Cámaras de infrarrojos, a la vanguardia del mantenimiento preventivo
El calor suele ser un síntoma temprano de daños o funcionamiento incorrecto en el equipo, lo cual hace que resulte importante supervisar programas de mantenimiento preventivo. La puesta en práctica de labores de mantenimiento preventivo por infrarrojos periódicamente para comprobar la temperatura de equipos críticos le permite llevar el seguimiento de las condiciones de funcionamiento con el paso del tiempo e identificar rápidamente lecturas inusuales para inspeccionarlas con mayor profundidad.
Al supervisar el rendimiento de los equipos y programar las tareas de mantenimiento cuando sean necesarias, en estas instalaciones se reduce la probabilidad de un tiempo de inactividad inesperado debido a fallos en los equipos, disminuye el gasto en mantenimiento "reactivo" y los costes en reparaciones de equipos, se amplía la vida útil de la maquinaria.
Consejo: para ahorrar dinero, el mantenimiento preventivo no debe añadir excesivos esfuerzos de mantenimiento. El objetivo es conseguir que los recursos de mantenimiento pasen de ser reparaciones de emergencia a inspecciones programadas de equipos clave. Las inspecciones llevan menos tiempo que las reparaciones, especialmente si se llevan a cabo con una cámara termográfica.
En este artículo se tratan los ahorros de costes derivados del mantenimiento preventivo con técnicas de termografía y PM, se proporcionan las directrices para capturar y analizar con éxito los datos termográficos y se describe cómo integrar la termografía en un programa de mantenimiento preventivo.
Rentabilidad de la inversión y ahorro de costes
Los estudios efectuados por el programa FEMP (Federal Energy Management Program) calculan que un programa de mantenimiento preventivo que funcione correctamente puede generar un ahorro del 30% al 40%. Otros estudios independientes indican que, de media, el desarrollo de un programa de mantenimiento preventivo industrial permite obtener los siguientes ahorros:
- Rentabilidad de la inversión: 10 veces
- Reducción de los costes de mantenimiento: 25 % a 30 %
- Eliminación de averías: 70 % a 75 %
- Reducción del tiempo de inactividad: 35 % a 45 %
- Aumento de la producción: 20 % a 25 %
Puede compartir esta información con su supervisor o sus clientes. Para calcular los ahorros obtenidos en las instalaciones, calcule los costes derivados de los fallos no previstos en los equipos. A continuación, incluya los recursos humanos, los costes de las piezas y la pérdida de ingresos en cada línea de producción.
Sería recomendable que el responsable de mantenimiento llevase un registro de la disponibilidad de la maquinaria, del rendimiento de la producción, de la distribución del presupuesto dedicado al mantenimiento y del coste de mantenimiento total a lo largo del tiempo. Estas cifras le ayudarán a calcular el retorno de la inversión en mantenimiento y en termografía.
Integración de la termografía en el mantenimiento predictivo
A menudo las cámaras de infrarrojos son la primera herramienta de inspección que los técnicos se plantean utilizar como parte de su programa de mantenimiento preventivo. Pueden medir y comparar rápidamente curvas de calor de todos los equipos de la ruta de inspección sin necesidad de interrumpir el funcionamiento.
Si la temperatura es muy diferente a la obtenida en las anteriores lecturas, las instalaciones podrán utilizar otras tecnologías de mantenimiento (vibraciones, análisis del circuito del motor, ultrasonidos transmitidos por el aire y análisis de lubricantes) para investigar el origen del problema y determinar cómo proceder.
Para obtener los mejores resultados, integre todas sus tecnologías de mantenimiento en el mismo sistema informático, de modo que pueda compartir las listas, los historiales, los informes y las órdenes de trabajo de los mismos equipos. Una vez correlacionados los datos infrarrojos con los datos procedentes de otras tecnologías, se podrá informar del estado de funcionamiento real de todos los componentes en un formato integrado.
Aplicaciones
- Supervisión y medida de temperaturas de rodamientos en motores grandes u otros equipos giratorios.
- Identificación de "puntos calientes" en equipos electrónicos.
- Identificación de fugas en recipientes herméticos.
- Búsqueda de aislamientos defectuosos en tuberías u otros procesos aislados.
