en la actualidad, especialmente en las economías desarrolladas.
Los equipos más pequeños disponen de menos tiempo para tutorías y formación en el trabajo, hasta el punto de que el conocimiento específico de sistemas y equipos no se transfiere correctamente de la persona a la empresa. Cuando se jubilan los operarios e ingenieros de más edad, se llevan con ellos sus conocimientos sobre equipos y sistemas.
El ingeniero jefe de instrumentación y controles de una gran refinería del Medio Oeste de los Estados Unidos lo explica con claridad: "Todos los días a las 4 de la tarde, el caudal de experiencia acumulada de la planta abandona las instalaciones. Y, a veces, para no regresar".
Mientras tanto, muchas instalaciones todavía necesitan dos técnicos para cada calibración in situ, uno en el transmisor y otro en el sistema de control. La Fundación Fieldbus estima que la puesta en marcha requiere dos técnicos durante un mínimo de dos horas.
Utilice calibradores documentadores multifunción
Una nueva generación de instrumentos de calibración de campo más "inteligentes" está aumentando la productividad de los trabajadores mediante la consolidación de varios instrumentos en uno y la realización de funciones más allá de las pruebas y medidas básicas, como la asistencia en el análisis y la documentación.
Los "calibradores documentadores de procesos" multifunción son instrumentos de prueba portátiles y electrónicos que consolidan varios pasos y funciones de calibración en un único dispositivo, con capacidad de simulación y medida de valores de presión, temperatura y una amplia variedad de señales eléctricas y electrónicas.
Ventajas:
- Los técnicos necesitan menos instrumentos en el campo y, por tanto, menos tiempo de formación
- Procesos de calibración y salida de datos similares en varios dispositivos, en comparación con un proceso diferente para recopilar un conjunto diferente de datos procedente de cada instrumento y cada dispositivo
- Los procedimientos automatizados sustituyen muchos pasos de calibración manual
- No es necesario que un segundo técnico registre los estados anterior y posterior al mantenimiento del dispositivo de campo.
- Menor tiempo de calibración por dispositivo
- Calcule el error de un solo instrumento en lugar de acumular los errores de varios
Utilice rutas de calibración
El mayor ahorro derivado del uso de un calibrador documentador se debe a la herramienta de gestión de rutas integrada en el dispositivo. El uso de un único conjunto de permisos y documentación para un conjunto completo de calibraciones reduce considerablemente los costes.
Implemente un sistema de gestión de activos, gestión de calibración o gestión de mantenimiento informatizado (CMMS).
A diferencia de la documentación en papel, los datos del calibrador nunca son ilegibles, ambiguos o parciales. Los datos del calibrador documentador se pueden descargar directamente en varios CMMS sin necesidad de transcribir ni archivar.
Dado que la documentación de los calibradores de procesos registra automáticamente el estado "al llegar" y "al marchar" de cada dispositivo de campo in situ, y un solo técnico puede manejarlos, las prácticas de mantenimiento basado en rutas que utilizan calibradores documentadores pueden ahorrar hasta un 50% del tiempo y el coste de los métodos de calibración manuales tradicionales de un solo dispositivo. Dicho de otro modo, el mismo equipo ágil puede realizar el doble de calibraciones en el mismo periodo de tiempo.
Dirigir un equipo ágil siguiendo los requisitos operativos tradicionales es una fuente segura de errores. Las calibraciones no se llevarán a cabo como deberían. En lugar de ignorar el problema en ciernes, investigue cómo se puede aumentar la eficacia de las prácticas existentes.
Implemente calibración basada en rutas, documentación sin papel y gestión de datos CMMS. Se realizarán más calibraciones de forma más coherente, el conocimiento se transferirá de la persona al equipo y a la empresa, y aumentarán tanto la productividad como la calidad.
La calibración de varios instrumentos en una misma ruta reduce el coste por calibración, en comparación con la calibración de cada instrumento por separado.
Además de ahorrar costes de mantenimiento, evitará potenciales gastos millonarios en costas legales y pérdida de ingresos por accidentes. Las buenas prácticas de mantenimiento de calibración ayudan a reducir la probabilidad de que se produzca un incidente de este tipo. Y en caso de que se produjera, unos registros de calibración impecables pueden contribuir decisivamente a defender una empresa si se emprenden acciones legales, del mismo modo que unos registros deficientes pueden poner a una organización en una posición legal menos defendible.