- Búsqueda de conexiones defectuosas en circuitos eléctricos de alta potencia.
- Localización de disyuntores con sobrecarga en un cuadro eléctrico.
- Identificación de fusibles en el límite de su capacidad nominal de corriente, o próximos al mismo.
- Identificación de problemas en el cuadro de distribución eléctrica.
- Captura de lecturas de temperatura de procesos.
Proceso de inspección
- Utilice listas existentes de equipos de un sistema de gestión de mantenimiento asistido por ordenador (Computerized Maintenance Management System, CMMS) u otra herramienta de inventario.
- Elimine los elementos que no se miden a través de técnicas por infrarrojos.
- Revise los registros de producción y mantenimiento. Dé prioridad a los equipos clave propensos a sufrir fallos o que con frecuencia provoquen atascos en la producción.
- Emplee una base de datos u hoja de cálculo para agrupar los equipos fundamentales, bien por área o función, en bloques de inspección de apenas 2-3 horas.
- Utilice la cámara de infrarrojos para capturar las imágenes de referencia de cada pieza de los equipos más importantes. Nota: En algunos equipos es recomendable capturar varias imágenes térmicas de manera periódica de componentes clave o de subsistemas.
- Descargue las imágenes de referencia en el software y documente su ruta con descripciones de la ubicación, notas de inspección, niveles de emisividad y RTC y niveles de alarma, si corresponde.
- Cuando llegue el momento de realizar la siguiente inspección, si la cámara dispone de la función de carga, simplemente cargue las imágenes de inspección anteriores en la cámara y siga las indicaciones en pantalla.
Directrices de medida
Para capturar las mejores imágenes térmicas, siga estas recomendaciones:
- Compruebe que el sistema está funcionando al menos al 40% de la carga (una carga inferior no genera mucho calor, lo cual dificulta la detección de problemas).
- Acérquese al objetivo y no dispare a través de puertas, sobre todo a través del cristal. Cuando los procedimientos de seguridad lo permitan, se deben abrir los armarios eléctricos, o se deben emplear ventanas de infrarrojas o de visualización.
- Tenga en cuenta las corrientes de aire y el viento. Estas potentes fuerzas de convección enfrían los puntos más calientes de lo normal, a menudo por debajo del umbral de detección.
- Tenga en cuenta la temperatura ambiente del aire, sobre todo en exteriores. En un entorno caliente, es posible que el sol recaliente el equipo, mientras que en un entorno frío, es posible que este enmascare los efectos de los componentes sobrecalentados.
- No todos los problemas generan calor. Los fusibles fundidos y una restricción en el caudal de un sistema de refrigeración son dos ejemplos de situaciones en las que puede detectarse un problema a partir de una temperatura más baja de la habitual. En otros casos, un componente más frío de lo normal es indicador de una anormalidad como consecuencia de que la corriente se desvía de la conexión de alta resistencia. Los termógrafos deben entender cómo funciona el equipo en cuestión y cuáles son las indicaciones de averías relacionadas con el calor.
- Tenga en cuenta las fuentes que reflejan infrarrojos. Los elementos que tengan superficies reflectantes brillantes y que sean emisivos reflejarán la energía de infrarrojos desde otros objetos cercanos, incluido el sol. Esto puede interferir en la medida de la temperatura en el objetivo, así como la captura de imágenes.
- Los metales sin pintar son difíciles de medir. Para mejorar la precisión y la repetición de las medidas, considere la posibilidad de fijar "sujetos", normalmente en forma de adhesivos de papel, cinta aislante o puntos pintados en dichos componentes.
- Acumule temperaturas numéricas e imágenes térmicas para facilitar el análisis de datos a largo plazo. Las tendencias de las temperaturas le indicarán dónde debe investigar más y dónde puede realizar inspecciones con menor frecuencia.
- En cuanto disponga de una base de datos de imágenes de referencia, asocie una temperatura de alarma a cada una. Cargue la versión más reciente en su cámara antes de cada inspección. Si la alarma se desactiva al realizar la nueva medición, esto indica que se ha producido un cambio significativo en la temperatura que es necesario investigar.
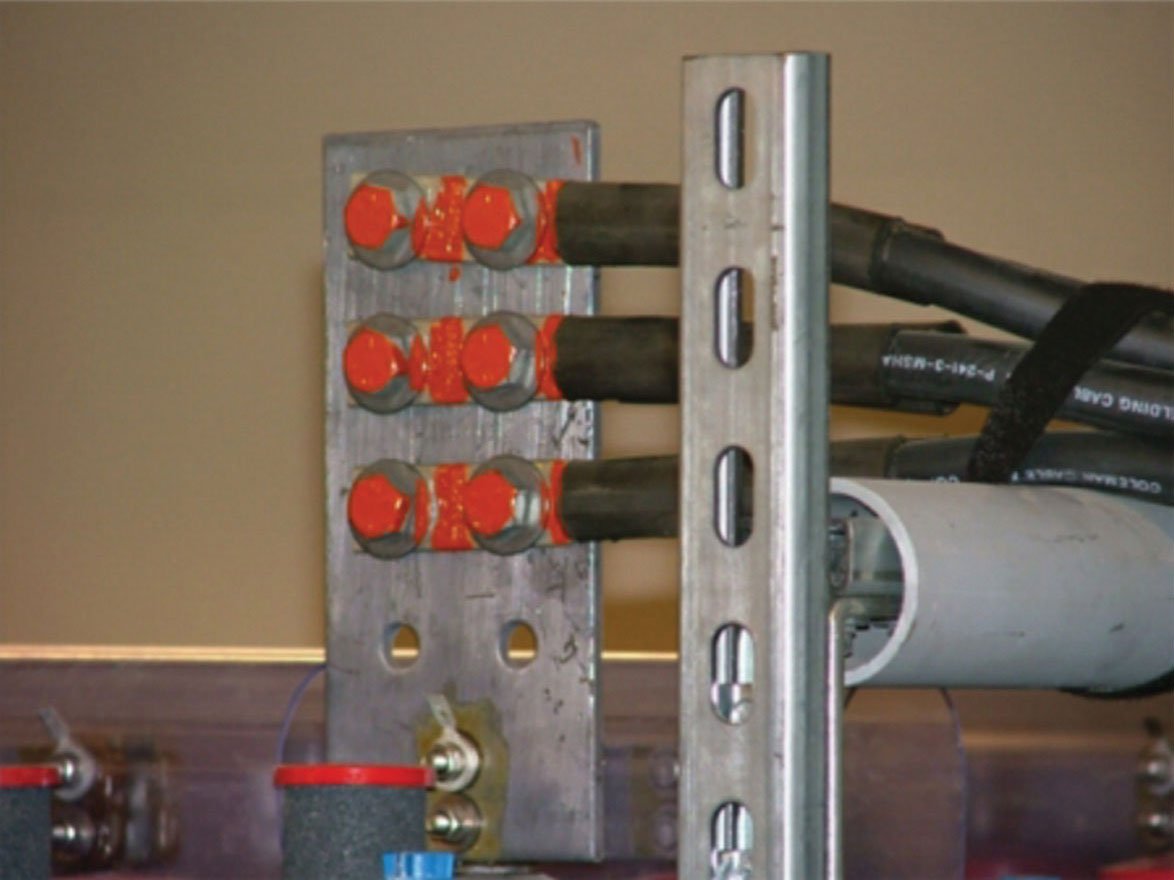
En las condiciones adecuadas, incluyendo el acceso directo y las cargas normales, problemas como el que plantea este conector de alta resistencia suelen ser fáciles de localizar.
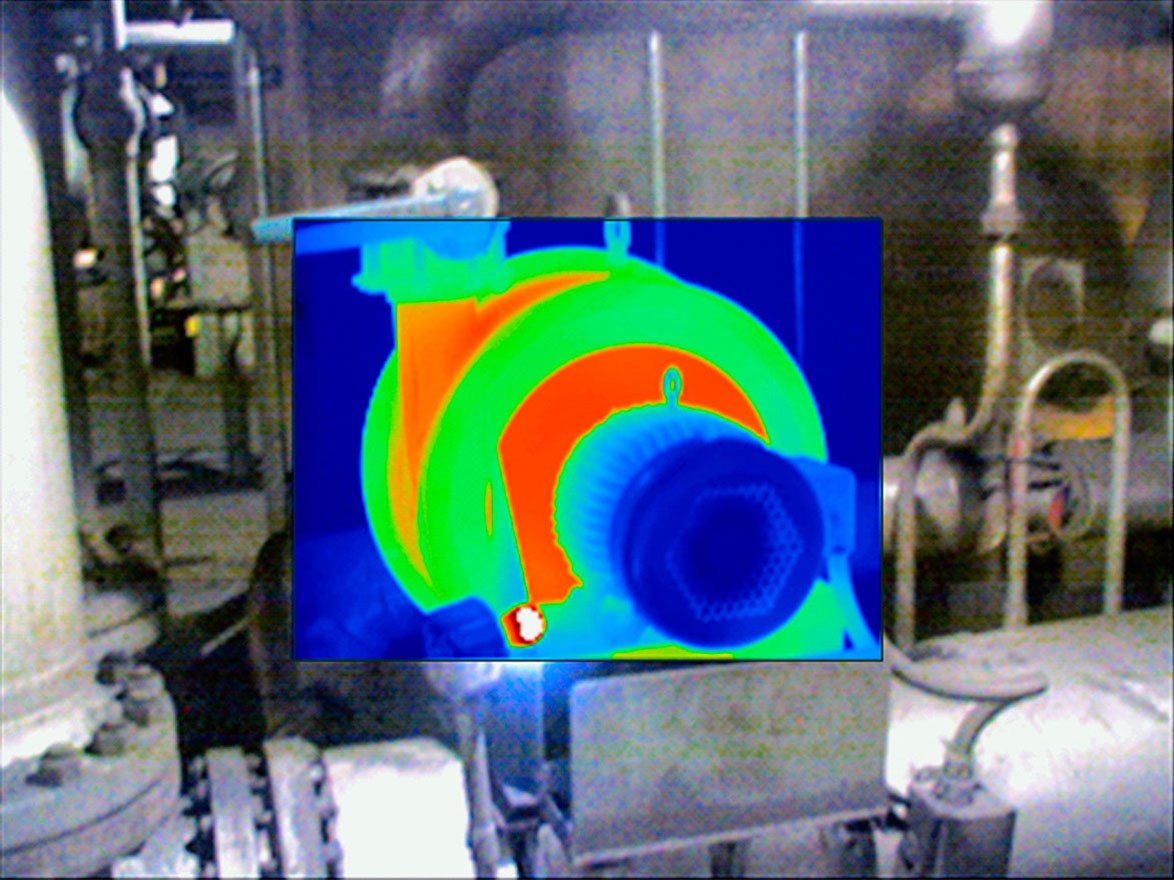
El rodamiento superior del motor del extremo está fallando debido a un sobrecalentamiento de todo el motor. (Fotografía cortesía de Greg McIntosh, Snell Infrared Canada)
Inspección de rodamientos de motores
La comprobación de rodamientos de motores es un ejemplo perfecto. Empiece con un motor que se haya puesto en servicio recientemente y que esté recién lubricado; tome una instantánea del alojamiento de rodamientos mientras el motor está en funcionamiento. Utilice esta imagen a modo de referencia.
Con el paso del tiempo en el motor y su lubricación, los rodamientos se desgastan y se producirá fricción generadora de calor, lo que provocará que se recaliente la parte exterior del alojamiento. Tome imágenes adicionales en intervalos regulares, comparándolas con el valor de referencia para analizar el estado en que se encuentra el motor.
Cuando las imágenes térmicas indiquen un rodamiento recalentado, elabore una orden de mantenimiento para sustituir o lubricar el alojamiento del rodamiento, reduciendo o eliminando así la posibilidad de un costoso fallo del motor.
Detección de fugas en cierres y juntas
Las fugas en recipientes herméticos se detectan al instante con una cámara termográfica. La mayoría de las fugas se generan en el interior o alrededor de una junta o cierre. Con menos frecuencia, la corrosión provoca una vulnerabilidad que acaba aumentando y llega a romper el depósito.
Sea como fuere, una cámara termográfica puede diagnosticar el problema. Para detectar una fuga en una junta o cierre solo tiene que analizar las anomalías de tipo térmico. Un gran cambio en la temperatura a lo largo del cierre o junta indica una pérdida de calor o frío que evidencia una avería.